In 2025, the global screen printing market is projected to reach USD 12.01 billion, driven by technological advancements and increasing demand across various sectors.
Table of Contents:
– Understanding the Screen Printing Industry
– Key Considerations for Selecting a Screen Printer
– Evaluating Different Types of Screen Printers
– Assessing Costs and Return on Investment
– Future Trends in Screen Printing Technology
– Making the Final Decision
Understanding the Screen Printing Industry
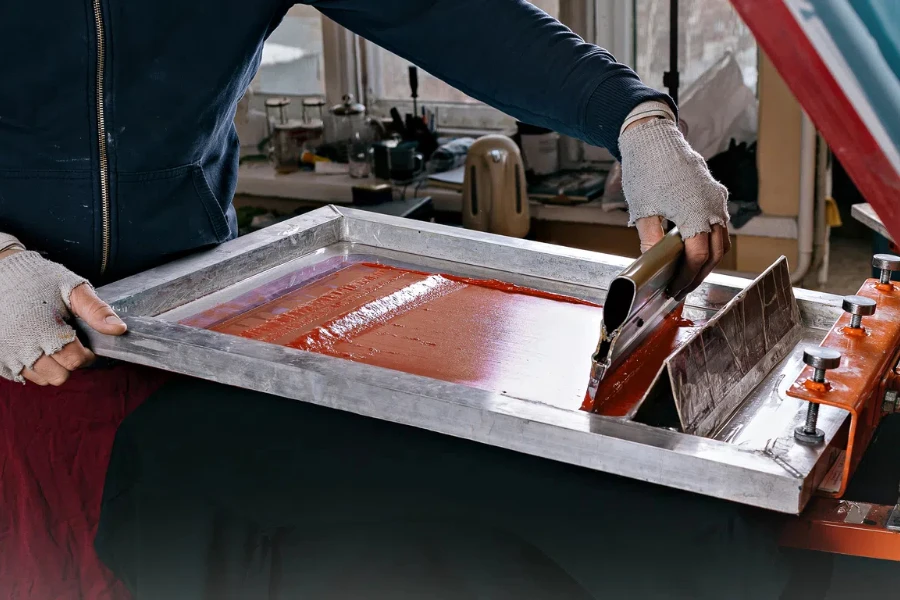
Market Size and Growth
The screen printing industry is experiencing significant growth, driven by advancements in technology and increasing demand across various sectors. As of 2024, the global screen printing market is worth approximately USD 11.34 billion, with projections indicating a rise to USD 12.01 billion by 2025, reflecting a compound annual growth rate (CAGR) of 5.9%. This growth is attributed to the expanding applications of screen printing in textiles, electronics, and packaging industries, among others.
The market’s expansion is further supported by the increasing adoption of screen printing in the advertising and promotional sectors. The versatility of screen printing, which allows for printing on a wide range of materials including textiles, ceramics, and glass, is a key factor driving its popularity. Additionally, the rise of e-commerce and the need for customized packaging solutions are contributing to the market’s growth, with the packaging sector alone expected to see a significant increase in demand for screen-printed labels and packaging materials.
Technological advancements in screen printing equipment are also playing a crucial role in market growth. Innovations such as automated screen printers and the integration of digital technologies are enhancing the efficiency and precision of screen printing processes. These advancements are expected to continue driving the market forward, with the global screen printing market projected to reach USD 15.08 billion by 2028, growing at a CAGR of 5.9% from 2024 to 2028.
Key Players and Manufacturers
The screen printing market is characterized by the presence of several key players and manufacturers who are driving innovation and competition. Major companies in the industry include M&R Printing Equipment, Anatol Equipment Manufacturing Co., and ROQ International. These companies are known for their extensive product portfolios and continuous investment in research and development to introduce advanced screen printing solutions.
M&R Printing Equipment, for instance, is renowned for its high-quality automatic and manual screen printing presses, which are widely used in the textile industry. The company’s focus on innovation has led to the development of state-of-the-art equipment that offers enhanced print quality and efficiency. Similarly, Anatol Equipment Manufacturing Co. is a leading manufacturer of screen printing machines, known for its robust and reliable equipment that caters to both small and large-scale printing operations.
