Recent advancements in foam machinery technology have revolutionized production efficiency and product quality in 2025. This article provides an in-depth analysis of the latest market trends, key factors to consider, and the latest technology features. Professional buyers will find valuable guidance to make informed decisions, ensuring their investments yield maximum returns.
Table of Contents:
– Comprehensive Market Overview of Foam Machinery
– In-Depth Analysis of the Foam Machinery Market
– Key Factors When Selecting Foam Machinery
– Latest Technology Features in Foam Machinery
– Regulatory Compliance and Safety Standards
– Cost and Budget Considerations
– Selecting the Best Foam Machinery for Your Needs
– Final Thoughts
Comprehensive Market Overview of Foam Machinery
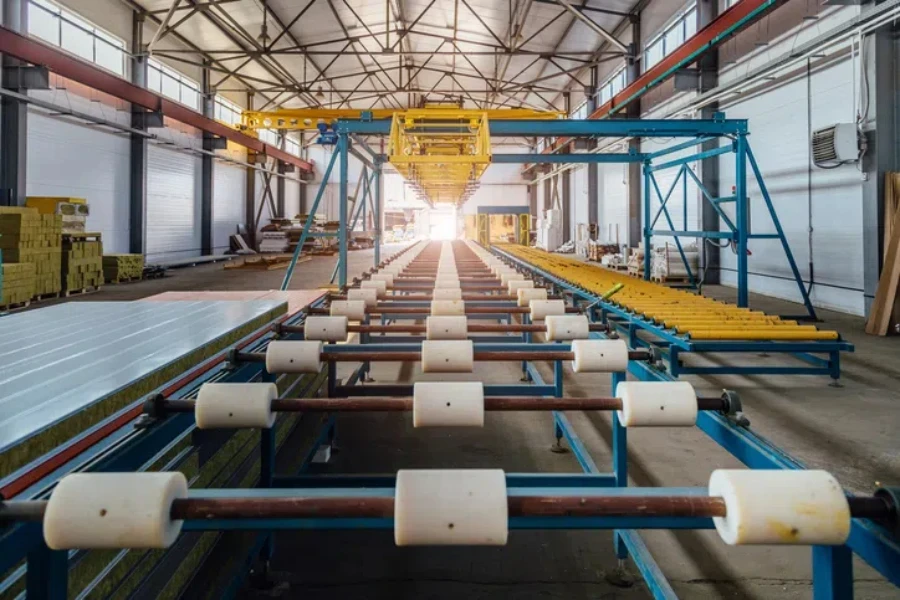
The foam machinery market has shown robust growth, driven by the rising demand for lightweight and high-performance materials in various industries. In 2024, the global market value for automotive foam reached USD 50.5 billion, with a projected value of USD 71.1 billion by 2030, growing at a CAGR of 5.8%. Similarly, the aerospace foam market was valued at USD 8.41 billion in 2024 and is expected to reach USD 15.57 billion by 2030, with a CAGR of 10.6%. These figures indicate a significant demand for foam machinery, essential for producing various types of foam materials used in automotive, aerospace, and other industrial applications.
The foam machinery market’s expansion is closely tied to the growth of the automotive and aerospace industries and the increasing adoption of foam materials in construction, packaging, and consumer goods. Market dynamics are influenced by technological advancements, the need for energy-efficient materials, and stringent environmental regulations. Additionally, the development of sustainable and biodegradable foam materials is expected to create new growth opportunities.
Key players in the foam machinery market include BASF SE, The Dow Chemical Company, Huntsman Corporation, and Recticel NV. These companies invest heavily in research and development to innovate and improve the performance of foam materials, catering to the evolving needs of end-user industries. The competitive landscape is characterized by strategic partnerships, mergers and acquisitions, and the introduction of advanced foam machinery technologies.
