The diamond grinder wheel market has seen significant growth since 2025, driven by innovations and increasing industrial applications. This article delves into the market dynamics, key selection criteria, and the latest technological advancements. Professional buyers will find valuable insights to make informed purchasing decisions, ensuring optimal performance and compliance with safety standards.
Table of Contents:
- Marktübersicht
– In-Depth Market Analysis
– Key Factors When Selecting a Diamond Grinder Wheel
– Understanding the Applications of Diamond Grinder Wheels
– Innovations in Diamond Grinder Wheel Technology
– Ensuring Safety and Compliance with Diamond Grinder Wheels
- Fazit
Marktübersicht
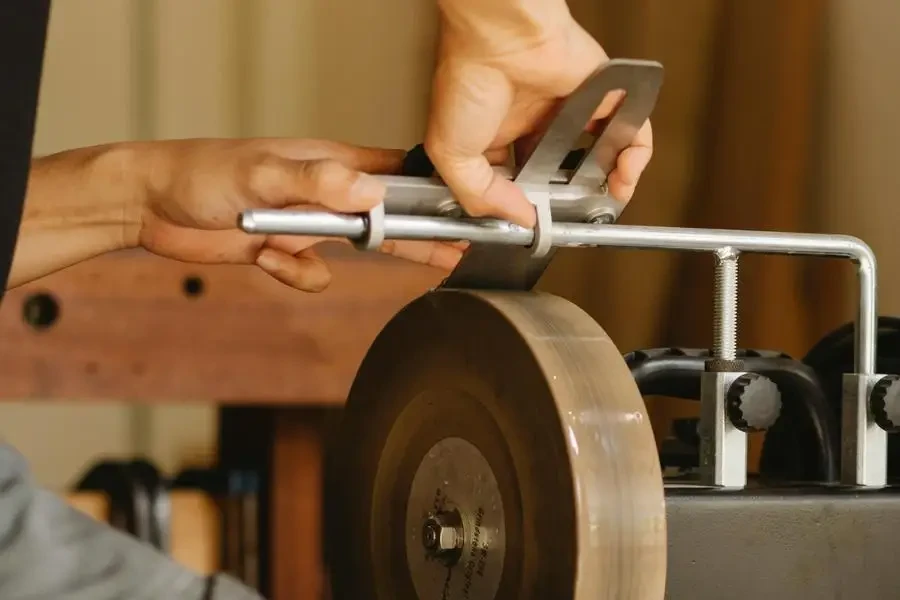
The global market for diamond grinder wheels is experiencing robust growth, driven by increasing demand across various industrial sectors. Valued at USD 2.5 billion in 2023, the market is projected to reach USD 3.4 billion by 2030, growing at a compound annual growth rate (CAGR) of 4.5%. This growth is primarily due to the expanding applications of diamond grinder wheels in industries such as automotive, aerospace, metalworking, and electronics. The Asia-Pacific region, particularly China and India, is expected to witness significant growth due to rapid industrialization and infrastructure development.
In the U.S., the market was valued at USD 600 million in 2023, with a forecasted growth rate of 3.8% CAGR to reach USD 800 million by 2030. Meanwhile, the Chinese market, valued at USD 450 million in 2023, is expected to grow at an impressive 6.0% CAGR, reaching USD 650 million by 2030. Other key regions, including Europe and Japan, are also anticipated to contribute significantly to market growth due to technological advancements and the increasing adoption of high-performance grinding tools.
Market segmentation includes several types of diamond grinder wheels such as straight wheels, cup wheels, dish wheels, and cylindrical wheels. The straight wheels segment is expected to dominate, with an estimated value of USD 1.2 billion by 2030, growing at a CAGR of 4.0%. The cylindrical wheels segment is projected to grow at a CAGR of 3.5%, reaching USD 800 million by 2030. The diverse applications and growing demand for precision grinding are key factors fueling the growth of these segments.
