Before you set your foot into purchasing any weaving machines, there are things you need to know. The first thing to keep in mind is that there are different types of weaving machines available, and the second thing is that the market is flooded with different models of weaving machines. Many buyers make the mistake of buying weaving machines without knowing their machine capabilities and type.
This article will focus on how buyers can select suitable weaving machines as well as the different weaving machines available in the market right now. Additionally, it is going to look at the share, size, demand, and expected growth of the weaving machine market.
Table of Contents
Overview of the weaving machine market
Structure of weaving machines
Types of weaving machines
How to select suitable weaving machines
Conclusion
Overview of the weaving machine market
Globally, the weaving machinery market is segmented by machine types, weaving types, applications, and region. Some of the weaving types include plain weave, twill weaving, and stain weaving. The market is steadily expanding due to the increased intake of apparel-based products.
Mordor Intelligence reports that the global weaving market will grow at a CAGR of 4.1% from 2022 to 2027. This s due to the advent of technical fabrics that require the use of weaving machines. Also, weaving has extensive applications in the clothing and textile industries, which have employed products with higher efficiency and durability to meet the demand of buyers.
Regionally, North America, Asia Pacific, Europe, the Middle East, and Africa are the main segments of the international weaving market share. The demand for weaving machinery in these areas has increased due to the high presence of key manufacturers of weaving equipment. The governments’ initiatives like reduced duties on weaving machinery have also led to the expansion of the market size.
Structure of weaving machines
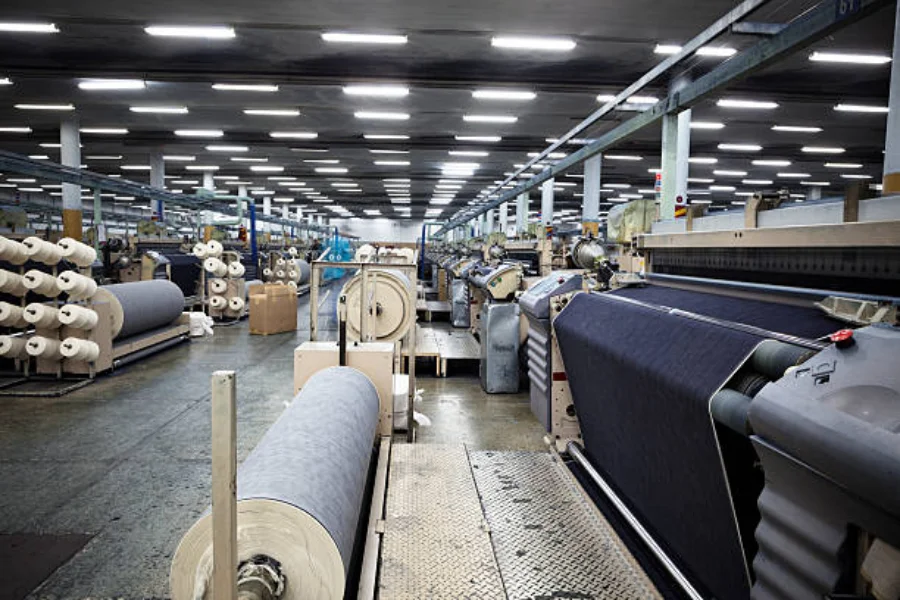
The principal components of a weaving machine are the frame, the weavers beam or warp beam, the apron bar (cloth roll), the reed, and the heddles with their mounting. The warp beam is a metal or wooden cylinder at the back of the loom where the warp is delivered. The warp threads extend in parallel order to the front of the loom from the warp beam and attach to the cloth roll.
As the threads pass through the openings in heddles, they are divided into two or more groups which are controlled and drawn up and down automatically by the movement of the heddles. Each movement opens a shed between the threads of the warp through which the pick is inserted. Traditional looms had the weft inserted by a shuttle. The process of weaving is repetitive in nature.
