Ein Blick auf aktuelle Trends und Lieferkettenthemen für die Automobilbranche
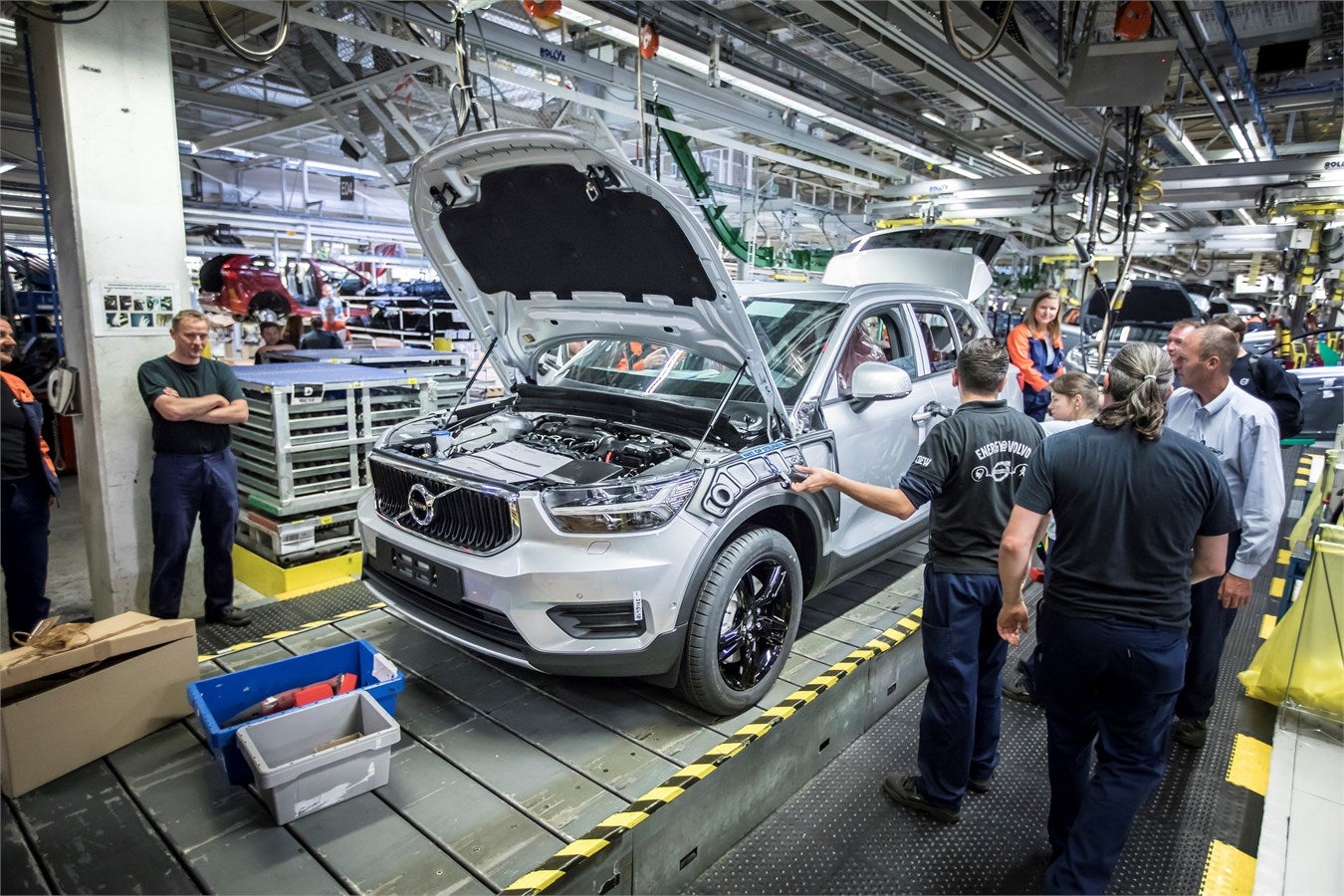
Ein atypisches Kraftfahrzeug kann aus 15,000 bis 25,000 Einzelteilen bestehen – abhängig von der Art und Weise ihrer Messung und der Konstruktionstechnik seiner Hauptsysteme. Das ist eine Menge Material, das zusammengeführt werden muss und für die Integrität des Endprodukts sorgt. Tatsächlich ist es keine leichte Aufgabe, all diese Teile in der richtigen Reihenfolge zusammenzufügen. Jedes existierende Auto ist eine Hommage an Prozessplanung, Organisation, Produktionstechnik und Fertigungslogistik. Früher waren Fahrzeughersteller stark vertikal integriert, aber dieser Ansatz wich veräußerten (erinnert sich jemand daran, wo Visteon herkam und an das verworrene Netz von Unternehmen, aus denen die Automotive Components Group von General Motors bestand?) und spezialisierten Teilelieferanten, auf die man sich konzentrieren konnte Sie können die Produktentwicklung verbessern und in größerem Maßstab effizienter für mehr als einen Kunden arbeiten.
