En el Campus de Fabricación Aditiva de Oberschleißheim, el Grupo BMW está probando la fabricación aditiva por arco eléctrico (WAAM), en la que se funde un alambre de aluminio o similar mediante un arco. A continuación, un robot controlado por software coloca con precisión un gran número de cordones de soldadura unos encima de otros, hasta obtener un componente completo.
Debido a que la presión hace que capa por capa no sea necesario prestar atención a la desmoldeabilidad, son posibles estructuras huecas con una relación óptima entre rigidez y peso.
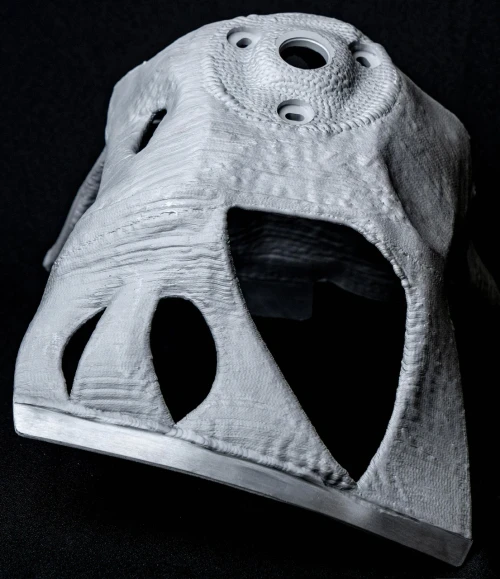
Esto significa que los componentes pueden ser más ligeros y rígidos que las piezas de fundición a presión comparables que se fabrican actualmente en serie. También se pueden producir de forma más sostenible gracias a menores requisitos energéticos y menos desperdicio de material. En el futuro, el plan es utilizar componentes fabricados mediante el proceso WAAM en los vehículos de producción del Grupo BMW.
La gran anchura y altura de una sola costura de soldadura permite fabricar componentes con WAAM de forma extremadamente rápida. A diferencia de la fusión por rayo láser, que ya se utiliza en la producción de prototipos y series pequeñas en el Grupo BMW, WAAM es especialmente adecuado para componentes más grandes. Los espesores de pared típicos se adaptan bien a los componentes de la carrocería, la transmisión y el chasis. Sin embargo, también se pueden fabricar herramientas y dispositivos mediante este proceso de alta tecnología, que también se utiliza en la industria de la aviación.
Los empleados del Grupo BMW se centran desde 2015 en el proceso WAAM, también conocido como soldadura por acumulación. Desde 2021 se utiliza una célula WAAM para la producción de componentes de prueba en el Campus de Fabricación Aditiva. Una de estas aplicaciones de ejemplo es una Soporte telescópico, que se compara tras exhaustivas pruebas en el banco de pruebas con el componente de serie fabricado mediante fundición a presión de aluminio.
En esta primera etapa ya está claro que el proceso WAAM puede dar lugar a menores emisiones en el proceso de producción. El menor peso de los componentes, su ventajosa relación de uso de material y la posibilidad de utilizar energía renovable permiten producir los componentes de forma más eficiente.
—Jens Ertel, director de fabricación aditiva de BMW
La siguiente etapa de desarrollo en el camino hacia la producción en serie son las pruebas de componentes del vehículo, que comenzarán en un futuro previsible.
Debido a las costuras de soldadura más anchas en el proceso WAAM, las superficies de los componentes no son lisas, sino ligeramente onduladas y deben ser repasadas en zonas críticas. Sin embargo, los ingenieros del Grupo BMW pudieron demostrar que los componentes WAAM se pueden utilizar para cargas elevadas, incluidas cargas cíclicas, incluso sin tratamiento posterior de la superficie.
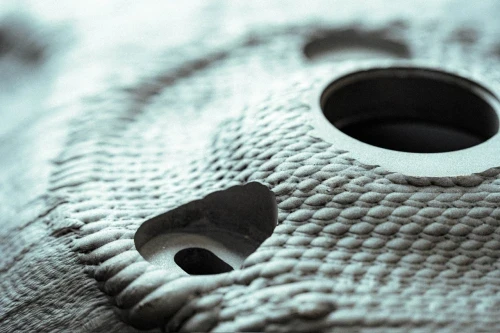
Los parámetros de proceso optimizados son cruciales para garantizar la durabilidad directamente desde la producción, por lo que la combinación del proceso de soldadura y la planificación robótica de la ruta debe coordinarse de manera óptima.
Para hacer un uso óptimo de los componentes producidos en el proceso WAAM, la combinación del proceso de fabricación y un diseño general de nuevos componentes es primordial. Con este fin, BMW Group continúa acelerando el uso del diseño generativo. Aquí, la computadora utiliza algoritmos para diseñar componentes optimizados según los requisitos específicos.
Estos algoritmos se desarrollan en estrecha colaboración con equipos interdisciplinarios y están inspirados en parte en procesos evolutivos de la naturaleza. Al igual que con las estructuras biónicas, el primer paso es utilizar sólo el material que realmente se necesita para la topología del componente y, durante el ajuste fino del segundo paso, el componente se refuerza sólo cuando sea necesario. En última instancia, esto da como resultado componentes más ligeros y rígidos, así como una mayor eficiencia y una mejor dinámica del vehículo.
Los diferentes procesos de producción aditiva no necesariamente compiten entre sí, sino que deben considerarse complementarios. Por ejemplo, la fusión por rayo láser seguirá siendo más ventajosa que el proceso WAAM cuando se trata del mayor nivel de resolución de detalles. Sin embargo, en términos del posible tamaño del componente y la tasa de deposición, la fabricación aditiva por arco eléctrico es superior.
El Grupo BMW planea inicialmente una producción centralizada de componentes WAAM en Oberschleißheim; en el futuro, también es posible la producción en otros lugares y el uso de la tecnología por parte de los proveedores. Además, sería posible incluso producir componentes individuales directamente en la línea de montaje utilizando este proceso y fabricar diferentes piezas sin nuevas herramientas, simplemente cambiando el software. La sostenibilidad también se puede mejorar aún más aumentando el uso de metales reciclados.
Fuente de Congreso de coches ecológicos
Descargo de responsabilidad: La información establecida anteriormente es proporcionada por greencarcongress.com independientemente de Chovm.com. Chovm.com no representa ni garantiza la calidad y confiabilidad del vendedor y los productos.