In 2025, the Boring Machine market is booming, driven by technological advancements and rising industrial demand. This article provides an in-depth analysis of key selection factors, including application specificity, machine specifications, and cost considerations. It offers valuable guidance to professional buyers in making informed decisions, ensuring optimal performance and profitability.
Table of Contents:
-Boring Machine Market Overview
-Detailed Introduction and Analysis of the Boring Machine Market
-Key Factors When Selecting a Boring Machine
-Innovations in Boring Machine Technology
-Environmental Considerations in Boring Machine Operations
-Future Trends in Boring Machine Technology
-Wrapping Up
Boring Machine Market Overview
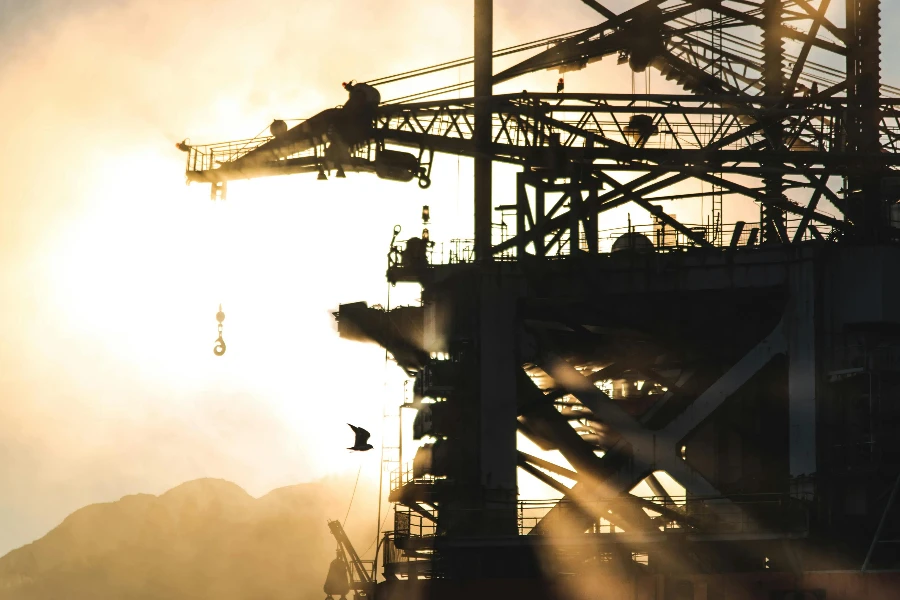
The global market for boring machines has seen significant growth in recent years. In 2023, the market was worth approximately USD 4.4 billion and is projected to reach USD 6.2 billion by 2030, growing at a CAGR of 5.0%. This growth is driven by advancements in manufacturing technologies and increasing demand from industries such as automotive, aerospace, and heavy machinery. The transportation end-use segment is expected to see the most substantial growth, reaching USD 2.9 billion by 2030 with a CAGR of 5.3%, while the general machinery segment is anticipated to grow at a CAGR of 4.4%.
Regionally, the U.S. market was estimated at USD 1.2 billion in 2023, and China’s market is forecasted to grow at an impressive CAGR of 7.6%, reaching USD 1.4 billion by 2030. Other significant markets include Japan, Canada, Germany, and the broader Asia-Pacific region, all of which are expected to contribute to the overall growth of the boring machine market.
Detailed Introduction and Analysis of the Boring Machine Market
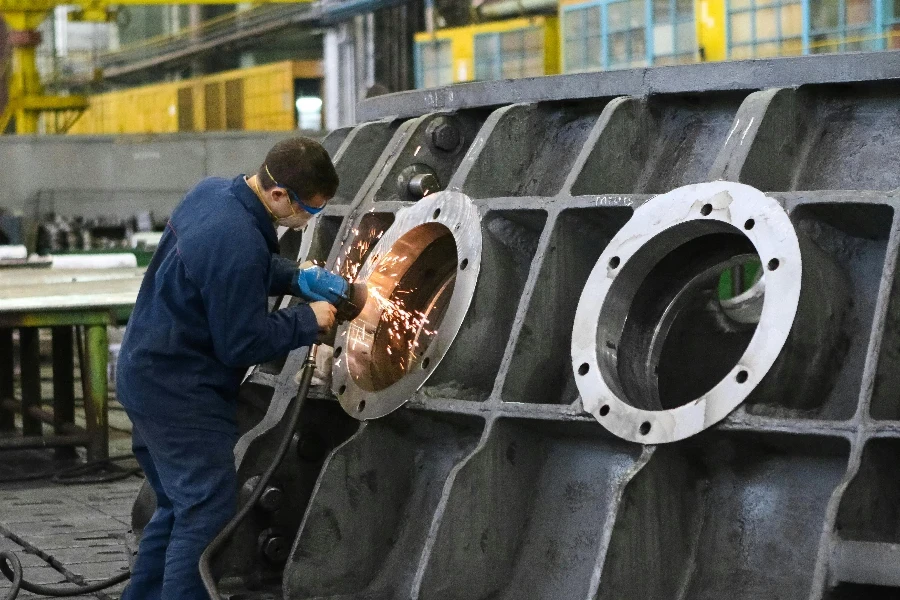
Boring machines are crucial in precision machining, particularly in industries that require high accuracy and smooth finishes, such as automotive, aerospace, and heavy machinery. These machines are designed to enlarge and finish pre-drilled or cast holes with high precision, ensuring that the diameter, surface finish, and tolerance meet exact specifications. The market is segmented into fine boring and rough boring types, each serving different needs based on the material and cutting conditions.