Die großen Tier-1-Systemintegratoren beliefern die Fahrzeughersteller direkt, oft aus Lieferantenparks, die günstig in der Nähe von Fahrzeugmontage- und -fertigungsanlagen liegen. Unter der obersten Ebene gibt es jedoch mehrere Ebenen kleinerer Lieferanten, die jeweils eine wichtige Rolle auf dem langen Weg vom Rohmaterial spielen Materialien bis zum fertigen Produkt.
Die internationale Beschaffung von Komponenten ist über viele Jahrzehnte zu einem Industriestandard geworden, da OEMs und größere Zulieferer versucht haben, sich auf dem Weltmarkt nach Teilen und Materialien umzusehen, die die erforderlichen Qualitätsschwellenwerte zu den niedrigsten Kosten erfüllen. Entfernungen (und Kosten) für den Transport und Vereinbarungen zur Lagerhaltung spielen ebenfalls eine Rolle, aber höhere Effizienz und technologische Fortschritte im internationalen Frachttransport haben zu einem phänomenalen Wachstum bei internationalen Teilelieferungen geführt.
Das Wachstum der chinesischen Automobilindustrie in den letzten zwei Jahrzehnten war auch ein wichtiger Faktor bei der weltweiten Beschaffung von Automobilkomponenten, insbesondere von so genannten Universal- oder Standardteilen, die hauptsächlich zum Selbstkostenpreis verkauft werden. Chinesische Zulieferer haben von großen lokalen Verträgen profitiert, die Skaleneffekte fördern, sowie von versteckten Subventionen, die sich aus komplexen Eigentümerstrukturen ergeben, an denen OEM-Muttergesellschaften, staatliche Unternehmen und diversifizierte Lagerbestände beteiligt sind. In den frühen 2000er Jahren gingen insbesondere die US-amerikanischen Fahrzeughersteller dazu über, mehr kostengünstige Teile aus Asien zu beziehen, was einige seit langem etablierte Unternehmen in der US-Zuliefererbasis untergrub.
Weltweit sind die internationalen Handelsströme mit Automobilprodukten – sowohl Fertigfahrzeugen als auch Komponenten – mittlerweile riesig. Schätzungen zusammengestellt von Global zeigen, dass Deutschland bei den Auslieferungen von Produkten aus der Automobilindustrie mit Abstand weltweiter Spitzenreiter ist. Diese Exporte werden durch Importe und ein verworrenes Netz von Zwischenprodukten widergespiegelt, die als Input für Komponentensysteme dienen, die in verschiedenen Phasen des Herstellungsprozesses verfeinert und konstruiert werden und mehrfach über internationale Grenzen hinweg versendet werden können.
