The MIG welder market is booming, fueled by rising demand across automotive, construction, and manufacturing industries for precision and efficiency. With the global electric welding machine market projected to reach USD 9.35 billion by 2030 at a CAGR of 7.81%, this article explores the key drivers behind this growth, leading manufacturers, technological advancements, and critical purchasing considerations to guide professional buyers in making strategic decisions.
Table of Contents:
Understanding the MIG Welder Market
Key Features to Look for in a MIG Welder
Types of MIG Welders and Their Applications
Latest Trends in MIG Welding Technology
Budget Considerations and Cost Analysis
Making the Final Decision
Understanding the MIG Welder Market
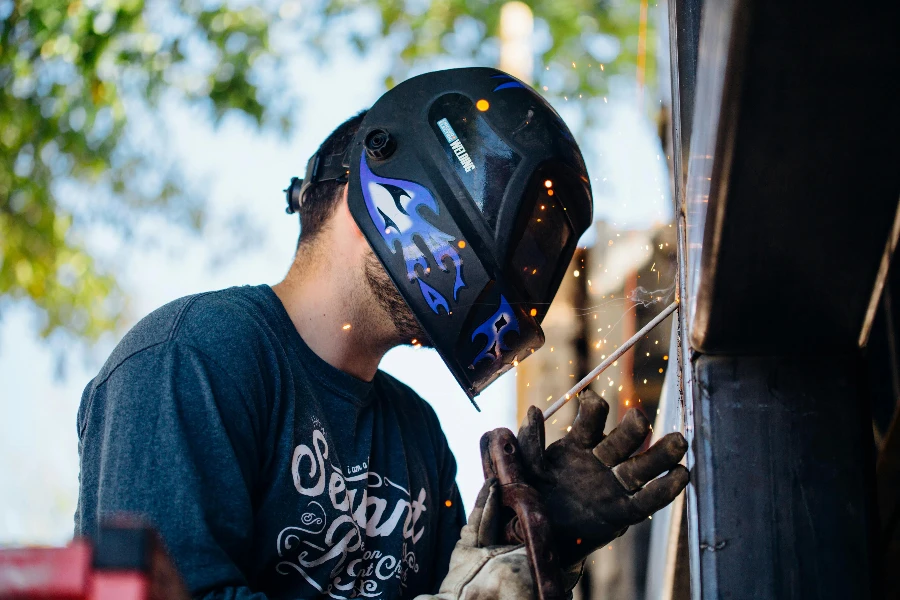
Introduction
As of late 2024, the global electric welding machine market has seen significant growth, reaching USD 5.93 billion, up from USD 5.52 billion in 2023. This growth is driven by the increasing demand for precision welding in various industries, including automotive, construction, and manufacturing. The market is expected to continue its upward trajectory, with projections indicating a CAGR of 7.81%, reaching USD 9.35 billion by 2030. This article delves into the specifics of the MIG welder market, exploring global demand, key players, and regional variations.
Global Demand and Growth Projections
The global demand for MIG welders is on the rise, driven by their versatility and efficiency in welding various metals. In 2024, the electric welding machine market, which includes MIG welders, was valued at USD 5.93 billion. This market is projected to grow at a CAGR of 7.81%, reaching USD 9.35 billion by 2030. The increasing need for durable and reliable structures in infrastructure projects worldwide is a significant driver of this growth.
The automotive industry is a major consumer of MIG welders, with the sector’s demand expected to grow at a CAGR of 4.3% over the next eight years. The construction industry also significantly contributes to the market, with ongoing infrastructure projects requiring high-quality welding solutions. Additionally, the shipping industry relies heavily on MIG welders for repair and manufacturing, further boosting market demand.
Technological advancements in welding equipment, such as the development of automated and semi-automated MIG welders, are expected to enhance market growth. These innovations improve welding precision and efficiency, making them attractive to various industries. The trend towards automation in welding processes is also anticipated to drive market expansion in the coming years.
Key Players and Manufacturers
The MIG welder market is highly competitive, with several key players dominating the industry. Leading companies include Lincoln Electric Holdings, Inc., Miller Electric Mfg. LLC, and ESAB Corporation. These companies are known for their innovative welding solutions and extensive product portfolios, catering to various industrial needs.
