In 2025, advancements in pressure relief valve technology are revolutionizing industrial safety. This article delves into essential factors for selecting the right valve, including types, performance, materials, and regulatory compliance. Professional buyers will find valuable guidance to make informed purchasing decisions.
Table of Contents:
– Market Overview of Pressure Relief Valves
– In-Depth Analysis of the Pressure Relief Valve Market
– Key Factors When Selecting a Pressure Relief Valve
– Material Considerations for Pressure Relief Valves
– Technological Advancements in Pressure Relief Valves
– Regulatory Compliance and Industry Standards
– Final Thoughts on Pressure Relief Valves
Market Overview of Pressure Relief Valves
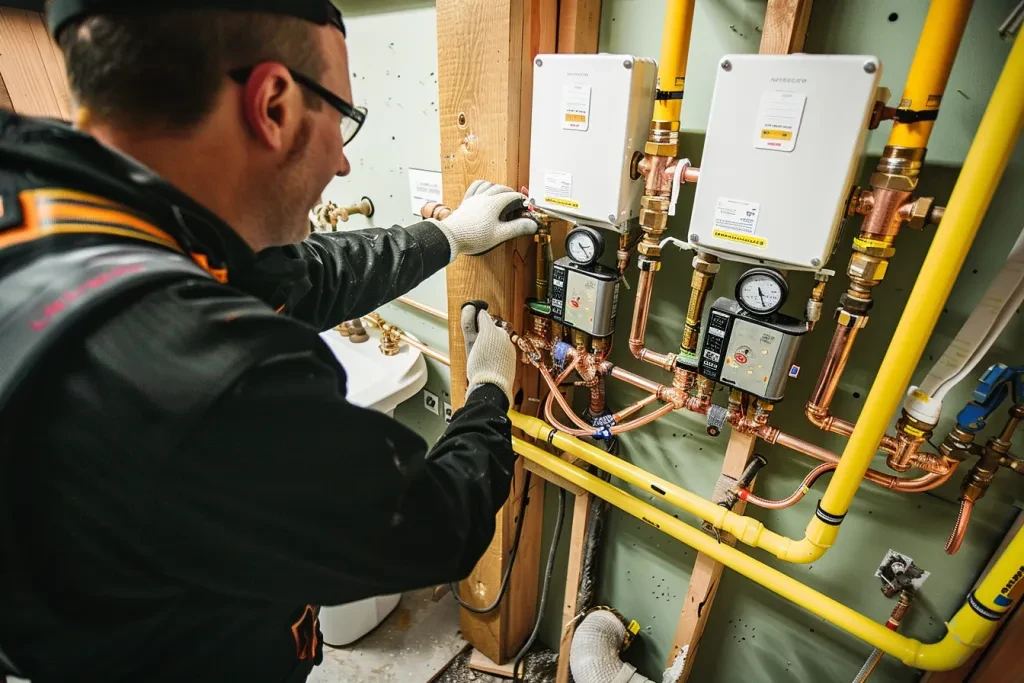
The global market for pressure relief valves was worth approximately USD 4.3 billion in 2023. It is projected to reach around USD 6.0 billion by 2030, growing at a compound annual growth rate (CAGR) of 4.9% from 2023 to 2030. This growth is driven by increasing industrialization and urbanization, which require critical infrastructure with robust safety mechanisms. Stricter regulatory standards and safety protocols in industries such as oil and gas and chemical processing are further boosting demand for advanced pressure relief solutions.
Technological advancements, including the integration of smart sensors and Internet of Things (IoT) connectivity, are enhancing valve performance and reliability. The focus on plant safety and maintenance efficiency in various industries is also increasing the adoption of high-performance pressure relief valves. Additionally, the expansion of renewable energy projects and the need for effective pressure management in energy storage systems are contributing to market growth.
Regionally, the U.S. market was worth USD 736.2 million in 2023, while China is expected to grow at a remarkable CAGR of 6.0%, reaching USD 1.1 billion by 2030. Other key regions, including Japan, Canada, Germany, and the Asia-Pacific, also show promising growth trends.