Ein weiteres wichtiges Strukturmerkmal der Lieferketten in der Automobilindustrie ist die Bedeutung einer Supply-Chain-Management-Philosophie, die die Lagerkosten minimiert und die Prozesseffizienz sowie Feedback-Kommunikationsschleifen für verbesserte Qualitätsstandards steigert. Bekannt als „Lean Manufacturing“, begann es mit Toyota und seine Essenz wird durch den Begriff „Just-in-Time“ zusammengefasst, der die schlanken Liefermethoden und -prinzipien beschreibt. Der Aufstieg digitaler und vernetzter Technologien, die alle Teile des Herstellungs- und Einzelhandelsprozesses zusammenführen, hat diese Arbeitsweisen im letzten Jahrzehnt oder so weiter untermauert.
In der Vergangenheit haben Naturkatastrophen und ihre konzentrierten Auswirkungen auf Standorte Automobilunternehmen beeinträchtigt und die Fragilität der Automobillieferketten deutlich gemacht. Nach dem Erdbeben und dem Tsunami 2011 in Japan kam es zu mehreren bemerkenswerten Störungen. Ein weltweit agierender Premium-Automobilhersteller hatte Probleme mit der Versorgung mit einem in Japan bezogenen roten Farbpigment. Später in diesem Jahr kam es in Thailand zu Überschwemmungen, die zu einer Verknappung der Versorgung mit LCD-Bildschirmen für die Anzeige von Fahrzeuginformationen führten. OEMs und Händler mussten sich entsprechend auf Engpässe einstellen. Der Krieg in der Ukraine zeigt, wie unerwartete geopolitische Ereignisse auch Lieferketten stören können.
Die Halbleiter-Herausforderung
Alle Unternehmen waren direkt von der Gesundheitskrise im Jahr 2020 und indirekt von vielen weiteren Auswirkungen auf die globalen Lieferketten betroffen. Darüber hinaus wurde die Erholung des weltweiten Umsatzes im Jahr 2021 durch eine unvorhergesehene Folge der Covid-Krise ein Jahr zuvor erheblich beeinträchtigt. Da die Fahrzeughersteller im Jahr 2020 auf Anordnung der Regierung ihre Fabriken schlossen und ihre Teilebestellungen drastisch zurückfuhren, fanden die Hersteller von Halbleitern alternative Geschäftsmöglichkeiten in Bereichen wie der Unterhaltungselektronik.
Als die sich erholenden Automobilfabriken im ersten Quartal 2021 ihre Chipbestellungen erhöhten, wurde schnell ein Problem des knappen Angebots deutlich.
Aufgrund der langen Vorlaufzeiten bei der Erweiterung der Chip-Foundry-Kapazität im Vorfeld ließen sich auch Halbleiterengpässe nicht so leicht überwinden. Das Fehlen eines sicherheitskritischen oder auf andere Weise für das fertige Produkt als notwendig erachteten Teils führte dazu, dass einige Modellreihen stärker betroffen waren als andere. In einigen Fällen könnten Fahrzeughersteller den Marktmix neu gestalten, aber ein altes Sprichwort bewahrheitete sich wieder: Lieferketten sind nur so gut/robust wie ihr schwächster Punkt.
In der gesamten Branche stehen Beschaffungsmethoden und -prozesse auf dem Prüfstand wie nie zuvor.
Es ist auch erwähnenswert, dass es ein strukturelles Element gibt, das bedeutet, dass ein gewisser Versorgungsdruck bei Halbleitern wahrscheinlich auch in Zukunft ein Risiko darstellen wird: Der Anteil an hochentwickelter Elektronik in Fahrzeugen nimmt zu, da immer mehr anspruchsvollere technologische Funktionen eingebaut werden. Dies veranlasst einige Unternehmen dazu, strategische Allianzen mit Chipherstellern einzugehen. Dies kann nicht nur dazu beitragen, die zukünftige Versorgung mit kritischen Mikroprozessoren zu sichern, sondern auch vorteilhafte Kooperationen bei der künftigen Produktentwicklung in einem offensichtlich strategisch wertvollen Komponentenbereich ermöglichen.
