ارتفع الطلب على المنتجات المصفحة عالية الجودة في عام 2025، مدفوعًا بالتقدم في مختلف الصناعات. تقدم هذه المقالة تحليلًا متعمقًا لسوق آلات التصفيح، وتغطي الأنواع والأداء والمواصفات الفنية والمزيد. سيجد المشترون المحترفون رؤى قيمة لاتخاذ قرارات شراء مستنيرة، وضمان الكفاءة التشغيلية والموثوقية على المدى الطويل.
جدول المحتويات:
– نظرة عامة على سوق آلات التصفيح العالمية
– تحليل متعمق لسوق آلات التصفيح
- العوامل الرئيسية عند اختيار آلة التصفيح
– أحدث ميزات التكنولوجيا في آلات التصفيح
- العوامل المؤثرة على متانة وعمر آلات التصفيح
- ضمان الامتثال للقواعد التنظيمية ومعايير السلامة
- افكار اخيرة
نظرة عامة على سوق آلات التصفيح العالمية
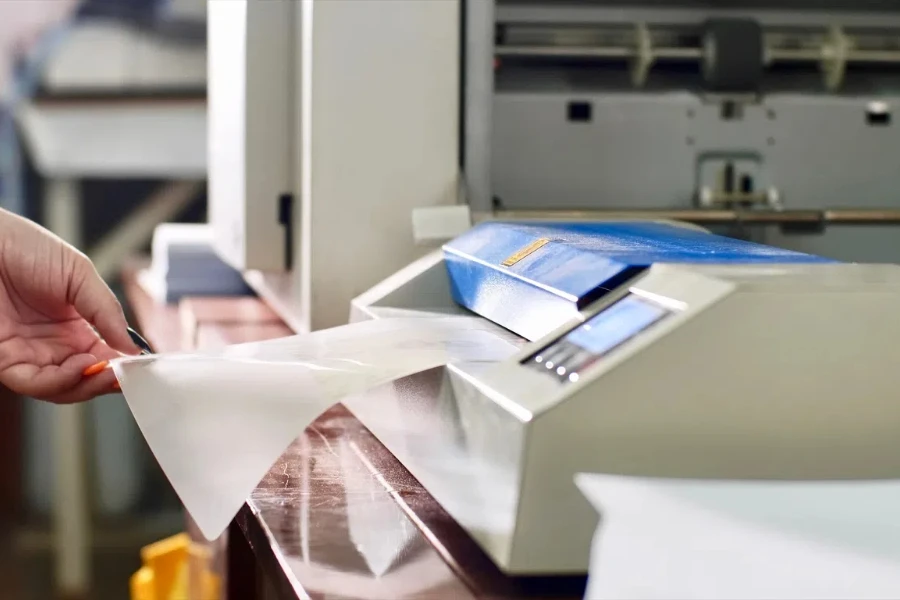
شهد السوق العالمي لآلات الترقق نموًا كبيرًا في السنوات الأخيرة، مدفوعًا بالطلب المتزايد على منتجات الترقق عالية الجودة عبر مختلف الصناعات. في عام 2024، قُدِّرت القيمة السوقية لآلات الترقق الأوتوماتيكية بنحو 3.5 مليار دولار أمريكي، مع توقعات تشير إلى معدل نمو سنوي مركب (CAGR) بنسبة 6.3٪ حتى عام 2029. ويرجع هذا النمو إلى حد كبير إلى التبني المتزايد لتكنولوجيا الترقق في قطاعات مثل التعبئة والتغليف والسيارات والإلكترونيات والنشر.
تحتل منطقة آسيا والمحيط الهادئ الحصة الأكبر في السوق، حيث تمثل أكثر من 35% من سوق آلات الترقق العالمية. وتعود هذه الهيمنة إلى قطاع التصنيع القوي، وخاصة في دول مثل الصين والهند واليابان. تليها أمريكا الشمالية وأوروبا، مع مساهمات كبيرة من الولايات المتحدة وألمانيا. ويعتمد السوق في هذه المناطق على التقدم التكنولوجي والحاجة إلى منتجات متينة وجذابة من الناحية الجمالية.