Types of weaving machines
1. Shuttle weaving machine
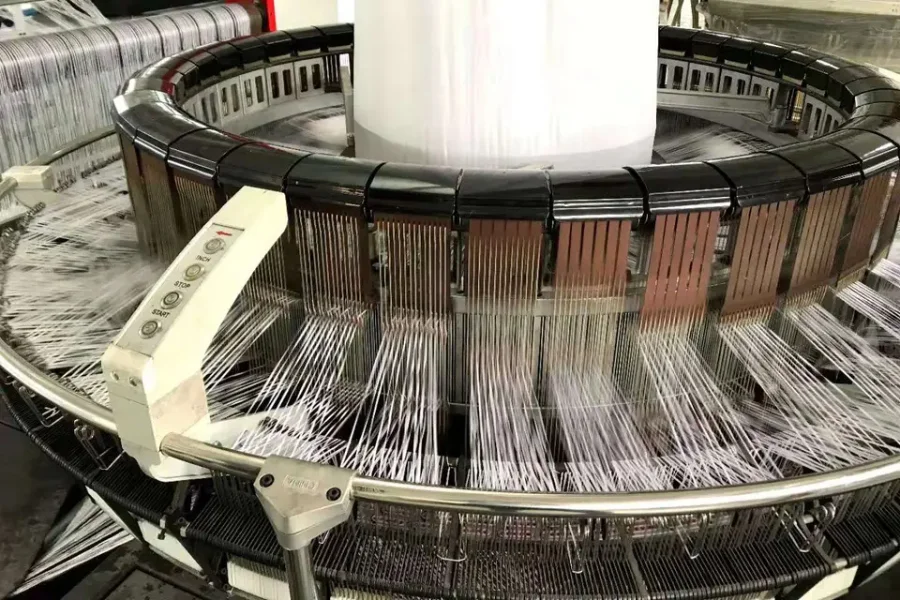
Shuttle weaving machines have a spindle-shaped device that carries the weft (crosswise threads) through the warp (lengthwise threads). Weaving machines without a shuttle draw weft from a stationary supply. The shuttle looms are grouped into two depending on whether the shuttle is moved automatically or by hand. On average, shuttle looms register a speed range of 150 to 160 picks per minute (ppm).
Pros
– It is more economical as compared to looms without the shuttle.
– It is suited for small-scale production lines.
– It is easy to operate, and the spare parts are readily available.
Cons
– The equipment makes a lot of noise while in operation.
– It results in an abrasion on warp yarn thus increasing wastage.
– The production rate is slower compared to shuttleless looms.
2. Circular weaving machine
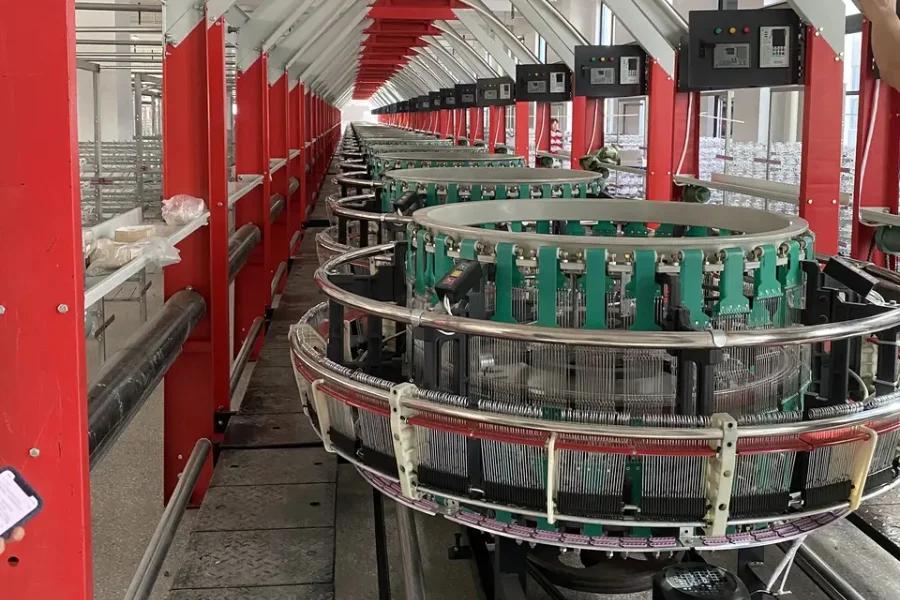
Circular weaving machines are created with continuously circulating shuttles that run around a periphery. Even though the shuttle seed is limited in this system, several shuttles can be sued at the same time thus increasing productivity. Faults like slough-off are eliminated due to the uniform speed of the weft package. These machines have an operating speed of about 110 to 225 ppm.
Pros
– It has a higher operating efficiency.
– It offers excellent weaving quality due to lower wastage.