Eingehende Marktanalyse
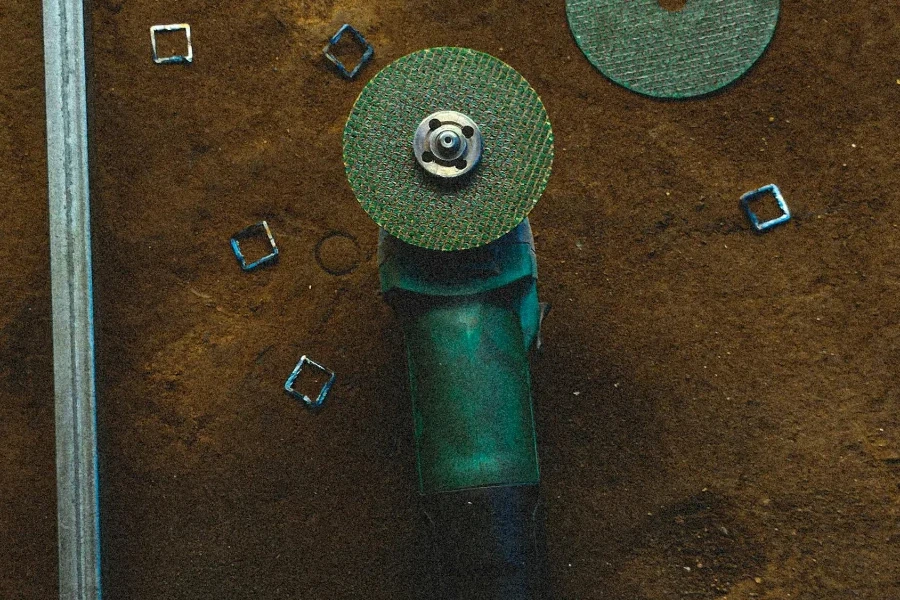
The diamond grinder wheel market is characterized by key performance benchmarks including durability, cutting efficiency, and precision. Advancements in bonding materials and diamond quality have significantly enhanced the performance and lifespan of these wheels. High-performance resin bonds and vitrified bonds, for instance, have improved cutting efficiency and thermal stability, making these wheels suitable for high-speed and heavy-duty grinding operations.
Market share dynamics reveal that leading players such as 3M Company, Norton Abrasives, and Saint-Gobain are heavily investing in research and development to introduce innovative products. For example, 3M’s Cubitron II wheels have set new benchmarks in cutting speed and longevity, capturing a significant market share. The competitive landscape is also witnessing consolidation, with major companies acquiring smaller firms to expand their product portfolio and geographical reach.
Economic influences such as fluctuating raw material prices and trade policies impact market dynamics. The volatile cost of synthetic diamonds, a key raw material, affects manufacturers’ pricing strategies. Additionally, ongoing trade tensions between major economies like the U.S. and China have led to uncertainties in the supply chain, prompting companies to explore alternative sourcing strategies.
Consumer behavior shifts are also crucial in shaping the market. The increasing demand for precision-engineered components in the automotive and aerospace industries is driving the adoption of high-performance diamond grinder wheels. Moreover, the growing trend towards automation and digitalization in manufacturing processes is leading to a preference for advanced grinding solutions that deliver consistent quality and reduce operational costs.
Distribution channels are evolving, with a growing inclination towards online sales platforms. E-commerce channels provide manufacturers with a wider reach and enable end-users to compare and purchase products conveniently. Specialized stores and direct sales remain prevalent, particularly for customized and high-value products.
Recent innovations include the development of hybrid diamond grinder wheels that combine the benefits of different bonding materials to enhance performance. Hybrid wheels that use a combination of resin and metal bonds offer improved cutting efficiency and thermal stability, making them suitable for a wide range of applications.
The product lifecycle stages of diamond grinder wheels indicate that the market is in a growth phase, with increasing adoption across various industries. However, the introduction of new technologies such as laser-based grinding solutions could pose a potential threat to traditional grinding wheels in the long term.
Digitalization is transforming the market, with manufacturers leveraging data analytics and IoT (Internet of Things) to enhance product performance and customer service. Smart grinding solutions that can monitor and adjust grinding parameters in real-time are gaining traction, offering significant benefits in terms of productivity and quality control.
Customer pain points such as high initial costs and the need for frequent wheel replacement are being addressed through innovations in bonding materials and diamond quality, which enhance the durability and efficiency of the wheels. Brand positioning strategies focus on highlighting these technological advancements and the long-term cost benefits of using high-performance diamond grinder wheels.