Ein weiterer Druck auf die Lieferketten entsteht aus anderen Quellen, beispielsweise durch unvorhergesehenen Arbeitskräftemangel und viel höhere Preise für internationale Containertransporte, da die Energiepreise in die Höhe geschossen sind.
Die Dual-versus-Multi-Sourcing-Debatte
Die Fragilität in Automobillieferketten geht mit der Verbreitung mehrerer Ebenen, internationalen Beschaffungsströmen und der Tendenz zur Einzelbeschaffung einher, um Skaleneffekte bei globalen Fahrzeugprogrammen zu maximieren. In vielen Fällen ist diese traditionelle Struktur auch in einer Kultur bevorzugter Partner auf allen Lieferebenen verankert. Zu den Vorteilen können auch gemeinsame Systeme und Logistikkosten gehören, wobei die Kosten auch bei anderen Modellen und Systemen auf die Volumina verteilt werden.
Auch die Technologie hat bei der Förderung von Single Sourcing eine Rolle gespielt, da Unternehmen – einschließlich derer der Stufen 3 und 4 – in der Regel in der Lage waren, Fachwissen und Investitionen in einer Anlage zu zentralisieren, die auf die Massenfertigung ausgerichtet ist. Die Probleme treten auf, wenn etwas schief geht, was die Pläne zunichte macht (z. B. der Brand in einem Mikroprozessorwerk von Renesas im letzten Jahr).
Elektronik und Sensoren sind Beispiele für kritische Komponenten für Unterbaugruppen, die große Auswirkungen auf die nachgelagerte Fahrzeugfertigung haben können, wenn es im vorgelagerten Bereich zu Störungen kommt. Sehr kurzfristig alternative Lieferanten mit freien Kapazitäten zu finden, ist eine große Herausforderung.
Die Bevorratung einiger Teilereserven ist mit Kosten verbunden und widerspricht den Leitprinzipien der schlanken Fertigung. Selbstverständlich kann die Entscheidung getroffen werden, etwaige Ausreißer-Störungskosten zu absorbieren oder abzuschreiben, sobald sie auftreten – dies hängt letztendlich von der Quantifizierung der Risikobewertung ab.
Die Erfahrungen der letzten Jahre deuten zumindest darauf hin, dass sich Unternehmen zunehmend die Frage stellen, ob Singe-Sourcing noch so wünschenswert ist wie früher. Eine Welt, die von höheren Risiken und Unsicherheiten geprägt ist, erfordert möglicherweise eine Neuausrichtung des Ansatzes. Eine Duplizierung innerhalb der Lieferkette, auch wenn sie bedeutet, dass man sich einer gemeinsamen Nutzung mit einem Konkurrenten annähert, kann – zumindest für einige Komponenten – eine bessere Lösung bieten als die Einzelbeschaffung. Der Vorteil von Dual Sourcing wäre eine größere Produktsicherheit. Wie immer ist es eine Frage der Gesamtkosten.
Elektrifizierung und neue Lieferkettenmuster
Die Elektrifizierung bringt neue Herausforderungen für zukünftige Lieferketten in der Automobilindustrie mit sich. Die OEMs sind mit erheblichen Unsicherheiten hinsichtlich der Lieferung neuer und wichtiger Komponenten – insbesondere Antriebsstrangbatterien – konfrontiert, die sie zu lösen versuchen. Es gibt auch strategische Fragen zum Grad der vertikalen Integration, der wünschenswert ist, um zukünftige Risiken zu mindern und die Kontrolle über die kommerziellen Aspekte von Liefervereinbarungen auszuüben. Es wurden Joint Ventures mit Batteriespezialisten gegründet. Auch andere Schlüsselkomponenten für Elektrofahrzeuge – wie Motoren, Antriebssystemteile, Hochspannungswechselrichter – werden neben Überlegungen zur Lieferkette zunehmenden Investitionen unterliegen.
