Bandsaw blade welders are used by hobbyists, workmen, and manufacturers to join new or broken bandsaw blades. With a range of bandsaw blade welders available with differing technology and output capacity, this tool is able to optimize bandsaw blade welding processes for a whole range of business sizes.
Read on to discover how to select the best bandsaw blades for your buyers in 2025!
Table of Contents
What are bandsaw blade welders?
Advantages of using bandsaw blade welders
Types of bandsaw blade welders
Key components and processes of a bandsaw blade welder
Choosing the right bandsaw blade welder
Innovation and trends in bandsaw blade technology
Conclusion
What are bandsaw blade welders?
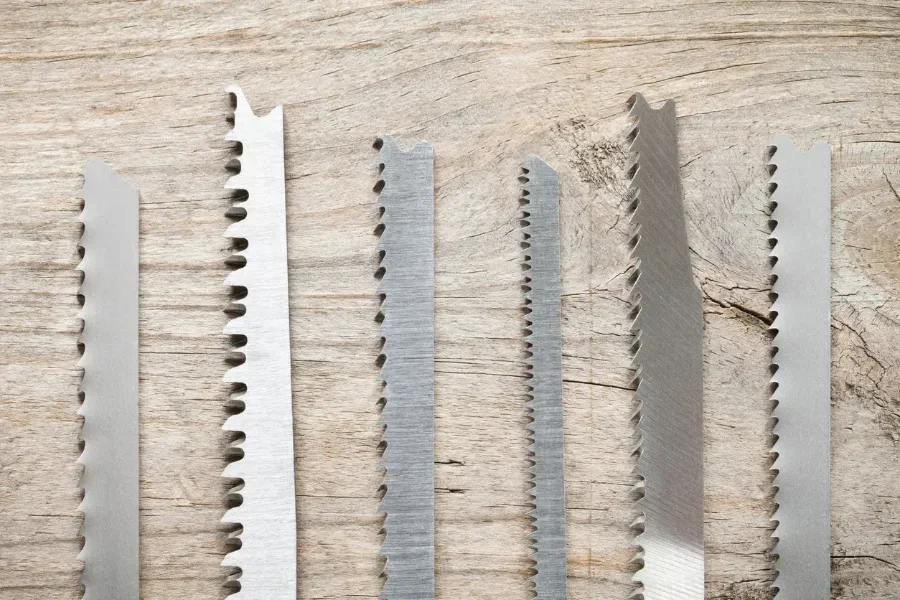
Bandsaw blade welders are essential tools used to join new or broken bandsaw blades. They function by driving a heating electrical current through the two ends of a bandsaw blade to seamlessly weld them together, creating a continuous, strong joint. After the welding process, the bandsaw blade welder will anneal the blade to create a durable yet flexible metal that cuts with precision. This makes them indispensable in industries where fast, continuous, and precise cutting is needed, including metalworking and woodworking, as well as in the lumber and automotive sectors.
Advantages of using bandsaw blade welders
Buying a quality bandsaw blade welder gives the owner significant advantages over using a different product.
Enhanced blade durability
Broken bandsaw blades welded with a bandsaw blade welder are as strong as new blades, even when the weld was carried out as a repair. This ensures a longer life for every blade and doesn’t compromise on cutting performance.
Cost savings from in-house welding
As well as the cost savings from having blades with a longer life, owners of a bandsaw blade welder benefit from cutting the downtime and costs involved with having to buy new saw blades or outsource the repairs. This not only reduces costs, but also improves efficiency.
Improved cutting precision
The saw blades that are properly held in place by the welding machine are aligned and finished to create a blade capable of providing clean, precise cuts. This means more efficient production and reduced material waste.
