The year 2025 has seen a surge in demand for plastic injection molders, driven by advancements across industries. This article provides an in-depth analysis of the crucial factors to consider when selecting a plastic injection molder, offering valuable insights and assistance for professional buyers. Read on to discover how to navigate this thriving market effectively.
Table of Contents:
– Thriving Market for Plastic Injection Molders
– Key Factors to Consider When Selecting a Plastic Injection Molder
– Advanced Features in Modern Plastic Injection Molders
– Future Trends in Plastic Injection Molding
– Wrapping Up
Thriving Market for Plastic Injection Molders
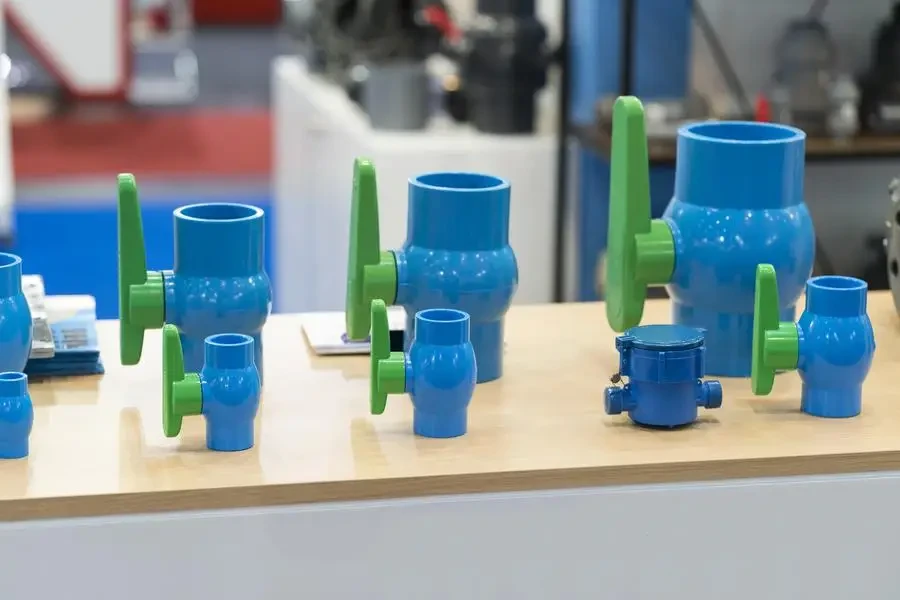
Expanding Global Market Overview
The global plastic injection molding machines market is growing rapidly, driven by increasing demand across various industries. As of 2023, the market was worth USD 11.7 billion and is projected to reach USD 17.8 billion by 2032, with a CAGR of 4.77%. The need for plastic components in automotive, packaging, healthcare, and consumer electronics sectors is a key growth driver. Asia-Pacific leads the market due to rapid industrialization and a booming automotive industry.
The market size is expected to grow from USD 10.05 billion in 2023 to USD 13.78 billion by 2030, with a CAGR of 5.36%. This growth is fueled by advancements in machinery and the increasing use of eco-friendly materials. The automotive industry remains a primary consumer, demanding lightweight and durable plastic components. The packaging sector’s reliance on plastic for efficiency and versatility also drives market expansion.
In 2023, hydraulic machines dominated the market due to their high injection pressure capabilities and cost-effectiveness. However, hybrid machines are expected to gain traction from 2024 to 2032 due to their enhanced efficiency and precision. The 201-500 Ton Force category led the market in 2023 and is projected to experience the highest CAGR during the forecast period, meeting the rising demand for medium-sized molded parts.
In-Depth Market Analysis and Key Dynamics
Plastic injection molding machines are essential for manufacturing a wide range of products, from automotive parts to medical devices. Market growth is supported by technological advancements that improve machine efficiency and precision. Innovations like servo-hydraulic systems have reduced energy consumption, while automation and robotics integration has optimized production processes, minimizing downtime and operational costs.
The automotive sector’s shift towards lightweight components to improve fuel efficiency and reduce emissions is a crucial market driver. Plastic injection molding is ideal for producing intricate parts like dashboards, bumpers, and battery casings for electric vehicles. Similarly, the healthcare industry’s reliance on plastic for medical devices like syringes and surgical instruments boosts demand for injection molding machines, ensuring consistent quality and mass production capabilities.
