En 2025, el mercado de discos para amoladoras de hormigón evolucionará con nuevos avances tecnológicos y tendencias ecológicas. Este artículo ofrece un análisis profundo del mercado, los tipos de discos y los criterios de selección esenciales, ofreciendo información valiosa para que los compradores profesionales tomen decisiones informadas.
Índice:
– Comprender el mercado de discos para amoladoras de hormigón
– Diferentes tipos de discos para amoladoras de hormigón
– Factores a tener en cuenta al seleccionar discos para amoladoras de hormigón
– Cómo mantener y reemplazar los discos de amoladora de concreto
– Beneficios de utilizar discos de amoladora de hormigón de alta calidad
– Consideraciones finales sobre la selección de discos para amoladoras de hormigón
Comprender el mercado de discos para amoladoras de hormigón
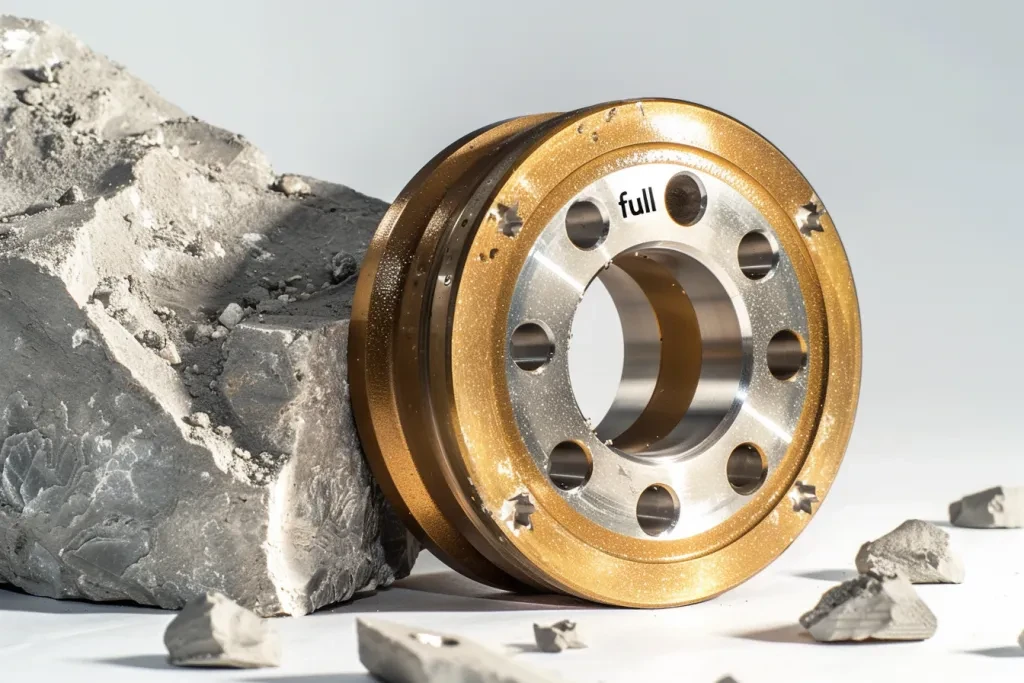
Actores clave en la industria de discos para amoladoras de hormigón
El mercado de discos para amoladoras de hormigón está dominado por varios actores clave que se han consolidado a través de la innovación y la calidad. Empresas como 3M Company, Carborundum Universal Ltd. y NORITAKE Co., Ltd. lideran el mercado con sus soluciones de amolado avanzadas. Estas empresas tienen una presencia significativa en el mercado en varias geografías, incluidos EE. UU., China y Europa. Por ejemplo, 3M Company ha estado a la vanguardia del desarrollo de discos de amolado de alto rendimiento que satisfacen las necesidades de las industrias de la construcción y la fabricación.
Además de estos gigantes, otros actores destacados incluyen Camel Grinding Wheels Works Sarid Ltd. y DEERFOS Co., Ltd. Estas empresas se han centrado en ampliar sus carteras de productos para incluir una amplia gama de discos de rectificado adecuados para diferentes aplicaciones. El panorama competitivo se caracteriza por la innovación continua, con empresas que invierten mucho en investigación y desarrollo para mejorar el rendimiento y la durabilidad de sus productos. Por ejemplo, NORITAKE Co., Ltd. ha estado desarrollando muelas de rectificado diseñadas a medida para aplicaciones específicas, lo que permite obtener resultados superiores con menos tiempo de inactividad y desperdicio de material.
