نگاهی به روندهای فعلی و مسائل زنجیره تامین برای بخش خودرو
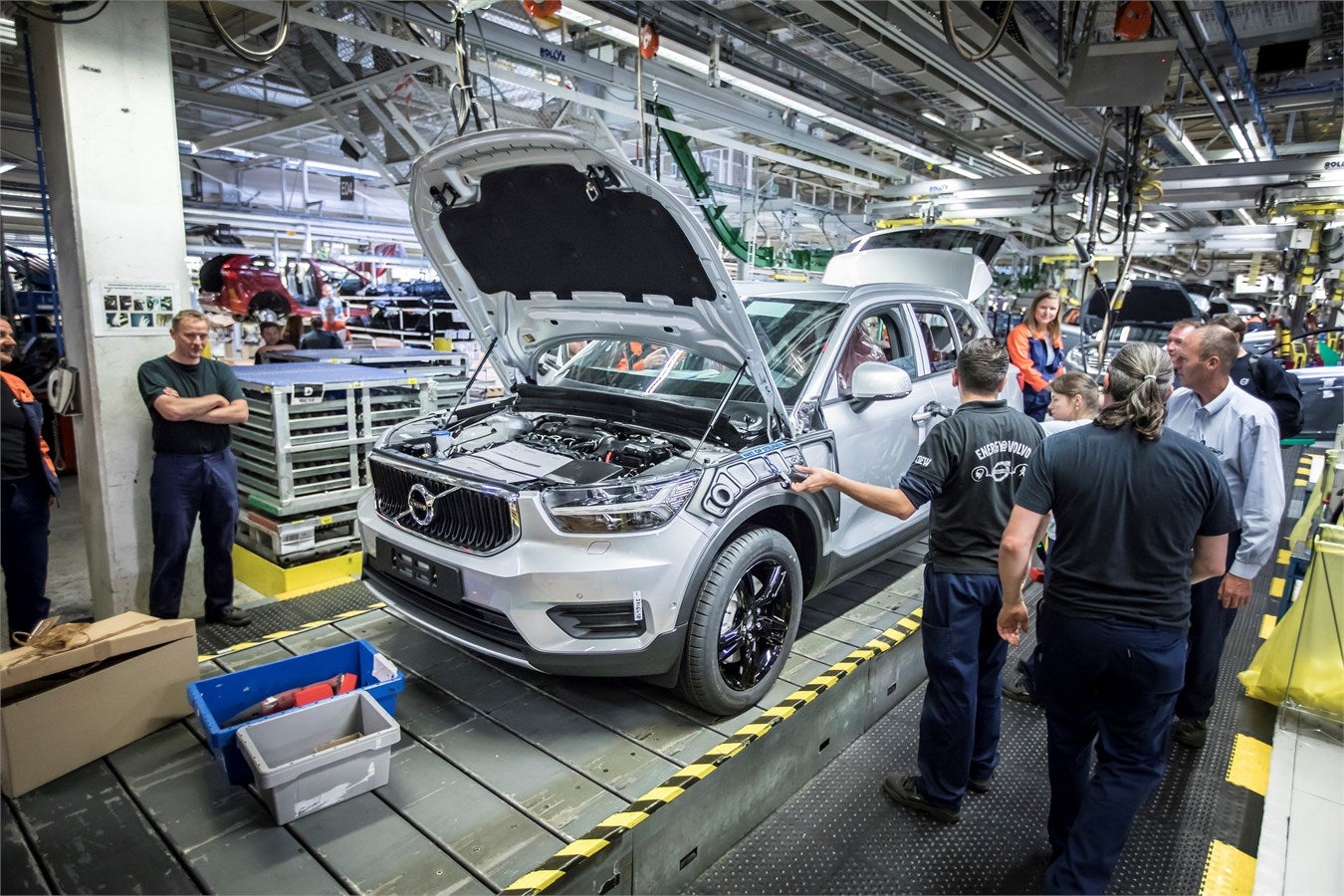
وسیله نقلیه موتوری غیر معمول می تواند حاوی چیزی بین 15,000 تا 25,000 قطعه باشد - بسته به نحوه اندازه گیری آنها و مهندسی طراحی سیستم های اصلی آن. این مواد بسیار زیادی برای گردآوری و ایجاد یکپارچگی برای محصول نهایی است. در واقع، قرار دادن همه آن قسمت ها در کنار هم به ترتیب درست، کار بدی نیست. هر خودرویی که وجود دارد ادای احترامی به برنامه ریزی فرآیند، سازماندهی، مهندسی تولید و لجستیک تولید است. روزی روزگاری، تولیدکنندگان خودرو بهطور عمودی یکپارچه بودند، اما این رویکرد جای خود را به واگذاریها داد (کسی به یاد میآورد که Visteon از کجا آمده و شبکه پیچیده شرکتهایی که گروه قطعات خودرو جنرال موتورز را تشکیل میدهند؟) و تامینکنندگان تخصصی قطعات که میتوانستند روی توسعه محصول تمرکز کنند و در مقیاس بالاتر به بیش از یک مشتری کار کنند.
