En 2025, el mercado de las máquinas perforadoras está en auge, impulsado por los avances tecnológicos y la creciente demanda industrial. Este artículo proporciona un análisis en profundidad de los factores de selección clave, incluida la especificidad de la aplicación, las especificaciones de la máquina y las consideraciones de costo. Ofrece una valiosa orientación a los compradores profesionales para tomar decisiones informadas, asegurando un rendimiento y una rentabilidad óptimos.
Índice:
- Descripción general del mercado de máquinas perforadoras
-Introducción y análisis detallado del mercado de máquinas perforadoras
- Factores clave a la hora de seleccionar una mandrinadora
-Innovaciones en la tecnología de máquinas perforadoras
-Consideraciones ambientales en las operaciones con máquinas perforadoras
-Tendencias futuras en la tecnología de máquinas perforadoras
-Concluyendo
Descripción general del mercado de máquinas perforadoras
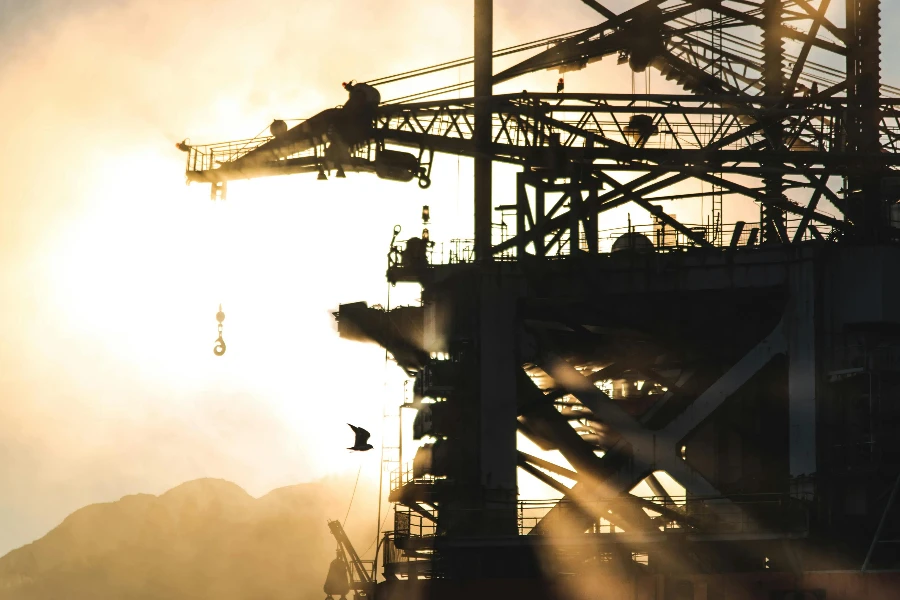
El mercado mundial de máquinas perforadoras ha experimentado un crecimiento significativo en los últimos años. En 2023, el mercado valía aproximadamente 4.4 millones de dólares y se prevé que alcance los 6.2 millones de dólares en 2030, con una tasa de crecimiento anual compuesta del 5.0 %. Este crecimiento está impulsado por los avances en las tecnologías de fabricación y la creciente demanda de industrias como la automotriz, la aeroespacial y la maquinaria pesada. Se espera que el segmento de uso final del transporte experimente el crecimiento más sustancial, alcanzando los 2.9 millones de dólares en 2030 con una tasa de crecimiento anual compuesta del 5.3 %, mientras que se prevé que el segmento de maquinaria general crezca a una tasa de crecimiento anual compuesta del 4.4 %.
A nivel regional, se estimó que el mercado estadounidense alcanzaría los 1.2 millones de dólares en 2023, y se prevé que el mercado de China crezca a una impresionante CAGR del 7.6 %, alcanzando los 1.4 millones de dólares en 2030. Otros mercados importantes son Japón, Canadá, Alemania y la región más amplia de Asia y el Pacífico, todos los cuales se espera que contribuyan al crecimiento general del mercado de máquinas perforadoras.