ROQ International, another prominent player, specializes in automated screen printing machines that are designed to meet the demands of high-volume production. The company’s advanced technology and commitment to sustainability have positioned it as a key player in the global screen printing market. These manufacturers, along with others, are continuously striving to improve their product offerings and expand their market presence through strategic partnerships and acquisitions.
Technological Advancements
Technological advancements are at the forefront of the screen printing industry’s growth, with innovations aimed at improving print quality, efficiency, and sustainability. One of the significant advancements in the industry is the development of automated screen printing machines. These machines are equipped with advanced features such as automatic screen alignment, digital controls, and high-speed printing capabilities, which significantly enhance production efficiency and reduce labor costs.
The integration of digital technologies in screen printing is another notable trend. Digital screen printing combines the benefits of traditional screen printing with digital printing technology, allowing for high-resolution prints and greater design flexibility. This hybrid approach is gaining popularity, particularly in the textile and apparel industries, where there is a growing demand for customized and intricate designs.
Sustainability is also a key focus area in the screen printing industry, with manufacturers developing eco-friendly inks and printing processes. Water-based and UV-curable inks are becoming increasingly popular due to their lower environmental impact compared to traditional solvent-based inks. Additionally, advancements in ink formulations and curing technologies are enabling faster drying times and improved print durability, further driving the adoption of sustainable screen printing solutions.
Key Considerations for Selecting a Screen Printer
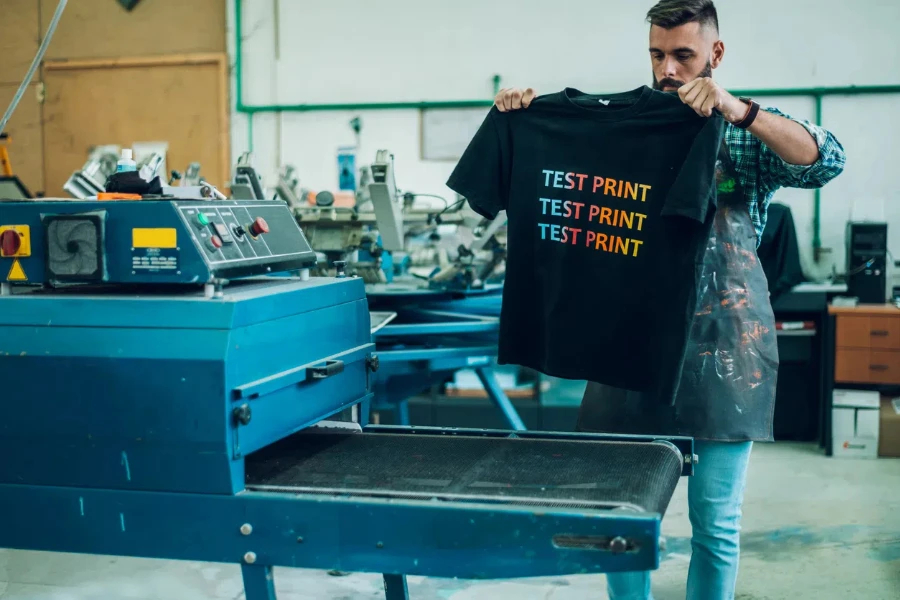
Print Quality and Precision
When selecting a screen printer, print quality and precision are paramount considerations. High-quality screen printers are designed to produce sharp, vibrant, and consistent prints, which are essential for applications in textiles, electronics, and packaging. The resolution of the screen printer, measured in dots per inch (DPI), is a critical factor that determines the level of detail and clarity in the printed output. For instance, a screen printer with a resolution of 1200 DPI is capable of producing fine details and smooth gradients, making it suitable for high-end graphic applications.
The type of ink used also plays a significant role in determining print quality. Water-based and UV-curable inks are known for their excellent color vibrancy and durability. These inks are particularly suitable for printing on textiles and other porous materials, as they provide good adhesion and resistance to fading. Additionally, the mesh count of the screen, which refers to the number of threads per inch, affects the amount of ink deposited on the substrate. A higher mesh count results in finer details and smoother prints, making it ideal for intricate designs.