In-Depth Analysis of the Foam Machinery Market
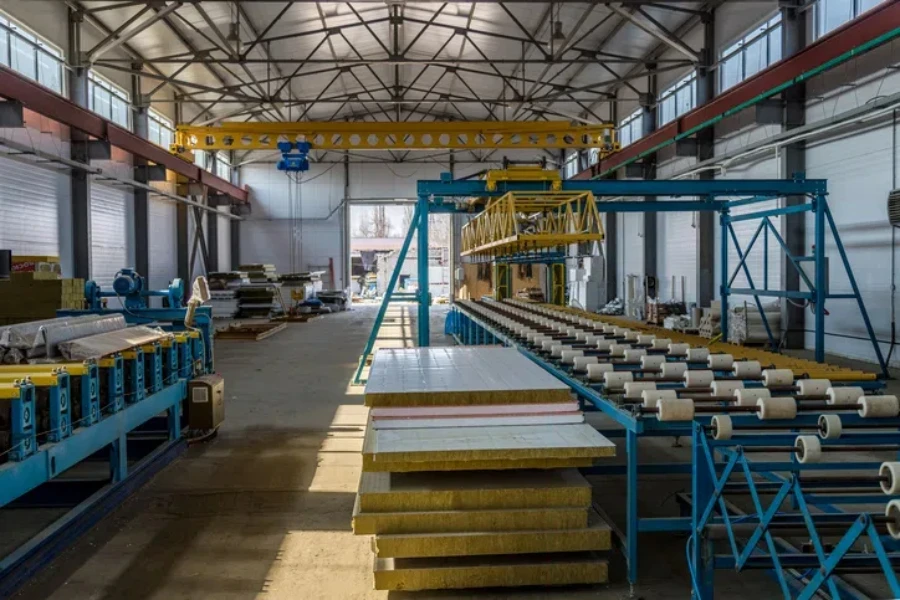
The foam machinery market is witnessing significant advancements in technology and production processes, aimed at enhancing the efficiency and performance of foam materials. Key performance benchmarks for foam machinery include high precision, energy efficiency, and the ability to handle various foam types such as polyurethane, polyolefin, and metal foams. These materials are crucial for applications in automotive seating, insulation, soundproofing, and aerospace components.
Market share dynamics reveal a competitive environment where leading companies focus on expanding their product portfolios and geographical presence. Economic influences, such as fluctuations in raw material prices and geopolitical tensions, play a critical role in shaping market trends. Consumer behavior is shifting towards eco-friendly and sustainable products, driving the demand for bio-based and recyclable foam materials.
Distribution channels are evolving, with an increasing emphasis on direct sales and online platforms to reach a broader customer base. Recent innovations in foam machinery include advanced extrusion and molding technologies, enabling the production of high-quality foams with improved structural integrity and performance. The digitalization of manufacturing processes, including the integration of IoT and AI technologies, is further enhancing the efficiency and precision of foam machinery.
Customer pain points often revolve around the high cost of advanced equipment and the technical challenges of handling different foam materials. To address these issues, companies are focusing on providing comprehensive after-sales support, training, and maintenance services. Brand positioning strategies emphasize innovation, sustainability, and cost-effectiveness, with differentiation strategies aimed at offering customized solutions to meet specific industry requirements.
Niche markets within the foam machinery industry include specialized applications such as medical foams, high-performance insulation materials, and lightweight structural components for electric vehicles and aerospace. These segments offer lucrative opportunities for companies that can develop tailored solutions to meet the stringent performance and regulatory standards of these industries.
Key Factors When Selecting Foam Machinery
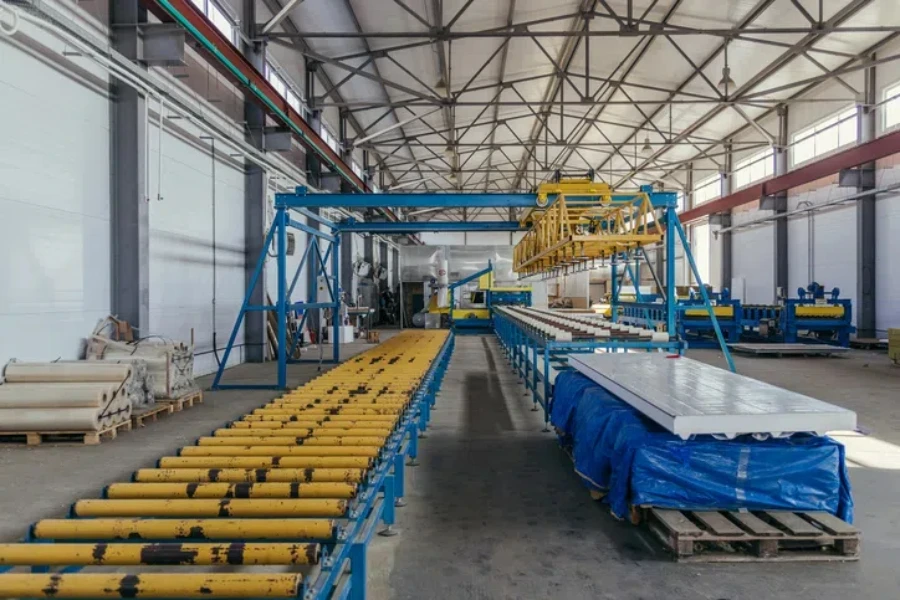
Choosing the right foam machinery is crucial for ensuring optimal production, efficiency, and quality in various applications. Several key factors must be considered to make an informed decision.