El mercado también está siendo testigo de la entrada de nuevos actores que aprovechan tecnologías avanzadas para obtener una ventaja competitiva. Empresas como DSA Products Ltd. y Kure Grinding Wheel están dando pasos importantes al introducir productos innovadores que satisfacen las necesidades cambiantes de la industria. Estos nuevos participantes se están centrando en nichos de mercado y aplicaciones especializadas, creando así un entorno de mercado diverso y competitivo.
Demanda y tendencias del mercado
La demanda de discos para amoladoras de hormigón está impulsada por varias tendencias clave del mercado, incluido el enfoque cada vez mayor en la fabricación de precisión y el crecimiento de la industria de la construcción. El mercado mundial de muelas abrasivas, que incluye discos para amoladoras de hormigón, fue de aproximadamente USD 20.7 mil millones en 2023 y se proyecta que alcance los USD 25.0 mil millones para 2030, creciendo a una CAGR del 2.8%. Este crecimiento se atribuye a la creciente demanda de productos de alta calidad y acabado fino en varias industrias, incluidas la automotriz, la aeroespacial y la construcción.
Los avances tecnológicos también están desempeñando un papel crucial en la conformación del mercado. Las innovaciones en materiales abrasivos, como el diamante y el nitruro de boro cúbico (CBN), están mejorando las capacidades de corte de los discos de desbaste, lo que les permite trabajar en materiales más duros con mayor precisión. Los avances en las tecnologías de unión están ampliando la vida útil de los discos de desbaste, reduciendo el desgaste y aumentando su eficiencia en operaciones de desbaste de alta velocidad y alta resistencia. Estos avances tecnológicos están impulsando la adopción de discos de desbaste avanzados en varias industrias, lo que respalda el crecimiento del mercado.
Otra tendencia importante es la creciente adopción de soluciones de rectificado respetuosas con el medio ambiente. Los fabricantes se están centrando en el desarrollo de discos de rectificado que produzcan menos polvo y ruido, reduciendo así el impacto medioambiental y mejorando la seguridad en el lugar de trabajo. Esta tendencia es especialmente evidente en regiones con normativas medioambientales estrictas, como Europa y América del Norte. Se espera que el enfoque continuo en la sostenibilidad y la protección del medio ambiente impulse la demanda de discos de rectificado respetuosos con el medio ambiente en los próximos años.
Diferentes tipos de discos para amoladoras de hormigón
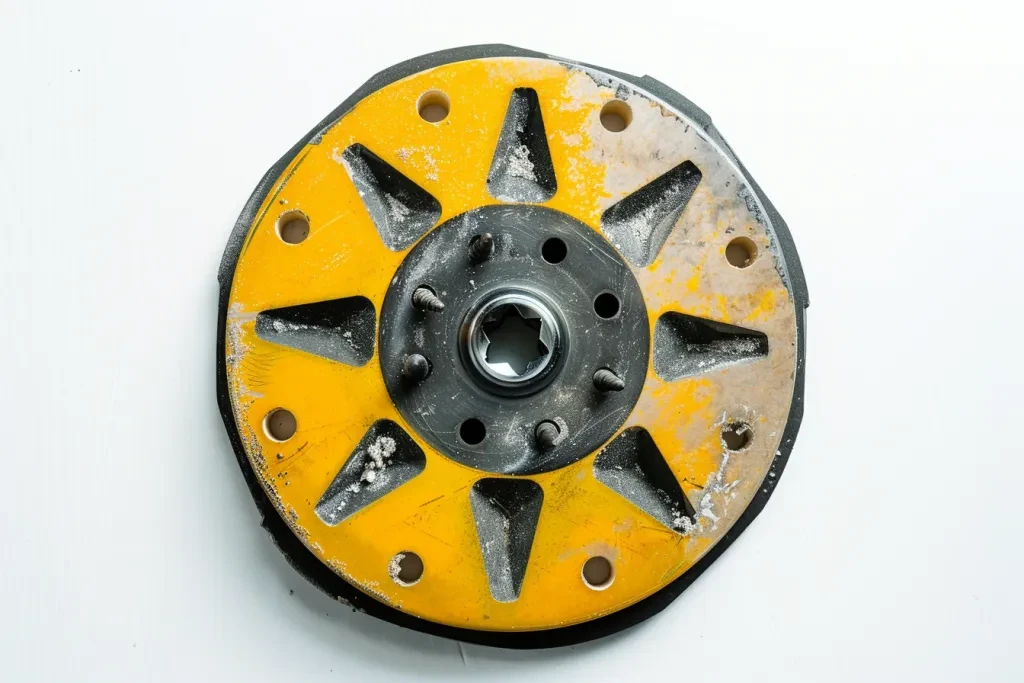
Discos de Diamante
Los discos de diamante se encuentran entre los tipos más populares de discos para amoladoras de hormigón debido a sus capacidades de corte superiores y su durabilidad. Estos discos están incrustados con partículas de diamante, que proporcionan una dureza y una resistencia al desgaste excepcionales. Los discos de diamante son ideales para cortar y amolar materiales duros como hormigón, granito y mármol. Se utilizan ampliamente en proyectos de construcción y renovación donde la precisión y la eficiencia son cruciales.