Precision in screen printing is achieved through advanced features such as automatic screen alignment and digital controls. Automated screen printers are equipped with sensors and software that ensure accurate registration of colors and patterns, reducing the risk of misalignment and improving overall print quality. These features are particularly important for multi-color printing and complex designs, where precision is crucial to achieving the desired results.
Production Speed and Efficiency
Production speed and efficiency are critical factors to consider when selecting a screen printer, especially for high-volume printing operations. Automated screen printers are designed to offer high-speed printing capabilities, with some models capable of producing up to 1,000 prints per hour. This level of productivity is essential for meeting tight deadlines and large orders, particularly in industries such as textiles and packaging.
The efficiency of a screen printer is also influenced by its setup and changeover times. Modern screen printers are equipped with features such as quick-change screens and automated cleaning systems, which minimize downtime and streamline the printing process. For example, a screen printer with an automated screen cleaning system can reduce the time required for cleaning and preparation, allowing for faster transitions between print jobs and increased overall productivity.
Energy efficiency is another important consideration, as it directly impacts operational costs. Screen printers with energy-efficient components, such as LED curing systems, consume less power and generate less heat compared to traditional curing methods. This not only reduces energy costs but also extends the lifespan of the equipment. Additionally, energy-efficient printers contribute to sustainability efforts by minimizing the environmental impact of the printing process.
Machine Durability and Maintenance
The durability and maintenance requirements of a screen printer are crucial factors that affect its long-term performance and cost-effectiveness. High-quality screen printers are built with robust materials and components that can withstand the rigors of continuous use. For instance, printers with stainless steel frames and corrosion-resistant parts are more durable and less prone to wear and tear, ensuring reliable performance over time.
Regular maintenance is essential to keep screen printers in optimal condition and prevent unexpected breakdowns. Automated maintenance features, such as self-cleaning printheads and automated lubrication systems, help reduce the need for manual intervention and extend the lifespan of the equipment. These features also contribute to consistent print quality by preventing issues such as clogged nozzles and uneven ink distribution.
Manufacturers often provide comprehensive maintenance and support services, including regular inspections, software updates, and technical assistance. Investing in a screen printer from a reputable manufacturer with a strong support network can help minimize downtime and ensure smooth operation. Additionally, having access to genuine replacement parts and consumables is important for maintaining the printer’s performance and avoiding compatibility issues.
Evaluating Different Types of Screen Printers
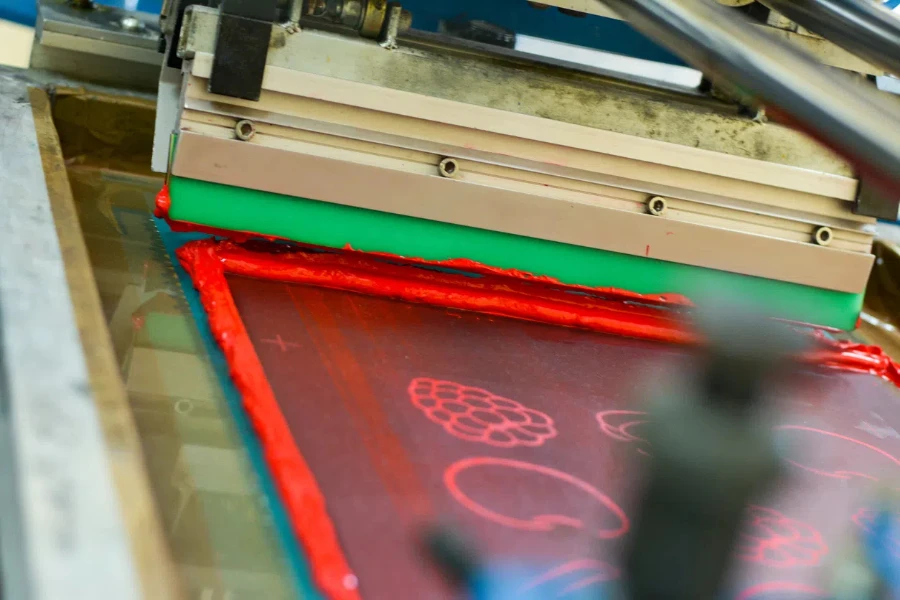
Manual Screen Printers
Manual screen printers are the most basic type of screen printing equipment, operated entirely by hand. These printers are ideal for small-scale operations and businesses with limited budgets. Manual screen printers offer flexibility and control, allowing operators to adjust the pressure and speed of the printing process to achieve the desired results. They are commonly used for printing on textiles, promotional items, and small batches of custom products.