In-Depth Analysis of the Pressure Relief Valve Market
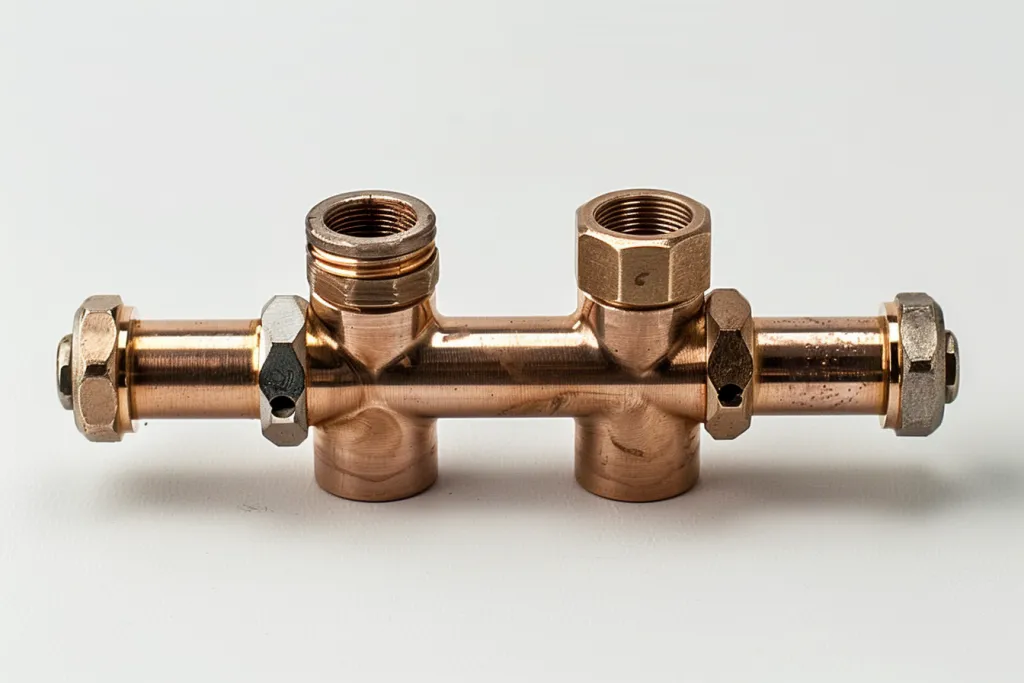
The pressure relief valve market is characterized by key performance benchmarks and market dynamics. The Spring Loaded Pressure Relief Valves segment is expected to reach USD 2.6 billion by 2030, growing at a CAGR of 4.5%. The Pilot Operated Pressure Relief Valves segment is projected to grow at a CAGR of 5.3%. These segments are driven by their reliability and efficiency in maintaining system pressure within safe limits.
Increased investments in infrastructure and industrial projects across emerging economies significantly drive market growth. Consumer behavior is shifting towards more sophisticated and reliable pressure relief systems, influenced by the need for enhanced safety and regulatory compliance. Distribution channels are evolving, with a preference for direct sales and strategic partnerships between manufacturers and end-users to ensure timely and efficient valve supply.
Recent innovations include smart pressure relief valves with advanced monitoring capabilities. These valves provide real-time data on system pressure and valve performance, enabling predictive maintenance and reducing downtime. The product lifecycle of pressure relief valves is also extending due to durable materials and advanced manufacturing techniques.
Digitalization and IoT integration are revolutionizing the market by enabling remote monitoring and control of valve systems. This trend is enhancing operational efficiency and safety across various industries. There is a growing awareness of safety and environmental sustainability, further driving demand for high-quality pressure relief valves.
Customer pain points, such as the need for reliable performance in harsh environments and compliance with stringent safety standards, are being addressed through continuous product innovation and improvement. Brand positioning strategies focus on offering comprehensive solutions, including installation, maintenance, and real-time monitoring services.