Se espera que el mercado de discos de diamante crezca significativamente, impulsado por la creciente demanda de soluciones de pulido de alto rendimiento. Según el informe Global Grinding Wheels Market, la adopción de abrasivos de diamante y CBN está en aumento, ya que estos materiales ofrecen capacidades de corte mejoradas y una vida útil más larga. Esta tendencia es particularmente evidente en la industria de la construcción, donde la necesidad de herramientas de pulido eficientes y confiables es primordial.
Además de su rendimiento de corte, los discos de diamante también son conocidos por su versatilidad. Están disponibles en varios tamaños de grano y tipos de aglomerante, lo que los hace adecuados para una amplia gama de aplicaciones. Por ejemplo, los discos de diamante de grano grueso se utilizan para la eliminación agresiva de material, mientras que los discos de grano fino se utilizan para el pulido y el acabado. Esta versatilidad hace que los discos de diamante sean la opción preferida por los profesionales de las industrias de la construcción y la fabricación.
Discos de carburo de silicio
Los discos de carburo de silicio son otro tipo popular de disco para amoladora de hormigón, conocidos por su dureza y filo. Estos discos están hechos de carburo de silicio, un material sintético que proporciona un excelente rendimiento de corte y durabilidad. Los discos de carburo de silicio se utilizan comúnmente para amolar y cortar materiales más blandos, como hormigón, mampostería y piedra. También se utilizan para aplicaciones de preparación y acabado de superficies.
El mercado de discos de carburo de silicio está impulsado por la creciente demanda de soluciones de pulido rentables. El carburo de silicio es relativamente económico en comparación con el diamante, lo que lo convierte en una opción atractiva para los compradores que cuidan su presupuesto. Según el informe Global Grinding Wheels Market, se espera que la demanda de discos de carburo de silicio crezca de manera constante, respaldada por el aumento de las actividades de construcción y los proyectos de desarrollo de infraestructura en todo el mundo.
Los discos de carburo de silicio están disponibles en varios tamaños de grano y configuraciones, lo que permite a los usuarios elegir el disco adecuado para sus necesidades específicas. Por ejemplo, los discos de carburo de silicio de grano grueso se utilizan para la eliminación de material pesado, mientras que los discos de grano fino se utilizan para el pulido y el acabado. La disponibilidad de diferentes tamaños de grano y configuraciones hace que los discos de carburo de silicio sean una opción versátil y rentable para diversas aplicaciones de pulido.
Discos de carburo de tungsteno
Los discos de carburo de tungsteno son conocidos por su excepcional dureza y resistencia al desgaste, lo que los hace ideales para aplicaciones de rectificado de alta resistencia. Estos discos están hechos de carburo de tungsteno, un material que es significativamente más duro que el acero y proporciona un excelente rendimiento de corte. Los discos de carburo de tungsteno se utilizan comúnmente para rectificar y cortar materiales duros como hormigón, metal y cerámica.
Se espera que el mercado de discos de carburo de tungsteno crezca, impulsado por la creciente demanda de herramientas de rectificado de alto rendimiento en diversas industrias. Según el informe Global Grinding Wheels Market, la adopción de materiales abrasivos avanzados como el carburo de tungsteno está en aumento, ya que estos materiales ofrecen capacidades de corte superiores y una vida útil más larga. Esta tendencia es particularmente evidente en las industrias metalúrgica y de la construcción, donde la necesidad de herramientas de rectificado duraderas y eficientes es fundamental.
Los discos de carburo de tungsteno están disponibles en varios tamaños de grano y tipos de aglomerante, lo que los hace adecuados para una amplia gama de aplicaciones. Por ejemplo, los discos de carburo de tungsteno de grano grueso se utilizan para la eliminación agresiva de material, mientras que los discos de grano fino se utilizan para el pulido y el acabado. La versatilidad y durabilidad de los discos de carburo de tungsteno los convierten en la opción preferida de los profesionales de las industrias de la construcción, la metalurgia y la fabricación.