Differentiation strategies include offering customized solutions tailored to specific applications and providing comprehensive after-sales support. Niche markets, such as the medical device manufacturing industry, which requires ultra-precision grinding, present lucrative opportunities for market players.
Key Factors When Selecting a Diamond Grinder Wheel
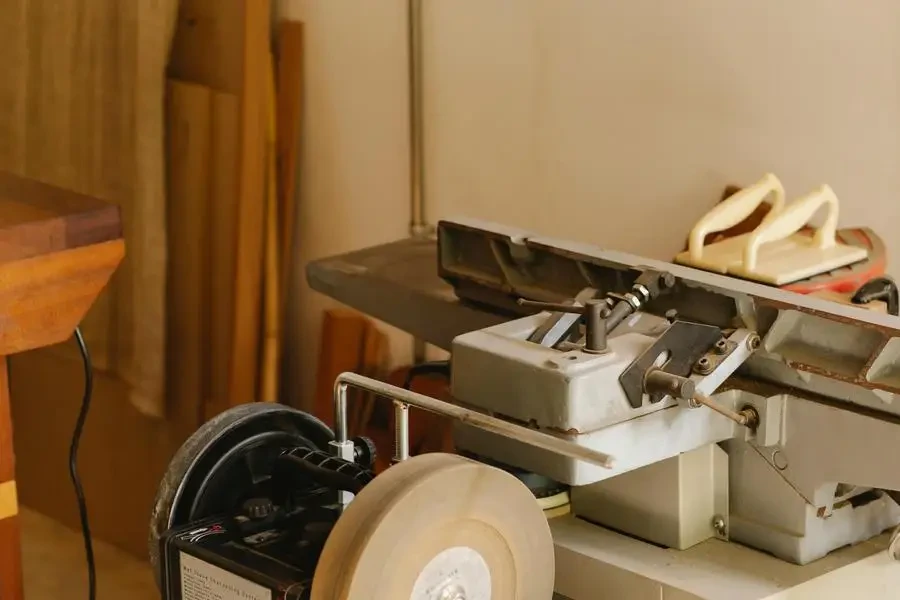
When selecting a diamond grinder wheel, various aspects need to be considered to ensure optimal performance and longevity. These factors include the type of abrasive grain, bond type, grit size, wheel shape, and rotational speed capabilities. Each plays a crucial role in determining the wheel’s suitability for specific applications.
Type of Abrasive Grain
The type of abrasive grain used in a diamond grinder wheel is critical for its performance. Synthetic diamond superabrasives are commonly used due to their extreme hardness and durability. These grains are suitable for grinding nonferrous metals, ceramics, glass, stone, and building materials. The choice of abrasive grain impacts the wheel’s cutting efficiency and lifespan.
Synthetic diamond grains are produced under high-pressure, high-temperature conditions, ensuring uniformity and consistency in performance. They offer superior grinding capabilities compared to other abrasive materials, making them ideal for demanding applications. Cubic boron nitride (CBN) is another superabrasive that provides excellent grinding performance on carbon and alloy steels.
Bond Type
The bond type in a diamond grinder wheel affects its cutting action and durability. Common bond types include resin, metal, and vitrified bonds. Resin bonds are flexible and provide a smooth cutting action, making them suitable for precision grinding and polishing applications. They are typically used where a fine finish is required.
Metal bonds are known for their durability and strength. They are often used in applications requiring aggressive cutting and high material removal rates, especially in grinding hard materials such as ceramics and glass. Vitrified bonds, made from ceramic materials, offer a balance between cutting efficiency and durability, suitable for both rough and finish grinding.
Körnung Größe
Grit size measures the abrasive particles’ size in the diamond grinder wheel. It determines the wheel’s cutting speed and surface finish quality. Coarse grits (lower grit numbers) are used for heavy material removal and rough grinding, while finer grits (higher grit numbers) are used for finishing and polishing.
The selection of grit size depends on specific application requirements. For example, a grit size of 40 to 60 is suitable for rough grinding, while a grit size of 120 to 240 is ideal for finishing operations. The ANSI, FEPA, and JIS grading systems ensure consistency and standardization across different manufacturers.