یکپارچهکنندههای سیستمهای Tier 1 مستقیماً به سازندگان خودرو عرضه میکنند، اغلب از پارکهای تامینکننده که در نزدیکی تأسیسات مونتاژ و تولید خودرو قرار دارند، اما چندین لایه از تأمینکنندگان کوچکتر در زیر لایه بالایی وجود دارد - هر کدام نقشهای حیاتی را در مسیر طولانی از مواد خام تا محصول نهایی ایفا میکنند.
منابع بینالمللی قطعات جزء در طول چندین دهه به یک روش استاندارد صنعتی تبدیل شده است زیرا OEMها و تامینکنندگان بزرگتر به دنبال خرید قطعات و ورودیهای مواد در سراسر بازار جهانی بودهاند که آستانه کیفیت لازم را با کمترین هزینه برآورده میکنند. مسافتها (و هزینهها) برای حمل و نقل و ترتیبات انبارداری نیز بخشی از تصویر هستند، اما راندمان بالاتر و پیشرفتهای فناوری در حملونقل بینالمللی بار باعث رشد خارقالعاده در محمولههای بینالمللی قطعات شده است.
رشد صنعت خودروی چین در دو دهه گذشته نیز عامل بزرگی در تامین جهانی قطعات خودرو بوده است، به ویژه آنچه که ممکن است قطعات جهانی یا کالایی نامیده شود که عمدتاً بر اساس قیمت تمام شده به فروش می رسند. تامین کنندگان چینی از قراردادهای بزرگ محلی که اقتصاد مقیاس را تقویت می کند و همچنین یارانه های پنهانی که از ساختارهای مالکیت پیچیده شامل والدین OEM، شرکت های دولتی و سهام های متنوع سرچشمه می گیرد، سود برده اند. در اوایل دهه 2000، سازندگان خودروهای آمریکایی، بهویژه، به سمت تامین قطعات ارزانتر از آسیا روی آوردند و در این فرآیند برخی از شرکتهای قدیمی در پایگاه تامینکنندگان ایالات متحده را تضعیف کردند.
در سرتاسر جهان، جریان تجارت بینالمللی در محصولات خودرو - اعم از وسایل نقلیه نهایی و قطعات سازنده - اکنون بسیار زیاد است. برآوردهای گردآوری شده توسط GlobalData آلمان را از نظر محموله های خروجی محصولات صنعت خودرو به عنوان رهبر بین المللی جهان نشان می دهد. این صادرات با واردات و شبکه درهم تنیده کالاهای واسطه ای منعکس می شود که به عنوان ورودی سیستم های اجزایی که در مراحل مختلف فرآیند تولید پالایش و مهندسی شده اند استفاده می شوند و می توانند چندین بار از مرزهای بین المللی حمل شوند.