Factores a tener en cuenta al seleccionar discos para amoladoras de hormigón
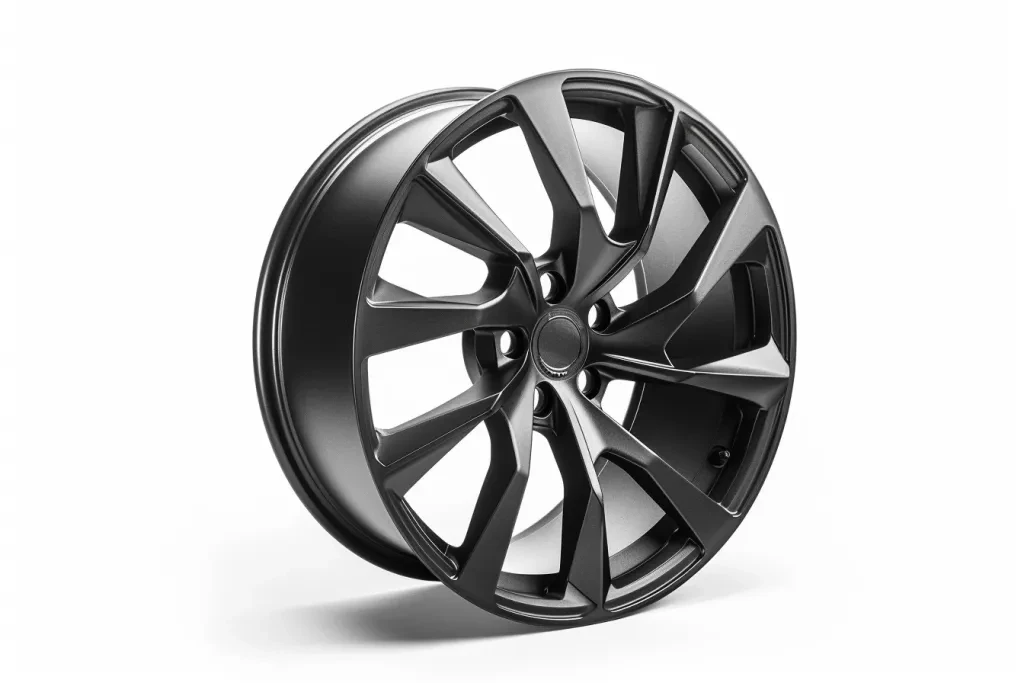
Dureza material
La dureza del material es un factor crítico a tener en cuenta al seleccionar discos para amoladoras de hormigón. La dureza del material que se está moliendo determina el tipo de material abrasivo que se debe utilizar. Por ejemplo, los discos de diamante son ideales para moler materiales duros como el hormigón y el granito, mientras que los discos de carburo de silicio son adecuados para materiales más blandos como la mampostería y la piedra. Según el informe Global Grinding Wheels Market, la adopción de materiales abrasivos avanzados como el diamante y el CBN está en aumento, impulsada por la necesidad de soluciones de pulido eficientes y confiables.
La dureza del disco de amoladora también es importante, ya que afecta a la durabilidad y el rendimiento del disco. Los discos más duros, como los fabricados con diamante y carburo de tungsteno, ofrecen una resistencia al desgaste superior y una vida útil más larga, lo que los hace adecuados para aplicaciones de amolado de alta resistencia. Por otro lado, los discos más blandos, como los fabricados con carburo de silicio, son más rentables y adecuados para tareas de amolado más ligeras. Comprender la dureza tanto del material que se está moliendo como del disco de amoladora es esencial para seleccionar el disco adecuado para el trabajo.
Además de la dureza del material, también se deben tener en cuenta otros factores como el tipo de aglomerante y el tamaño del grano. El tipo de aglomerante afecta el rendimiento de corte y la durabilidad del disco, mientras que el tamaño del grano determina el nivel de eliminación de material y el acabado de la superficie. Al considerar estos factores, los usuarios pueden seleccionar el disco de amoladora adecuado que satisfaga sus necesidades específicas y garantice un rendimiento y una eficiencia óptimos.
Tamaño del grano del disco
El tamaño del grano del disco es otro factor importante a tener en cuenta al seleccionar discos para amoladoras de hormigón. El tamaño del grano se refiere al tamaño de las partículas abrasivas del disco, que determina el nivel de eliminación de material y el acabado de la superficie. Los discos de grano grueso, con partículas abrasivas más grandes, se utilizan para la eliminación agresiva de material y el desbaste basto, mientras que los discos de grano fino, con partículas abrasivas más pequeñas, se utilizan para el pulido y el acabado.