Consumer behavior is shifting towards sustainable products, driving the adoption of eco-friendly and energy-efficient machines. This trend is evident in the increasing use of recycled and biodegradable plastics. Additionally, the market is witnessing a shift towards direct sales channels, enabling manufacturers to establish closer relationships with customers, enhancing service quality and understanding customer needs. This shift is expected to register the highest CAGR from 2024 to 2032, as it eliminates intermediary costs and potentially increases profit margins.
Technological Advancements and Market Innovations
Technological advancements are reshaping the plastic injection molding industry, with Industry 4.0 technologies playing a pivotal role. Smart sensors, IoT, and AI are enhancing machine performance by enabling predictive maintenance, real-time monitoring, and autonomous operation. These technologies increase production efficiency, reduce human error, and ensure high-quality output, making injection molding a competitive and attractive manufacturing method.
The development of hybrid injection molding machines, combining the precision of electric machines with the power of hydraulic systems, is a notable innovation. These machines offer enhanced efficiency, precision, and repeatability, making them suitable for sectors like automotive and consumer goods. Hybrid machines are projected to register the highest CAGR from 2024 to 2032, driven by the need for energy-efficient and eco-friendly manufacturing solutions.
Sustainability is a critical factor influencing market trends. Manufacturers are focusing on reducing the carbon footprint of their machines through improved energy efficiency and the use of eco-friendly materials. The push towards a circular economy model in manufacturing has increased the emphasis on machine durability and ease of maintenance, ensuring longer lifespans and lower environmental impacts.
Key Factors to Consider When Selecting a Plastic Injection Molder
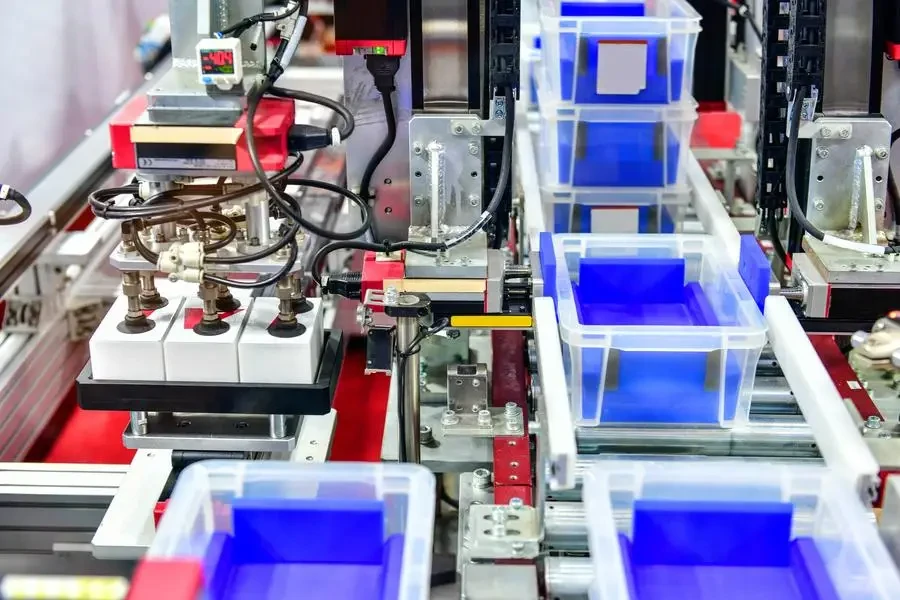
Performance and Efficiency
Performance and efficiency are critical when selecting a plastic injection molder. A high-performance machine can significantly impact production speed and product quality. Modern plastic injection molders often feature advanced computer controls, ensuring precise and consistent output. These controls manage injection pressure, temperature, and speed, leading to improved efficiency and reduced cycle times.
Energy consumption is a major consideration for efficiency. Older models might consume more power, increasing operational costs. Contemporary models are designed with energy-efficient components like variable frequency drives (VFDs) and servo motors, adapting the machine’s energy use to specific production demands, thereby reducing overall consumption and contributing to cost savings.
Predictive maintenance capabilities also enhance efficiency. Machines with sensors and IoT technology can predict potential failures and maintenance needs, minimizing downtime and prolonging equipment lifespan. This proactive maintenance approach ensures continuous production and avoids costly interruptions.
Technical Specifications
Technical specifications are paramount when evaluating plastic injection molders. Key specifications include clamping force, injection capacity, and mold size. The clamping force, measured in tons, determines the machine’s ability to keep the mold closed during the injection process. For instance, a 100-ton machine is suitable for small to medium-sized parts, while larger parts may require a machine with a clamping force of 500 tons or more.
Injection capacity, typically measured in cubic centimeters (cc), defines the maximum volume of plastic that can be injected into the mold. This specification must align with the part’s volume requirements to ensure quality. Additionally, mold size and platen dimensions must accommodate the specific mold used in production.