Radform
The shape of the diamond grinder wheel is another critical consideration. Different shapes are designed for specific grinding needs. Common wheel shapes include straight, cup, and dish wheels. Straight wheels are flat discs used for surface grinding and cutting. They are versatile for various grinding applications.
Cup wheels have a cup-like shape and are used for grinding flat surfaces and edge grinding, commonly in masonry and stone grinding applications. Dish wheels have a concave shape and are used for precision grinding and finishing operations. The choice of wheel shape depends on the workpiece geometry and grinding requirements.
Drehzahlfähigkeiten
The rotational speed capabilities of the diamond grinder wheel are crucial for safe and efficient operation. The wheel’s maximum operating speed should match the grinder’s speed to prevent accidents and ensure optimal performance. Exceeding the wheel’s maximum speed can lead to wheel failure and pose safety risks to the operator.
Manufacturers specify the maximum rotational speed for their diamond grinder wheels, typically measured in revolutions per minute (RPM). It is essential to select a wheel that matches the grinder’s speed capabilities. The wheel’s structure and bond type should also be compatible with the operating speed to ensure stability and performance.
Understanding the Applications of Diamond Grinder Wheels
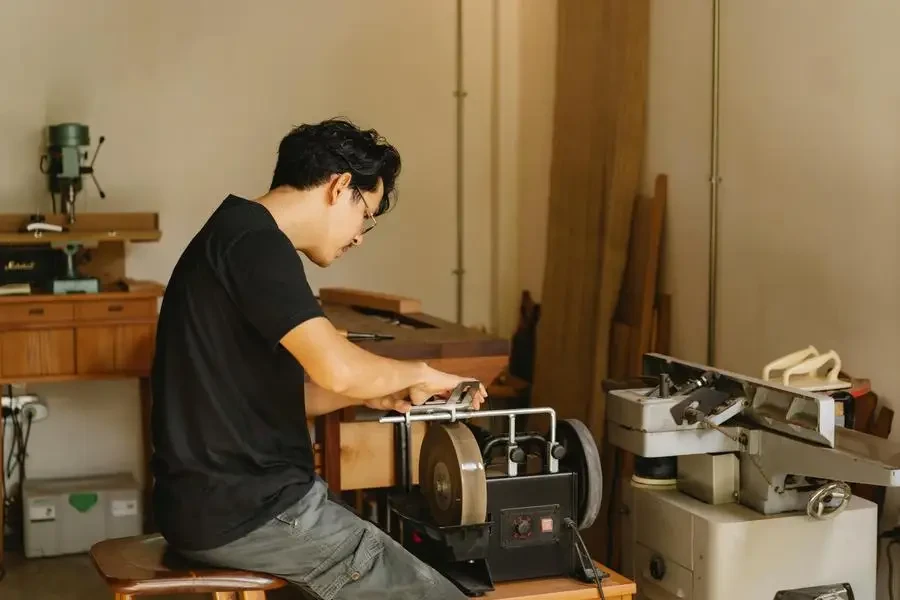
Diamond grinder wheels are used in various applications across multiple industries. Their ability to cut and grind hard materials makes them indispensable in sectors such as construction, manufacturing, and maintenance. Here, we explore common applications and the benefits they offer.
Construction and Masonry
In construction, diamond grinder wheels are extensively used for cutting and grinding concrete, stone, and masonry materials. Their superior cutting efficiency and durability make them ideal for tasks such as surface preparation, concrete repair, and tile cutting. Maintaining sharpness over extended use reduces downtime and increases productivity on construction sites.
For example, during the renovation of a commercial building, diamond grinder wheels can remove old coatings, grind down uneven surfaces, and prepare the floor for new installations. The precision and speed offered by diamond grinder wheels ensure projects are completed efficiently, meeting tight deadlines and reducing labor costs.
Manufacturing and Metalworking
In manufacturing and metalworking, diamond grinder wheels are used for precision grinding and finishing of hard metals and alloys. They are essential in producing aerospace components, automotive parts, and medical devices. The high hardness and thermal conductivity of diamond grains enable efficient material removal and superior surface finish.
For instance, in producing turbine blades for jet engines, diamond grinder wheels achieve the precise tolerances and smooth surface finish required for optimal performance. The wheels’ ability to maintain their shape and sharpness over extended use ensures consistent quality and reduces the need for frequent wheel changes.