Differentiation strategies involve developing customized solutions tailored to specific industry requirements. Niche markets, such as renewable energy and high-pressure applications in the oil and gas sector, are emerging as significant growth areas for pressure relief valve manufacturers.
Key Factors When Selecting a Pressure Relief Valve
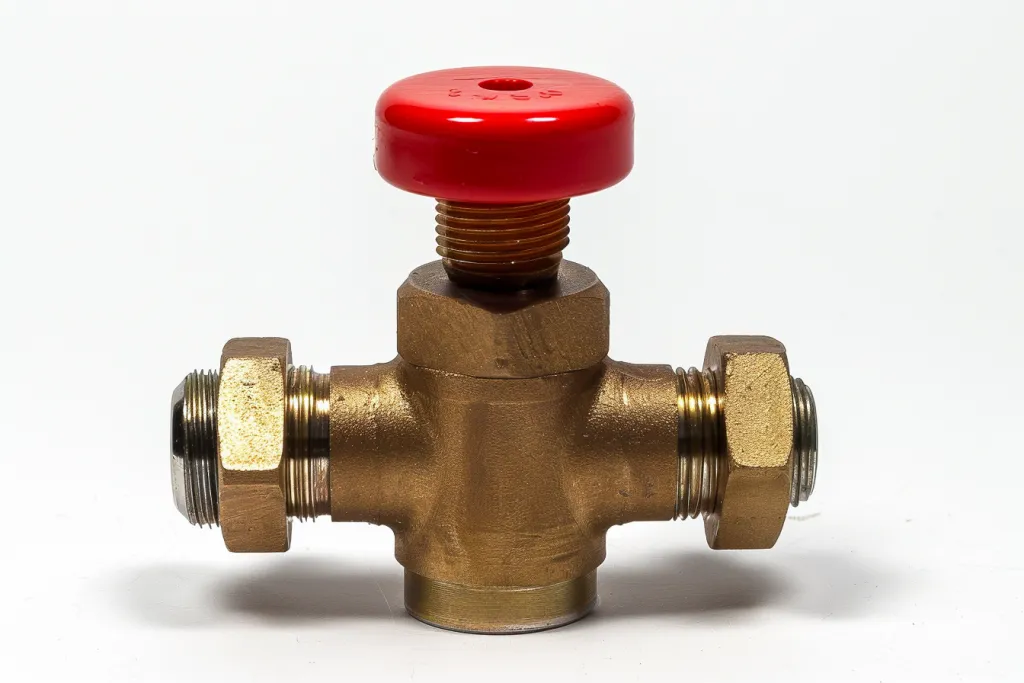
Selecting the right pressure relief valve (PRV) is crucial for ensuring system safety and efficiency. Consider the following key factors:
Types of Pressure Relief Valves
Pressure relief valves come in various types, each suited for specific applications. The most common types are spring-loaded, pilot-operated, and balanced bellows valves.
Spring-loaded valves are the simplest and most widely used. They rely on a spring to hold the valve closed until the system pressure exceeds a preset limit. The spring’s tension can be adjusted to change the relief pressure. They are suitable for a wide range of applications but can be affected by back pressure.
Pilot-operated valves use system pressure to control the opening and closing of the valve. They are more complex than spring-loaded valves but offer higher accuracy and are less affected by back pressure. They are ideal for high-pressure systems and applications requiring precise pressure control.
Balanced bellows valves have a bellows that balances the pressure on both sides of the valve, minimizing the effect of back pressure. They are used in applications where back pressure is a concern, such as in exhaust systems and closed-loop systems.
Performance and Functionality
The performance and functionality of a pressure relief valve are critical to its selection. Key performance parameters include set pressure, blowdown, and capacity.
Set pressure is the pressure at which the valve opens. It should be set slightly above the normal operating pressure of the system to provide protection without unnecessary discharges. The set pressure must be accurate and repeatable to ensure reliable operation.
Blowdown is the difference between the set pressure and the reseating pressure. A smaller blowdown indicates a more sensitive valve that can reseat quickly after relieving excess pressure. This is important for maintaining system pressure stability.