Introducción y análisis detallados del mercado de máquinas perforadoras
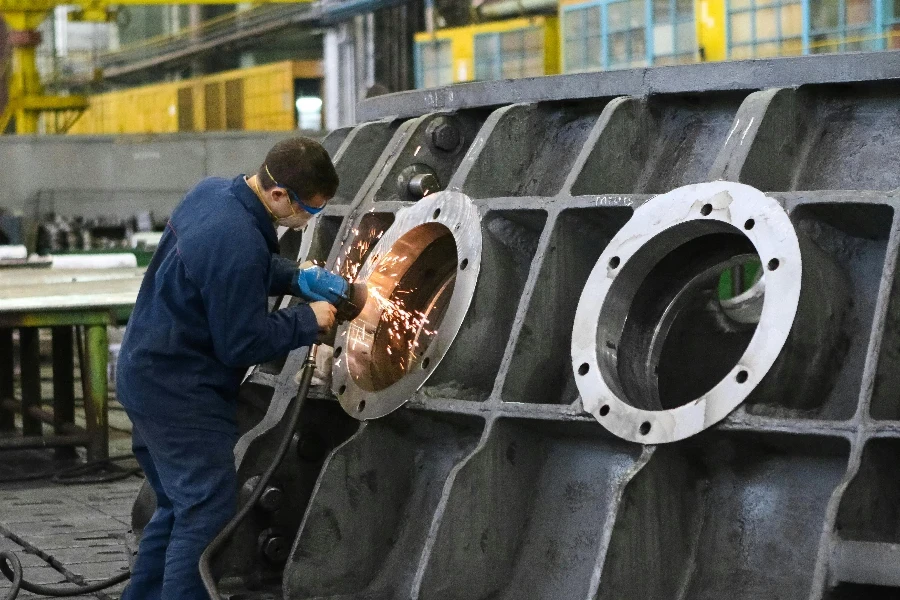
Las máquinas de mandrilar son fundamentales en el mecanizado de precisión, en particular en industrias que requieren alta precisión y acabados suaves, como la automotriz, la aeroespacial y la maquinaria pesada. Estas máquinas están diseñadas para agrandar y terminar agujeros pretaladrados o fundidos con alta precisión, asegurando que el diámetro, el acabado de la superficie y la tolerancia cumplan con las especificaciones exactas. El mercado está segmentado en tipos de mandrilado fino y mandrilado de desbaste, cada uno de los cuales satisface diferentes necesidades según el material y las condiciones de corte.
Los avances tecnológicos han mejorado significativamente el rendimiento y la versatilidad de las máquinas de mandrilado. Innovaciones como los recubrimientos y materiales avanzados para los filos de corte, incluidos el diamante policristalino (PCD) y el nitruro de boro cúbico (CBN), ofrecen una resistencia al desgaste superior y una vida útil más prolongada de la herramienta. Además, los cabezales de mandrilado controlados digitalmente permiten realizar ajustes en tiempo real durante el mecanizado, lo que proporciona una precisión incomparable y reduce los errores. La integración de la tecnología de sensores para el mantenimiento predictivo ha optimizado aún más el proceso de mecanizado y ha reducido el tiempo de inactividad.
A pesar de estos avances, el mercado de las máquinas perforadoras enfrenta desafíos. Mantener la precisión en una amplia gama de materiales, controlar la generación de calor y abordar la tendencia hacia la miniaturización en industrias como la electrónica y los dispositivos médicos son problemas constantes. Los fabricantes están explorando técnicas de enfriamiento avanzadas y desarrollando herramientas más robustas y versátiles para abordar estos desafíos. Las presiones de costos en la fabricación también impulsan la necesidad de máquinas perforadoras más eficientes que puedan ofrecer un alto rendimiento y minimizar el tiempo de inactividad y el desperdicio.