Glas und Keramik
In the glass and ceramics industry, diamond grinder wheels are used for cutting, shaping, and finishing glass products and ceramic components. Their ability to produce clean cuts and smooth edges without causing chipping or cracking is highly valued. Diamond grinder wheels are used in producing optical lenses, decorative glass, and ceramic tiles.
For example, in producing optical lenses, diamond grinder wheels grind and polish the lenses to the required specifications. The wheels’ precision and consistency ensure the lenses meet stringent quality standards, providing clear and accurate optical performance.
Innovations in Diamond Grinder Wheel Technology
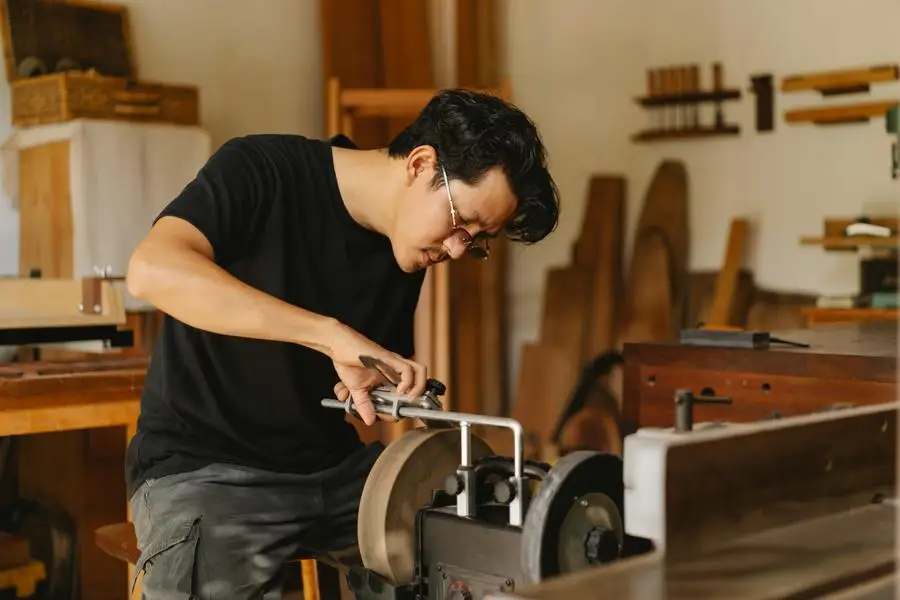
The diamond grinder wheel market continues to evolve with advancements in technology and materials. These innovations aim to enhance the performance, durability, and versatility of diamond grinder wheels, meeting the growing demands of various industries.
High-Performance Bond Systems
Recent advancements in bond systems have led to high-performance diamond grinder wheels. New resin formulations and metal bond technologies offer improved cutting efficiency, longer wheel life, and enhanced thermal stability. These advancements enable diamond grinder wheels to perform effectively in high-speed and high-temperature applications.
For example, hybrid bond systems that combine the benefits of resin and metal bonds have resulted in wheels that offer both flexibility and strength. These wheels can handle a wide range of grinding tasks, from rough cutting to precision finishing, making them versatile and cost-effective.
Advanced Abrasive Grains
The development of advanced abrasive grains has also contributed to the evolution of diamond grinder wheels. New synthetic diamond grains with enhanced hardness and thermal conductivity offer superior cutting performance and longer lifespan. These grains are designed to withstand high-stress conditions, making them suitable for demanding applications.
For instance, using nano-diamond grains in diamond grinder wheels has led to significant improvements in cutting efficiency and surface finish quality. These grains provide a sharper cutting edge and reduce the heat generated during grinding, resulting in faster material removal and extended wheel life.
Smart Grinding Solutions
The integration of smart technologies in diamond grinder wheels is another exciting development. Smart grinding solutions leverage sensors and data analytics to monitor wheel performance in real-time. These systems provide valuable insights into wheel wear, cutting efficiency, and operating conditions, allowing users to optimize their grinding processes.
For example, smart diamond grinder wheels equipped with sensors can detect changes in wheel performance and alert operators to potential issues before they lead to wheel failure. This proactive approach to maintenance reduces downtime, extends wheel life, and ensures consistent grinding quality.