Types of bandsaw blade welders
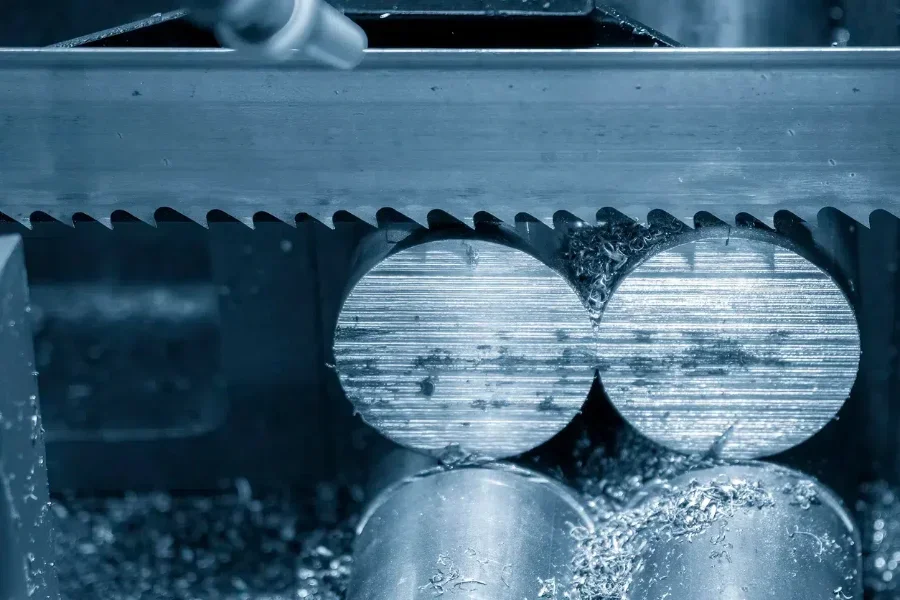
Bandsaw blade welders come in a variety of sizes and prices. Depending on the output a person or business requires, as well as the speed and efficiency of that output, a person may be inclined to buy one type of bandsaw blade welder or another.
Manual bandsaw blade welders
Manual bandsaw welders mean the welding of the bandsaw blade is carried out manually, from start to finish. This means the owner can adjust the blade during the welding process for more flexibility and precision — as long as they have the right technique.
Manual bandsaw blade welders are smaller to their more automated counterparts and are more cost-effective too, however, they are slower and require more work on the part of the operator. They are ideal for bandsaw blade repairs or small-scale production and are used by hobbyists working on DIY projects, professionals requiring flexibility in their blade welds, or small shop owners who specialize in welding-type machinery and tools.
Semi-automatic bandsaw blade welders
Semi-automated bandsaw blade welders offer a good balance between manual control for adjustments and the consistency and efficiency offered by automation. With semi-automated bandsaw blade welders, the operator will need to initiate the welding process but the welder will carry out the welding, annealing, and finishing independently. Semi-automated bandsaw blade welders are optimal purchases for those requiring consistency for midsize production capacity.
Automatic bandsaw blade welders
Automated bandsaw blade welders are larger machines that take care of the welding process from start to finish. Although larger and more costly than its counterparts, this type of bandsaw blade welder will create consistent welds at speed, making it an ideal choice for high production capacity buyers.
Key components and processes of a bandsaw blade welder
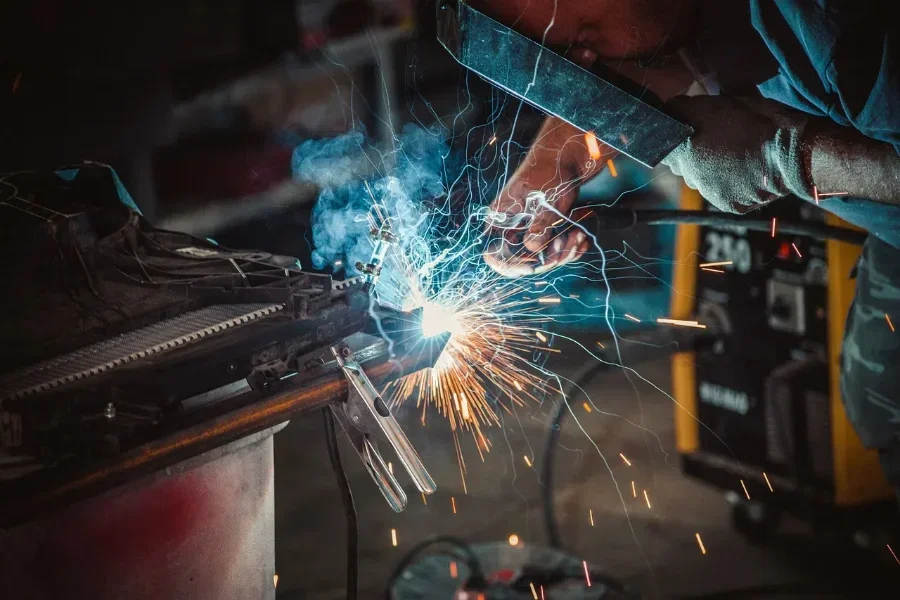
Welding clamps and jaws
The clamps and jaws hold the broken or new bandsaw blades in place to ensure there is no movement during the welding process. These bandsaw blade welder parts ensure that the weld is carried out smoothly and efficiently at speed.