یکی دیگر از ویژگیهای ساختاری مهم زنجیرههای تامین در صنعت خودرو، اهمیت فلسفه مدیریت زنجیره تامین است که هزینههای موجودی را به حداقل میرساند و کارایی فرآیند و حلقههای ارتباطی بازخورد را برای ارتقای استانداردهای کیفیت افزایش میدهد. که به عنوان «تولید ناب» شناخته می شود، با تویوتا آغاز شد و ماهیت آن با عبارت «در زمان مناسب» برای توصیف روش ها و اصول عرضه ناب گنجانده شده است. ظهور فناوریهای دیجیتال و متصل که تمام بخشهای فرآیند تولید و خردهفروشی را گرد هم میآورد، در دهه گذشته یا بیشتر این روشهای کار را تقویت کرده است.
در گذشته، بلایای طبیعی و تأثیرات متمرکز آنها بر مکانها، شرکتهای خودروسازی را تحت تأثیر قرار داده و شکنندگی زنجیرههای تأمین خودرو را به تصویر کشیده است. پس از زلزله و سونامی سال 2011 در ژاپن، چندین نمونه قابل توجه از اختلال وجود داشت. یک تولیدکننده خودروی درجه یک جهانی از نظر عرضه یا یک رنگدانه رنگ قرمز تکی که در ژاپن تهیه میشود، مشکل داشت. سیل در تایلند در اواخر همان سال باعث کمبود عرضه صفحه نمایش LCD برای نمایش اطلاعات خودرو شد. OEM ها و فروشندگان مجبور بودند بر این اساس خود را با کمبودها وفق دهند. جنگ در اوکراین نشان میدهد که چگونه رویدادهای ژئوپلیتیک غیرمنتظره میتوانند زنجیره تامین را نیز مختل کنند.
چالش نیمه هادی ها
همه شرکت ها به طور مستقیم تحت تأثیر بحران بهداشت عمومی سال 2020 و به طور غیرمستقیم از تأثیرات بیشتر بر زنجیره های تأمین جهانی قرار گرفتند. علاوه بر این، بهبود فروش جهانی در سال 2021 به دلیل پیامدهای پیش بینی نشده بحران کووید یک سال قبل به شدت آسیب دید. از آنجایی که خودروسازان کارخانه ها را تحت دستورات دولتی تعطیل کردند و سفارشات قطعات را در سال 2020 به شدت کاهش دادند، تولیدکنندگان نیمه هادی ها تجارت جایگزینی را در زمینه هایی مانند لوازم الکترونیکی مصرفی یافتند.
هنگامی که کارخانههای خودروسازی در حال بهبود سفارشات تراشههای خود را در سه ماهه اول سال 2021 افزایش دادند، مشکل کمبود عرضه به سرعت آشکار شد.
کمبودهای نیمه هادی نیز به دلیل زمان طولانی در افزایش ظرفیت ریخته گری تراشه در بالادست، به راحتی قابل رفع نبود. یک قطعه غایب که ایمنی حیاتی است یا به روش دیگری برای محصول نهایی ضروری تلقی می شود به این معنی است که برخی از خطوط مدل شدیدتر از سایرین تحت تأثیر قرار می گیرند. سازندگان خودرو در برخی موارد میتوانستند ترکیب بازار را تغییر دهند، اما یک ضربالمثل قدیمی دوباره در حال تحقق بود: زنجیرههای تامین به اندازه ضعیفترین نقطه خود خوب/محکم هستند.
در سرتاسر صنعت، روشها و فرآیندهای تدارکات بدون هیچوقت مورد بررسی قرار میگیرند.
همچنین شایان ذکر است که یک عنصر ساختاری در کار است که به این معنی است که برخی از فشارهای تامین نیمهرسانا احتمالاً در آینده به عنوان یک خطر باقی میمانند: محتوای الکترونیکی پیشرفته خودروها به دلیل تطبیق روزافزون ویژگیهای فنآوری پیچیدهتر در حال افزایش است. این امر باعث می شود برخی از شرکت ها به سمت اتحاد استراتژیک با سازندگان تراشه حرکت کنند. این نه تنها میتواند به تامین امنیت آتی ریزپردازندههای حیاتی کمک کند، بلکه میتواند روابط سودمند توسعه محصول آینده مشترک را در آنچه که آشکار میشود، یک بخش با ارزش استراتژیک است، تسهیل کند.
