Mit der Einführung eines autonom fahrenden Transportfahrzeugs im Presswerk treibt das BMW Group Werk Regensburg die Digitalisierung und Automatisierung seiner Fertigungsprozesse voran und macht damit einen weiteren Schritt hin zur digitalen und intelligent vernetzten BMW iFACTORY.
Der fahrerlose Plattformwagen mit Elektroantrieb übernimmt künftig autonom den innerbetrieblichen Transport von Presswerkzeugen und Stahlplatinen für die Pressenlinien mit einer Nutzlast von bis zu 55 Tonnen. Mittels Sensortechnik navigiert das Transportsystem mit einer Geschwindigkeit von vier Kilometern pro Stunde zielgenau und vollautonom durch die Produktionshallen des Regensburger Presswerks. Laut BMW gibt es diese Lösung derzeit weltweit nicht.
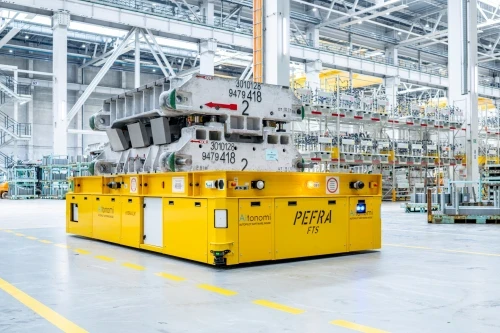
Wir sehen großes Potenzial im Einsatz autonomer Logistiklösungen. Mit dem emissionsfreien Elektrofahrzeug können wir die Fertigungsprozesse in unserem Presswerk noch effizienter und flexibler gestalten sowie Transportwege und Durchlaufzeiten verkürzen. Das steigert nicht nur die Produktivität, sondern spart auch Energie und verbessert die Arbeitssicherheit unserer Mitarbeiter.
—Tobias Müller, Leiter Instandhaltung Presswerk im BMW Group Werk Regensburg
Das neue fahrerlose Transportfahrzeug nutzt die innovative LiDAR-Technologie (Light Detection And Ranging) des Herstellers Pefra. In Verbindung mit Kameras und Radarsensoren überwachen sie ihre Umgebung, helfen bei der Orientierung, Hinderniserkennung und Abstandsmessung und sorgen so für mehr Sicherheit und Effizienz in einem komplexen Umfeld – sei es auf stark befahrenen Straßen oder in automatisierten Industrieumgebungen wie im Presswerk der BMW Group in Regensburg. Beim 3D-LiDAR-Verfahren wird die Umgebung mithilfe vieler einzelner optischer Abstandsmessungen gescannt, die anschließend zu einem 3D-Streudiagramm der vom LiDAR-Sensor erfassten Umgebung kombiniert werden.
Das Presswerk im BMW Group Werk Regensburg verarbeitet arbeitstäglich rund 1,100 Tonnen Stahl, das entspricht einer Tagesproduktion von 131,000 Pressteilen. Der Produktionsumfang umfasst 113 verschiedene Karosseriebauteile. Neben Struktur- und Verstärkungsteilen formt das Presswerk aus bis zu 4.5 Meter langen Stahlblechen auch große Außenhautteile wie Seitenrahmen, Türaußenhäute und Motorhauben.
Die verarbeiteten Stahlwalzen können bis zu 33 Tonnen schwer sein. Die leistungsstärkste der vier Pressenlinien im Regensburger Presswerk ist mit Highspeed-Servotechnik ausgestattet und damit eine der schnellsten Pressen der Welt. Ihre Presskraft beträgt 9,000 Tonnen – das entspricht dem Gewicht des Eiffelturms. Die Presse erreicht dabei eine Taktrate von bis zu 23 Hüben pro Minute. Die im Presswerk gefertigten Karosserieteile werden anschließend im nahegelegenen Karosseriebau des BMW Group Werks Regensburg zu Fahrzeugkarosserien montiert.
Im Presswerk Regensburg fallen jährlich rund 80,000 Tonnen Verschnitt an, die in einem geschlossenen Kreislauf recycelt werden. Im ersten Schritt werden die Verschnitte in einer Recyclingpresse zu 40 mal 40 Zentimeter großen und 220 Kilogramm schweren Stahlwürfeln geformt. Diese werden dann an den Stahllieferanten zurückgeschickt und dort zu sogenanntem Sekundärstahl verarbeitet.
Durch den Einsatz von Sekundärstahl im Presswerk Regensburg der BMW Group werden zwei Tonnen CO eingespart2 pro Tonne Stahl im Vergleich zur Produktion von Primärstahl. Dies reduziert den CO2 Der CO160,000-Fußabdruck wird um rund XNUMX Tonnen pro Jahr reduziert. Um Mitarbeiter, Anwohner und Umwelt vor Lärmemissionen und Erschütterungen zu schützen, sind die Produktions- und Recyclinganlagen im Presswerk Regensburg mit Schallschutz ausgestattet. Zudem arbeiten alle Produktionsanlagen vibrationsarm.
Quelle aus Green Car Kongress
Haftungsausschluss: Die oben dargelegten Informationen werden von greencarcongress.com unabhängig von Chovm.com bereitgestellt. Chovm.com gibt keine Zusicherungen und Gewährleistungen hinsichtlich der Qualität und Zuverlässigkeit des Verkäufers und der Produkte.