Índice del contenido
- Introducción
– Mito n.º 1: Talla única: los AMR son adecuados para cada estilo de recolección
– Mito #2: Su WMS es la mejor herramienta para gestionar flujos de trabajo entre humanos y robots
– Mito n.º 3: el software AMR puede optimizar perfectamente la coordinación entre humanos y robots
– Mito #4: Los robots por sí solos pueden minimizar los viajes de los trabajadores
– Mito #5: Los sistemas existentes son suficientes para orquestar el trabajo entre humanos y robots.
- Conclusión
Introducción
A medida que la tendencia a la robótica y la automatización continúa creciendo en los almacenes, y según un estudio reciente se espera que el mercado alcance los 23.09 millones de dólares en 2027, es crucial que las empresas comprendan cómo integrar de manera efectiva robots y trabajadores humanos. Sin embargo, existen varios conceptos erróneos comunes sobre la coordinación y optimización de tareas entre humanos y robots en el almacén.
Mito n.º 1: Talla única: los AMR son adecuados para cada estilo de recolección
Un error común es creer que los robots móviles autónomos (AMR) pueden manejar todos los estilos de recolección igualmente bien. Sin embargo, la realidad es que diferentes AMR se especializan en diferentes flujos de trabajo. Algunos de estos flujos de trabajo incluyen robots a mercancías, mercancías a personas, seguimiento del robot, robots de tránsito y movimientos de paletas completas.
Para obtener la mejor combinación de robótica en su centro de distribución, es posible que necesite diferentes AMR de distintos proveedores para satisfacer cada proceso. Esto puede generar complejidades en la integración, ya que cada sistema AMR puede tener sus propios requisitos e interfaces únicos.
La clave para superar este desafío es utilizar un socio de integración, como software inteligente y tecnologías móviles, para orquestar y optimizar estos procesos. Este enfoque basado en software puede ayudarle a aprovechar al máximo los robots y reducir el tiempo y el esfuerzo de los compañeros de trabajo humanos, a menudo sin necesidad de nuevos sistemas de automatización o cambios en la distribución del almacén o los sistemas de almacenamiento.
Mito n.º 2: su WMS es la mejor herramienta para gestionar flujos de trabajo entre humanos y robots
Otra creencia común es que su sistema de gestión de almacenes (WMS) existente es la mejor herramienta para gestionar flujos de trabajo que involucran tanto a humanos como a robots. Sin embargo, la mayoría de las soluciones WMS siguen una lógica básica y rutas de selección de secuencia de ubicación al asignar el trabajo, sin considerar la optimización de lotes y rutas en el contexto de la colaboración entre humanos y robots.
Para optimizar verdaderamente la toma de decisiones y la ejecución de tareas en un sistema que involucra humanos y robots, es esencial implementar una capa adicional que sincronice los tres componentes bajo una sola entidad de control. Las soluciones WMS a menudo carecen de esta capacidad, ya que normalmente siguen una secuencia de ubicación fija utilizando un camino de serpiente alrededor de la instalación, lo que no siempre es óptimo.
Incluso si un WMS tiene algunas rutas optimizadas, a menudo están codificadas y son inflexibles. Para lograr un enfoque verdaderamente dinámico, se requiere una solución que permita ajustes intuitivos en tiempo real. Esta capa adicional de optimización puede ayudar a garantizar que los humanos y los robots trabajen juntos de manera eficiente, minimizando la pérdida de tiempo y esfuerzo.