فشارهای دیگر بر زنجیرههای تامین از منابع دیگری مانند کمبود نیروی کار پیشبینینشده و قیمتهای بسیار بالاتر حملونقل کانتینری بینالمللی به دلیل افزایش قیمت انرژی ناشی شده است.
بحث دو منبعی در مقابل چند منبعی
شکنندگی در زنجیرههای تامین خودرو با رواج چندین لایه، جریانهای منابع بینالمللی و تمایل به منبعیابی واحد برای به حداکثر رساندن صرفهجویی در مقیاس در برنامههای جهانی خودرو همراه است. در بسیاری از موارد، این ساختار سنتی نیز در فرهنگ شرکای ترجیحی در سراسر سطوح عرضه تعبیه شده و ریشهدار است. مزایا همچنین میتواند شامل سیستمهای مشترک و هزینههای لجستیکی باشد و هزینهها در مدلها و سیستمهای دیگر نیز توزیع شود.
فناوری همچنین نقشی در تشویق منبع یابی واحد ایفا کرده است، زیرا شرکت ها - از جمله آنهایی که در سطوح 3 و 4 هستند - معمولاً می توانند تخصص و سرمایه گذاری را در یک مرکز اختصاص داده شده به تولید با حجم بالا متمرکز کنند. مشکلات زمانی به وجود می آیند که مشکلی پیش می آید که scuppers برنامه ریزی می کند (مثلاً آتش سوزی در یک کارخانه ریزپردازنده Renesas در سال گذشته).
قطعات الکترونیکی و حسگرها نمونههایی از اجزای حیاتی برای مجموعههای فرعی هستند که در صورت بروز هرگونه اختلال در بالادست، میتوانند پیامدهای بزرگی در تولید خودرو داشته باشند. یافتن تامین کنندگان جایگزین با ظرفیت اضافی در مدت زمان کوتاه یک چالش بزرگ است.
نگهداری برخی از ذخایر قطعات در انبارها هزینه دارد و برخلاف اصول راهنمای تولید ناب است. البته میتوان تصمیم گرفت که هر گونه هزینههای نابسامان را بهموقع و زمانی که رخ میدهد جذب یا حذف کند - این در نهایت به کمیت ارزیابی ریسک بستگی دارد.
تجربه سالهای اخیر حداقل به شرکتها اشاره میکند که به طور فزایندهای این سوال را مطرح میکنند که آیا منبع یابی به اندازه گذشته مطلوب است یا خیر. دنیایی که با خطرات و عدم قطعیت های بالاتر احاطه شده است، شاید نیاز به تغییر رویکرد داشته باشد. تکرار در زنجیره تامین، حتی اگر به معنای نزدیک شدن به اشتراک گذاری با یک رقیب باشد، ممکن است راه حل بهتری - حداقل برای برخی از اجزا - نسبت به منبع یابی واحد ارائه دهد. امنیت بیشتر محصول مزیت منبع یابی دوگانه خواهد بود. مثل همیشه، بحث هزینه کلی است.
برق رسانی و الگوهای جدید زنجیره تامین
برقیسازی چالشهای جدیدی را برای زنجیرههای تامین آینده در خودرو به ارمغان میآورد. OEM ها با ابهامات قابل توجهی در مورد تامین قطعات جدید و کلیدی - به ویژه باتری های پیشرانه - مواجه شده اند که سعی در حل آن دارند. همچنین سوالات استراتژیک در مورد درجه یکپارچگی عمودی وجود دارد که برای کاهش خطرات آینده و اعمال کنترل بر جنبه های تجاری ترتیبات عرضه مطلوب است. سرمایه گذاری های مشترک با متخصصان باتری راه اندازی شده است. سایر اجزای کلیدی وسایل نقلیه الکتریکی - مانند موتورها، قطعات سیستم محرکه، اینورترهای ولتاژ بالا - نیز در کنار ملاحظات زنجیره تامین مشمول افزایش سرمایه گذاری خواهند بود.