One of the main advantages of manual screen printers is their affordability. They have a lower initial cost compared to automated and semi-automatic printers, making them accessible to startups and small businesses. Additionally, manual screen printers are relatively easy to set up and maintain, with fewer mechanical components that require regular servicing. However, manual screen printing can be labor-intensive and time-consuming, limiting its suitability for high-volume production.
Despite their limitations, manual screen printers are valued for their versatility and ability to produce high-quality prints. They are particularly useful for printing on irregularly shaped or delicate items that require careful handling. With the right techniques and materials, manual screen printers can achieve excellent print quality and durability, making them a popular choice for artisanal and custom printing applications.
Semi-Automatic Screen Printers
Semi-automatic screen printers combine manual and automated features, offering a balance between flexibility and efficiency. These printers are equipped with automated mechanisms for tasks such as screen alignment, ink application, and curing, while still requiring manual intervention for loading and unloading substrates. Semi-automatic screen printers are suitable for medium-scale production and businesses looking to increase their output without fully transitioning to automated systems.
The primary advantage of semi-automatic screen printers is their ability to improve production speed and consistency. Automated features such as precise screen alignment and controlled ink application reduce the risk of errors and ensure uniform print quality. This makes semi-automatic printers ideal for multi-color printing and complex designs that require accurate registration. Additionally, semi-automatic printers can handle a wider range of substrates and print sizes compared to manual printers.
While semi-automatic screen printers offer increased efficiency, they also come with higher initial costs and maintenance requirements. The presence of automated components means that regular servicing and technical support are necessary to keep the equipment in optimal condition. However, the investment in semi-automatic screen printers can be justified by the increased productivity and improved print quality they provide, making them a valuable asset for growing businesses.
Fully Automatic Screen Printers
Fully automatic screen printers are designed for high-volume production and large-scale operations. These printers are equipped with advanced automation features that handle the entire printing process, from loading substrates to curing and unloading finished products. Fully automatic screen printers offer the highest level of efficiency and consistency, making them ideal for industries such as textiles, electronics, and packaging.
The key advantage of fully automatic screen printers is their ability to produce large quantities of prints with minimal manual intervention. Automated features such as robotic arms, conveyor systems, and digital controls ensure precise and repeatable results, reducing the risk of errors and increasing overall productivity. Fully automatic printers are capable of handling complex designs and multi-color prints with ease, making them suitable for demanding applications.
However, fully automatic screen printers come with significant initial costs and require regular maintenance to ensure optimal performance. The complexity of these machines means that technical expertise is necessary for setup, operation, and troubleshooting. Despite these challenges, the benefits of fully automatic screen printers, including increased production speed, consistent print quality, and reduced labor costs, make them a worthwhile investment for large-scale operations.
Specialty Screen Printers
Specialty screen printers are designed for specific applications and substrates that require unique printing techniques. These printers are used for printing on items such as ceramics, glass, electronics, and promotional products. Specialty screen printers are equipped with features tailored to the requirements of the specific application, such as high-temperature curing systems for ceramics or precision alignment mechanisms for electronic components.
One of the main advantages of specialty screen printers is their ability to produce high-quality prints on challenging substrates. For example, screen printers designed for ceramics can handle the high temperatures required for firing, ensuring durable and vibrant prints. Similarly, printers for electronics are equipped with fine mesh screens and precise alignment systems to achieve the intricate details needed for circuit boards and other components.
Specialty screen printers often come with higher costs and require specialized knowledge for operation and maintenance. However, their ability to meet the unique demands of specific applications makes them an essential tool for businesses in niche markets. Investing in specialty screen printers can provide a competitive advantage by enabling the production of high-quality, customized products that meet the needs of discerning customers.