Other important technical factors include the machine’s screw diameter, affecting plasticizing capacity, and injection pressure, influencing material flow into the mold. Machines with adjustable screw diameters and high injection pressures offer greater flexibility and can handle a wider range of materials and part complexities.
Material Compatibility
Material compatibility is crucial when selecting a plastic injection molder. Different plastics have unique properties and processing requirements. Common materials include thermoplastics like polypropylene (PP), polyethylene (PE), and acrylonitrile butadiene styrene (ABS).
For instance, polypropylene requires precise temperature control due to its relatively low melting point, while ABS demands higher temperatures and pressures for optimal results. Machines with advanced temperature control systems and high-pressure capabilities are better suited for handling such diverse materials.
Some applications may involve composite materials or reinforced plastics, requiring specialized injection molders with enhanced wear resistance and corrosion protection. Machines with hardened steel components and corrosion-resistant coatings are ideal for these demanding applications, ensuring longevity and consistent performance.
Cost and Budget Considerations
The cost of a plastic injection molder is a significant factor for any business. Prices vary widely depending on the machine’s size, capabilities, and technological advancements. Entry-level machines may cost around $50,000, while advanced models with high clamping forces and sophisticated control systems can exceed $500,000.
However, the initial purchase price is not the only cost to consider. Operating costs, including energy consumption, maintenance, and labor, also impact the overall budget. Energy-efficient machines, though possibly more expensive upfront, can lead to substantial savings over time due to reduced power usage.
Businesses should also consider the potential for future upgrades. Machines offering modular components and software updates can extend the equipment’s lifespan and adapt to evolving production needs without requiring complete replacement. This flexibility can be a cost-effective solution for maintaining competitiveness.
Safety Standards and Certifications
Safety standards and certifications are non-negotiable when selecting a plastic injection molder. Compliance with international standards such as ISO 20430 ensures the equipment meets rigorous safety criteria. Machines adhering to these standards feature emergency stop buttons, safety guards, and interlock systems to protect operators from hazards.
Certifications from recognized bodies like CE (Conformité Européenne) and UL (Underwriters Laboratories) indicate that the machine has been tested and certified for safety and performance. These certifications provide assurance that the equipment is reliable and safe for use in various industrial settings.
Regular safety audits and maintenance checks are essential to ensure ongoing compliance with safety standards. Machines with safety monitoring systems can alert operators to potential issues, allowing for timely interventions and preventing accidents. Investing in equipment that prioritizes safety protects workers and minimizes the risk of costly downtime and legal liabilities.
Advanced Features in Modern Plastic Injection Molders
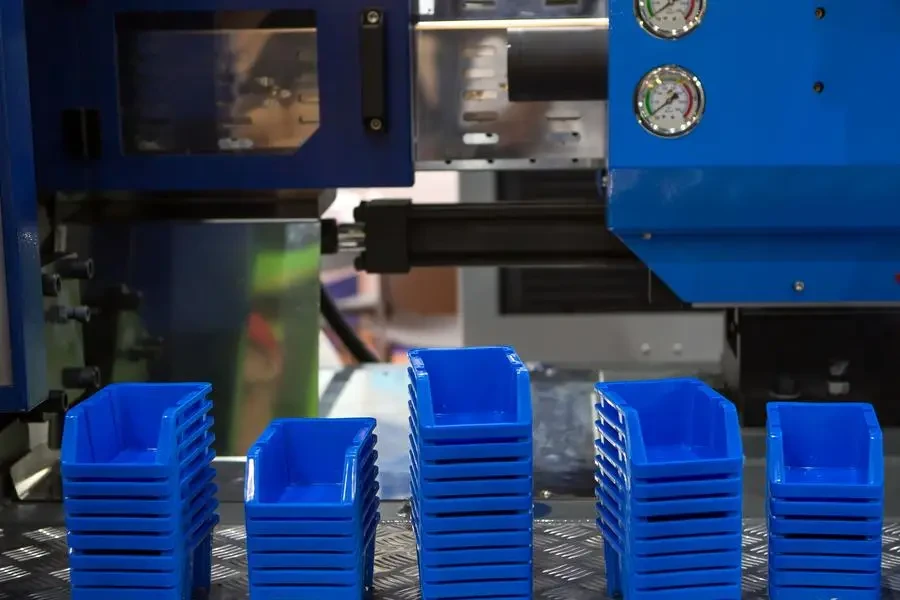
Modern plastic injection molders come with advanced features that enhance functionality, efficiency, and versatility, meeting the evolving demands of the manufacturing industry.