Factores clave a la hora de seleccionar una mandrinadora
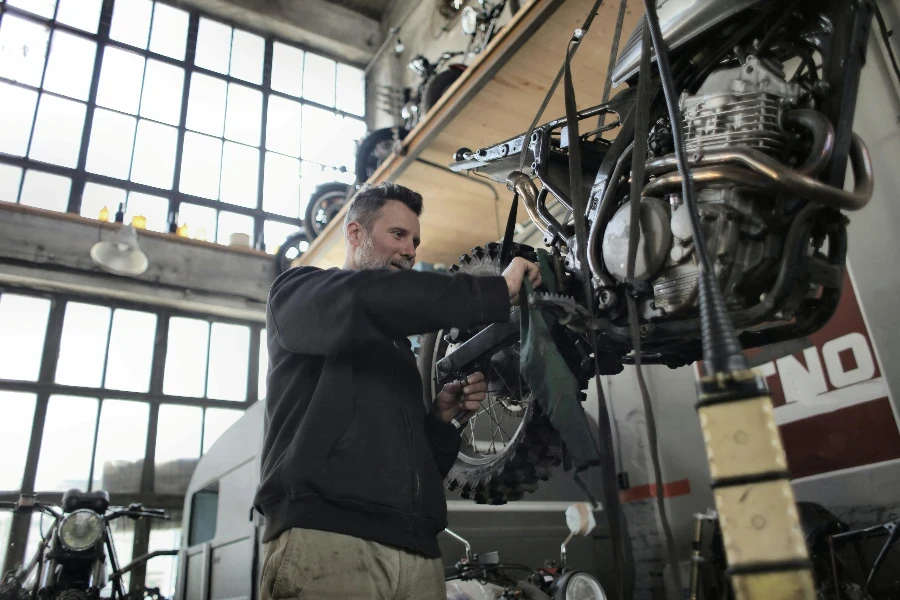
Especificidad de la aplicación
Al seleccionar una mandrinadora, el primer factor a tener en cuenta es la aplicación específica para la que se utilizará. Existen distintas mandrinadoras diseñadas para realizar distintas tareas, como mandrinado de precisión, mandrinado con plantilla, mandrinado con torno, mandrinado vertical y mandrinado horizontal. Por ejemplo, las mandrinadoras de precisión son ideales para producir superficies cilíndricas internas de gran precisión, mientras que las mandrinadoras con plantilla son adecuadas para crear agujeros con dimensiones y ubicaciones precisas. Comprender los requisitos específicos de la tarea ayudará a elegir el tipo de máquina adecuado.
Las máquinas de mandrilado de precisión suelen utilizar operaciones de corte de un solo punto para lograr una precisión de ±0.0001 pulgadas, lo que las hace adecuadas para tareas de alta precisión, como el acabado de superficies de cojinetes internos. Por el contrario, las máquinas de mandrilado horizontales, que pueden manipular piezas de trabajo más grandes y ofrecen capacidades multifuncionales, como fresado y taladrado, son mejores para aplicaciones de trabajo pesado que requieren versatilidad.
La complejidad de la pieza de trabajo, las tolerancias requeridas y el material con el que se trabaja son factores críticos. Por ejemplo, los materiales con mayor dureza, como el acero inoxidable, pueden requerir máquinas equipadas con herramientas de carburo o diamante para mantener la precisión y la eficiencia.
Especificaciones de la máquina
Las especificaciones técnicas de una mandrinadora son fundamentales para garantizar que cumpla con las exigencias de su aplicación. Las especificaciones clave incluyen la velocidad del husillo, la velocidad de avance, la velocidad de corte y la potencia de la máquina. La velocidad del husillo, medida en revoluciones por minuto (RPM), determina la velocidad con la que gira la herramienta de corte y puede afectar la calidad del acabado y la eficiencia del proceso de mecanizado. Por lo general, se requieren velocidades de husillo más altas para acabados más finos y materiales más duros.
La velocidad de avance, que suele medirse en pulgadas por minuto (IPM), indica la velocidad a la que la herramienta de corte avanza en el material. Un equilibrio adecuado entre la velocidad del husillo y la velocidad de avance es fundamental para evitar el desgaste de la herramienta y lograr el acabado superficial deseado. La velocidad de corte, la velocidad a la que el filo de corte de la herramienta se mueve a lo largo de la superficie de la pieza de trabajo, también desempeña un papel importante a la hora de determinar la eficiencia y la calidad del proceso de mandrilado.
Los requisitos de potencia de la máquina, que normalmente se especifican en caballos de fuerza (HP), deben estar en consonancia con la velocidad de eliminación de material y la dureza del material que se está mecanizando. Por ejemplo, las máquinas de mandrilar que trabajan con materiales como acero inoxidable y hierro fundido, que tienen mayores requisitos de potencia unitaria, necesitarán motores más potentes para mantener el rendimiento.