Power source and control panel
Welding with a bandsaw blade welder requires heat via electrical current, meaning that an electric power source is essential. The control panel is used by the operator to set the current, pressure, and timing in order to weld different material types and blade thicknesses. The control panel may offer more or less functionality depending on the level of automation of the machine.
Flash butt welding mechanism
The flash butt mechanism is the most commonly used system in bandsaw blade welding. It uses pressure to force the blade ends together while the electric current heats and welds them into a joint. This mechanism is able to create the strong, consistent joints needed to withstand the stress of cutting hard materials.
Annealing device
The annealing device is the element of the bandsaw blade welder that undertakes the annealing process — a heat treatment carried out on the blade after the welding has been finished. The annealing process brings flexibility to the newly-joined blade, reduces blade hardness, and stops it from becoming brittle, as these elements can cause the breaking of the blade.
Grinding and finishing tools
As with any material that has undergone work, it must be smoothed off and polished, and this is where the grinding and finishing tools come in. These tools grind bandsaw blades and then smooth and polish them to remove any imperfections and ensure the new blade is ready for use or sale.
Choosing the right bandsaw blade welder
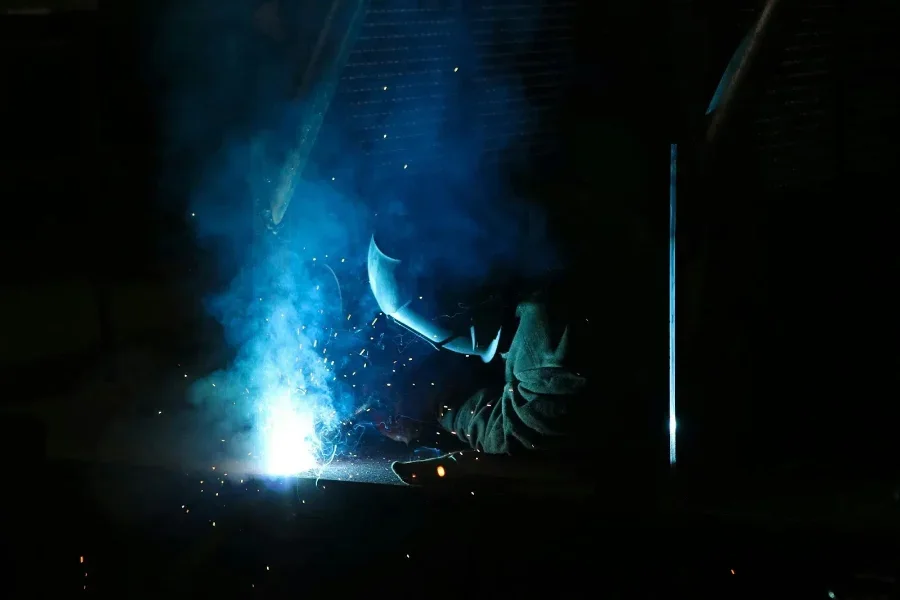
When choosing the right bandsaw blade welders, it is important to remember that each type may have different control panel settings, different sized clamps, different output capacity, and more. So, before buying a bandsaw blade welder, it’s important to do some research and narrow down exactly what type would be the best fit.
Considerations based on material
Bandsaw blades come in a variety of materials, including carbon steel, bi-metals, and carbide-tipped blades, and each of these have their own set of welding requirements. Consider the welder’s ability to cut different material types and compare this to the jobs carried out before making a purchase.
