Auf dem Additive Manufacturing Campus in Oberschleißheim erprobt die BMW Group das Wire Arc Additive Manufacturing (WAAM), bei dem ein Draht aus Aluminium oder ähnlichem mittels Lichtbogen geschmolzen wird. Anschließend legt ein softwaregesteuerter Roboter eine Vielzahl von Schweißnähten präzise übereinander, bis ein komplettes Bauteil fertig ist.
Da durch den Druck Schicht für Schicht nicht auf die Entformbarkeit geachtet werden muss, sind Hohlstrukturen mit einem optimalen Verhältnis zwischen Steifigkeit und Gewicht möglich.
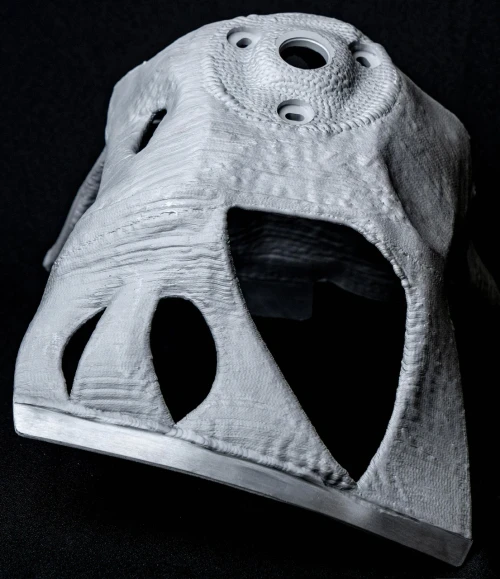
Dadurch können die Bauteile leichter und steifer sein als vergleichbare Druckgussteile, die derzeit in Serie gefertigt werden. Dank geringerem Energiebedarf und weniger Materialverschwendung können sie zudem nachhaltiger produziert werden. Zukünftig ist geplant, im WAAM-Verfahren hergestellte Komponenten in Serienfahrzeugen der BMW Group einzusetzen.
Durch die große Breite und Höhe einer einzelnen Schweißnaht können Bauteile mit WAAM äußerst schnell hergestellt werden. Im Gegensatz zum Laserstrahlschmelzen, das bei der BMW Group bereits in der Prototypen- und Kleinserienfertigung zum Einsatz kommt, eignet sich WAAM besonders für größere Bauteile. Die typischen Wandstärken eignen sich gut für Bauteile im Karosserie-, Antriebs- und Fahrwerksbereich. Aber auch Werkzeuge und Geräte lassen sich mit diesem Hightech-Verfahren herstellen, das auch in der Luftfahrtindustrie Anwendung findet.
Seit 2015 beschäftigen sich Mitarbeiter der BMW Group mit dem WAAM-Verfahren, auch Auftragsschweißen genannt. Seit 2021 ist auf dem Additive Manufacturing Campus eine WAAM-Zelle zur Herstellung von Testbauteilen im Einsatz. Eine dieser Beispielanwendungen ist a Federbeinträger, der in umfangreichen Tests auf dem Prüfstand mit dem Serienbauteil aus Aluminium-Druckguss verglichen wird.
Bereits in diesem frühen Stadium ist klar, dass das WAAM-Verfahren zu geringeren Emissionen im Produktionsprozess führen kann. Das geringere Gewicht der Bauteile, ihr vorteilhaftes Materialeinsatzverhältnis und die Möglichkeit zur Nutzung erneuerbarer Energien ermöglichen eine effizientere Herstellung der Bauteile.
—Jens Ertel, Leiter BMW Additive Manufacturing
Der nächste Entwicklungsschritt auf dem Weg zur Serienreife ist die Erprobung von Komponenten im Fahrzeug, die in absehbarer Zeit beginnen wird.
Durch die breiteren Schweißnähte im WAAM-Verfahren sind die Oberflächen der Bauteile nicht glatt, sondern leicht wellig und müssen an kritischen Stellen nachbearbeitet werden. Die Ingenieure der BMW Group konnten jedoch nachweisen, dass WAAM-Komponenten auch ohne Nachbehandlung der Oberfläche für hohe Belastungen, auch zyklische Belastungen, einsetzbar sind.
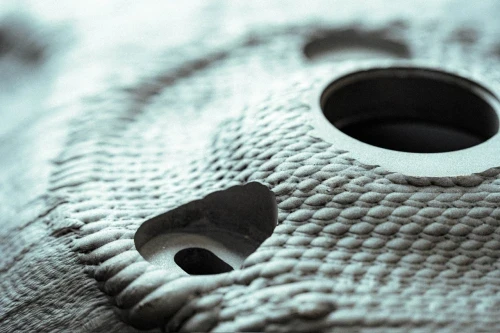
Für die Sicherstellung der Haltbarkeit direkt ab der Produktion sind optimierte Prozessparameter entscheidend, daher muss die Kombination aus Schweißprozess und Roboterbahnplanung optimal aufeinander abgestimmt sein.
Um die im WAAM-Verfahren hergestellten Komponenten optimal nutzen zu können, ist die Kombination des Herstellungsprozesses und eines generell neuen Komponentendesigns von größter Bedeutung. Zu diesem Zweck forciert die BMW Group weiterhin den Einsatz generativen Designs. Dabei entwirft der Computer mithilfe von Algorithmen optimierte Komponenten basierend auf den spezifischen Anforderungen.
Diese Algorithmen werden in enger Zusammenarbeit mit interdisziplinären Teams entwickelt und sind teilweise von evolutionären Prozessen in der Natur inspiriert. Wie bei bionischen Strukturen wird im ersten Schritt nur das Material verwendet, das tatsächlich für die Topologie des Bauteils benötigt wird, und bei der Feinabstimmung im zweiten Schritt wird das Bauteil nur dort verstärkt, wo es notwendig ist. Dies führt letztendlich zu leichteren und steiferen Bauteilen sowie zu höherer Effizienz und verbesserter Fahrzeugdynamik.
Unterschiedliche additive Fertigungsverfahren stehen nicht zwangsläufig in Konkurrenz zueinander, sondern sollten vielmehr als komplementär betrachtet werden. Beispielsweise wird das Laserstrahlschmelzen bei höchster Detailauflösung weiterhin vorteilhafter sein als das WAAM-Verfahren. Hinsichtlich der möglichen Bauteilgröße und der Abschmelzleistung ist jedoch die additive Fertigung mit Drahtlichtbogen überlegen.
Die BMW Group plant zunächst eine zentrale WAAM-Produktion von Komponenten in Oberschleißheim, künftig ist auch die Produktion an anderen Standorten und die Nutzung der Technologie durch Zulieferer möglich. Darüber hinaus wäre es sogar denkbar, mit diesem Verfahren einzelne Bauteile direkt am Fließband zu fertigen und durch einen einfachen Softwarewechsel unterschiedliche Teile ohne neue Werkzeuge herzustellen. Die Nachhaltigkeit kann auch durch den verstärkten Einsatz recycelter Metalle weiter verbessert werden.
Quelle aus Green Car Kongress
Haftungsausschluss: Die oben dargelegten Informationen werden von greencarcongress.com unabhängig von Chovm.com bereitgestellt. Chovm.com gibt keine Zusicherungen und Gewährleistungen hinsichtlich der Qualität und Zuverlässigkeit des Verkäufers und der Produkte.