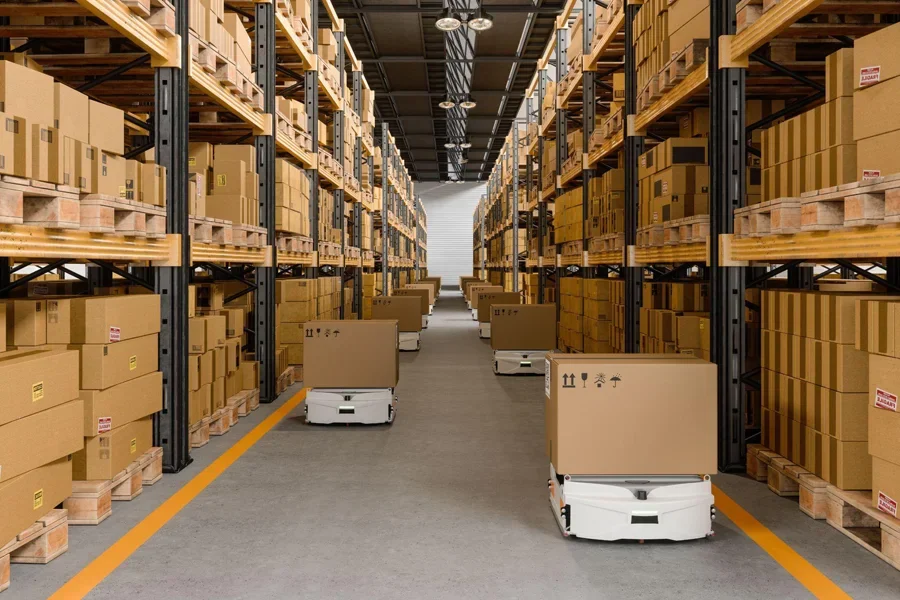
Mito n.º 3: el software AMR puede optimizar perfectamente la coordinación entre humanos y robots
Mucha gente cree que el software proporcionado por los proveedores de AMR es capaz de optimizar perfectamente la coordinación entre humanos y robots. Sin embargo, es importante comprender que los AMR están diseñados para optimizar el rendimiento del robot, no necesariamente el rendimiento humano.
Hay dos procesos comunes que involucran a los AMR: estilos de seguimiento del robot/cobot y selección de zonas. En la selección de cobots, un humano sigue al robot, a menudo en función de las tareas asignadas por el WMS. La selección de zonas mantiene a los humanos en una zona fija, lo que reduce los viajes humanos pero requiere que los recolectores sean asignados a las zonas correctas y estén listos para los AMR. Ambos enfoques pueden ser bastante estáticos y es posible que no optimicen completamente los viajes humanos.
La verdadera optimización implica tres aspectos clave: priorización del trabajo, optimización de lotes y búsqueda de la ruta de selección más eficiente. En el mejor de los casos, el sistema debería considerar estas prioridades justo a tiempo, aumentando la densidad de selección y creando mejores lotes. A medida que ingresan nuevos pedidos al sistema, deben ubicarse automáticamente y priorizarse de manera adecuada. Los jefes y supervisores del almacén deben tener control total sobre el cambio de prioridad de sus pedidos, garantizando que el sistema funcione según demanda y siempre proporcione un trabajo con una prioridad óptima cuando un usuario lo solicite.
Mito n.º 4: Los robots por sí solos pueden minimizar los viajes de los trabajadores
Otro error común es que los propios robots pueden minimizar los desplazamientos de los trabajadores en el almacén. Si bien la selección por zonas puede reducir los viajes humanos al mantener a los trabajadores en un área específica, es poco probable que la selección por robots logre el mismo resultado.
En el picking con cobot, el trabajador humano recorre el almacén con el robot, siguiendo el mismo camino. Aunque una ruta robótica optimizada puede conducir a una ruta más eficiente para el humano, el concepto aún implica que el humano y el robot estén unidos, lo que puede no siempre ser el enfoque más eficiente.
La recolección basada en zonas, por otro lado, puede reducir los viajes humanos, pero es un sistema muy rígido. En este escenario, los humanos están asignados a zonas específicas y deben estar presentes cuando llega un robot para recoger y cargar artículos. Si un trabajador necesita tomar un descanso o no es reemplazado, toda la solución puede comenzar a desmoronarse. Además, equilibrar la fuerza laboral en un sistema basado en zonas puede ser un desafío, ya que las demandas de recolección pueden variar significativamente de un día a otro, lo que genera personal subutilizado o con exceso de trabajo en ciertas zonas.
