From cutting to shaping to engraving and drilling stones, waterjet stone cutters are the superheroes of the stone cutting world. These machines use high-pressure water and abrasive materials to precisely slice through stone, making them a staple in many industries.
Whether you’re a small-scale stone fabricator or a large production company, it’s important to stay ahead of the curve and understand the latest trends in the industry.
In this guide, we’ll explore the factors to consider when selecting a stone cutting machine in 2023.
Table of Contents
Waterjet stone cutter global market and driving factors
What to look for when selecting a waterjet stone machine
The potential market for waterjet stone cutters
Conclusion
Waterjet stone cutter global market and driving factors
In 2021, the waterjet cutting machine market had a total worth of US $1141.27 million and is projected to grow at a compound annual growth rate (CAGR) of 6.14%, reaching US $1631.39 million between 2021 and 2027. The upsurge in demand is largely due to the rising popularity of eco-friendly techniques and practices in the automotive, electronics, aerospace defense, mining, and metal fabrication industries.
In addition, there is a growing trend toward process automation in these target industries as well as an increasing focus on product launch and advancement, leading to the adoption of advanced machines and contributing to overall industry growth.
Other factors propelling the market include the need for precision cutting techniques, favorable reimbursement scenarios, and the rapid pace of industrialization.
What to look for when selecting a waterjet stone machine
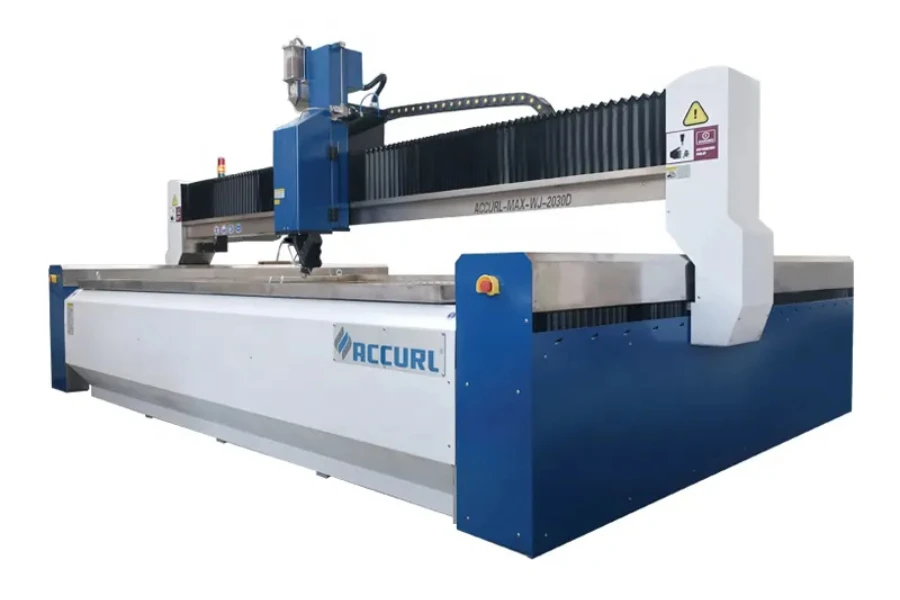
- Utilization
The most important details to consider when investing in equipment is the number of hours and shifts that it will be used for per week. If the equipment will only be used for a short amount of time, it may not be worth investing in the fastest and most powerful machine.
If the equipment is likely to be used for more than one shift, it’s best to invest in a high-output machine with a hyperJet pump. These pumps can increase water pressure to 94,000 psi, allowing for faster cutting with significantly less abrasion.
- Type of material
When cutting with a waterjet, it is important to determine the materials that you work with most frequently. There are two main types of waterjet cutting: pure waterjet and abrasive waterjet cutting. Pure waterjets can handle soft materials such as gaskets, foam, and plastic, while abrasive waterjets can handle tougher materials such as metals, glass, stone, and composite materials.
The size and thickness of the materials you intend to cut also play a role in the waterjet cutting process. It is important to ensure that your equipment is properly calibrated and that you have the necessary resources to handle larger or thicker materials.
- Material size and thickness
The size and thickness of the materials being cut are crucial factors to consider when using a waterjet cutting machine. The size and thickness of the material affect various aspects of the cutting process, including the number of cutting heads required, the pump specifications, and the size of the work bed.
To cut stone, the most common sheet and plate sizes usually dictate a 6.5 x 13 ft. (2 x 4 m) work bed size, covering nearly all North American and European material plate sizes. The 13-foot bed allows for easy loading of aluminum, which often comes in 12-foot sheets in North America. Meanwhile, the 6.5-feet-wide bed accommodates 6-feet-wide stone slabs. It is advisable to get a work bed that is slightly larger than the stock material you intend to cut so to reduce the chance of loading and fixturing issues. A less obvious reason to obtain a relatively large work bed is that it provides room for installing multiple, semi-permanent tooling locations to enable quick changeover from one job to another.
To cut brittle materials such as stone, it is recommended that you equip your machine with UltraPierce, a vacuum-assisted device that reduces the chance of cracking when cutting such materials.