استراتژیهای بلندپروازانه برقسازی، تقاضا برای سلولهای باتری لیتیوم یونی را افزایش میدهد. تولیدکنندگان باتری در سرتاسر جهان متعهد به استراتژیهای توسعه چند میلیارد دلاری هستند و «گیگاکارخانههای» جدیدی را برای عرضه سلولها به خودروسازان باز میکنند.
یک نمونه قابل توجه از همکاری عمیق OEM-Tier 1 در این زمینه با امضای تفاهم نامه بین فولکس واگن و بوش ارائه شده است. این دو شرکت قصد دارند سیستمهای تولید باتری یکپارچه، افزایش در محل، و پشتیبانی تعمیر و نگهداری را برای تولیدکنندگان باتری و سیستمهای باتری عرضه کنند. آنها می گویند که هدف آنها رهبری هزینه و فناوری در فناوری باتری در مقیاس صنعتی و تولید حجمی "باتری های پیشرفته و پایدار" است.
تنها در اروپا، گروه فولکس واگن قصد دارد تا سال 2030 شش کارخانه تولید سلول سلولی بسازد و سایر سازندگان نیز اقدامات مشابهی را برای تضمین منابع آینده سلول ها و بسته های باتری انجام می دهند. این منطقه باید تا سال 700 شاهد ظرفیت کل بسته باتری سالانه حدود 2030 گیگاوات ساعت باشد.
با نگاهی به بالادست، تویوتا با پاناسونیک (Prime Planet Energy & Solutions - PPES) یک شرکت مشترک با غول معدنی BHP برای تامین آتی سولفات نیکل امضا کرده است، که مبنایی برای نیکل موجود در کاتد اکثر سلولهای باتری لیتیوم یون است. تسلا همچنین قراردادی مشابه با BHP امضا کرده است که نشان میدهد مواد خام نیز برای امنیت عرضه در آینده بسیار در ترکیب هستند.
این قراردادها نیاز بازیگران خودرو را برای بررسی بیشتر زنجیره تامین باتری، برای اطمینان از دسترسی به مواد خام کافی برای تامین رشد ظرفیت عظیم مورد نیاز در بخش باتریهای لیتیوم یونی برای موج جدید خودروهای برقی باتری که در سالهای آینده عرضه میشوند، برجسته میکند. بازیافت نیز در بسیاری از معاملاتی که انجام شده است، یک نکته کلیدی است.
بلاک چین برای دیده شدن زنجیره تامین
شرکت های خودروسازی به طور فزاینده ای از فناوری بلاک چین برای به دست آوردن شفافیت در مورد مسائل زنجیره تامین مانند انتشار CO2 و منبع کبالت برای باتری ها (که می تواند با سوالات اخلاقی پیرامون استخراج مواد معدنی گرانبها همراه باشد) استفاده می کنند.
مفهوم اصلی بلاک چین، همانطور که از نام آن پیداست، زنجیره ای از بلوک ها یا سوابق دارای مهر زمانی است (بلوک = اطلاعات دیجیتال؛ زنجیره = پایگاه داده عمومی/جامعه). بلوک ها اطلاعات مربوط به تراکنش ها را ذخیره می کنند. هنگامی که یک بلوک داده های جدیدی را ذخیره می کند - یک تراکنش - به زنجیره بلوکی اضافه می شود و پس از تأیید توسط یک شبکه همتا به همتا از رایانه ها، همه می توانند آن را ببینند (یا ممکن است مشروط به مجوز یک شبکه خصوصی مانند زنجیره تأمین OEM - «دفتر کل توزیع شده» باشد).