Para minimizar realmente los viajes de los trabajadores, es esencial armonizar los viajes tanto de los robots como de los humanos. Este enfoque permite a los trabajadores viajar dinámicamente a la ubicación de recolección más optimizada y cumplir con el AMR allí, reduciendo los viajes y manteniendo la flexibilidad. Al incorporar una capa de orquestación que minimice el tiempo de los trabajadores en la zona de recogida, las empresas pueden crear un sistema más eficiente y adaptable que optimice el rendimiento tanto humano como robótico.
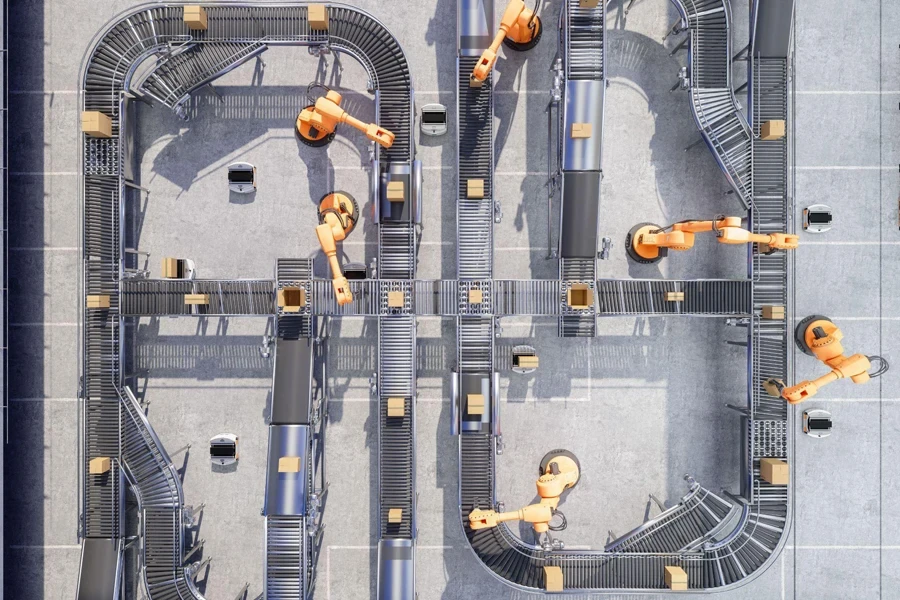
Mito #5: Los sistemas existentes son suficientes para orquestar el trabajo entre humanos y robots
Por último, existe la creencia común de que los sistemas existentes, como el software WMS y AMR, son suficientes para orquestar el trabajo de humanos y robots en el almacén. Sin embargo, estos sistemas a menudo carecen de verdaderas capacidades de orquestación, centrándose más en la siguiente selección más fácil, donde ya hay un robot presente en el mismo pasillo.
Para lograr una verdadera optimización, es fundamental incorporar software del sistema e inteligencia artificial (IA) que proporcionen la inteligencia necesaria. El objetivo principal de la optimización debe ser minimizar la ruta de selección humana, que a menudo los sistemas AMR y WMS pasan por alto.
La verdadera orquestación y optimización no sigue un enfoque rígido de selección basado en zonas. En cambio, emplean un modelo híbrido en el que el sistema toma decisiones dinámicamente en varios puntos para reducir los viajes humanos. Esta flexibilidad y toma de decisiones dinámica distinguen la verdadera orquestación y optimización de los sistemas tradicionales.
Por ejemplo, en un flujo de trabajo de recolección respaldado por AMR, un trabajador puede evitar caminar innecesariamente recogiendo artículos en un contenedor en un AMR, dirigiendo el AMR a un sistema transportador para descargar y luego activando otro robot para que se mueva a su lugar para que el trabajador pueda seguir recogiendo. Las interfaces con los robots y los trabajadores pueden dirigirse por voz, de forma similar a los sistemas de selección por voz convencionales, y los trabajadores confirman su trabajo mediante voz, escaneo, RFID o pantallas o luces montadas en robots.
Conclusión
En conclusión, la integración de robots y trabajadores humanos en el almacén es un proceso complejo que requiere una comprensión profunda de los diversos desafíos y conceptos erróneos que rodean el tema. Al desacreditar estos cinco mitos comunes, las empresas pueden comprender mejor la importancia de una orquestación y optimización efectivas para lograr todos los beneficios de la colaboración entre humanos y robots.