Technological advancements have significantly enhanced the performance and versatility of boring machines. Innovations such as advanced coatings and materials for cutting edges, including polycrystalline diamond (PCD) and cubic boron nitride (CBN), offer superior wear resistance and longer tool life. Additionally, digitally controlled boring heads enable real-time adjustments during machining, providing unparalleled precision and reducing errors. The integration of sensor technology for predictive maintenance has further optimized the machining process and reduced downtime.
Despite these advancements, the boring machine market faces challenges. Maintaining accuracy across a wide range of materials, managing heat generation, and addressing the trend towards miniaturization in industries like electronics and medical devices are ongoing issues. Manufacturers are exploring advanced cooling techniques and developing more robust and versatile tools to address these challenges. The cost pressures in manufacturing also drive the need for more efficient boring machines that can deliver high performance while minimizing downtime and waste.
Key Factors When Selecting a Boring Machine
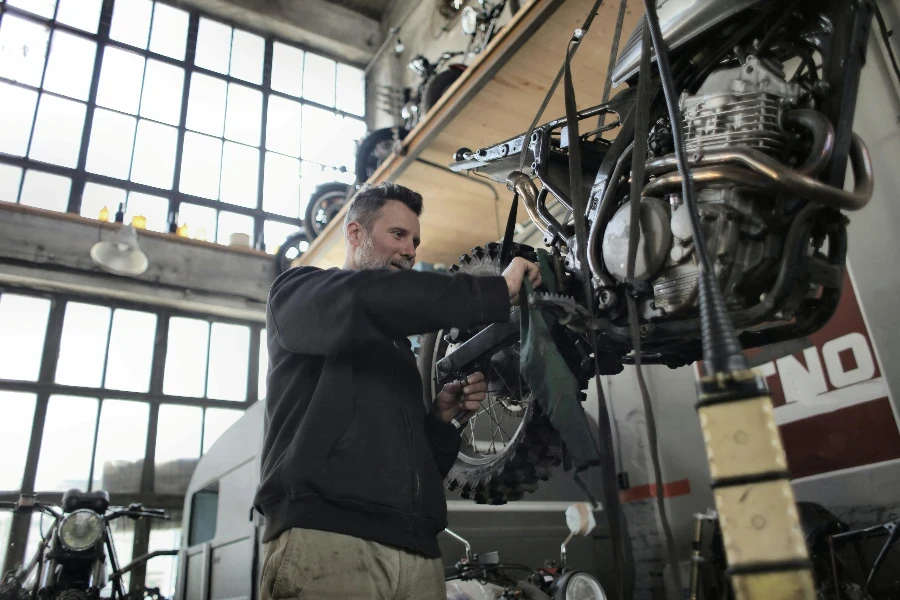
Application Specificity
When selecting a boring machine, the first factor to consider is the specific application it will be used for. Different boring machines are designed to handle varying tasks, such as precision boring, jig boring, lathe boring, vertical boring, and horizontal boring. For instance, precision boring machines are ideal for producing highly accurate internal cylindrical surfaces, whereas jig boring machines are suited for creating holes with precise dimensions and locations. Understanding the specific requirements of the task will help in choosing the appropriate machine type.
Precision boring machines typically use single-point cutting operations to achieve accuracy within ±0.0001 inches, making them suitable for high-precision tasks such as finishing internal bearing surfaces. In contrast, horizontal boring machines, which can handle larger workpieces and offer multi-functional capabilities such as milling and drilling, are better for heavy-duty applications that require versatility.