Assessing Costs and Return on Investment
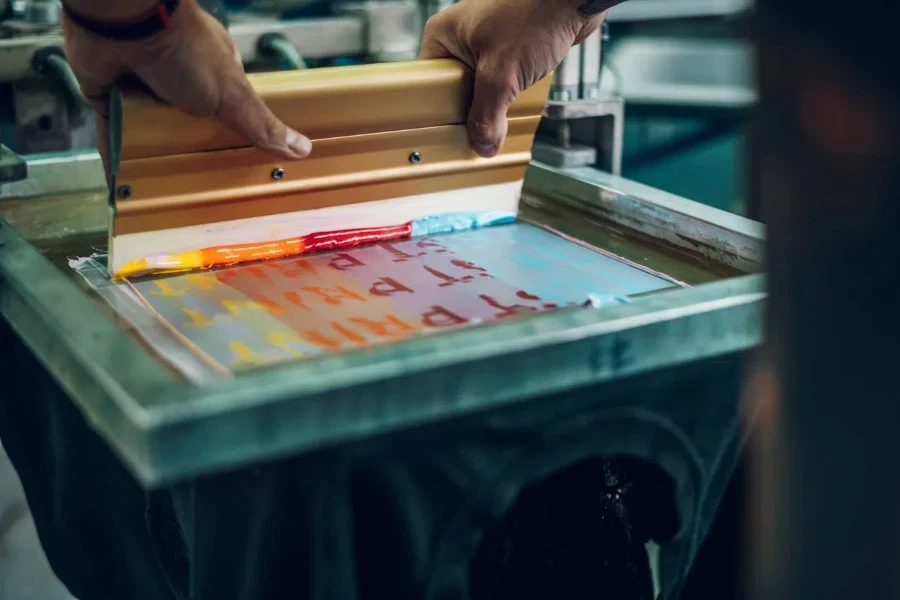
Initial Purchase Price
The initial purchase price of screen printing equipment can vary significantly based on the type and capabilities of the machine. For instance, a basic manual screen printing press may cost around $1,000, while an advanced automatic press can exceed $50,000. It’s crucial to consider the specific needs of your business, such as production volume and print quality, when evaluating the initial investment. Additionally, some manufacturers offer financing options, which can help mitigate the upfront cost and spread the expense over time.
Operating Costs
Operating costs for screen printing equipment include consumables like ink, screens, and squeegees, as well as utilities such as electricity and water. For example, the cost of ink can range from $30 to $100 per gallon, depending on the type and quality. Regular maintenance is also essential to ensure optimal performance and longevity of the equipment, which can add to the overall operating expenses. Furthermore, labor costs should be factored in, especially if the process involves manual intervention or requires skilled operators.
Longevity and Depreciation
The longevity of screen printing equipment is influenced by factors such as build quality, usage frequency, and maintenance practices. High-quality machines from reputable manufacturers can last over a decade with proper care. Depreciation is another critical aspect, as it affects the equipment’s resale value and financial planning. Typically, screen printing equipment depreciates at a rate of 10-20% per year. Understanding the depreciation schedule can help businesses plan for future upgrades and replacements, ensuring continuous production efficiency.