Lincoln Electric Holdings, Inc. is a prominent player, offering a wide range of MIG welders known for their durability and performance. The company’s focus on research and development has led to the introduction of advanced welding technologies, enhancing its market position. Similarly, Miller Electric Mfg. LLC has made significant strides in the market with its Millermatic series, which includes the recently launched Millermatic 142 MIG welder, designed for both novice and experienced welders.
ESAB Corporation is another key player, known for its high-quality welding equipment and solutions. The company’s commitment to innovation and customer satisfaction has helped it maintain a strong market presence. Other notable manufacturers include Fronius International GmbH, Panasonic Corporation, and Kemppi Oy, each contributing to the market with their unique product offerings and technological advancements.
Regional Market Variations
The MIG welder market exhibits significant regional variations, driven by differing industrial needs and economic conditions. In the Americas, the market is robust, particularly in the United States, where the automotive, construction, and manufacturing sectors drive demand. The U.S. market alone was estimated at USD 1.4 billion in 2023, with a strong emphasis on advanced welding technologies to improve efficiency and productivity.
In the Asia-Pacific region, countries like China, India, and Japan are experiencing rapid market growth due to expansive infrastructure projects and booming automotive industries. The region’s market is expected to grow at an impressive CAGR of 6.5%, reaching USD 1.6 billion by 2030. Innovations in welding technology and increased investments in regional research and development have produced high-efficiency and cost-effective welding solutions.
Europe also represents a significant market for MIG welders, driven by the region’s advanced automotive and aerospace industries. The market in Europe emphasizes high-quality and precision welding technologies, with a surge in demand for energy-efficient and environmentally sustainable solutions. The Middle East and Africa are witnessing growth driven by infrastructural developments and the oil and gas sector, while Africa’s demand is fueled by construction and infrastructural projects.
Key Features to Look for in a MIG Welder
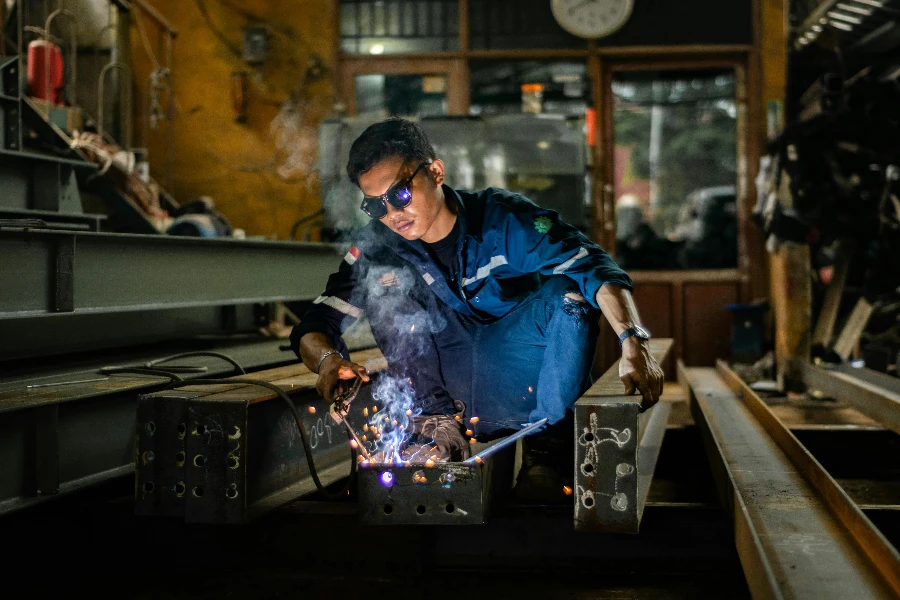
Power Output and Voltage Requirements
When selecting a MIG welder, power output and voltage requirements are critical factors to consider. MIG welders typically operate on either 110V or 220V power sources, with industrial models often requiring higher voltage for more demanding applications. The power output, measured in amperes, determines the welder’s capability to handle different metal thicknesses and types.
For light to medium-duty welding tasks, a MIG welder with a power output range of 30-140 amps is usually sufficient. However, for heavy-duty industrial applications, welders with power outputs exceeding 200 amps are preferred. The ability to adjust the voltage settings allows for greater control over the welding process, ensuring optimal performance and weld quality.
Advanced MIG welders come equipped with features such as auto-set controls, which automatically adjust the voltage and wire feed speed based on the material thickness and type. This simplifies the setup process and enhances efficiency, making these welders suitable for both novice and experienced users. The Millermatic 142, for example, features advanced auto-set controls, making it a versatile choice for various applications.