Types of Foam Machinery
Foam machinery comes in several types, each designed for specific applications and materials. Understanding the different types can help in selecting the most suitable equipment for your needs.
Open Cellular Foam Machinery: These machines produce foam with interconnected pores, ideal for filtration applications. They are typically used in industries where air or liquid filtration is required, such as HVAC systems and water treatment plants. The performance of open cellular foam machinery depends on the size and uniformity of the pores, which can significantly impact filtration efficiency.
Closed Cellular Foam Machinery: These machines manufacture foam with sealed pores, making them suitable for buoyancy and flotation applications. Closed cellular foam is commonly used in marine and automotive industries due to its excellent resistance to water absorption. The machinery must ensure consistent cell structure to maintain the foam’s buoyant properties.
Flexible Foam Machinery: Flexible foam machinery produces foam that can bend and absorb impacts without cracking. This type of foam is widely used in cushioning applications, such as furniture, automotive seating, and packaging. The machinery should provide precise control over the foam’s density and flexibility to meet specific application requirements.
Rigid Foam Machinery: Rigid foam machinery creates foam with a solid matrix and little to no flexibility. This type of foam is used in construction for insulation panels and structural components. The machinery must ensure high compressive strength and dimensional stability to meet building standards.
Reticular Foam Machinery: Reticular foam machinery produces foam with an open structure and a network of thin material strands. This foam is used in applications requiring high surface area, such as filters and sound absorbers. The machinery should offer precise control over the reticulation process to achieve the desired pore structure.
Performance and Functionality
The performance and functionality of foam machinery are critical factors that determine the efficiency and quality of the foam produced. Key performance indicators include production speed, foam density, and cell structure uniformity.
Production Speed: High-speed foam machinery can significantly increase production efficiency, reducing lead times and operational costs. However, it is essential to ensure that increased speed does not compromise foam quality. Advanced control systems and automation can help maintain consistency at higher production rates.
Foam Density: The density of the foam affects its mechanical properties, such as strength, flexibility, and insulation capabilities. Foam machinery should offer precise control over density to produce foam that meets specific application requirements. This can be achieved through adjustable mixing ratios and controlled expansion processes.
Cell Structure Uniformity: Uniform cell structure is crucial for ensuring consistent foam properties. Machinery with advanced mixing and molding technologies can produce foam with uniform cell size and distribution. This is particularly important in applications where foam performance is critical, such as medical devices and high-performance insulation.
Technical Specifications
Technical specifications of foam machinery provide insights into its capabilities and compatibility with different materials and applications. Key specifications to consider include power requirements, mixing capacity, and control systems.
Power Requirements: Foam machinery can have varying power requirements depending on its size and production capacity. It is essential to ensure that the available power supply can support the machinery’s operation. Additionally, energy-efficient machines can reduce operational costs and minimize environmental impact.
Mixing Capacity: The mixing capacity of foam machinery determines the volume of foam that can be produced in a single cycle. For large-scale production, machines with high mixing capacities are preferred to increase throughput. However, for specialized applications, smaller machines with precise mixing capabilities may be more suitable.
Control Systems: Advanced control systems in foam machinery enable precise monitoring and adjustment of production parameters. Computerized control systems with real-time feedback can ensure consistent foam quality and reduce the risk of defects. Integration with production management systems can also enhance overall efficiency and traceability.
Materials and Build Quality
The materials used in the construction of foam machinery and its build quality directly impact its durability, maintenance requirements, and overall performance.