Ehrgeizige Elektrifizierungsstrategien werden die Nachfrage nach Lithium-Ionen-Batteriezellen in die Höhe schnellen lassen. Batteriehersteller auf der ganzen Welt verpflichten sich zu milliardenschweren Expansionsstrategien und eröffnen neue „Gigafabriken“, um Zellen an Autohersteller zu liefern.
Ein bemerkenswertes Beispiel für eine intensive Zusammenarbeit zwischen OEM und Tier 1 in diesem Bereich ist die Unterzeichnung einer Absichtserklärung zwischen Volkswagen und Bosch. Die beiden Unternehmen planen, integrierte Batterieproduktionssysteme, Hochlauf vor Ort und Wartungsunterstützung für Hersteller von Batteriezellen und Batteriesystemen bereitzustellen. Sie streben nach eigenen Angaben eine Kosten- und Technologieführerschaft in der Batterietechnologie im industriellen Maßstab und die Massenproduktion „nachhaltiger, hochmoderner Batterien“ an.
Allein in Europa plant der Volkswagen-Konzern den Bau von sechs Zellfabriken bis 2030 und andere Hersteller unternehmen ähnliche Schritte, um die zukünftige Versorgung mit Zellen und Batteriepaketen sicherzustellen. Bis 700 soll die Region über eine jährliche Gesamtbatteriekapazität von rund 2030 Gigawattstunden verfügen.
Im Upstream-Bereich hat Toyota ein Joint Venture mit Panasonic (Prime Planet Energy & Solutions – PPES) gegründet, das eine Vereinbarung mit dem Bergbaugiganten BHP über die künftige Lieferung von Nickelsulfat unterzeichnet hat, der Grundlage für das Nickel, das in der Kathode der meisten Lithium-Ionen-Akkus vorhanden ist Batteriezellen. Tesla hat auch eine ähnliche Vereinbarung mit BHP unterzeichnet, was zeigt, dass auch Rohstoffe eine wichtige Rolle für die künftige Versorgungssicherheit spielen.
Diese Vereinbarungen unterstreichen die Notwendigkeit für Automobilunternehmen, weiter nach oben in der Batterielieferkette zu schauen, um sicherzustellen, dass sie Zugang zu ausreichend Rohstoffen haben, um das enorme Kapazitätswachstum zu liefern, das im Lithium-Ionen-Batteriesektor für die neue Welle batteriebetriebener Elektrofahrzeuge erforderlich ist, die in den USA auf den Markt kommen kommende Jahre. Auch Recycling ist bei vielen der abgeschlossenen Geschäfte ein zentraler Aspekt.
Blockchain für Transparenz in der Lieferkette
Zunehmend nutzen Automobilunternehmen die Blockchain-Technologie, um Transparenz über Lieferkettenprobleme wie CO2-Emissionen und die Quelle von Kobalt für Batterien zu gewinnen (was ethische Fragen im Zusammenhang mit dem Abbau wertvoller Mineralien mit sich bringen kann).
Das ursprüngliche Blockchain-Konzept ist, wie der Name schon sagt, eine Kette von Blöcken oder Datensätzen mit Zeitstempel (Block = digitale Informationen; Kette = die öffentliche/gemeinschaftliche Datenbank). Blöcke speichern Informationen über Transaktionen. Wenn ein Block neue Daten – eine Transaktion – speichert, wird er der Blockchain hinzugefügt und kann, sobald er von einem Peer-to-Peer-Netzwerk von Computern überprüft wurde, von jedem gesehen werden (oder er kann der Erlaubnis eines privaten Netzwerks wie z. B. unterliegen). die Lieferkette eines OEMs – das „Distributed Ledger“).
Allerdings haben alle Parteien nur Zugriff auf die Informationen, zu deren Einsicht sie berechtigt sind. Jeder Computer im Blockchain-Netzwerk verfügt über eine eigene Kopie der Blockchain. Im Prinzip besteht die Idee jedoch darin, ein hochtransparentes System zu schaffen, bei dem zwischen den beiden Parteien, die einen Block bilden, keine Transaktionskosten anfallen.