Computerized Control Systems
One significant advancement is the integration of computerized control systems. These systems enable precise control over the injection process, including temperature, pressure, and speed. By utilizing advanced algorithms and real-time data from sensors, computerized control systems ensure consistent product quality and reduce defects.
These systems offer user-friendly interfaces, allowing operators to monitor and adjust parameters easily. Features like programmable logic controllers (PLCs) and human-machine interfaces (HMIs) provide intuitive controls and detailed diagnostics, facilitating efficient operation and troubleshooting.
Multi-Material and Multi-Component Molding
Multi-material and multi-component molding capabilities are increasingly important in modern manufacturing. These features allow the production of complex parts with multiple materials or colors in a single molding cycle. Machines with multiple injection units and specialized molds can combine different materials, such as hard and soft plastics, creating parts with enhanced functionality and aesthetics.
For example, automotive components often require a combination of rigid and flexible materials for desired performance characteristics. Multi-material molding machines can produce these components efficiently, reducing assembly time and costs while ensuring high-quality results.
Integrated Quality Control Systems
Quality control is critical in the injection molding process, and modern machines are equipped with integrated quality control systems to ensure precision and consistency. These systems use sensors and cameras to monitor aspects of the molding process, such as temperature, pressure, and part dimensions. Any deviations from set parameters are detected in real-time, allowing for immediate corrective actions.
Some advanced machines feature automated inspection systems using machine vision technology to detect defects and measure critical dimensions. This integration minimizes the need for manual inspections and ensures only high-quality parts are produced.
Energy-Efficient Technologies
Energy efficiency is key in modern plastic injection molders, driven by the need to reduce operational costs and environmental impact. Many machines now incorporate energy-efficient technologies like servo motors, variable frequency drives, and advanced insulation materials. These technologies optimize energy consumption by adjusting power usage based on each molding cycle’s specific requirements.
For instance, servo motors provide precise control over machine movements, reducing energy wastage and improving overall efficiency. Variable frequency drives adjust motor speed to match the load, further reducing energy consumption. Advanced insulation materials help maintain consistent temperatures within the machine, minimizing heat loss and energy usage.
Predictive Maintenance and IoT Integration
Predictive maintenance and IoT integration are transforming the maintenance and operation of plastic injection molders. Machines with IoT sensors can collect and analyze data on various parameters, such as temperature, pressure, and vibration. This data predicts potential failures and maintenance needs, allowing for proactive interventions before issues escalate.
Predictive maintenance reduces downtime and extends equipment lifespan. By identifying and addressing issues early, businesses can avoid costly repairs and replacements, ensuring continuous production and optimal performance. IoT integration also enables remote monitoring and control, providing operators with real-time insights and the ability to manage machines from anywhere.
Future Trends in Plastic Injection Molding
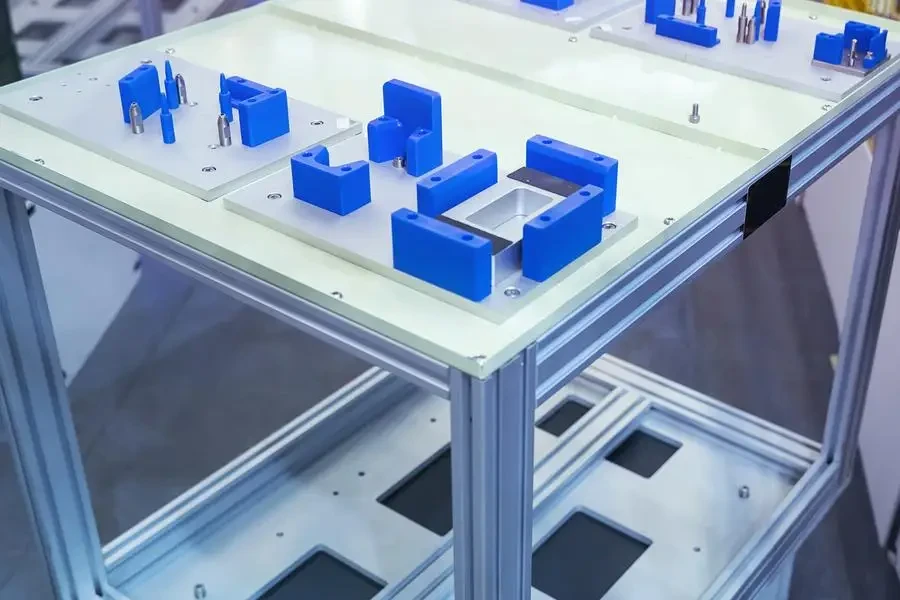
As technology evolves, the plastic injection molding industry is set to experience several exciting trends focusing on enhancing efficiency, sustainability, and precision in manufacturing.