Capacity is the valve’s ability to relieve the required flow rate to prevent system overpressure. The capacity is determined by the valve size, type, and set pressure. It is typically expressed in terms of mass or volumetric flow rate.
Materials and Build Quality
The materials and build quality of a pressure relief valve determine its durability and suitability for different environments and fluids.
Body materials include stainless steel, carbon steel, brass, and bronze. Stainless steel offers excellent corrosion resistance and is suitable for aggressive fluids and harsh environments. Carbon steel provides good strength and is cost-effective for less corrosive applications.
Seal materials must be compatible with the fluid and operating conditions. Elastomers like Viton and EPDM are used for general applications, while PTFE and graphite are used for high-temperature and aggressive chemical environments.
The manufacturing quality and precision of the valve components are crucial for reliable operation. Look for valves from reputable manufacturers with stringent quality control processes and industry certifications.
Safety Standards and Certifications
Compliance with safety standards and certifications ensures that the pressure relief valve meets industry requirements and provides reliable protection.
Valves should comply with standards such as ASME Boiler and Pressure Vessel Code Section VIII and API 526. These standards specify design, testing, and performance requirements for pressure relief valves.
For valves used in Europe, CE marking indicates compliance with the Pressure Equipment Directive (PED), ensuring the valve meets safety and performance requirements.
Depending on the application, other certifications such as ISO 9001 for quality management, and certifications from industry-specific bodies like the American Bureau of Shipping (ABS) or the National Board of Boiler and Pressure Vessel Inspectors may be required.
Ease of Use and Maintenance
The ease of use and maintenance of a pressure relief valve affects its operational reliability and lifecycle costs.
The valve should be easy to install and integrate into the existing system. Consideration should be given to connection types (flanged, threaded, welded), orientation, and space requirements.
The valve should allow for easy adjustment of the set pressure and testing of its operation. Features like external adjustment mechanisms and test levers can simplify these tasks.
The valve should be designed for easy disassembly and reassembly, with readily available replacement parts. Regular maintenance is essential for ensuring long-term reliability and performance.
Material Considerations for Pressure Relief Valves
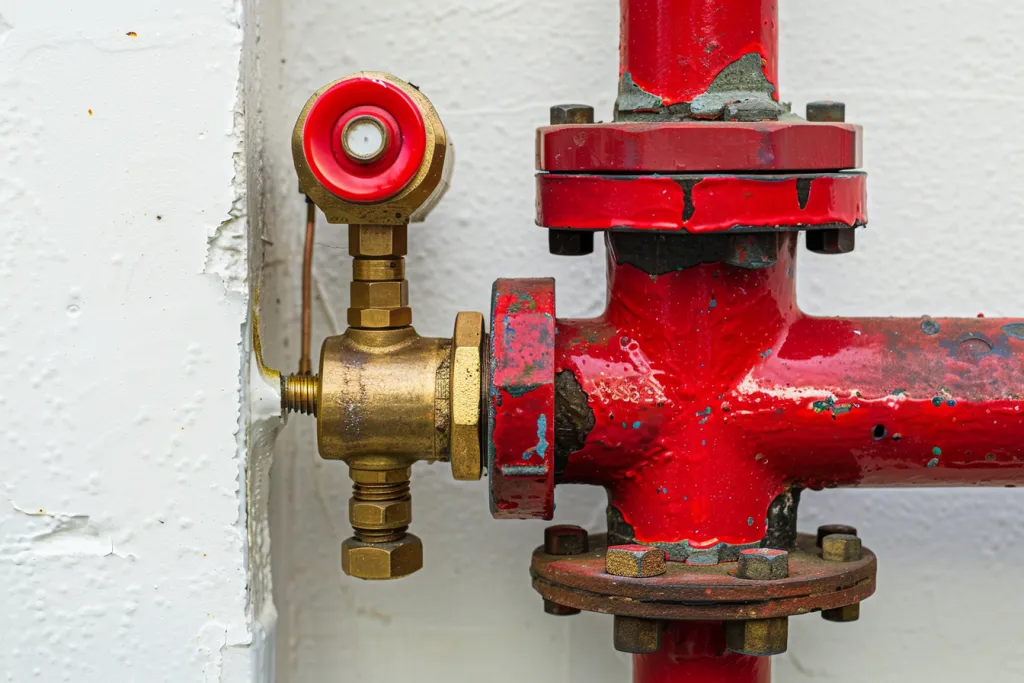
The choice of materials used in the construction of pressure relief valves is critical for ensuring their durability and compatibility with the system they protect.