The complexity of the workpiece, the required tolerances, and the material being worked on are critical considerations. For example, materials with higher hardness, such as stainless steel, may necessitate machines equipped with carbide or diamond tools to maintain precision and efficiency.
Machine Specifications
The technical specifications of a boring machine are essential to ensure it meets the demands of your application. Key specifications include spindle speed, feed rate, cutting speed, and the power of the machine. Spindle speed, measured in revolutions per minute (RPM), determines how fast the cutting tool rotates and can affect the quality of the finish and the efficiency of the machining process. Higher spindle speeds are typically required for finer finishes and harder materials.
Feed rate, often measured in inches per minute (IPM), indicates the rate at which the cutting tool advances into the material. A proper balance between spindle speed and feed rate is crucial to avoid tool wear and achieve the desired surface finish. Cutting speed, the speed at which the cutting edge of the tool moves along the surface of the workpiece, also plays a significant role in determining the efficiency and quality of the boring process.
Power requirements of the machine, usually specified in horsepower (HP), should align with the material removal rate and the hardness of the material being machined. For instance, boring machines working with materials like stainless steel and cast iron, which have higher unit power requirements, will need more powerful motors to maintain performance.
Tolerance and Precision
Tolerance and precision are critical factors in the selection of a boring machine, especially for applications requiring high accuracy. The tolerance of a boring machine refers to the allowable deviation from the specified dimensions, which can vary depending on the type of machine and the application. Precision boring machines, for instance, can achieve tolerances as tight as ±0.0001 inches, making them suitable for applications where dimensional accuracy is paramount.
Environmental conditions, tool geometry, and the alignment of machine components and fixtures also influence the precision of the boring process. Using cutting fluids can help maintain tool temperature, reduce wear, and allow for higher cutting speeds and feed rates, thereby enhancing precision.
Additionally, the rigidity of the machine, workpiece, and tool setup is crucial for maintaining accuracy during the boring process. Machines with robust construction and high-quality components are less likely to experience deflection or vibration, which can compromise precision.
Material Compatibility
The compatibility of the boring machine with different materials is another important consideration. Boring tools are typically made from high-speed steel (HSS), carbide, ceramics, or diamonds, each suitable for different materials and applications. For instance, carbide and diamond tools are preferred for machining hard materials like stainless steel, while HSS tools are suitable for softer materials like aluminum and brass.
Understanding the material properties, such as hardness and machinability, is essential for selecting the right boring machine and tools. For example, materials with high hardness values, such as cast iron and stainless steel, require tools with higher wear resistance and cutting speeds to maintain efficiency and precision.
Moreover, the choice of cutting fluid can impact the machining process, particularly when working with materials that generate significant heat. Cutting fluids help reduce tool wear, improve surface finish, and increase cutting speeds, making them a vital component in boring operations.
Cost and Budget
Finally, the cost and budget for acquiring a boring machine must be considered. Boring machines vary significantly in price based on their type, specifications, and features. Automated and CNC-controlled boring machines, which offer higher precision and efficiency, tend to be more expensive than manual or semi-automatic machines.
Investment in a boring machine should be aligned with the expected return on investment (ROI) and the specific needs of the operation. For small-scale or less frequent operations, a lower-cost machine with basic features may suffice. However, for high-volume production or applications requiring high precision, investing in a more advanced and expensive machine can result in long-term cost savings through improved efficiency and reduced downtime.
Maintenance costs, tool replacement, and energy consumption should also be factored into the overall budget. Machines with higher energy efficiency and lower maintenance requirements can significantly reduce operating costs over time.
Innovations in Boring Machine Technology
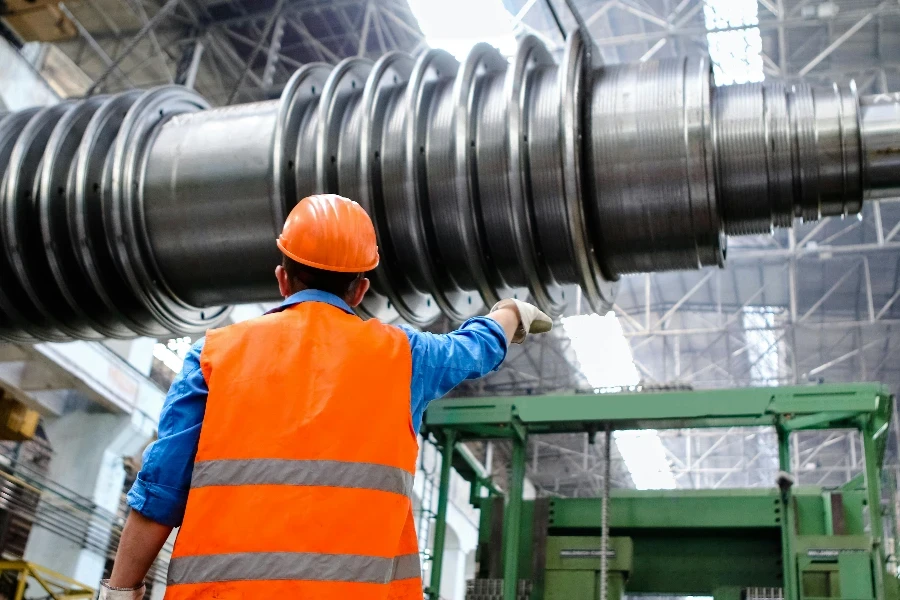
CNC Integration
The integration of Computer Numerical Control (CNC) technology in boring machines has revolutionized the industry by enhancing precision, efficiency, and automation. CNC boring machines are programmed using G-code, allowing for precise control over the cutting tool’s movement, speed, and feed rate. This technology enables complex and repetitive tasks to be performed with minimal human intervention, reducing the likelihood of errors and increasing productivity.