Industry 4.0 and Smart Manufacturing
Industry 4.0 and smart manufacturing are revolutionizing the plastic injection molding industry. Integrating advanced technologies like artificial intelligence (AI), machine learning, and big data analytics enables manufacturers to optimize processes and improve productivity. Smart manufacturing systems analyze vast amounts of data in real-time, identifying patterns and making adjustments to enhance efficiency and product quality.
For example, AI algorithms can optimize injection parameters based on historical data, ensuring consistent output and reducing defects. Machine learning models can predict maintenance needs and identify potential issues before they impact production. These advancements lead to more agile and responsive manufacturing processes, allowing businesses to meet changing market demands effectively.
Sustainable and Eco-Friendly Materials
Sustainability is a growing concern in the manufacturing industry, and the plastic injection molding sector is no exception. There is an increasing focus on using sustainable and eco-friendly materials to reduce the environmental impact of plastic products. Biodegradable plastics, recycled materials, and bio-based polymers are gaining popularity as alternatives to traditional petroleum-based plastics.
Injection molding machines are being designed to handle these new materials effectively, ensuring they can be processed without compromising quality. Advancements in material science are leading to high-performance eco-friendly plastics that offer comparable properties to conventional materials, making them suitable for a wide range of applications.
Additive Manufacturing and Hybrid Processes
Additive manufacturing, also known as 3D printing, complements traditional injection molding processes, leading to hybrid manufacturing techniques. These hybrid processes combine the strengths of both technologies, enabling the production of complex and customized parts with high precision and efficiency.
For instance, additive manufacturing can create intricate mold inserts or prototypes, which are then used in the injection molding process to produce final parts. This approach allows for rapid prototyping and reduces the time and cost associated with mold fabrication. Hybrid manufacturing is particularly beneficial for low-volume production runs and highly customized products, providing manufacturers with greater flexibility and innovation opportunities.
Wrapping Up
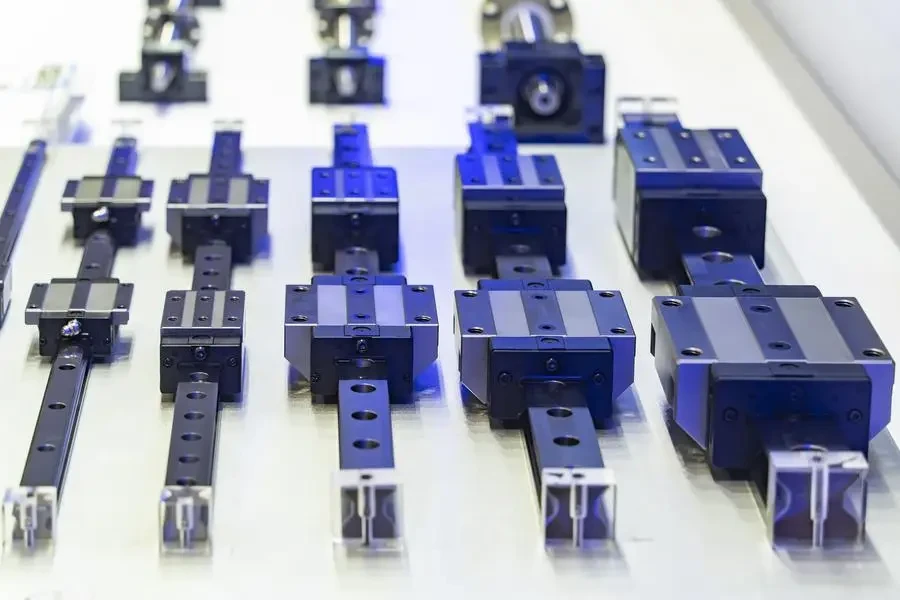
In summary, selecting the right plastic injection molder involves careful consideration of factors like performance, technical specifications, material compatibility, cost, and safety standards. Advanced features such as computerized control systems, multi-material molding, integrated quality control, energy-efficient technologies, and predictive maintenance are transforming the industry, enhancing efficiency, and ensuring high-quality production. As the industry moves towards smart manufacturing, sustainability, and hybrid processes, businesses must stay abreast of these trends to remain competitive and meet evolving market demands.