ينقسم السوق إلى آلات التصفيح الساخن وآلات التصفيح البارد وآلات التصفيح الرقمية. تهيمن آلات التصفيح الساخن بحصة تبلغ حوالي 55%، وذلك بسبب استخدامها على نطاق واسع في التطبيقات التجارية ذات الحجم الكبير. وتستحوذ آلات التصفيح البارد على حوالي 30% من السوق، وهي مفضلة لقدرتها على تصفيح المواد الحساسة للحرارة. ومن المتوقع أن تشهد آلات التصفيح الرقمية، على الرغم من أنها تستحوذ حاليًا على حصة أصغر، أسرع نمو بسبب الرقمنة المتزايدة لعمليات الطباعة.
تحليل متعمق لسوق آلات التصفيح
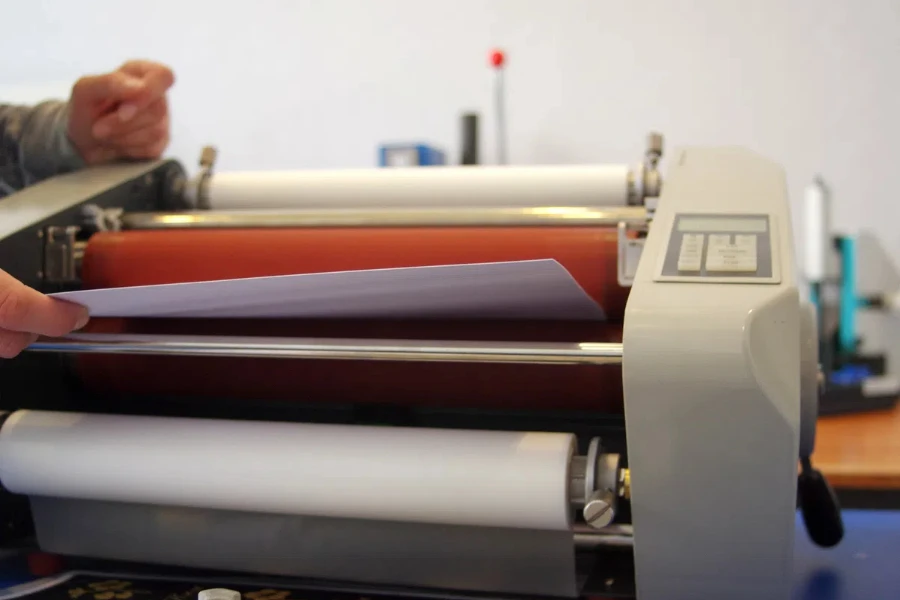
تتميز سوق آلات الترقق بمعايير أداء صارمة، بما في ذلك سرعة الترقق والدقة والمتانة. وقد وضعت شركات التصنيع الرائدة مثل Mitsubishi Electric Corporation وSiemens AG وSchneider Electric SE معايير عالية، مع التركيز على الابتكارات التي تعزز الكفاءة التشغيلية وجودة المنتج. على سبيل المثال، تتميز آلات الترقق المتقدمة من Mitsubishi Electric بسرعة ترقق تصل إلى 30 مترًا في الدقيقة، مما يلبي احتياجات قطاع التعبئة والتغليف عالي الطلب.
تكشف ديناميكيات حصة السوق عن مشهد تنافسي حيث يتمتع اللاعبون الراسخون بنفوذ كبير، ومع ذلك فإن الشركات الناشئة تحقق تقدمًا ملحوظًا. على سبيل المثال، اكتسبت شركة Shenzhen Jiaye Industrial Equipment Co., Ltd. قوة جذب بفضل آلات الترقق الفعالة من حيث التكلفة والمتقدمة تقنيًا، حيث استحوذت على حصة متزايدة من السوق في منطقة آسيا والمحيط الهادئ. تلعب التأثيرات الاقتصادية مثل تقلب أسعار المواد الخام وسياسات التجارة أيضًا دورًا حاسمًا في تشكيل ديناميكيات السوق.
يتحول سلوك المستهلك نحو المنتجات الصديقة للبيئة والمستدامة، مما يجبر الشركات المصنعة على الابتكار من حيث المواد والعمليات. ويكتسب تفضيل الصفائح الصديقة للبيئة، والتي يمكن إعادة تدويرها وقابلة للتحلل البيولوجي، زخمًا متزايدًا. بالإضافة إلى ذلك، فإن دمج التقنيات الرقمية مثل إنترنت الأشياء والذكاء الاصطناعي في آلات التصفيح يحدث ثورة في الصناعة. تمكن هذه التقنيات من المراقبة في الوقت الفعلي والصيانة التنبؤية والدقة المحسنة، مما يقلل بشكل كبير من وقت التوقف عن العمل وتكاليف التشغيل.