Tolerancia y Precisión
La tolerancia y la precisión son factores críticos a la hora de seleccionar una mandrinadora, especialmente para aplicaciones que requieren una gran precisión. La tolerancia de una mandrinadora se refiere a la desviación admisible de las dimensiones especificadas, que puede variar según el tipo de máquina y la aplicación. Las mandrinadoras de precisión, por ejemplo, pueden alcanzar tolerancias tan ajustadas como ±0.0001 pulgadas, lo que las hace adecuadas para aplicaciones en las que la precisión dimensional es primordial.
Las condiciones ambientales, la geometría de la herramienta y la alineación de los componentes y accesorios de la máquina también influyen en la precisión del proceso de mandrilado. El uso de fluidos de corte puede ayudar a mantener la temperatura de la herramienta, reducir el desgaste y permitir velocidades de corte y de avance más altas, mejorando así la precisión.
Además, la rigidez de la máquina, la pieza de trabajo y la configuración de la herramienta es crucial para mantener la precisión durante el proceso de mandrilado. Las máquinas con una construcción robusta y componentes de alta calidad tienen menos probabilidades de sufrir deflexiones o vibraciones, que pueden comprometer la precisión.
Compatibilidad de materiales
La compatibilidad de la máquina perforadora con diferentes materiales es otro factor importante a tener en cuenta. Las herramientas de perforación suelen estar hechas de acero de alta velocidad (HSS), carburo, cerámica o diamante, cada uno de los cuales es adecuado para diferentes materiales y aplicaciones. Por ejemplo, las herramientas de carburo y diamante son las preferidas para mecanizar materiales duros como el acero inoxidable, mientras que las herramientas HSS son adecuadas para materiales más blandos como el aluminio y el latón.
Comprender las propiedades del material, como la dureza y la maquinabilidad, es esencial para seleccionar la mandrinadora y las herramientas adecuadas. Por ejemplo, los materiales con valores de dureza elevados, como el hierro fundido y el acero inoxidable, requieren herramientas con mayor resistencia al desgaste y velocidades de corte para mantener la eficiencia y la precisión.
Además, la elección del fluido de corte puede afectar el proceso de mecanizado, en particular cuando se trabaja con materiales que generan mucho calor. Los fluidos de corte ayudan a reducir el desgaste de la herramienta, mejoran el acabado de la superficie y aumentan las velocidades de corte, lo que los convierte en un componente vital en las operaciones de mandrilado.
Costo y Presupuesto
Por último, hay que tener en cuenta el coste y el presupuesto de adquisición de una mandrinadora. El precio de las mandrinadoras varía considerablemente en función de su tipo, especificaciones y características. Las mandrinadoras automatizadas y controladas por CNC, que ofrecen mayor precisión y eficiencia, suelen ser más caras que las máquinas manuales o semiautomáticas.
La inversión en una mandrinadora debe estar en consonancia con el rendimiento de la inversión (ROI) esperado y las necesidades específicas de la operación. Para operaciones a pequeña escala o menos frecuentes, puede ser suficiente una máquina de menor costo con funciones básicas. Sin embargo, para la producción en gran volumen o para aplicaciones que requieren alta precisión, invertir en una máquina más avanzada y costosa puede resultar en ahorros de costos a largo plazo a través de una mayor eficiencia y una reducción del tiempo de inactividad.
Los costos de mantenimiento, el reemplazo de herramientas y el consumo de energía también deben tenerse en cuenta en el presupuesto general. Las máquinas con mayor eficiencia energética y menores requisitos de mantenimiento pueden reducir significativamente los costos operativos a lo largo del tiempo.