Para integrar con éxito robots y humanos en el almacén, las empresas deben abordar los desafíos laborales incorporando robots en múltiples flujos de trabajo, asignando dinámicamente trabajadores y robots para maximizar la productividad y mejorando la ergonomía y la seguridad. Al utilizar software inteligente, inteligencia artificial y un enfoque híbrido y flexible de orquestación, las empresas pueden desbloquear el verdadero potencial de la colaboración entre humanos y robots y mantenerse a la vanguardia en un mundo cada vez más automatizado.
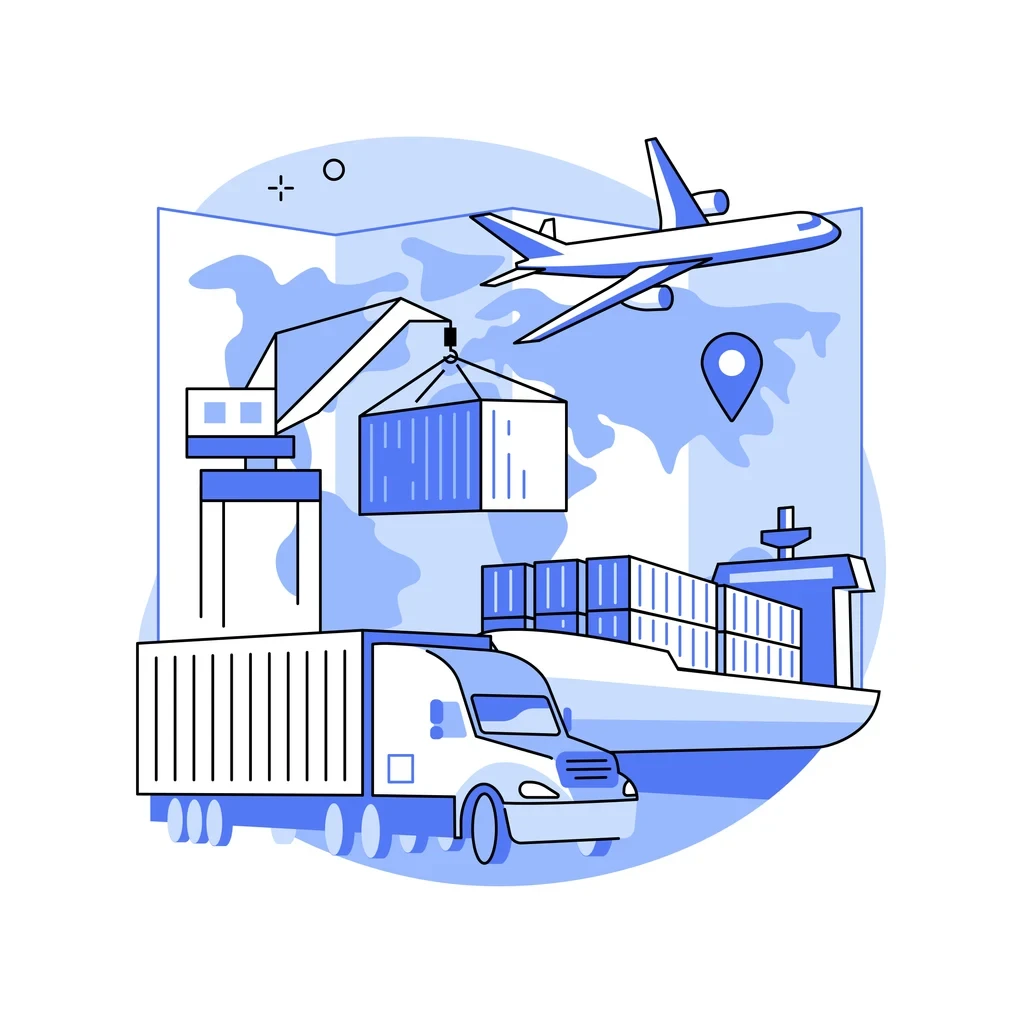
¿Busca una solución logística con precios competitivos, visibilidad total y atención al cliente de fácil acceso? Revisar la Mercado logístico de Chovm.com .