تتضمن الابتكارات الحديثة في السوق تطوير آلات الترقق عالية السرعة الموفرة للطاقة والتي تلبي الطلب المتزايد على حلول التغليف المستدامة. على سبيل المثال، يتميز أحدث طراز من آلات الترقق من شركة Siemens AG بتقنية هجينة تجمع بين الترقق التقليدي وقدرات الطباعة الرقمية، مما يوفر تنوعًا وكفاءة لا مثيل لها. تمتد دورة حياة منتج آلات الترقق عادةً من 10 إلى 15 عامًا، مع الصيانة والترقيات المنتظمة لضمان الأداء الأمثل.
وتشكل الرقمنة اتجاهاً رئيسياً آخر، حيث يستفيد المصنعون من حلول البرامج المتقدمة لتبسيط العمليات وتعزيز قدرات تخصيص المنتجات. كما تؤثر الاتجاهات الاجتماعية مثل الطلب المتزايد على التغليف المخصص والمتميز على السوق. ويتم التعامل مع نقاط الضعف لدى العملاء، وخاصة فيما يتعلق بتوقف الماكينة وصيانتها، من خلال حلول مبتكرة مثل التشخيص عن بعد واستكشاف الأخطاء وإصلاحها تلقائيًا.
تركز استراتيجيات تحديد موقع العلامة التجارية في سوق آلات التصفيح على التمايز من خلال التفوق التكنولوجي والاستدامة والخدمات التي تركز على العملاء. تستثمر الشركات بكثافة في البحث والتطوير للبقاء في صدارة المنافسة وتلبية الاحتياجات المتطورة لعملائها. تظهر أسواق متخصصة مثل التصفيح للإلكترونيات المرنة والتغليف الذكي، مما يوفر فرصًا مربحة للاعبين المتخصصين.
العوامل الرئيسية عند اختيار آلة التصفيح
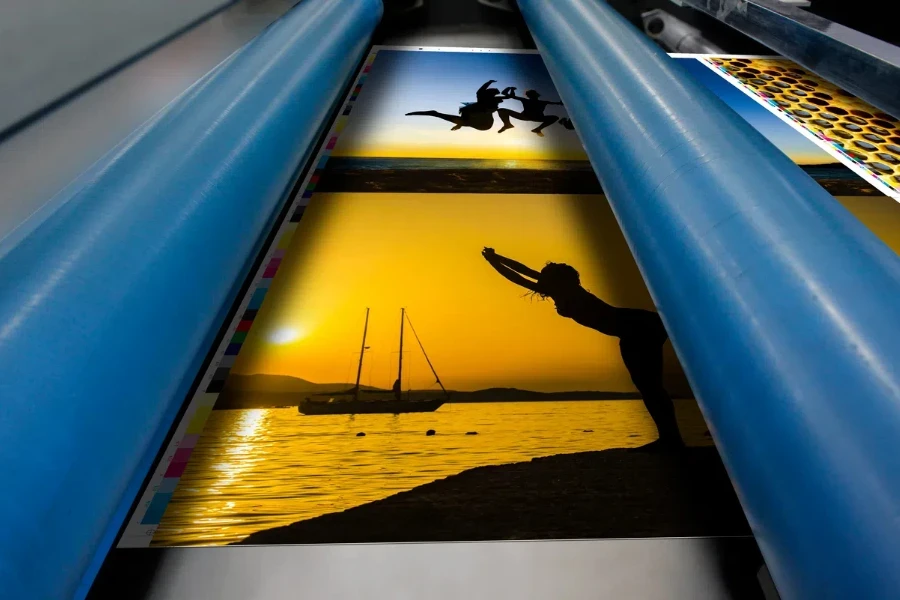
يعد اختيار آلة الترقق المناسبة أمرًا بالغ الأهمية لضمان نتائج عالية الجودة وكفاءة تشغيلية وموثوقية طويلة الأجل. يجب مراعاة العديد من العوامل الرئيسية، بما في ذلك الأنواع والأداء والمواصفات الفنية وسهولة الاستخدام والسعر. سيتم مناقشة كل من هذه العوامل بالتفصيل في الأقسام التالية.