Innovaciones en la tecnología de las máquinas perforadoras
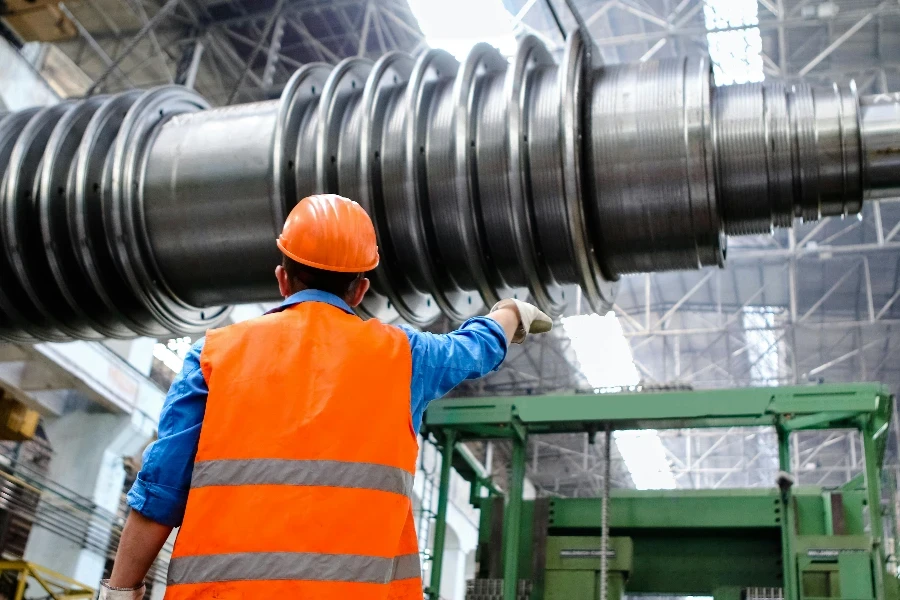
Integración CNC
La integración de la tecnología de control numérico por computadora (CNC) en las máquinas de mandrilar ha revolucionado la industria al mejorar la precisión, la eficiencia y la automatización. Las máquinas de mandrilar CNC se programan mediante código G, lo que permite un control preciso del movimiento, la velocidad y la velocidad de avance de la herramienta de corte. Esta tecnología permite realizar tareas complejas y repetitivas con una mínima intervención humana, lo que reduce la probabilidad de errores y aumenta la productividad.
Las máquinas de mandrilado CNC pueden estar equipadas con funciones avanzadas, como cambiadores automáticos de herramientas, que permiten el uso de múltiples herramientas en una sola operación sin intervención manual. Esta capacidad es particularmente beneficiosa para aplicaciones que requieren diferentes herramientas de corte para varias etapas del proceso de mandrilado, como el desbaste y el acabado.
Además, la tecnología CNC facilita el uso de software de simulación para modelar el proceso de mandrilado antes del mecanizado real, lo que permite identificar posibles problemas y optimizar los parámetros para mejorar la eficiencia y la precisión. Esta capacidad predictiva reduce los tiempos de configuración y minimiza el desperdicio de material, lo que contribuye al ahorro de costos y a la sostenibilidad ambiental.
Materiales de herramientas avanzadas
El desarrollo de materiales avanzados para herramientas ha tenido un impacto significativo en el rendimiento y la durabilidad de las máquinas de mandrilar. Los materiales de alto rendimiento, como el diamante policristalino (PCD) y el nitruro de boro cúbico (CBN), ofrecen una dureza y una resistencia al desgaste superiores en comparación con las herramientas tradicionales de acero de alta velocidad y carburo. Estos materiales permiten velocidades de corte más altas, una vida útil más prolongada de la herramienta y acabados superficiales mejorados, en particular al mecanizar materiales duros y abrasivos.
Las herramientas PCD son ideales para materiales no ferrosos como el aluminio y los materiales compuestos, ya que proporcionan una alta precisión y una vida útil prolongada. Por otro lado, las herramientas CBN son adecuadas para materiales ferrosos como el acero endurecido y el hierro fundido, ya que ofrecen una excelente estabilidad térmica y resistencia al desgaste.
El uso de recubrimientos avanzados, como el nitruro de titanio (TiN) y el óxido de aluminio (Al2O3), mejora aún más el rendimiento de la herramienta al reducir la fricción y la generación de calor durante el proceso de corte. Estos recubrimientos mejoran la evacuación de virutas, reducen el desgaste de la herramienta y permiten velocidades de corte más altas, lo que se traduce en una mayor productividad y ahorro de costos.
Automatización y Robótica
La automatización y la robótica desempeñan un papel cada vez más importante en la industria de las máquinas perforadoras, ya que mejoran la eficiencia, la precisión y la seguridad. Las máquinas perforadoras automatizadas pueden realizar tareas complejas con una mínima intervención humana, lo que reduce los costos de mano de obra y el riesgo de errores. Los sistemas robóticos se pueden integrar con las máquinas perforadoras para automatizar la manipulación de materiales, los cambios de herramientas y las inspecciones de calidad, lo que agiliza aún más el proceso de fabricación.