– It requires lower energy consumption and lower maintenance.
Cons
– It creates less flexible fabric in width.
– It has a narrow range of options in terms of fabrics and patterns.
3. Narrow fabric weaving machine
Narrow fabric weaving machines create fabrics that are ultimately a few centimeters broad. The maximum width is 15 cm. These machines can weave several narrow fabrics next to each other simultaneously on one narrow weaving loom. The modern narrow weaving machines lack the normal shuttle that transports the weft yarn. They instead have a hook-like mode of movement or grippers that move the weft yarn from side to side. Some mechanical narrow weaving machines register speeds of up to 2,750 rpm.
Pros
– It is capable of processing all textiles in weft and warp.
– It is suitable to manufacture elastic and non-elastic ribbons that are of light to medium weight.
– It features enhanced safety, efficiency, and high performance.
Cons
– It is difficult to control sensitive or elastic yarns due to the small warp beams.
– Warp tension control is more demanding in narrow fabric weaving.
How to select suitable weaving machines
1. Ease of use
There are various factors that affect the ease of learning and operating the weaving machines. The learning curve for a particular loom is determined by the knowledge of the basics and the functionality of the specific components. Simpler or smaller looms have fewer steps in setting up and getting to the weaving process. This easily enables the buyers to achieve the desired designs at the set production goals. It can only require online videos or manual user handbooks to learn everything. On the other hand, muti-shaft weaving machines involve a lengthier process to set up and get to warp on them. Also, the more shafts they have, the more complex the patterning will be.
2. Cost
Usually, the more complex and bigger a weaving machine is, the higher the price. The simplest looms, like the rigid heddle looms, are the least costly but will increase in cost as shafts and weaving width are added. Buyers need to understand that for more complex looms, the initial investment is quite high but they provide service for a longer time. Modern weaving machines offer more capabilities and are cost-effective when it comes to maintenance. Some of these machines have a lower initial investment because they have fewer shafts, which can be added later as the production increases and diversifies.
3. Number of harnesses
Most of the simplest weaving machines offer 2-shaft capabilities, for instance, the inkles. They produce simple over or under alternating threads called plain waves. Buyers can create more complex patterns if they use pick-up sticks or other hand-manipulated methods to weave textured patterns and lace. Meanwhile, multi-shaft weaving machines have a range of 4 to 32 shafts. The more the number of shafts, the more the count of pattern capabilities. However, the most common configuration includes the 4- and 8-shaft weaving machines, which provide various patterns and weave structures.
4. Speed
The speed of a weaving machine depends on the reed space. For a wider loom, more time is taken by the shuttle to move from one box to another. Additionally, a double lift jacquard or double lift dobby loom has a higher speed than a single lift jacquard or a single lift dobby loom, respectively. On average, conventional shuttle weaving machines can operate at speeds of around 150 to 160 ppm. There are faster industrial weaving machines that register a speed of up to 2,105 rpm. Industrial weaving machines like the rapier loom operate at speeds ranging from 200 to 260 ppm while using around 1300 m of weft yarn per minute.
5. Suitability
This factor is ascribed to the weaving width of the loom, which indicates the widest warp to be woven on it. First, the woven cloth tends to be narrower as a result of shrinkage (wet finishing) and take up (amount of fabric drawn in). The finished piece could be around 10-25% smaller based on the weave structure and fiber content. Secondly, it is not advisable to weave on full width as the beater needs space on either side of the fabric.
Based on the projects at hand, buyers need to consider the following guidelines suited to their weaving machines:
– 10-inch weaving machine – bags, scarves, and table runners
– 15-20 inches loom – shawlettes, narrow dish towels, placemats, and fabric to piece into blankets or clothing
– 25-30 inches loom – all of the above, standard dish towels, throws, shawls, rugs, and standard dish towels
– 36-59 inches loom – all the above, tablecloths, full-size blankets, and coverlets
Conclusion
Buyers need to look at the kind of products they intend to weave to determine the required weaving machines. This is because the size of the loom prescribes the types of woven tasks in two ways. These include the weaving width of the weaving machine and the types of fabrics woven. Also, the complexity of patterns determines the number of shafts or time spent on different weaving tasks. These factors have been clearly highlighted in the above guide to help buyers with their choice of the appropriate weaving equipment. To acquire quality and efficient weaving machines, visit Chovm.com.