أنواع آلات التصفيح
تتوفر آلات الترقق بأنواع مختلفة، كل منها مناسب لتطبيقات محددة. تشمل الأنواع الأساسية آلات الترقق الساخنة، وآلات الترقق الباردة، وآلات الترقق الكيسية.
آلات التصفيح الساخنة:تستخدم آلات الترقق الساخنة الحرارة لتنشيط المادة اللاصقة على فيلم الترقق، مما يؤدي إلى إنشاء رابط قوي مع المادة. هذه الآلات مثالية للوثائق والصور والعناصر التي تتطلب لمسة نهائية متينة. تضمن الحرارة التصاقًا آمنًا، وتوفر الحماية ضد الرطوبة والأوساخ والتآكل.
آلات التصفيح الباردة:تستخدم آلات الترقق البارد أغشية لاصقة حساسة للضغط، مما يجعلها مناسبة للمواد الحساسة للحرارة مثل الصور الفوتوغرافية وبعض الأعمال الفنية. تُستخدم هذه الآلات غالبًا للعناصر الكبيرة مثل الملصقات واللافتات. تعد آلات الترقق البارد أكثر أمانًا لأنها لا تنطوي على درجات حرارة عالية، مما يقلل من خطر الحروق وتلف المواد.
تصفيح الحقيبة:تستخدم آلات الترقق بالأكياس عادةً للأغراض الأصغر حجمًا مثل بطاقات الهوية والشارات. يتم وضع العنصر في كيس الترقق، ثم يتم تغذيته عبر الآلة. آلات الترقق بالأكياس متعددة الاستخدامات وسهلة الاستخدام، مما يجعلها شائعة الاستخدام في المكاتب والمدارس. وهي متوفرة في كل من الأنواع الساخنة والباردة، اعتمادًا على نوع اللاصق المستخدم في الأكياس.
الأداء والوظيفة
يتم تحديد أداء آلة الترقق من خلال عوامل مثل سرعة الترقق، وأقصى عرض للترقق، وجودة فيلم الترقق المستخدم. تتعامل آلات الترقق عالية الأداء مع أحجام أكبر من العمل بجودة ثابتة.
سرعة الترقق:يتم قياس سرعة الترقق بالبوصات في الدقيقة (IPM) أو الأمتار في الدقيقة (MPM). تعد الآلات الأسرع مفيدة للبيئات ذات الحجم الكبير مثل متاجر الطباعة ومرافق الإنتاج. بالنسبة للمكاتب الأصغر أو الاستخدام العرضي، قد تكون الآلة الأبطأ كافية.
الحد الأقصى لعرض التغليف:إن الحد الأقصى لعرض الورق الذي يمكن لآلة الترقق التعامل معه أمر ضروري، وخاصة بالنسبة للشركات التي تحتاج إلى ترقق مواد كبيرة الحجم. عادةً ما تتعامل آلات الترقق المكتبية القياسية مع عرض يصل إلى 12 بوصة، بينما يمكن لآلات الترقق الصناعية استيعاب عرض يصل إلى 27 بوصة أو أكثر. إن اختيار آلة تتناسب مع أحجام المستندات الخاصة بك يضمن الأداء والجودة الأمثل.
جودة فيلم الترقق:تؤثر جودة فيلم الترقق بشكل كبير على الناتج النهائي. تأتي الأفلام بسماكات مختلفة، تقاس بالملليمتر (الألف من البوصة)، تتراوح من 1.5 مليمتر إلى 10 مليمتر. توفر الأفلام الأكثر سماكة حماية أفضل ولكنها قد تتطلب آلات أكثر قوة. يعد ضمان التوافق بين الآلة والفيلم أمرًا حيويًا لتحقيق النتائج المرجوة.
بيانات المعدة
إن فهم المواصفات الفنية لآلة الترقق يمكن أن يساعد في اتخاذ قرار مستنير. تتضمن المواصفات الرئيسية التحكم في درجة الحرارة ونظام الأسطوانة ومتطلبات الطاقة.