La elección del tamaño de grano depende de la aplicación específica y del acabado de superficie deseado. Por ejemplo, los discos de grano grueso son ideales para eliminar capas gruesas de material, como pintura o revestimientos viejos, mientras que los discos de grano fino se utilizan para lograr una superficie lisa y pulida. Según el informe Global Grinding Wheels Market, la demanda de discos de pulido de alto rendimiento con varios tamaños de grano está en aumento, impulsada por la necesidad de precisión y eficiencia en varias industrias.
Además del tamaño del grano, el tipo de material abrasivo y el tipo de aglomerante también desempeñan un papel crucial a la hora de determinar el rendimiento del disco. Por ejemplo, los discos de diamante con tamaños de grano fino se utilizan para pulir materiales duros como el granito y el mármol, mientras que los discos de carburo de silicio con tamaños de grano grueso se utilizan para pulir materiales más blandos como el hormigón y la mampostería. Al tener en cuenta el tamaño del grano, el material abrasivo y el tipo de aglomerante, los usuarios pueden seleccionar el disco de amoladora adecuado que satisfaga sus necesidades específicas y garantice un rendimiento y una eficiencia óptimos.
Tipo de enlace de disco
El tipo de aglomerante de un disco de amoladora de hormigón es un factor crítico que afecta su rendimiento y durabilidad. El tipo de aglomerante se refiere al material que mantiene unidas las partículas abrasivas en el disco. Los tipos de aglomerante más comunes incluyen aglomerante de resina, metálico y vitrificado, cada uno de los cuales ofrece diferentes niveles de rendimiento y durabilidad. Por ejemplo, los aglomerantes de resina proporcionan flexibilidad y son adecuados para el aglomerante de uso general, mientras que los aglomerantes metálicos ofrecen una durabilidad superior y son ideales para aplicaciones de aglomerante de uso intensivo.
La elección del tipo de aglomerante depende de la aplicación específica y del material que se va a pulir. Por ejemplo, los discos aglomerados con resina se utilizan habitualmente para pulir materiales más blandos, como hormigón y mampostería, mientras que los discos aglomerados con metal se utilizan para pulir materiales más duros, como granito y metal. Según el informe Global Grinding Wheels Market, la demanda de tecnologías de aglomerante avanzadas está en aumento, impulsada por la necesidad de soluciones de pulido duraderas y de alto rendimiento.
Además del tipo de aglomerante, también se deben tener en cuenta otros factores, como el tamaño del grano y el material abrasivo. La combinación de estos factores determina el rendimiento de corte, la durabilidad y la eficiencia del disco. Al seleccionar el tipo de aglomerante adecuado, los usuarios pueden asegurarse de que el disco de amoladora satisfaga sus necesidades específicas y proporcione un rendimiento y una longevidad óptimos.
Compatibilidad con Grinder
La compatibilidad con la amoladora es otro factor importante a tener en cuenta al seleccionar discos para amoladora de hormigón. El disco de amoladora debe ser compatible con el tipo y modelo específico de amoladora que se utilice. Esto incluye factores como el tamaño del disco, el tamaño del eje y la velocidad máxima de funcionamiento. El uso de un disco incompatible puede provocar un rendimiento deficiente, daños en la amoladora y posibles riesgos de seguridad.
El tamaño del disco se refiere al diámetro del disco de la amoladora, que debe coincidir con el tamaño del protector de la rueda de la amoladora. Los tamaños de disco más comunes incluyen 4.5 pulgadas, 7 pulgadas y 9 pulgadas, y los discos más grandes se utilizan para aplicaciones de amolado de alta resistencia. El tamaño del eje se refiere al diámetro del orificio en el centro del disco, que debe coincidir con el tamaño del eje de la amoladora. Los tamaños de eje más comunes incluyen 5/8 pulgadas y 7/8 pulgadas.
La velocidad máxima de funcionamiento del disco de la amoladora también debe ser compatible con la velocidad nominal de la amoladora. El uso de un disco con una velocidad nominal inferior a la de la amoladora puede provocar fallos en el disco y posibles riesgos de seguridad. Al garantizar la compatibilidad con la amoladora, los usuarios pueden garantizar un rendimiento, una seguridad y una eficiencia óptimos.
Costo y Presupuesto
El costo y el presupuesto son factores importantes a tener en cuenta a la hora de seleccionar discos para amoladoras de hormigón. El costo de los discos para amoladoras puede variar significativamente según factores como el tipo de material abrasivo, el tipo de aglomerante, el tamaño del grano y la marca. Por ejemplo, los discos de diamante suelen ser más caros que los de carburo de silicio debido a su mayor rendimiento de corte y durabilidad. Sin embargo, el mayor costo de los discos de diamante se puede justificar por su mayor vida útil y la menor necesidad de reemplazos frecuentes.