Body Materials
Pressure relief valve bodies are typically made from metals such as stainless steel, carbon steel, bronze, and brass. Stainless steel is preferred for its excellent corrosion resistance, making it suitable for harsh and aggressive environments. Carbon steel is chosen for its strength and cost-effectiveness in less corrosive applications. Bronze and brass are used in applications where corrosion resistance is needed, but the operating pressures and temperatures are lower.
Seal Materials
The seal materials within a pressure relief valve must be compatible with the fluid being handled and the operating conditions. Common seal materials include elastomers such as Viton and EPDM, which are suitable for general applications. For high-temperature and aggressive chemical environments, PTFE and graphite are often used due to their superior chemical resistance and thermal stability.
Other Components
Other components, such as springs and diaphragms, also require careful material selection. Springs are usually made from stainless steel or Inconel to withstand the stresses and corrosive environments. Diaphragms may be made from elastomers or metals, depending on the application requirements.
Technological Advancements in Pressure Relief Valves
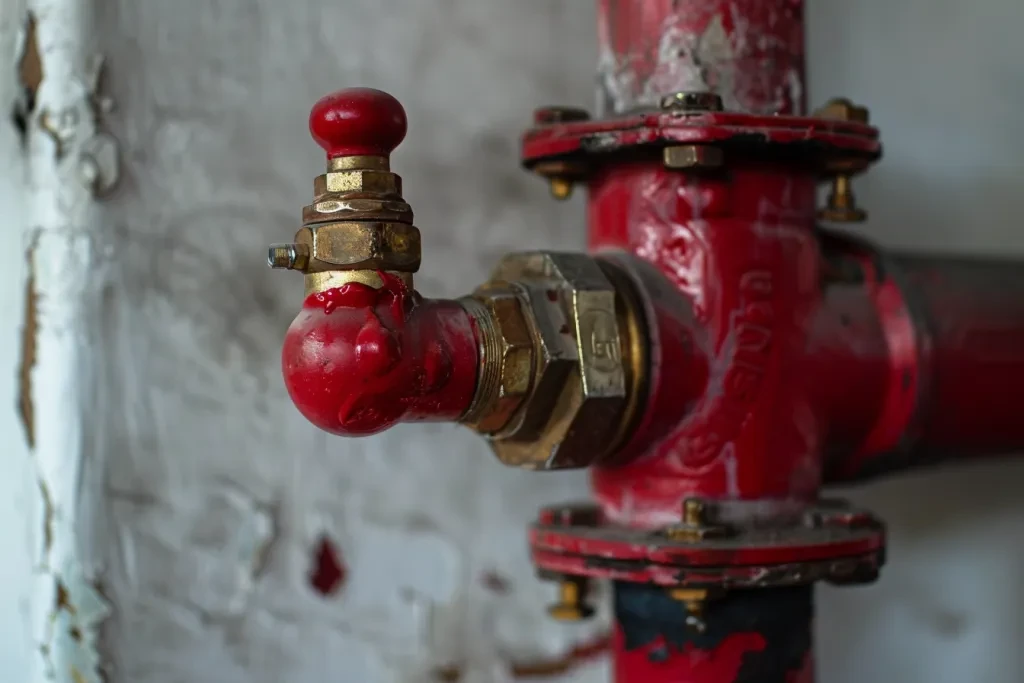
Technological advancements in pressure relief valves have enhanced their performance, reliability, and ease of use.