التحكم في درجة الحرارة:إن التحكم الدقيق في درجة الحرارة أمر ضروري لآلات الترقق الساخنة لضمان تفعيل المادة اللاصقة بشكل صحيح دون إتلاف المادة. توفر الآلات المتقدمة إعدادات درجة حرارة قابلة للتعديل، مما يسمح للمستخدمين بتخصيص الحرارة لأنواع مختلفة من أفلام الترقق والمواد.
نظام الأسطوانة:يؤثر نظام الأسطوانة في آلة الترقق على تساوي الرقائق وأداء الآلة بشكل عام. تحتوي آلات الترقق عادةً على اثنتين إلى ست بكرات. يؤدي زيادة عدد البكرات بشكل عام إلى توزيع أفضل للضغط ونتائج أكثر سلاسة. قد تتميز الآلات المتطورة بأسطوانات ساخنة لتحسين تنشيط المادة اللاصقة وجودة التشطيب.
متطلبات الطاقة:تختلف متطلبات الطاقة بين الآلات، حيث تتطلب آلات الترقق الصناعية عادةً قدرًا أكبر من الطاقة بسبب حجمها الأكبر وقدراتها العالية على الأداء. يعد التأكد من قدرة منشأتك على دعم احتياجات الطاقة للآلة أمرًا بالغ الأهمية لتجنب المشكلات التشغيلية.
سهولة الاستعمال
تؤثر سهولة استخدام آلة الترقق على الإنتاجية ورضا المستخدم. تعد الميزات مثل أدوات التحكم سهلة الاستخدام ومتطلبات الصيانة وميزات السلامة من الاعتبارات المهمة.
الضوابط سهلة الاستخدام:تم تجهيز آلات التصفيح الحديثة بشاشات رقمية ولوحات تحكم بديهية، مما يجعلها سهلة التشغيل. تعمل الميزات مثل أوضاع التصفيح المحددة مسبقًا والإغلاق التلقائي ومؤشرات الخطأ على تعزيز قابلية الاستخدام وتقليل منحنى التعلم للمستخدمين الجدد.
متطلبات الصيانة:الصيانة الدورية ضرورية للحفاظ على آلات الترقق في حالة مثالية. تعمل الآلات ذات المكونات التي يسهل الوصول إليها وإرشادات الصيانة الواضحة على تبسيط هذه العملية. تأتي بعض الموديلات مع بكرات تنظيف ذاتية وأنظمة تحميل فيلم أوتوماتيكية، مما يقلل بشكل أكبر من وقت التوقف عن العمل وجهود الصيانة.
ميزات السلامة:تعتبر ميزات السلامة مثل واقيات الحرارة والإغلاق التلقائي وآليات تحرير التشويش أمرًا بالغ الأهمية، خاصة في البيئات التي يستخدم فيها مستخدمون متعددون الماكينة. تمنع هذه الميزات الحوادث وتضمن التشغيل الآمن، مما يحمي الماكينة والمستخدمين.
النطاق السعري والميزانية
تختلف أسعار آلات التصفيح بشكل كبير بناءً على نوعها وميزاتها وقدراتها على الأداء. إن تحديد الميزانية وفهم نطاق الأسعار يمكن أن يساعد في تضييق الخيارات.
آلات مستوى الدخول:تعتبر آلات التصفيح للمبتدئين مناسبة للاستخدام العرضي في المكاتب الصغيرة أو البيئات المنزلية. يتراوح سعر هذه الآلات عادةً بين 50 و200 دولار. وهي توفر ميزات أساسية وهي مصممة لمهام التصفيح ذات الحجم المنخفض إلى المتوسط.
آلات متوسطة المدى:توفر آلات الترقق متوسطة المدى، التي يتراوح سعرها بين 200 و1000 دولار، توازنًا جيدًا بين الأداء والتكلفة. وهي مثالية للشركات الصغيرة والمتوسطة الحجم التي تتطلب آلات ترقق موثوقة وفعالة لمختلف أحجام وأنواع المستندات.
آلات متطورة:تم تصميم آلات التصفيح عالية الجودة، والتي قد تكلف 1000 دولار أو أكثر، للاستخدام الشاق في البيئات الصناعية والتجارية. توفر هذه الآلات ميزات متقدمة وسرعات عالية في التصفيح والقدرة على التعامل مع المستندات كبيرة الحجم والأفلام السميكة. يمكن أن يكون الاستثمار في آلة عالية الجودة فعالاً من حيث التكلفة للشركات التي تحتاج إلى التصفيح بكميات كبيرة.