Duty Cycle and Efficiency
The duty cycle of a MIG welder is another essential feature to consider, as it indicates the welder’s operational efficiency and performance. The duty cycle is expressed as a percentage and represents the amount of time the welder can operate continuously within a 10-minute period before needing to cool down. For instance, a welder with a 60% duty cycle at 200 amps can weld continuously for 6 minutes before requiring a 4-minute rest period.
Higher duty cycles are crucial for industrial applications where prolonged welding sessions are common. Welders with higher duty cycles reduce downtime and increase productivity, making them ideal for manufacturing and construction projects. Efficiency is also a key consideration, as energy-efficient welders help lower operational costs and reduce environmental impact.
Modern MIG welders incorporate advanced cooling systems and inverter technology to enhance duty cycles and efficiency. Inverter-based welders are more compact and lightweight, offering better energy efficiency compared to traditional transformer-based models. These features make them suitable for a wide range of applications, from light fabrication to heavy industrial welding.
Wire Feed Speed and Control
Wire feed speed is a critical parameter in MIG welding, as it directly affects the quality and consistency of the weld. The wire feed speed, measured in inches per minute (IPM), determines the rate at which the welding wire is fed into the weld pool. Proper control of the wire feed speed ensures a stable arc and consistent weld penetration.
MIG welders with adjustable wire feed speed settings allow users to fine-tune the welding process based on the material type and thickness. Advanced models feature digital displays and controls, providing precise adjustments and real-time feedback. This level of control is essential for achieving high-quality welds, especially when working with different metals and alloys.
Some MIG welders also come with synergic control, which automatically adjusts the wire feed speed and voltage settings based on the selected welding parameters. This feature simplifies the welding process and reduces the likelihood of errors, making it easier for operators to achieve consistent results. The Millermatic 142, for example, offers synergic control, enhancing its versatility and ease of use.
Portability and Weight
Portability and weight are important considerations, especially for welders who need to move their equipment frequently. Portable MIG welders are designed to be lightweight and compact, making them easy to transport and maneuver in various work environments. These welders are ideal for on-site repairs, maintenance tasks, and small-scale fabrication projects.
Portable MIG welders typically weigh between 20 to 50 pounds, with some models featuring built-in handles or wheels for added convenience. Despite their compact size, these welders offer robust performance and can handle a wide range of welding tasks. The use of inverter technology in portable welders further reduces weight and enhances energy efficiency.
For industrial applications, where mobility is less of a concern, heavier MIG welders with higher power outputs and duty cycles are preferred. These welders are often mounted on carts or integrated into welding stations, providing a stable and efficient setup for continuous welding operations. The choice between portability and weight ultimately depends on the specific needs and requirements of the welding project.
Safety Features and Certifications
Safety is paramount in welding operations, and MIG welders come equipped with various safety features to protect operators and ensure compliance with industry standards. Key safety features include thermal overload protection, which prevents the welder from overheating by automatically shutting down the machine when it reaches a critical temperature.
Other important safety features include voltage reduction devices (VRD), which reduce the open-circuit voltage to a safe level when the welder is not in use, and ground fault circuit interrupters (GFCI), which protect against electrical shocks. Additionally, some MIG welders feature built-in fume extraction systems to minimize exposure to harmful welding fumes and gases.
Certifications such as CE, UL, and CSA indicate that the welder meets specific safety and performance standards set by regulatory bodies. These certifications provide assurance that the equipment has undergone rigorous testing and complies with industry regulations. When selecting a MIG welder, it is essential to consider these safety features and certifications to ensure a safe and reliable welding experience.