Factors based on production volume
Bandsaw blade welders can be used by different people, from manufacturers to hobbyists, meaning required production capacity will not be the same. This will also translate to the cost of the machine, so it is important to compare the output size to ensure the right bandsaw blade welder is being bought for the job.
Key features to look out for
Consider the type of work being done before exploring the features offered by different bandsaw blade welders. For example, a hobbyist may not need the built-in annealing and grinding capabilities, as this might be something they prefer to do manually. By buying a bandsaw blade welding machine that does not have this feature, they will save on cost and space in their workshop. Likewise, buying this same bandsaw blade welder for a high-output manufacturer could have disastrous consequences on efficiency and speed of production.
Leading brands and models
Buying bandsaw blade welders from leading brands and models is a good way to ensure quality customer service and after-care, however, with proper research, great models at lower prices can be found from lesser-known brands too.
Innovation and trends in bandsaw blade technology
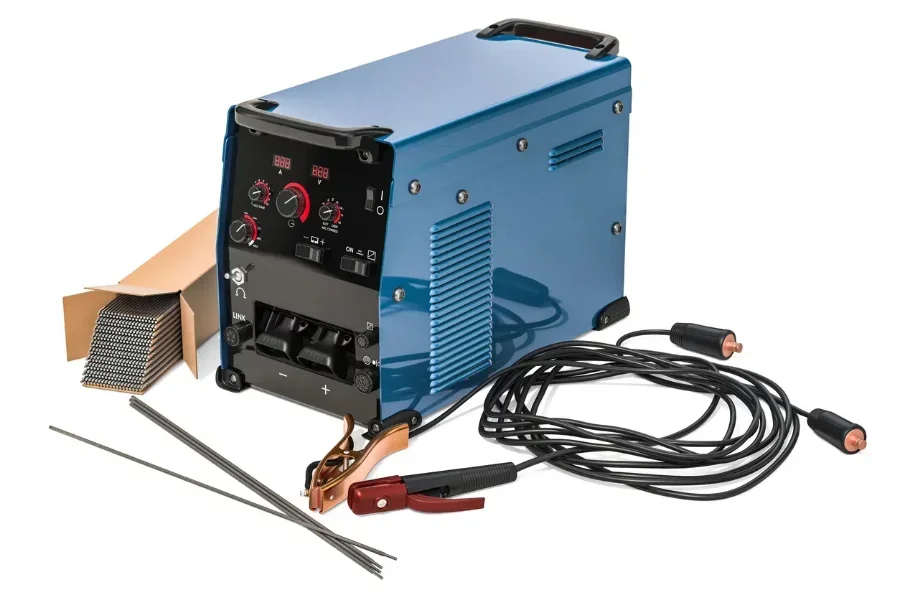
As with any machine, the technology behind bandsaw blade welders is evolving to keep up with the market and offer better capacity and features for more efficient and precise bandsaw blade welding.
Advances in automated welding systems
As bandsaw blade welders become fully automated, faster, and more efficient, the possibility of human error is reduced and productivity is increased. This trend will only increase as bandsaw blade welders begin to incorporate AI and smart technology.
Integration of smart technology and IoT
Some bandsaw blade welders for high output capacity have now integrated IoT and smart technology to enable remote monitoring for improved efficiency and reduced downtime. As further integrations are made down this avenue, the industries may see a reduced need for human intervention.
Eco-friendly welding solutions
The manufacturing industries are increasingly focusing on more sustainable solutions to tackle emissions. Within bandsaw blade welding machines, solutions include better welding efficiency to reduce waste, and solutions to reduce energy consumption. In addition to this, manufacturers are leaning toward green energy to power their welding machines.
Conclusion
Bandsaw blade welders play a crucial role in a variety of industries, reducing costs and downtime, increasing blade strength and cutting precision, and streamlining operations. Understanding the different components, types, and innovations in bandsaw blade welding machines will help guide buyers to the right machine for their needs and improve their understanding of how these tools will make their operations run smoother. As these industries grow and smart technologies become increasingly embedded, the demand for bandsaw blade welders will rise too, and by understanding these essential tools now, hobbyists, workers, and manufacturers alike will be ahead of the trends.