Al considerar el costo y el presupuesto, es importante equilibrar el costo inicial del disco de amoladora con su rendimiento y longevidad. Invertir en discos de amoladora de alta calidad puede resultar en ahorros de costos a largo plazo al reducir la necesidad de reemplazos frecuentes y mejorar la eficiencia general. Según el informe Global Grinding Wheels Market, la demanda de soluciones de amolado rentables y de alto rendimiento está en aumento, impulsada por la necesidad de mejorar la productividad y reducir los costos operativos.
Además del costo del disco de amoladora, también se deben considerar otros factores como la aplicación específica, el material que se va a amolar y el acabado superficial deseado. Al evaluar cuidadosamente estos factores, los usuarios pueden seleccionar el disco de amoladora adecuado que satisfaga sus necesidades específicas y ofrezca la mejor relación calidad-precio.
Cómo mantener y reemplazar los discos de amoladora de concreto
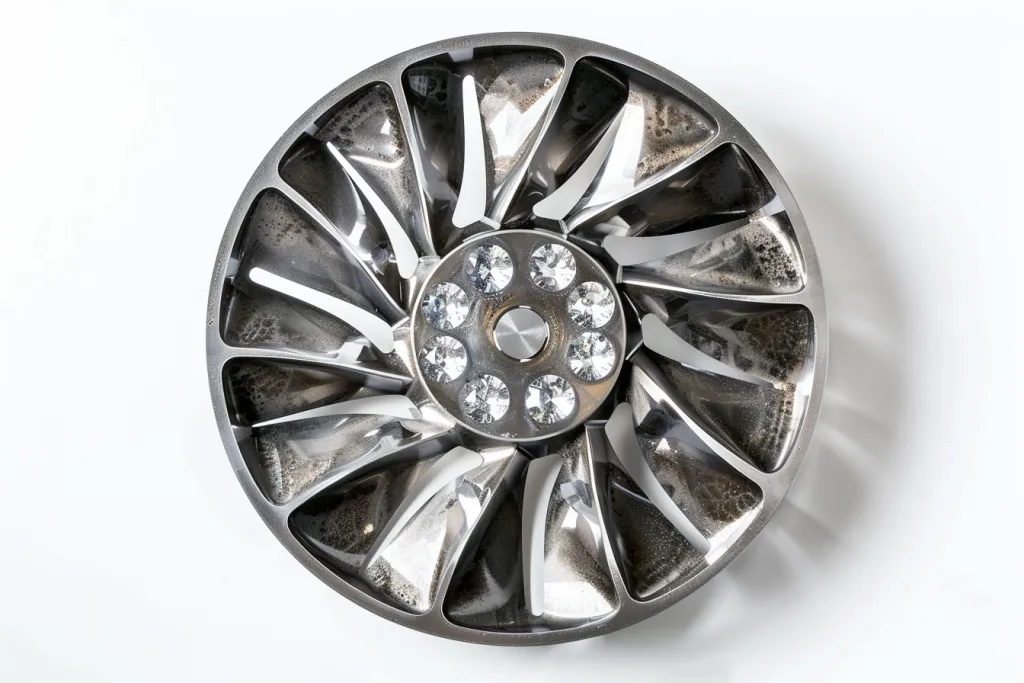
Técnicas de limpieza adecuadas
La limpieza adecuada de los discos de la amoladora de hormigón es esencial para mantener su rendimiento y longevidad. Comience por desconectar la amoladora de la fuente de alimentación para garantizar la seguridad. Utilice un cepillo de alambre o una herramienta de limpieza especializada para eliminar cualquier residuo o acumulación de la superficie del disco. Para una limpieza más profunda, considere utilizar una solución de detergente suave y un paño suave para limpiar el disco, asegurándose de eliminar todos los residuos.
Después de limpiarlo, es fundamental secarlo por completo para evitar la oxidación o la corrosión. Utilice un paño limpio y seco para eliminar la humedad y, si es necesario, deje que el disco se seque al aire. Se debe realizar una limpieza regular después de cada uso para mantener un rendimiento óptimo. Además, inspeccione el disco para detectar cualquier signo de daño o desgaste durante el proceso de limpieza.
En el caso de discos muy sucios, considere utilizar un limpiador químico diseñado específicamente para herramientas abrasivas. Siga atentamente las instrucciones del fabricante para evitar dañar el disco. El almacenamiento adecuado de los discos limpios en un entorno seco y sin polvo prolongará aún más su vida útil y garantizará que estén listos para su uso cuando sea necesario.