Types of MIG Welders and Their Applications
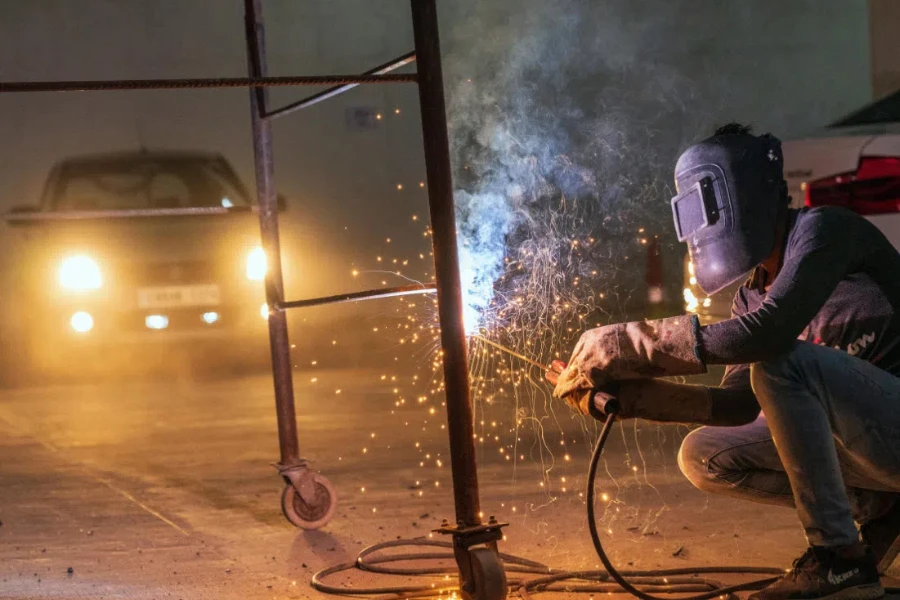
Gas Metal Arc Welding (GMAW)
Gas Metal Arc Welding (GMAW) is a versatile and widely used welding process. It employs a continuous wire feed as an electrode and an inert or semi-inert gas mixture to shield the weld from contamination. This method is known for its high deposition rates and efficiency in welding both thin and thick materials.
GMAW is particularly effective for welding aluminum, stainless steel, and carbon steel. The process is commonly used in automotive manufacturing, shipbuilding, and construction industries. Its ability to produce clean, strong welds with minimal post-weld cleanup makes it a preferred choice for many applications.
The equipment for GMAW includes a power source, wire feed unit, welding gun, and shielding gas supply. The power source can be either constant voltage (CV) or constant current (CC), depending on the specific requirements of the welding task. The choice of shielding gas, such as argon or carbon dioxide, also plays a crucial role in the quality of the weld.
Flux-Cored Arc Welding (FCAW)
Flux-Cored Arc Welding (FCAW) is a variation of GMAW that uses a tubular wire filled with flux. This process can be performed with or without an external shielding gas, depending on the type of flux-cored wire used. FCAW is known for its high deposition rates and ability to weld thicker materials in a single pass.
FCAW is widely used in heavy equipment manufacturing, structural steel construction, and shipbuilding. The process is particularly advantageous in outdoor and windy conditions where shielding gas might be blown away. The flux within the wire provides additional protection against contamination and helps stabilize the arc.
The equipment setup for FCAW is similar to GMAW, with a power source, wire feed unit, and welding gun. However, the choice of flux-cored wire is critical, as it determines the need for external shielding gas and influences the mechanical properties of the weld. Proper selection of wire and settings ensures optimal performance and weld quality.
Synergic MIG Welders
Synergic MIG welders are advanced welding machines that automatically adjust welding parameters based on the selected material and wire type. These welders simplify the welding process by providing pre-programmed settings for various applications, reducing the need for manual adjustments. This feature is particularly beneficial for less experienced welders.
Synergic MIG welders are used in industries where precision and consistency are crucial, such as aerospace, automotive, and high-end manufacturing. The ability to quickly switch between different welding programs enhances productivity and ensures high-quality welds. These welders are also equipped with advanced features like pulse welding, which reduces spatter and improves weld appearance.
The key components of synergic MIG welders include a digital control panel, power source, wire feed unit, and welding gun. The digital interface allows for easy selection of welding programs and real-time monitoring of welding parameters. This technology not only improves weld quality but also reduces the learning curve for new operators.