Future Trends in Screen Printing Technology
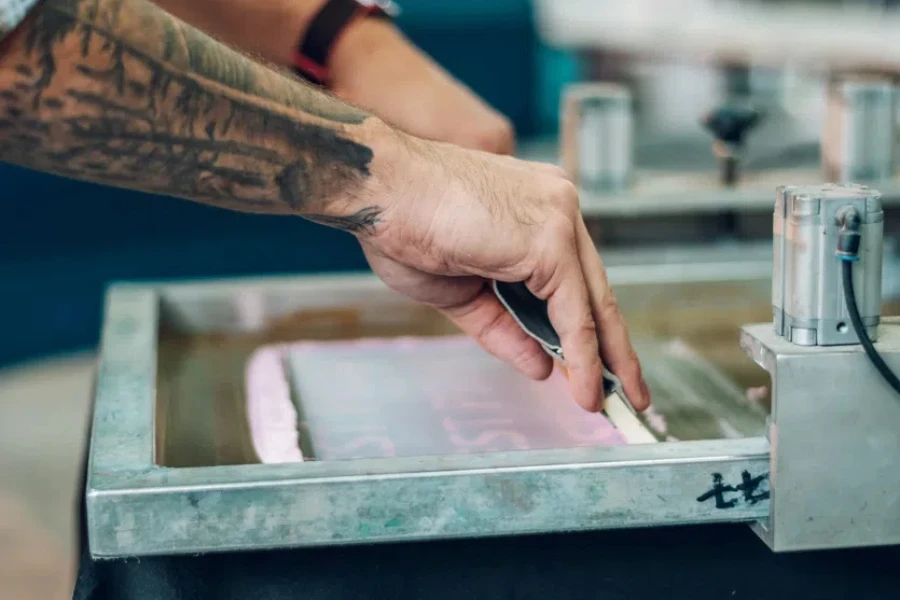
Digital Integration
Digital integration is revolutionizing the screen printing industry, offering enhanced precision and efficiency. Hybrid screen printing machines that combine traditional methods with digital printing capabilities are becoming increasingly popular. These machines allow for intricate designs and variable data printing, which were previously challenging with conventional screen printing. Additionally, advancements in software and automation are streamlining workflows, reducing setup times, and minimizing human error, leading to higher productivity and consistency.
Eco-Friendly Solutions
The demand for eco-friendly solutions in screen printing is on the rise, driven by environmental regulations and consumer preferences. Water-based inks, which are less harmful than traditional plastisol inks, are gaining traction due to their lower environmental impact. Moreover, innovations in screen reclamation processes are reducing water and chemical usage, making the entire printing process more sustainable. Companies are also exploring biodegradable and recyclable materials for screens and other consumables, further contributing to eco-friendly practices.
Making the Final Decision
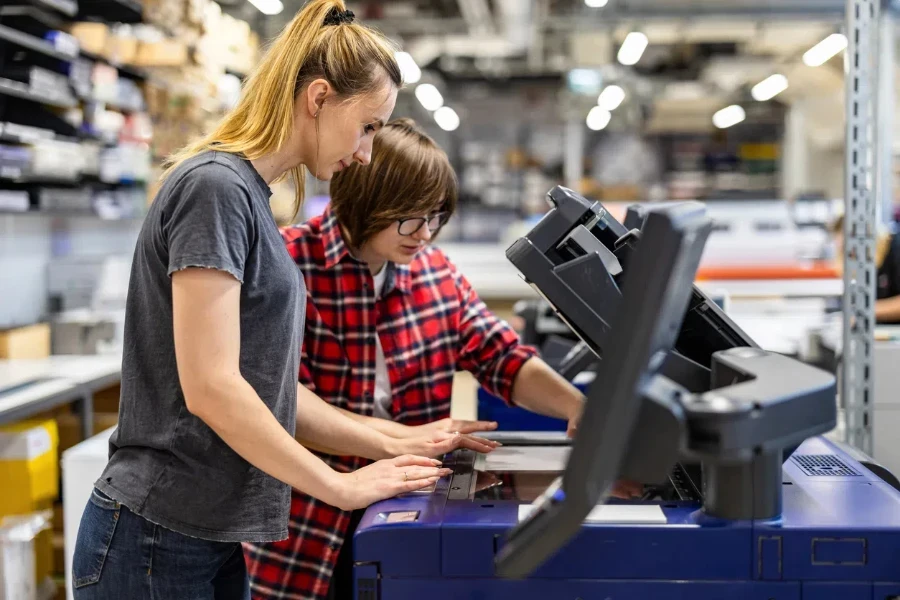
When making the final decision on screen printing equipment, it’s essential to balance cost, performance, and future-proofing. Evaluate the total cost of ownership, including initial purchase, operating expenses, and potential upgrades. Consider the specific needs of your business, such as production volume, print quality, and customization capabilities. Additionally, stay informed about emerging trends and technologies to ensure your investment remains relevant and competitive in the evolving market.