By die Additive Manufacturing-kampus in Oberschleißheim beproef die BMW-groep draadboogtoevoegingsvervaardiging (WAAM), waarin 'n draad wat van aluminium of soortgelyk gemaak is, met 'n boog gesmelt word. Dan plaas 'n sagteware-beheerde robot 'n groot aantal sweisnate met presisie op mekaar, totdat 'n volledige komponent klaar is.
Omdat die druk beteken dat daar nie laag vir laag aandag hoef te word aan ontvormbaarheid nie, is hol strukture met 'n optimale verhouding tussen styfheid en gewig moontlik.
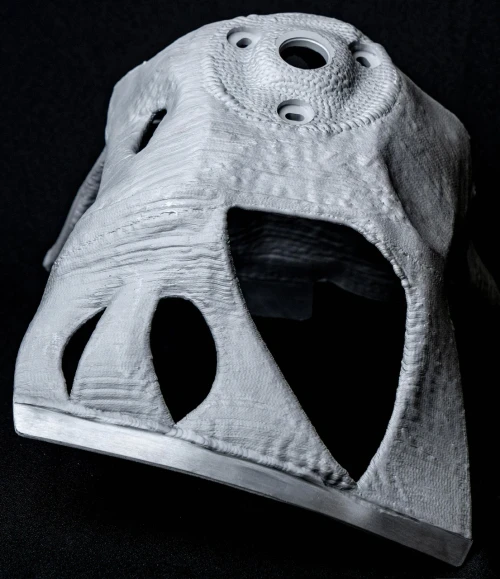
Dit beteken dat die komponente ligter en meer rigied kan wees as vergelykbare gegote dele wat tans in serieproduksie vervaardig word. Hulle kan ook meer volhoubaar geproduseer word danksy laer energievereistes en minder materiaalafval. In die toekoms is die plan om komponente wat volgens die WAAM-proses vervaardig is, in BMW Group-produksievoertuie te gebruik.
Die groot breedte en hoogte van 'n enkele sweisnaat beteken dat komponente uiters vinnig met WAAM vervaardig kan word. In teenstelling met laserstraalsmelting, wat reeds in prototipe- en kleinreeksproduksie by die BMW Groep gebruik word, is WAAM veral geskik vir groter komponente. Die tipiese wanddiktes is goed geskik vir komponente in die bak-, dryf- en onderstelareas. Gereedskap en toestelle kan egter ook vervaardig word met behulp van hierdie hoëtegnologie-proses, wat ook in die lugvaartbedryf gebruik word.
BMW Group-werknemers fokus sedert 2015 op die WAAM-proses, ook bekend as opbou-sweiswerk. 'n WAAM-sel vir die vervaardiging van toetskomponente word sedert 2021 op die Additive Manufacturing-kampus gebruik. Een van hierdie voorbeeldtoepassings is 'n veerstutsteun wat, in uitgebreide toetsing op die toetsbank, vergelyk word met die reeksproduksie-drukkomponent van 'n aluminium.
In hierdie vroeë stadium is dit reeds duidelik dat die WAAM-proses laer emissies in die produksieproses tot gevolg kan hê. Die laer gewig van die komponente, hul voordelige materiaalgebruikverhouding, en die opsie om hernubare energie te gebruik, beteken dat die komponente meer doeltreffend geproduseer kan word.
—Jens Ertel, Hoof van BMW Additive Manufacturing
Die volgende fase van ontwikkeling op die pad na reeksproduksie is om komponente in die voertuig te toets, wat in die afsienbare toekoms sal begin.
Die breër sweisnate in die WAAM-proses beteken dat die oppervlaktes van die komponente nie glad is nie, maar effens gerimpel en in kritieke areas afgewerk moet word. BMW Group-ingenieurs kon egter aantoon dat WAAM-komponente vir hoë vragte, insluitend sikliese vragte, gebruik kan word, selfs sonder nabehandeling van die oppervlak.
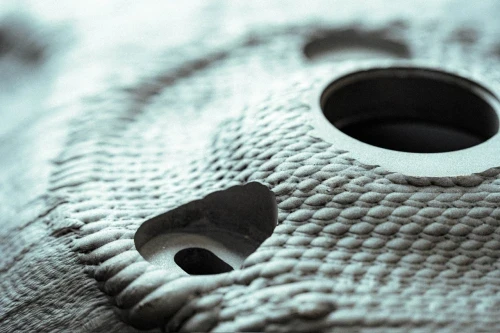
Geoptimaliseerde prosesparameters is van kardinale belang om duursaamheid direk vanaf produksie te verseker, dus moet die kombinasie van sweisproses en robotpadbeplanning optimaal gekoördineer word.
Om die komponente wat in die WAAM-proses vervaardig word, optimaal te benut, is die kombinasie van die vervaardigingsproses en 'n algemene nuwe komponentontwerp uiters belangrik. Vir hierdie doel gaan die BMW Groep voort om die gebruik van generatiewe ontwerp te versnel. Hier gebruik die rekenaar algoritmes om geoptimaliseerde komponente te ontwerp gebaseer op die spesifieke vereistes.
Hierdie algoritmes word ontwikkel in noue samewerking met interdissiplinêre spanne en is deels geïnspireer deur evolusionêre prosesse in die natuur. Soos met bioniese strukture, is die eerste stap om slegs die materiaal te gebruik wat eintlik benodig word vir die topologie van die komponent, en tydens fynverstelling in die tweede stap word die komponent slegs versterk waar nodig. Dit lei uiteindelik tot ligter en meer rigiede komponente sowel as groter doeltreffendheid en verbeterde voertuigdinamika.
Verskillende bymiddelproduksieprosesse is nie noodwendig in kompetisie met mekaar nie, hulle moet eerder as aanvullend beskou word. Laserstraalsmelting sal byvoorbeeld steeds voordeliger wees as die WAAM-proses wanneer dit by die hoogste vlak van detailresolusie kom. Wat die moontlike grootte van die komponent en die neerslagtempo betref, is die vervaardiging van draadboogtoevoegings egter beter.
Die BMW Groep beplan aanvanklik gesentraliseerde WAAM-produksie van komponente in Oberschleißheim, in die toekoms is produksie op ander plekke en die gebruik van die tegnologie deur verskaffers ook moontlik. Verder sou dit selfs denkbaar wees om individuele komponente direk op die monteerlyn te vervaardig deur hierdie proses te gebruik en om verskillende onderdele sonder nuwe gereedskap te vervaardig, bloot deur die sagteware te verander. Volhoubaarheid kan ook verder verbeter word deur die gebruik van herwonne metale te verhoog.
Bron van Groenmotorkongres
Vrywaring: Die inligting hierbo uiteengesit word verskaf deur greencarcongress.com onafhanklik van Chovm.com. Chovm.com maak geen voorstelling en waarborge oor die kwaliteit en betroubaarheid van die verkoper en produkte nie.