Latest Trends in MIG Welding Technology
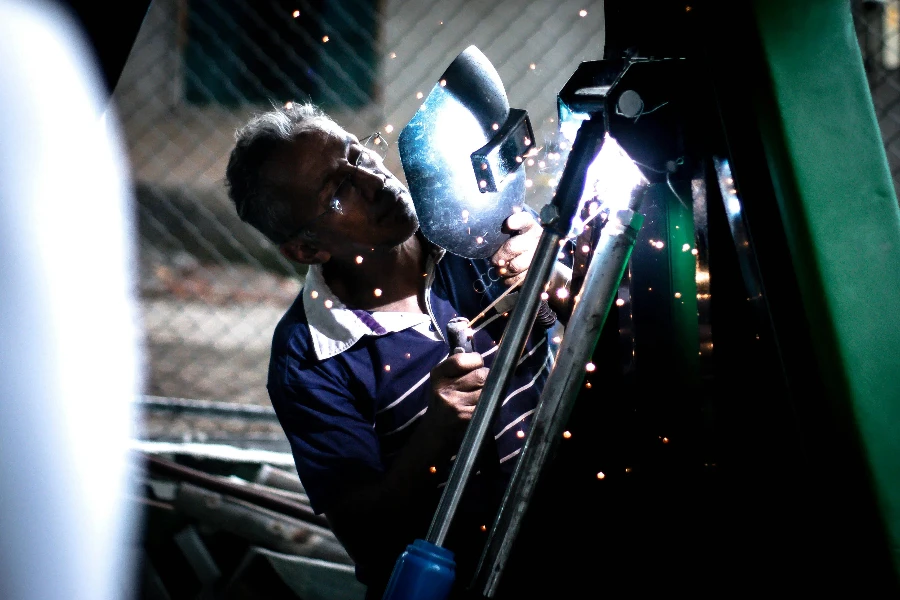
Advancements in Automation
Automation in MIG welding has seen significant advancements, particularly with the integration of robotic welding systems. These systems offer high precision, repeatability, and efficiency, making them ideal for large-scale production environments. Robotic welders can operate continuously, reducing downtime and increasing throughput.
The use of collaborative robots, or cobots, is also on the rise. Cobots are designed to work alongside human operators, enhancing productivity while ensuring safety. They are equipped with sensors and advanced control systems that allow them to adapt to various welding tasks. This flexibility makes them suitable for small to medium-sized enterprises looking to automate their welding processes.
Automated welding systems are increasingly incorporating machine learning algorithms to optimize welding parameters. These algorithms analyze data from previous welds to predict and adjust settings for future welds, improving overall quality and consistency. This trend towards smart automation is expected to continue, driven by the need for higher efficiency and reduced production costs.
Integration with IoT and Smart Technologies
The integration of Internet of Things (IoT) and smart technologies in MIG welding is transforming the industry. IoT-enabled welding machines can collect and transmit data in real-time, providing valuable insights into the welding process. This data can be used for predictive maintenance, quality control, and process optimization.
Smart welding systems are equipped with sensors that monitor various parameters such as temperature, voltage, and current. This information is analyzed to detect anomalies and prevent potential issues before they occur. The ability to remotely monitor and control welding operations enhances operational efficiency and reduces downtime.
The adoption of augmented reality (AR) in welding training is another emerging trend. AR-based training programs provide a simulated welding environment where trainees can practice without the risks associated with live welding. This technology accelerates the learning process and improves skill acquisition, making it a valuable tool for workforce development.
Budget Considerations and Cost Analysis
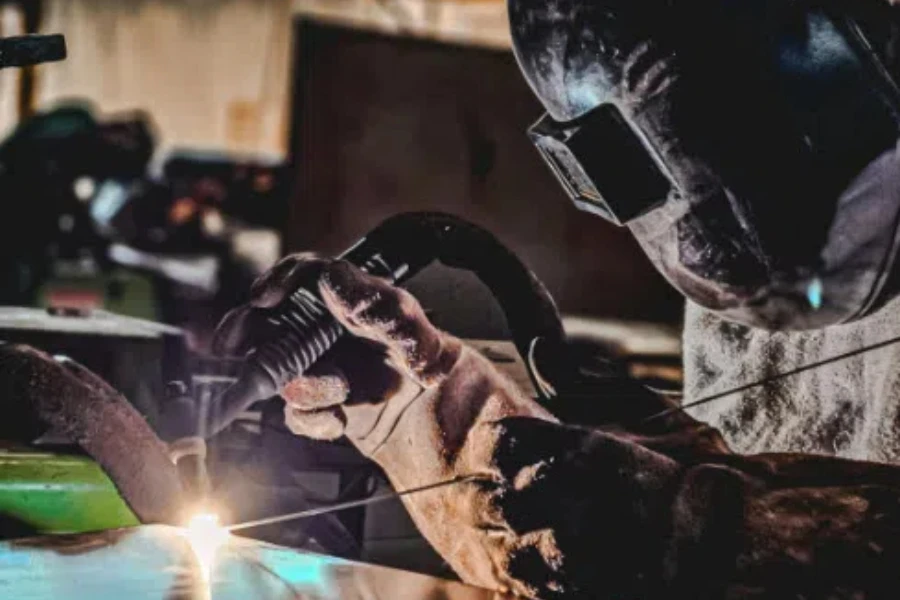
Initial Purchase Cost vs Long-term Investment
When evaluating MIG welders, it’s essential to consider both the initial purchase cost and the long-term investment. High-quality welders may have a higher upfront cost, but they often offer better performance, durability, and lower maintenance requirements. Investing in a reliable machine can lead to significant cost savings over time.