با این حال، همه طرفین فقط به اطلاعاتی دسترسی دارند که اجازه دیدن آنها را دارند. هر کامپیوتر در شبکه بلاک چین کپی مخصوص به خود را از بلاک چین دارد. اگرچه در اصل، ایده ایجاد یک سیستم بسیار شفاف با هزینه های مبادله صفر بین دو طرف است که یک بلوک ایجاد می کند.
ما میتوانیم انتظار داشته باشیم که شرکتهای خودروسازی بیشتری فرآیندهای بلاک چین را – به ویژه از نوع دفتر کل توزیع شده (یعنی شبکه خصوصی) – به عنوان وسیلهای برای کاهش خطر شکستهای زنجیره تامین و درک نقاط قوت و ضعف در طول زنجیره، و همچنین به عنوان راهی برای نشان دادن افزایش تقاضا برای انطباق در حوزههای نظارتی مانند پایداری، اتخاذ کنند.
درس هایی از تویوتا
تویوتا به طور کلی به عنوان یکی از عملکردهای بهتر در صنعت خودرو در مورد مدیریت زنجیره تامین در نظر گرفته می شود. علاوه بر این که مبتکر روشهای تولید ناب بود که بعداً به بهترین روش مورد استفاده اکثر OEMها و تامینکنندگان اصلی تبدیل شد، همچنین سیستمها و فرآیندهای خود را با توجه به شرایط متغیر در مورد اقدامات کاهش خطر اصلاح کرده است. علاوه بر این، در مواقعی و به نفع اهداف بخش گسترده تر در مواجهه با شرایط اضطراری، با تامین کنندگان خود بسیار نزدیک کار کرده است.
پس از زلزله و سونامی کیوتو در سال 2011، تویوتا در کنار تامین کنندگان در ژاپن برای تولید یک پایگاه داده جامع از اطلاعات زنجیره تامین برای حمایت از بخش تولید ژاپن کار کرد. تویوتا همچنین یک استراتژی برای تامین چندگانه قطعات کلیدی ارائه کرد که به معنای سازماندهی تامین از سه منبع مختلف است – اما با تامینکننده اصلی تقریباً دو سوم سفارش را برای اطمینان از صرفهجویی در مقیاس تولید میکند. چندین تامین کننده صرفه جویی در مقیاس را به خطر می اندازند، اما این بدان معناست که در صورت لزوم، جایگزین هایی نیز وجود دارد.
تویوتا همچنین دارای یک سیستم به خوبی توسعه یافته برای نظارت بر شبکه گسترده تامین کنندگان خود و یک سیستم هشدار اولیه برای کمبود است. در واقع، برخی از شرکتها برای ارزیابی پیشرفتها در زنجیرههای تامین خود به هوش مصنوعی روی میآورند – اگرچه این امر در وهله اول مبتنی بر داشتن یک پایگاه داده قابل اعتماد، گسترده و دقیق است.
یکی دیگر از گزینههای شرکتها، حفظ ذخایر اضطراری یا بافر قطعات کلیدی است – بهویژه آنهایی که میتوانند باعث توقف خط تولید شوند. باز هم، شامل هزینه اضافی در ذخیره سازی یا انبارداری می شود، اما این مسئله این است که چه سطحی از هزینه یا «حق بیمه» ارزش پرداخت را دارد. همچنین، این یک راه حل دائمی نخواهد بود. تویوتا ممکن است برخی از نیمه هادی ها را ذخیره کرده باشد، اما شدت کمبود جهانی تراشه باعث شد که در نهایت این شرکت نیز مجبور به کاهش تولید شود. شاید مهم ترین آموخته از تویوتا نیاز به بازبینی مداوم و سازگاری با شرایط متغیر و عدم قطعیت باشد.
منبع از فقط خودکار
سلب مسئولیت: اطلاعات ذکر شده در بالا توسط just-auto.com مستقل از Chovm.com ارائه شده است. Chovm.com هیچ گونه نمایندگی و ضمانتی در مورد کیفیت و قابلیت اطمینان فروشنده و محصولات نمی دهد.