Signos de desgaste
Identificar los signos de desgaste en los discos de las amoladoras de hormigón es fundamental para mantener operaciones de pulido efectivas. Un signo común es una disminución notable en la eficiencia del pulido, que puede indicar que la superficie abrasiva se ha desgastado. Además, inspeccione el disco para detectar grietas visibles, astillas o patrones de desgaste desiguales, que pueden comprometer su integridad estructural y su rendimiento.
Otro indicador de desgaste es la presencia de vibraciones o ruidos inusuales durante el funcionamiento. Estos síntomas pueden indicar que el disco ya no está equilibrado o que ha desarrollado irregularidades. También es importante comprobar periódicamente el espesor del disco, ya que un adelgazamiento excesivo puede provocar roturas bajo tensión.
Monitorear el rendimiento del disco y realizar inspecciones visuales de rutina puede ayudar a detectar el desgaste de manera temprana. Reemplazar los discos desgastados o dañados de inmediato evitará posibles riesgos de seguridad y garantizará una calidad de rectificado constante. Llevar un registro del uso del disco y los patrones de desgaste también puede ayudar a predecir los intervalos de reemplazo y mantener un suministro constante de discos funcionales.
Pautas de reemplazo
El reemplazo de los discos de la amoladora de concreto implica varios pasos clave para garantizar la seguridad y una instalación adecuada. Comience por desconectar la amoladora de su fuente de alimentación para evitar la activación accidental. Utilice la herramienta adecuada, como una llave inglesa, para quitar la tuerca de seguridad o la brida que fija el disco en su lugar. Retire con cuidado el disco viejo, prestando atención a su orientación y a las arandelas o espaciadores utilizados.
Antes de instalar el nuevo disco, inspeccione el eje de la amoladora y los herrajes de montaje para detectar cualquier signo de daño o desgaste. Limpie estos componentes para eliminar cualquier residuo que pueda afectar la alineación del disco. Coloque el nuevo disco en el eje, asegurándose de que esté asentado de manera correcta y segura. Vuelva a colocar la tuerca de seguridad o la brida, apretándola de acuerdo con las especificaciones del fabricante.
Después de la instalación, realice una prueba breve para verificar que el disco esté correctamente alineado y equilibrado. Escuche si hay ruidos inusuales y verifique si hay vibraciones excesivas, lo que podría indicar una instalación incorrecta. Reemplazar regularmente los discos desgastados y seguir estas pautas ayudará a mantener un rendimiento óptimo de la molienda y prolongar la vida útil de su equipo.
Beneficios de utilizar discos de amoladora de hormigón de alta calidad
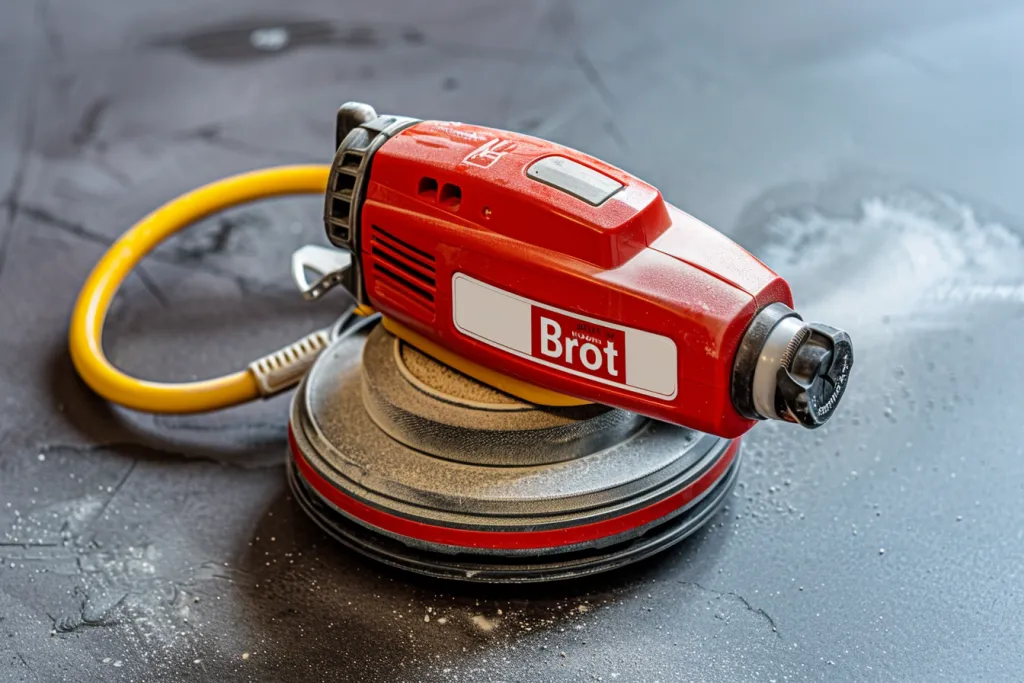
Rendimiento mejorado
Los discos de amoladora de hormigón de alta calidad mejoran significativamente el rendimiento al proporcionar capacidades superiores de corte y amolado. Estos discos suelen estar fabricados con materiales de primera calidad, como diamantes de calidad industrial o cerámica avanzada, que ofrecen una dureza y durabilidad excepcionales. Esto da como resultado velocidades de eliminación de material más rápidas y procesos de amolado más eficientes.