Lower-cost welders might seem attractive initially, but they can incur higher maintenance and repair costs. These machines may also have shorter lifespans and lower efficiency, leading to increased operational costs. It’s crucial to assess the total cost of ownership, including potential downtime and productivity losses, when making a purchasing decision.
Financing options and leasing programs are available for businesses looking to manage their cash flow. These options can make it easier to acquire high-quality welding equipment without a significant upfront investment. Evaluating the financial impact of different purchasing options helps in making an informed decision that aligns with the company’s budget and operational needs.
Maintenance and Operating Costs
Maintenance and operating costs are critical factors in the overall cost analysis of MIG welders. Regular maintenance ensures the longevity and optimal performance of the welding equipment. This includes routine inspections, cleaning, and replacement of consumables such as contact tips and nozzles.
Operating costs also include the consumption of shielding gas, welding wire, and electricity. Efficient welders with advanced features like pulse welding can reduce material waste and energy consumption. Implementing a preventive maintenance program can minimize unexpected breakdowns and extend the lifespan of the equipment.
Training for operators is another important consideration. Properly trained operators can maximize the efficiency and lifespan of the welding equipment. Investing in training programs can reduce the likelihood of operator errors, improve weld quality, and enhance overall productivity.
Warranty and After-Sales Support
Warranty and after-sales support are crucial aspects of purchasing MIG welders. A comprehensive warranty provides peace of mind and protects the investment in case of defects or malfunctions. It’s important to understand the terms and conditions of the warranty, including coverage duration and what components are included.
After-sales support includes technical assistance, spare parts availability, and repair services. Reliable support ensures that any issues are promptly addressed, minimizing downtime and maintaining productivity. Choosing a supplier with a strong reputation for customer service can significantly impact the overall ownership experience.
Some manufacturers offer extended warranty options and service contracts. These programs can provide additional coverage and support, further safeguarding the investment. Evaluating the after-sales support and warranty options is essential for ensuring long-term satisfaction and reliability of the welding equipment.
Making the Final Decision
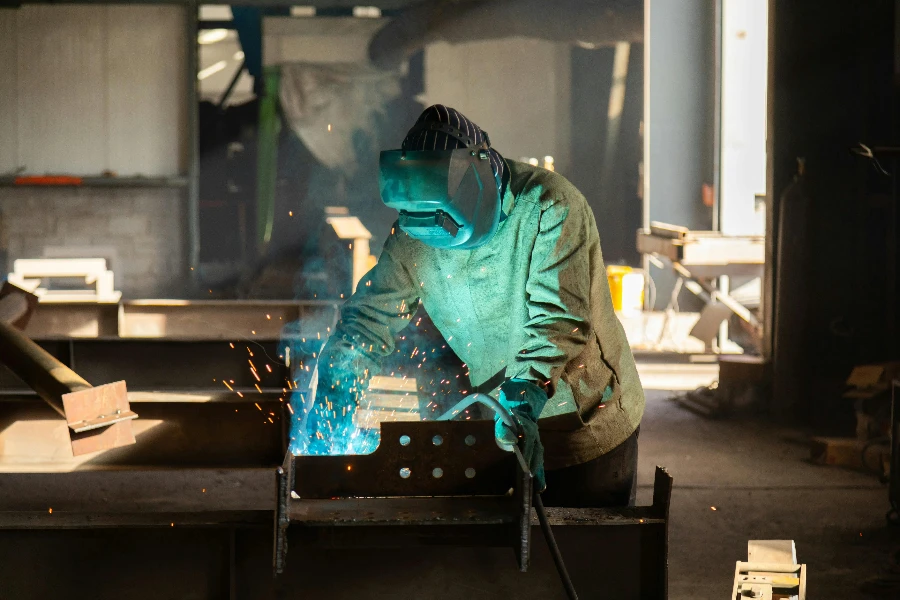
In conclusion, selecting the right MIG welder involves a comprehensive evaluation of various factors. Consider the specific welding applications, budget constraints, and long-term investment to make an informed decision.