Por ejemplo, los brazos robóticos pueden cargar y descargar piezas de trabajo, colocarlas con precisión en la máquina y realizar operaciones secundarias como desbarbado y limpieza. Este nivel de automatización no solo aumenta la productividad, sino que también mejora la seguridad en el lugar de trabajo al reducir la necesidad de manipular manualmente materiales pesados y peligrosos.
Los sistemas robóticos también pueden estar equipados con sensores avanzados y algoritmos de aprendizaje automático para supervisar el proceso de taladrado en tiempo real, detectar anomalías y realizar ajustes para optimizar el rendimiento. Esta capacidad mejora la eficiencia y la fiabilidad generales del proceso de mecanizado, lo que reduce el tiempo de inactividad y los costes de mantenimiento.
Consideraciones ambientales en las operaciones con máquinas perforadoras
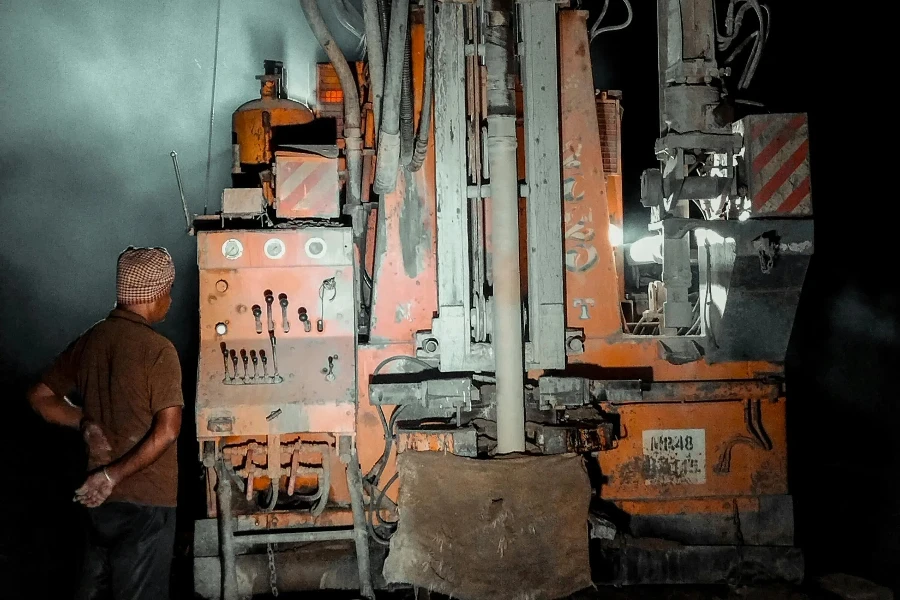
Eficiencia energética
La eficiencia energética es un factor crítico en las operaciones de las máquinas perforadoras modernas, impulsado por la necesidad de reducir los costos operativos y el impacto ambiental. Los avances en la tecnología de motores, como los motores eléctricos de alta eficiencia y los variadores de frecuencia (VFD), han mejorado significativamente la eficiencia energética de las máquinas perforadoras. Estas tecnologías permiten un control preciso de la velocidad y el par del motor, lo que reduce el consumo de energía y optimiza el rendimiento.
Además, el uso de componentes energéticamente eficientes, como iluminación LED y dispositivos electrónicos de bajo consumo, contribuye aún más al ahorro energético general. La implementación de sistemas de gestión energética para supervisar y controlar el uso de energía en tiempo real puede ayudar a identificar ineficiencias e implementar medidas correctivas, lo que se traduce en un ahorro sustancial de costos y una reducción de la huella de carbono.
Reducción de desperdicios
La reducción de desechos es otro aspecto importante de las operaciones sostenibles con máquinas perforadoras. La utilización eficiente de los materiales y los procesos de mecanizado optimizados pueden minimizar el desperdicio de material y reducir el impacto ambiental de la fabricación. El software de simulación avanzado y la tecnología CNC permiten un control preciso del proceso de perforación, lo que reduce las tasas de desechos y mejora el rendimiento del material.
El reciclaje y la reutilización de fluidos de corte, virutas y otros materiales de desecho también pueden contribuir a la reducción de desechos. La implementación de sistemas de circuito cerrado para la gestión de fluidos de corte y el reciclaje de virutas puede minimizar los costos de eliminación de desechos y reducir el impacto ambiental de las operaciones de mecanizado.