أحدث ميزات التكنولوجيا في آلات التصفيح
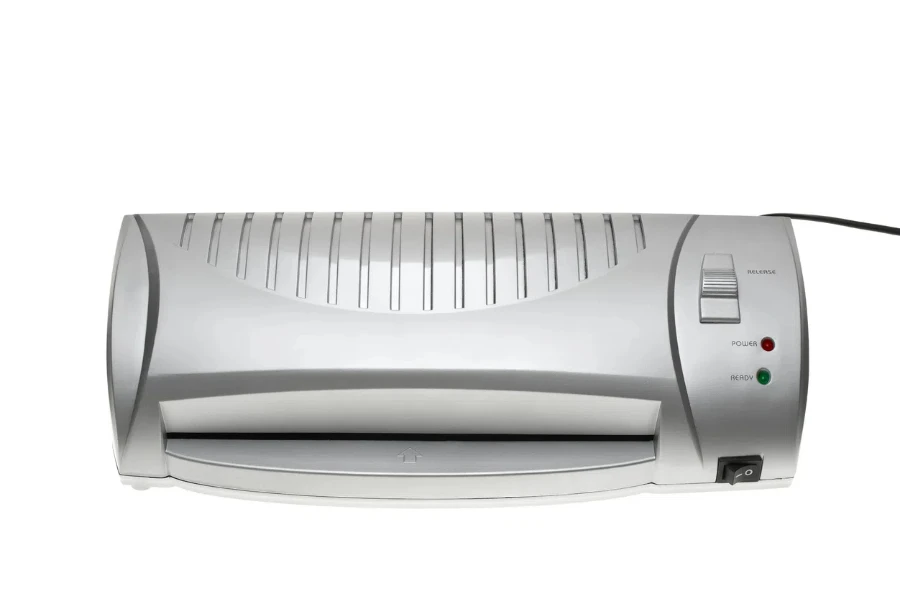
لقد أدى التقدم في التكنولوجيا إلى تطوير آلات التصفيح ذات الميزات المبتكرة التي تعمل على تعزيز الأداء والكفاءة والتنوع.
أنظمة التصفيح الآلية
تدمج أنظمة الترقق الآلية تقنيات متقدمة لتبسيط عملية الترقق. غالبًا ما تتميز هذه الأنظمة بآليات تحميل وتقطيع وتغذية الفيلم تلقائيًا، مما يقلل من التدخل اليدوي ويزيد من الإنتاجية. تعد الأنظمة الآلية مفيدة بشكل خاص في بيئات الإنتاج ذات الحجم الكبير حيث تكون السرعة والاتساق أمرًا بالغ الأهمية.
لوحات التحكم الذكية
تم تجهيز آلات الترقق الحديثة بلوحات تحكم ذكية توفر واجهات تعمل باللمس وإعدادات قابلة للبرمجة. تتيح هذه اللوحات للمستخدمين تخصيص معلمات الترقق مثل درجة الحرارة والسرعة وسمك الفيلم بسهولة. تتضمن بعض الطرز أيضًا أدوات تشخيص وتنبيهات صيانة، مما يضمن الأداء الأمثل ويقلل من وقت التوقف.
كفاءة إستهلاك الطاقة
تم تصميم آلات التصفيح الموفرة للطاقة لتقليل استهلاك الطاقة دون المساس بالأداء. تساعد الميزات مثل الإغلاق التلقائي وأوضاع توفير الطاقة في تقليل تكاليف التشغيل والتأثير البيئي. أصبحت النماذج الموفرة للطاقة تحظى بشعبية متزايدة مع سعي الشركات إلى تبني ممارسات مستدامة.
التوافق مع الأنظمة الرقمية
توفر آلات التصفيح المتوافقة مع الأنظمة الرقمية وظائف وقدرات تكامل محسّنة. يمكن لهذه الآلات الاتصال بأجهزة الكمبيوتر والأجهزة الرقمية الأخرى، مما يسمح بإدارة سير العمل بسلاسة. كما يتيح التوافق الرقمي المراقبة والتحكم عن بعد، مما يوفر مرونة وكفاءة أكبر في إدارة مهام التصفيح.