CNC boring machines can be equipped with advanced features such as automatic tool changers, which allow for the use of multiple tools in a single operation without manual intervention. This capability is particularly beneficial for applications requiring different cutting tools for various stages of the boring process, such as roughing and finishing.
Additionally, CNC technology facilitates the use of simulation software to model the boring process before actual machining, identifying potential issues and optimizing parameters for improved efficiency and accuracy. This predictive capability reduces setup times and minimizes material waste, contributing to cost savings and environmental sustainability.
Advanced Tooling Materials
The development of advanced tooling materials has significantly impacted the performance and durability of boring machines. High-performance materials such as polycrystalline diamond (PCD) and cubic boron nitride (CBN) offer superior hardness and wear resistance compared to traditional HSS and carbide tools. These materials enable higher cutting speeds, longer tool life, and improved surface finishes, particularly when machining hard and abrasive materials.
PCD tools are ideal for non-ferrous materials such as aluminum and composites, providing high precision and extended tool life. CBN tools, on the other hand, are suitable for ferrous materials like hardened steel and cast iron, offering excellent thermal stability and resistance to wear.
The use of advanced coatings, such as titanium nitride (TiN) and aluminum oxide (Al2O3), further enhances tool performance by reducing friction and heat generation during the cutting process. These coatings improve chip evacuation, reduce tool wear, and enable higher cutting speeds, resulting in increased productivity and cost savings.
Automation and Robotics
Automation and robotics are playing an increasingly important role in the boring machine industry, enhancing efficiency, precision, and safety. Automated boring machines can perform complex tasks with minimal human intervention, reducing labor costs and the risk of errors. Robotic systems can be integrated with boring machines to automate material handling, tool changes, and quality inspections, further streamlining the manufacturing process.
For example, robotic arms can load and unload workpieces, position them accurately on the machine, and perform secondary operations such as deburring and cleaning. This level of automation not only increases productivity but also improves workplace safety by reducing the need for manual handling of heavy and hazardous materials.
Robotic systems can also be equipped with advanced sensors and machine learning algorithms to monitor the boring process in real-time, detecting anomalies and making adjustments to optimize performance. This capability enhances the overall efficiency and reliability of the machining process, reducing downtime and maintenance costs.
Environmental Considerations in Boring Machine Operations
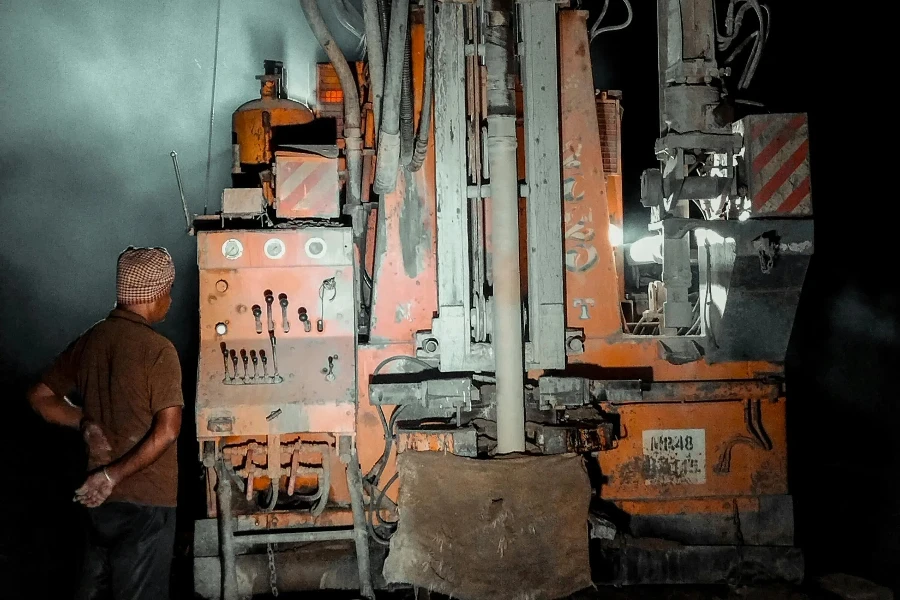
Energy Efficiency
Energy efficiency is a critical consideration in modern boring machine operations, driven by the need to reduce operational costs and environmental impact. Advances in motor technology, such as high-efficiency electric motors and variable frequency drives (VFDs), have significantly improved the energy efficiency of boring machines. These technologies enable precise control over motor speed and torque, reducing energy consumption and optimizing performance.