La fabricación precisa de discos de alta calidad garantiza un rendimiento constante y patrones de desgaste uniformes. Esta uniformidad permite un funcionamiento más suave y reduce la probabilidad de que el disco falle durante el uso. Además, los discos de alta calidad suelen contar con tecnologías de unión avanzadas que mejoran su eficiencia de corte y su vida útil.
El uso de discos de alta calidad también minimiza el tiempo de inactividad asociado con los cambios frecuentes de discos y el mantenimiento. El rendimiento y la confiabilidad mejorados de estos discos contribuyen a aumentar la productividad y a ahorrar costos a lo largo del tiempo. Invertir en discos de alta calidad para amoladoras de concreto es una decisión estratégica que puede generar beneficios significativos tanto en el rendimiento como en la eficiencia operativa.
Mayor longevidad
La longevidad de los discos para amoladoras de hormigón aumenta considerablemente cuando se utilizan productos de alta calidad. Estos discos están diseñados para soportar los rigores de las aplicaciones de amolado de alta resistencia, ofreciendo una vida útil más prolongada en comparación con los discos estándar. El uso de materiales abrasivos superiores y técnicas de unión avanzadas garantiza que los discos de alta calidad mantengan su filo durante períodos más prolongados.
Una mayor longevidad se traduce en menos reemplazos y menores costos operativos. Los discos de alta calidad son menos propensos a sufrir desgaste y daños prematuros, lo que significa que pueden soportar más ciclos de rectificado antes de necesitar reemplazo. Esta durabilidad es particularmente beneficiosa en entornos exigentes donde el rendimiento constante es fundamental.
Además, la vida útil prolongada de los discos de alta calidad contribuye a una mejor eficiencia general del equipo. Los operadores pueden confiar en que estos discos funcionarán de manera constante sin necesidad de realizar ajustes o reemplazos frecuentes. Esta confiabilidad mejora la continuidad del flujo de trabajo y reduce la probabilidad de tiempos de inactividad inesperados, lo que en última instancia mejora los plazos y los resultados del proyecto.
Mejor acabado superficial
El uso de discos de pulido de hormigón de alta calidad da como resultado un acabado de superficie superior, algo esencial para muchos proyectos de construcción y renovación. Estos discos están diseñados para proporcionar un pulido preciso y uniforme, lo que minimiza las imperfecciones de la superficie y logra un acabado suave y pulido. Los materiales abrasivos de alta calidad utilizados en estos discos garantizan una acción de corte uniforme, lo que reduce el riesgo de ranuras o pulido desigual.
Un mejor acabado de la superficie no solo mejora el atractivo estético del hormigón, sino que también mejora sus propiedades funcionales. Las superficies lisas son más fáciles de limpiar y mantener, y proporcionan una mejor adherencia para los revestimientos y selladores. Los discos de alta calidad son especialmente eficaces para lograr los acabados finos necesarios para aplicaciones de hormigón decorativo y tareas de alta precisión.
Además, el acabado superficial mejorado que se logra con discos de alta calidad puede reducir la necesidad de pasos de acabado adicionales, como lijar o pulir. Esta eficiencia ahorra tiempo y costos de mano de obra, lo que hace que el proceso de pulido general sea más rentable. Invertir en discos de pulido de hormigón de alta calidad es una opción práctica para lograr resultados de calidad profesional con el mínimo esfuerzo.
Consideraciones finales sobre la selección de discos para amoladoras de hormigón
Seleccionar los discos de amoladora de hormigón adecuados es fundamental para lograr un rendimiento y una durabilidad óptimos. Los discos de alta calidad ofrecen una mayor eficiencia de corte, mayor durabilidad y acabados superficiales superiores, lo que los convierte en una inversión valiosa para cualquier aplicación de amolado. Priorizar la calidad y el mantenimiento adecuado garantizará resultados consistentes y ahorros de costos a largo plazo.