ميزات السلامة المحسنة
السلامة هي مصدر قلق بالغ الأهمية في أي مكان عمل، وآلات الترقق الحديثة مجهزة بميزات أمان معززة لحماية المشغلين. تضمن ميزات مثل الإغلاق التلقائي، وواقيات الحرارة، وآليات تحرير التشويش التشغيل الآمن. بالإضافة إلى ذلك، تتضمن بعض الآلات أجهزة استشعار تكتشف العوائق وتوقف عملية الترقق تلقائيًا لمنع الحوادث.
العوامل المؤثرة على متانة وعمر آلات التصفيح
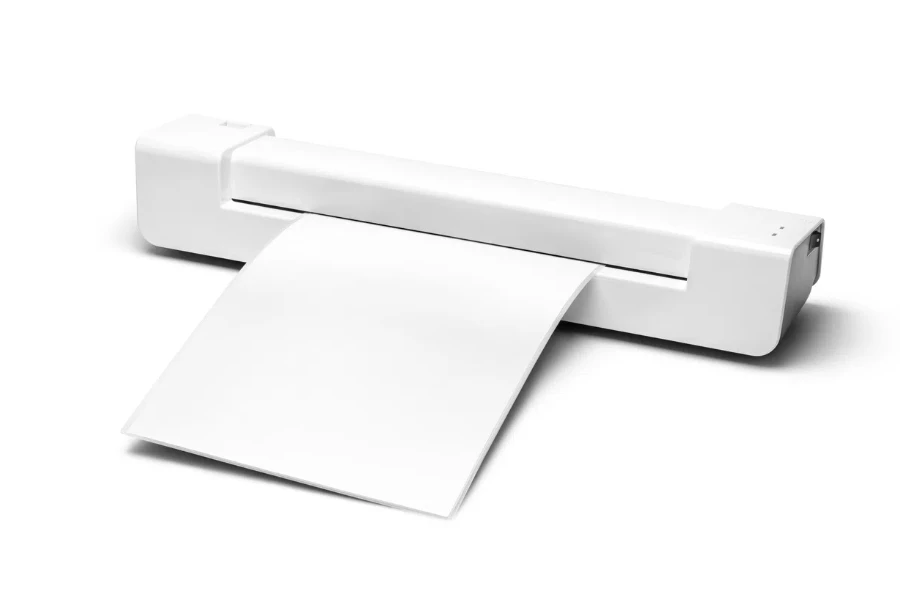
تتأثر متانة وعمر آلة التصفيح بعوامل مختلفة، بما في ذلك جودة البناء وممارسات الصيانة وأنماط الاستخدام.
بناء الجودة والمواد
تلعب جودة التصنيع والمواد المستخدمة في تصنيع آلة الترقق دورًا مهمًا في متانتها. فالآلات المصنوعة من مواد عالية الجودة مثل الفولاذ المقاوم للصدأ والبلاستيك المتين أكثر قدرة على تحمل الاستخدام المتكرر والظروف القاسية. ويمكن أن يؤدي الاستثمار في آلة جيدة التصنيع إلى توفير المال على المدى الطويل من خلال تقليل الحاجة إلى الإصلاحات والاستبدالات.
الصيانة العادية
الصيانة الدورية ضرورية لإطالة عمر آلة الترقق. ويشمل ذلك تنظيف الأسطوانات والتحقق من وجود أي تشويش في الفيلم والتأكد من أن جميع المكونات تعمل بشكل صحيح. إن اتباع إرشادات الصيانة الخاصة بالشركة المصنعة وجدولة الصيانة المهنية الدورية يمكن أن يمنع حدوث المشكلات ويطيل عمر تشغيل الآلة.
أنماط الاستخدام
تؤثر طريقة استخدام آلة الترقق أيضًا على متانتها. فالآلات التي تُستخدم ضمن قدرتها الموصى بها وللتطبيقات المقصودة أقل عرضة للتلف والتآكل. وقد يؤدي تحميل الآلة فوق طاقتها أو استخدامها مع مواد غير مناسبة إلى تلفها قبل الأوان وتقليل عمرها الافتراضي. ويمكن أن يساعد الالتزام بإرشادات الاستخدام وتجنب الإفراط في الاستخدام في الحفاظ على أداء الآلة وطول عمرها.