Additionally, the use of energy-efficient components, such as LED lighting and low-power electronics, further contributes to the overall energy savings. Implementing energy management systems to monitor and control energy usage in real-time can help identify inefficiencies and implement corrective measures, resulting in substantial cost savings and reduced carbon footprint.
Waste Reduction
Waste reduction is another important aspect of sustainable boring machine operations. Efficient material utilization and optimized machining processes can minimize material waste and reduce the environmental impact of manufacturing. Advanced simulation software and CNC technology enable precise control over the boring process, reducing scrap rates and improving material yield.
Recycling and reusing cutting fluids, chips, and other waste materials can also contribute to waste reduction. Implementing closed-loop systems for cutting fluid management and chip recycling can minimize waste disposal costs and reduce the environmental impact of machining operations.
Emission Control
Controlling emissions from boring machine operations is essential for maintaining a safe and environmentally friendly workplace. The use of advanced filtration systems, such as mist collectors and air scrubbers, can effectively capture and remove airborne contaminants, including oil mist, coolant vapors, and particulate matter. These systems help maintain air quality and comply with environmental regulations, protecting the health of workers and the surrounding community.
Additionally, the selection of environmentally friendly cutting fluids and lubricants can reduce harmful emissions and improve workplace safety. Water-based and biodegradable cutting fluids offer a safer and more sustainable alternative to traditional oil-based fluids, minimizing the environmental impact of machining operations.
Future Trends in Boring Machine Technology
Smart Manufacturing
The rise of Industry 4.0 and smart manufacturing is set to transform the boring machine industry, with increased connectivity, data analytics, and automation driving improvements in efficiency and precision. Smart boring machines equipped with sensors and IoT connectivity can collect and analyze data in real-time, providing valuable insights into machine performance, tool wear, and process parameters.
This data-driven approach enables predictive maintenance, reducing downtime and extending the lifespan of machines and tools. By identifying potential issues before they lead to machine failures, manufacturers can optimize maintenance schedules and reduce the risk of unexpected breakdowns, improving overall productivity and cost efficiency.
Additive Manufacturing Integration
The integration of additive manufacturing (AM) with traditional boring processes offers new possibilities for complex part production and customization. Hybrid machines that combine additive and subtractive manufacturing capabilities can produce intricate geometries and internal features that are difficult or impossible to achieve with conventional machining alone.
Additive manufacturing allows for the creation of near-net-shape parts, reducing material waste and minimizing the need for extensive machining. By combining AM with precision boring, manufacturers can achieve high-quality finishes and tight tolerances on complex parts, expanding the range of applications and improving overall efficiency.
Sustainability and Circular Economy
Sustainability and the circular economy are becoming increasingly important in the manufacturing industry, driving the development of more environmentally friendly boring machine technologies. Manufacturers are focusing on reducing energy consumption, minimizing waste, and promoting the reuse and recycling of materials.
The adoption of sustainable practices, such as using renewable energy sources, implementing closed-loop systems for cutting fluid management, and designing machines for easy disassembly and recycling, will play a crucial role in reducing the environmental impact of boring machine operations.
Wrapping Up
In summary, selecting the right boring machine involves careful consideration of application specificity, machine specifications, tolerance and precision, material compatibility, and cost. Advances in technology, such as CNC integration, advanced tooling materials, and automation, are driving improvements in efficiency, precision, and sustainability. Environmental considerations, including energy efficiency, waste reduction, and emission control, are becoming increasingly important in modern boring machine operations. Future trends, such as smart manufacturing, additive manufacturing integration, and sustainability, will continue to shape the industry, offering new possibilities and challenges for manufacturers.