Smart Valves
Smart pressure relief valves incorporate sensors and digital control systems to monitor and adjust their operation in real-time. These valves can provide data on system pressure, valve position, and performance metrics, enabling proactive maintenance and optimization of system performance. Integration with industrial IoT (IIoT) platforms allows for remote monitoring and control, improving safety and efficiency.
Advanced Materials
The development of advanced materials has improved the durability and performance of pressure relief valves. High-performance alloys and composite materials offer enhanced corrosion resistance, strength, and temperature stability, extending the valve’s service life and reliability in demanding applications.
Computational Fluid Dynamics (CFD)
The use of computational fluid dynamics (CFD) in the design and testing of pressure relief valves has led to more efficient and effective valve designs. CFD simulations allow engineers to analyze fluid flow, pressure distribution, and thermal effects, optimizing the valve’s performance and reducing the need for physical prototypes and testing.
Regulatory Compliance and Industry Standards
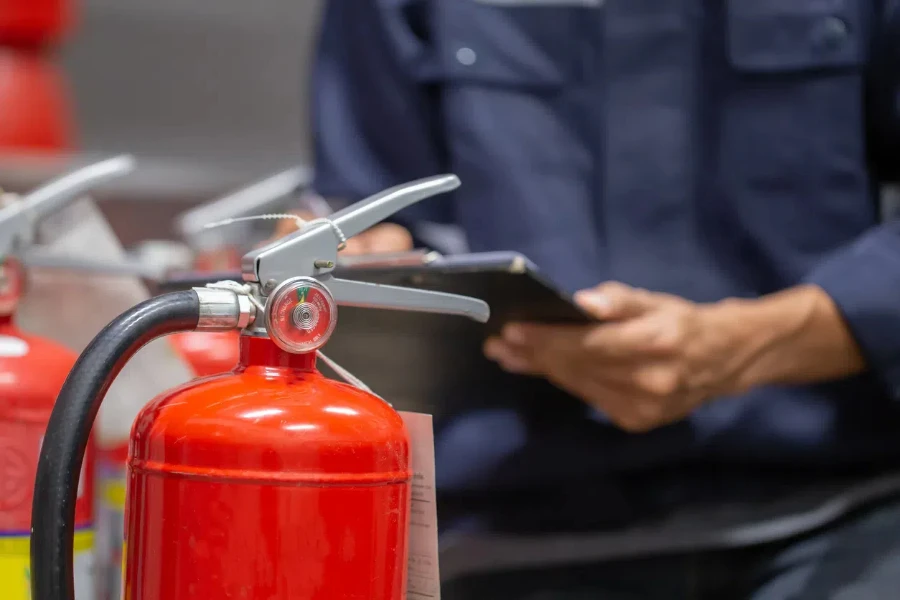
Compliance with regulatory requirements and industry standards is essential for ensuring the safety and reliability of pressure relief valves.
ASME and API Standards
Pressure relief valves must comply with standards such as the ASME Boiler and Pressure Vessel Code Section VIII and API 526. These standards specify requirements for design, materials, manufacturing, testing, and performance, ensuring that the valves provide reliable protection against overpressure.
European Pressure Equipment Directive (PED)
For valves used in Europe, compliance with the Pressure Equipment Directive (PED) is required. The PED sets out essential safety requirements for the design, manufacture, and conformity assessment of pressure equipment, ensuring that the valves meet high safety and performance standards.
Industry-Specific Certifications
Depending on the application, additional certifications may be required. For example, valves used in marine applications may need certification from the American Bureau of Shipping (ABS), while those used in the oil and gas industry may require compliance with ISO 10497 for fire testing.
Final Thoughts on Pressure Relief Valves
Pressure relief valves are critical components in ensuring the safety and efficiency of pressurized systems. Selecting the right valve involves considering factors such as type, performance, materials, safety standards, and ease of use. Technological advancements and compliance with regulatory requirements further enhance the reliability and effectiveness of these valves. By carefully evaluating these factors, businesses can ensure that their systems are protected against overpressure, minimizing the risk of damage and downtime.