ضمان الامتثال التنظيمي ومعايير السلامة
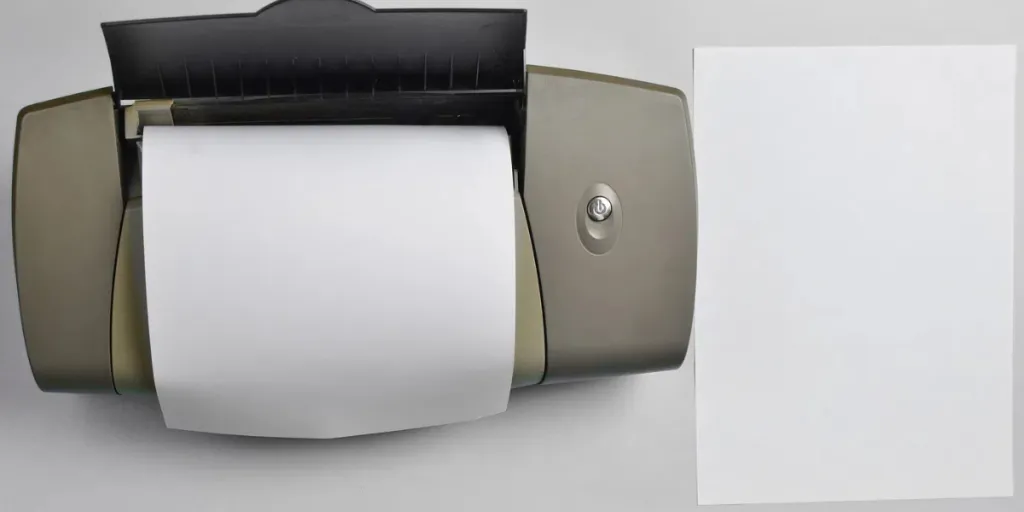
يعد الامتثال للمعايير التنظيمية وإرشادات السلامة أمرًا بالغ الأهمية للتشغيل الآمن والفعال لآلات الترقق.
المعايير التنظيمية
يجب أن تتوافق آلات الترقق مع معايير تنظيمية مختلفة لضمان السلامة والجودة. قد تتضمن هذه المعايير شهادات من منظمات مثل Underwriters Laboratories (UL)، واللجنة الكهروتقنية الدولية (IEC)، واللجنة الأوروبية للمعايير الكهروتقنية (CENELEC). يضمن الامتثال لهذه المعايير أن الآلة تلبي معايير السلامة والأداء والبيئة المحددة.
إرشادات السلامة
يعد الالتزام بإرشادات السلامة أمرًا ضروريًا لمنع الحوادث وضمان سلامة المشغلين. يوفر المصنعون تعليمات السلامة وأدلة التشغيل التي تحدد الاستخدام السليم والصيانة وإجراءات استكشاف الأخطاء وإصلاحها. يمكن أن يساعد تدريب المشغلين على هذه الإرشادات وإجراء عمليات تدقيق السلامة بشكل منتظم في الحفاظ على بيئة عمل آمنة.
المتطلبات الخاصة بالصناعة
قد يكون لدى بعض الصناعات متطلبات محددة لآلات التصفيح، مثل تلك المستخدمة في تغليف المواد الغذائية والأدوية والإلكترونيات. قد تتضمن هذه المتطلبات ميزات أمان إضافية ومعايير نظافة ومواد متخصصة. يعد التأكد من أن آلة التصفيح تلبي المعايير الخاصة بالصناعة أمرًا ضروريًا للامتثال والأداء الأمثل.
افكار اخيرة
يتضمن اختيار آلة التصفيح المناسبة مراعاة عوامل مختلفة مثل الأنواع والأداء والمواصفات الفنية وسهولة الاستخدام والسعر. كما أن فهم أحدث ميزات التكنولوجيا وضمان المتانة والالتزام بالامتثال التنظيمي ومعايير السلامة أمر بالغ الأهمية لاتخاذ قرار مستنير. من خلال تقييم هذه العوامل بعناية، يمكن للشركات اختيار آلة التصفيح التي تلبي احتياجاتها المحددة وتعزز كفاءتها التشغيلية.