Ensuring Safety and Compliance with Diamond Grinder Wheels
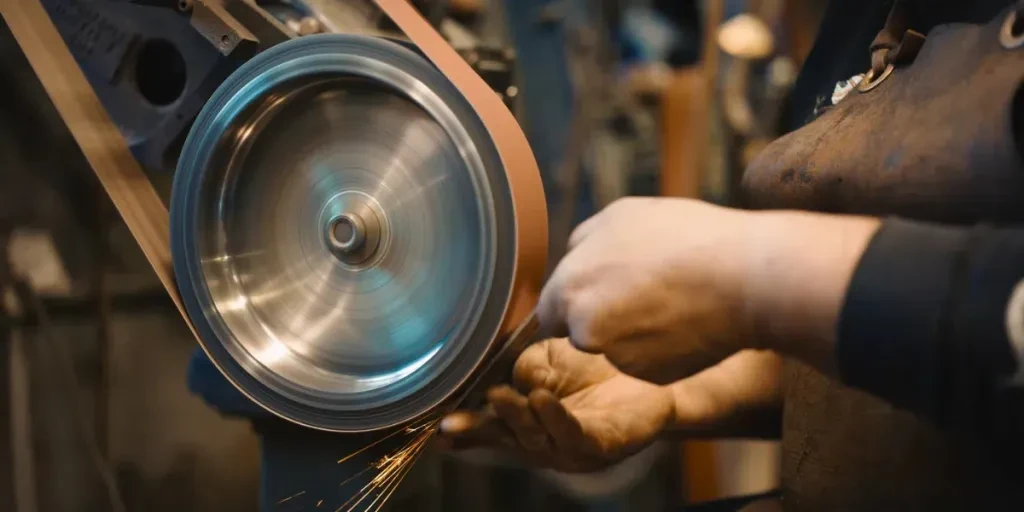
Safety and regulatory compliance are paramount when using diamond grinder wheels. Adhering to industry standards and best practices ensures the safe operation of grinding equipment and protects operators from potential hazards.
Sicherheitsstandards und Zertifizierungen
Diamond grinder wheels must comply with relevant safety standards and certifications to ensure their safe use. Standards such as ANSI B7.1 and ISO 6104 specify the requirements for the design, manufacture, and testing of grinding wheels. These standards ensure that wheels can withstand the stresses of high-speed grinding and provide guidelines for safe operation.
Manufacturers must adhere to these standards and obtain certifications to demonstrate compliance. Certified diamond grinder wheels undergo rigorous testing to ensure their structural integrity and performance. Users should always verify that the wheels they purchase meet the necessary safety standards and certifications.
Richtige Handhabung und Lagerung
Proper handling and storage of diamond grinder wheels are crucial for maintaining their safety and performance. Wheels should be stored in a dry, cool environment away from direct sunlight and moisture. They should be kept in their original packaging until ready for use to prevent damage and contamination.
When handling diamond grinder wheels, operators should avoid dropping or striking them against hard surfaces, as this can cause cracks and weaken the wheel. Inspecting wheels for damage before use is essential to ensure their safety and effectiveness. Any wheels with visible cracks or defects should be discarded immediately.
Operator Training and PPE
Operator training is vital for the safe use of diamond grinder wheels. Operators should be trained on the proper mounting, operation, and maintenance of grinding equipment. They should also be familiar with the specific safety guidelines and procedures for using diamond grinder wheels.
Personal protective equipment (PPE) is essential for protecting operators from potential hazards. PPE includes safety glasses, face shields, gloves, and hearing protection. Using the appropriate PPE reduces the risk of injury from flying debris, sparks, and noise generated during grinding.
Schlussfolgerung
In summary, diamond grinder wheels are indispensable tools in various industries due to their exceptional cutting efficiency and durability. Selecting the right wheel involves considering factors such as abrasive grain type, bond type, grit size, wheel shape, and rotational speed capabilities. Understanding the applications and innovations in diamond grinder wheel technology further enhances their effectiveness. Ensuring safety and compliance through adherence to standards, proper handling, and operator training is crucial for safe and efficient grinding operations.