- Cutting accuracy and speed
Cutting accuracy and speed are crucial as they determine the machine’s overall performance. Accuracy ensures that your cuts are precise and consistent, which is particularly important when working with high-end materials that require low tolerances. If your machine is not accurate enough, you risk damaging the material or producing parts that are not up to spec, which can lead to costly rework and delays.
If you own a fabrication or machine shop, the precision requirements of your waterjet cutting machine may differ. Generally, machine shops require more accuracy compared to a fab shop. A machine tool using a basic waterjet cutting head, typically called a conventional waterjet head, can cut to a +/-0.005 inches accuracy from any material that’s 3-inch thick.
A dynamic waterjet automatically tilts the cutting head impingement angle to compensate for stream lag and taper, making it two to four times more precise and faster (+/-0.12-0.2 inches).
The faster your machine can cut, the more parts you can produce in a given amount of time. However, to cut to the above precision, which is equivalent to +/-0.005 inches, the speed must be reduced to at least 15% of the machine tool’s maximum cutting speed.
- Machine motor performance
The motor is the heart of a waterjet stone cutting machine as it is responsible for providing consistent power, speed, and precision. A high-quality motor will ensure a machine has greater cutting accuracy and improved longevity, as well as reduce maintenance costs.
Furthermore, a powerful motor will enable the machine to cut through thicker materials at faster speeds, which ultimately saves time and increases productivity. A reliable motor also helps to reduce the chance of machine breakdowns and production delays.
- Gearbox performance
The gearbox transfers the rotational power from the motor to the cutting head. By increasing the machine’s torque and reducing its speed, the gearbox allows high-pressure water to be delivered to the cutting head with precision and accuracy.
A high-quality gearbox provides smooth and efficient power transmission for precise, consistent cutting. On the contrary, a low-quality gearbox can cause vibrations, noise, and poor cutting results. It is also important to consider the durability of the gearbox, as this will affect the machine’s longevity; a gearbox that is prone to wear and tear can be expensive to repair or may even require a full replacement.
- Machine material
The quality of the material from which a machine is made will have a significant impact on the performance, durability, and longevity of the machine. The machine should be made of high-quality materials such as steel and aluminum as they are both strong and resistant to corrosion – ideal if you’re working with water and abrasive materials.
Also, It is important to evaluate the quality of the components used in a machine. Look for machines with top-notch parts, such as precise cutting heads, robust pumps, and reliable electronics – these will improve the machine’s accuracy and dependability.
- Operational stability
A waterjet stone machine that is operationally unstable can lead to inconsistent cuts, resulting in wasted time, materials, and money.
Furthermore, it can lead to frequent breakdowns, repairs, and maintenance, which can be costly and disrupt workflow. Investing in a stable waterjet stone machine is therefore beneficial as it will not only produce consistently reliable results but also saves money in the long run.
- Granulometric preferences
Waterjet cutting machines use abrasive particles made of materials like garnet, aluminum oxide, or silicon carbide to increase the water stream’s cutting power. The granulometric preference of a waterjet cutting machine depends on the type and thickness of the material being cut, the desired cutting speed, and the quality of the cut. For example, larger abrasive particles (80-120 mesh) may be needed for faster cutting speeds and increased accuracy, while smaller abrasive particles (180-220 mesh) may be more appropriate for avoiding chipping or cracks in the material.
- Material absorption
More porous materials are likely to absorb more water during the cutting process, causing the water pressure to decrease and the cutting speed to slow down. This can result in longer cutting times, reduced productivity, and decreased precision in the final product.
On the other hand, if the materials are too dry, they may become brittle and more prone to cracking or chipping during the cutting process. This can also affect the precision and quality of the final product.
- Size of applicable parts
The size of the waterjet stone machine’s cutting bed is an important factor to consider when purchasing a machine as it will determine the maximum size of stone pieces that can be cut.
If the cutting bed is too small, it will limit the size of the pieces you can work with and may require multiple cuts to achieve the desired size. Conversely, if the cutting bed is too large for your needs, it could result in unnecessary expenses. It is important to select a waterjet stone machine with a cutting bed size that fits your needs as this will help to accomplish your desired results.
- Control accuracy
When choosing a waterjet stone cutter, the accuracy of the control system is essential in order to direct and position the water stream for cutting the stone.
If the control system is imprecise, the end product may have errors, leading to wasted materials, time, and costs. Additionally, the stones may not fit together correctly, creating a potential safety hazard.
Meanwhile, with precise control accuracy, intricate and detailed designs can be cut into the stone, allowing for more creative freedom and the ability to produce more unique pieces.
The potential market for waterjet stone cutters
Customers of waterjet stone cutters are typically businesses that work with stone, such as stone fabricators, contractors, and manufacturers. These customers require precise and efficient cutting tools for their projects, which waterjet cutters are able to provide. Additionally, the environmentally-friendly nature of waterjet cutting makes it an attractive option for customers who prioritize sustainability and eco-friendliness.
Conclusion
When selecting a stone machine for use in 2023, it is important to evaluate the requirements for the job. Considering the features and capabilities of different models can help to ensure that you choose the ideal stone machine for your specific needs and budget.
Investing in the right stone machine can lead to improved efficiency, productivity, and quality, resulting in greater success and profitability. If you’re looking for a wide selection of high-quality stone machines at competitive prices, be sure to visit Chovm.com.