Wir können damit rechnen, dass mehr Automobilunternehmen Blockchain-Prozesse einführen werden – insbesondere vom Typ „Distributed Ledger“ (d. h. ein privates Netzwerk) – als Mittel zur Minderung des Risikos von „Unterbrechungen“ in der Lieferkette und zum Verständnis der Stärken und Schwächen entlang der Kette, aber auch als Mittel Möglichkeit, steigende Anforderungen an Compliance in Regulierungsbereichen wie der Nachhaltigkeit aufzuzeigen.
Lehren von Toyota
Toyota gilt allgemein als einer der leistungsstärksten Anbieter der Automobilindustrie, wenn es um das Lieferkettenmanagement geht. Das Unternehmen ist nicht nur der Begründer der Lean-Manufacturing-Methoden, die später zu weitverbreiteten Best Practices wurden, die von den meisten OEMs und großen Zulieferern übernommen wurden, sondern hat auch seine Systeme und Prozesse entsprechend den sich ändernden Umständen hinsichtlich Risikominderungsmaßnahmen verfeinert. Darüber hinaus hat das Unternehmen in Notfällen zeitweise und im Interesse breiterer Branchenziele sehr eng mit seinen Lieferanten zusammengearbeitet.
Nach dem Erdbeben und Tsunami in Kyoto im Jahr 2011 arbeitete Toyota mit Zulieferern in Japan zusammen, um eine umfassende Datenbank mit Lieferketteninformationen zur Unterstützung des japanischen Fertigungssektors zu erstellen. Toyota führte außerdem eine Strategie für die Mehrfachbeschaffung wichtiger Teile ein, was bedeutet, dass die Lieferung aus drei verschiedenen Quellen organisiert wird – wobei der Hauptlieferant jedoch darauf ausgerichtet ist, fast zwei Drittel der Bestellung zu liefern, um Größenvorteile zu gewährleisten. Mehrere Lieferanten gefährden zwar die Größenvorteile, bedeuten aber auch, dass bei Bedarf Alternativen vorhanden sind.
Toyota verfügt außerdem über ein gut entwickeltes System zur Überwachung seines riesigen Lieferantennetzwerks und ein Frühwarnsystem für Engpässe. Tatsächlich greifen einige Unternehmen auf KI zurück, um Entwicklungen in ihren Lieferketten zu bewerten – obwohl dies in erster Linie voraussetzt, dass sie über eine zuverlässige, umfangreiche und detaillierte Datenbank verfügen.
Eine weitere Möglichkeit für Unternehmen besteht darin, Not- oder Pufferbestände an wichtigen Teilen vorzuhalten – insbesondere solchen, die zum Stillstand einer Produktionslinie führen können. Auch hier fallen zusätzliche Kosten für die Lagerung an, es kommt jedoch darauf an, zu entscheiden, welche Kosten oder „Versicherungsprämie“ es wert ist, gezahlt zu werden. Außerdem wird es keine dauerhafte Lösung sein. Toyota hat zwar einige Halbleitervorräte angelegt, aber die Schwere der weltweiten Knappheit an Chips führte dazu, dass auch das Unternehmen schließlich gezwungen war, die Produktion zu drosseln. Die vielleicht bedeutendste Erkenntnis von Toyota ist die Notwendigkeit einer ständigen Überprüfung und Anpassungsfähigkeit an sich ändernde Umstände und Unsicherheiten.
Quelle aus Nur Auto
Haftungsausschluss: Die oben dargelegten Informationen werden von just-auto.com unabhängig von Chovm.com bereitgestellt. Chovm.com gibt keine Zusicherungen und Gewährleistungen hinsichtlich der Qualität und Zuverlässigkeit des Verkäufers und der Produkte.