Control de emisión
El control de las emisiones de las operaciones con máquinas perforadoras es esencial para mantener un lugar de trabajo seguro y respetuoso con el medio ambiente. El uso de sistemas de filtración avanzados, como colectores de neblina y depuradores de aire, puede capturar y eliminar eficazmente los contaminantes del aire, como la neblina de aceite, los vapores de refrigerante y las partículas en suspensión. Estos sistemas ayudan a mantener la calidad del aire y a cumplir con las normas medioambientales, protegiendo la salud de los trabajadores y de la comunidad circundante.
Además, la selección de fluidos de corte y lubricantes respetuosos con el medio ambiente puede reducir las emisiones nocivas y mejorar la seguridad en el lugar de trabajo. Los fluidos de corte a base de agua y biodegradables ofrecen una alternativa más segura y sostenible a los fluidos tradicionales a base de aceite, lo que minimiza el impacto ambiental de las operaciones de mecanizado.
Tendencias futuras en la tecnología de las máquinas perforadoras
Fabricación inteligente
El auge de la Industria 4.0 y la fabricación inteligente transformarán la industria de las máquinas perforadoras, con una mayor conectividad, análisis de datos y automatización que impulsarán mejoras en la eficiencia y la precisión. Las máquinas perforadoras inteligentes equipadas con sensores y conectividad IoT pueden recopilar y analizar datos en tiempo real, lo que proporciona información valiosa sobre el rendimiento de la máquina, el desgaste de las herramientas y los parámetros del proceso.
Este enfoque basado en datos permite realizar un mantenimiento predictivo, reducir el tiempo de inactividad y prolongar la vida útil de las máquinas y herramientas. Al identificar posibles problemas antes de que provoquen fallas en las máquinas, los fabricantes pueden optimizar los programas de mantenimiento y reducir el riesgo de averías inesperadas, lo que mejora la productividad general y la rentabilidad.
Integración de fabricación aditiva
La integración de la fabricación aditiva (AM) con los procesos de mandrilado tradicionales ofrece nuevas posibilidades para la producción y personalización de piezas complejas. Las máquinas híbridas que combinan capacidades de fabricación aditiva y sustractiva pueden producir geometrías intrincadas y características internas que son difíciles o imposibles de lograr solo con el mecanizado convencional.
La fabricación aditiva permite la creación de piezas con una forma casi perfecta, lo que reduce el desperdicio de material y minimiza la necesidad de un mecanizado exhaustivo. Al combinar la fabricación aditiva con el mandrilado de precisión, los fabricantes pueden lograr acabados de alta calidad y tolerancias ajustadas en piezas complejas, lo que amplía la gama de aplicaciones y mejora la eficiencia general.
Sostenibilidad y Economía Circular
La sostenibilidad y la economía circular son cada vez más importantes en la industria manufacturera, lo que impulsa el desarrollo de tecnologías de mandriladoras más respetuosas con el medio ambiente. Los fabricantes se centran en reducir el consumo de energía, minimizar los residuos y promover la reutilización y el reciclaje de materiales.
La adopción de prácticas sustentables, como el uso de fuentes de energía renovables, la implementación de sistemas de circuito cerrado para la gestión de fluidos de corte y el diseño de máquinas para un fácil desmontaje y reciclaje, desempeñarán un papel crucial en la reducción del impacto ambiental de las operaciones de las máquinas perforadoras.
Resumen
En resumen, la selección de la mandrinadora adecuada implica una consideración cuidadosa de la especificidad de la aplicación, las especificaciones de la máquina, la tolerancia y la precisión, la compatibilidad de los materiales y el costo. Los avances en tecnología, como la integración de CNC, los materiales de herramientas avanzados y la automatización, están impulsando mejoras en la eficiencia, la precisión y la sostenibilidad. Las consideraciones ambientales, incluida la eficiencia energética, la reducción de desechos y el control de emisiones, son cada vez más importantes en las operaciones de las mandrinadoras modernas. Las tendencias futuras, como la fabricación inteligente, la integración de la fabricación aditiva y la sostenibilidad, seguirán dando forma a la industria, ofreciendo nuevas posibilidades y desafíos para los fabricantes.