Construction Materials: High-quality materials such as stainless steel and corrosion-resistant alloys are commonly used in foam machinery to ensure durability and longevity. These materials can withstand the harsh conditions of foam production, including exposure to chemicals and high temperatures.
Build Quality: The build quality of foam machinery affects its reliability and maintenance needs. Machines with robust construction and precision-engineered components are less prone to breakdowns and require less frequent maintenance. This can reduce downtime and increase overall productivity.
Safety Standards and Certifications: Compliance with safety standards and certifications is essential for ensuring safe operation and meeting regulatory requirements. Foam machinery should adhere to industry standards such as CE, UL, and ISO certifications. These certifications indicate that the machinery has been tested for safety and performance, providing assurance to operators and stakeholders.
Latest Technology Features in Foam Machinery
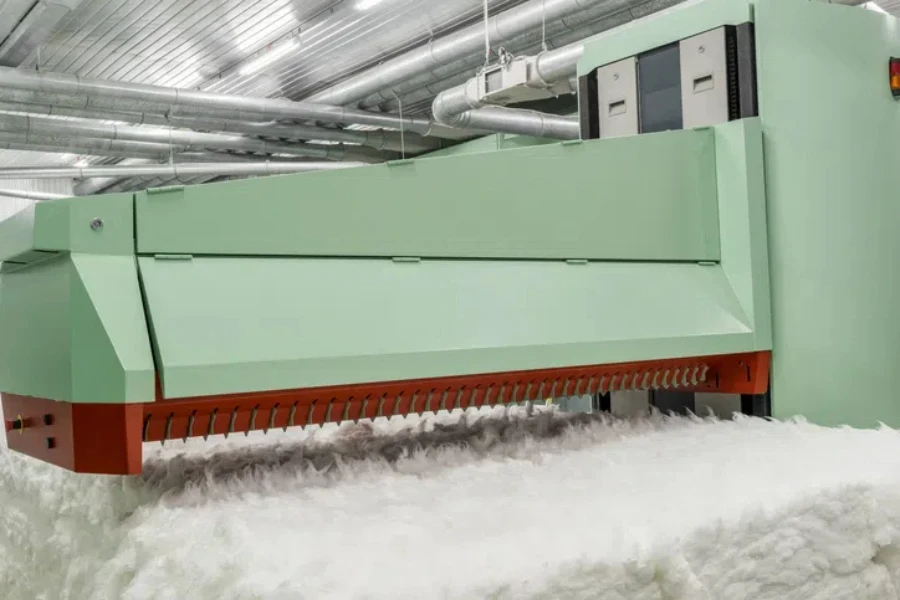
The foam machinery industry is continuously evolving with advancements in technology. Incorporating the latest features can enhance production efficiency, improve foam quality, and reduce operational costs.
Automation and Control
Automation and advanced control systems are revolutionizing foam machinery, enabling higher precision and efficiency. Automated machines can perform complex tasks with minimal human intervention, reducing the risk of errors and increasing production speed.
Robotic Integration: Integrating robotics with foam machinery can enhance automation and precision. Robots can handle material loading, mixing, and molding processes, ensuring consistent quality and reducing labor costs. Robotic systems can also perform repetitive tasks with high accuracy, improving overall efficiency.
Real-Time Monitoring: Advanced control systems with real-time monitoring capabilities allow operators to track production parameters and make adjustments as needed. Sensors and data analytics can provide insights into machine performance, enabling predictive maintenance and reducing downtime.
Energy Efficiency
Energy-efficient foam machinery can significantly reduce operational costs and environmental impact. Modern machines are designed to optimize energy usage without compromising performance.
Variable Frequency Drives (VFDs): VFDs in foam machinery can adjust motor speed based on production requirements, reducing energy consumption. VFDs also provide smoother operation and reduce wear on mechanical components, extending the machine’s lifespan.
Heat Recovery Systems: Heat recovery systems can capture and reuse heat generated during the foam production process. This can reduce the need for external heating sources, lowering energy costs and minimizing environmental impact.
Advanced Materials and Additives
The use of advanced materials and additives in foam production can enhance the properties of the final product. Foam machinery equipped to handle these materials can offer greater versatility and improved performance.
Nanocomposites: Incorporating nanocomposites into foam production can enhance mechanical properties such as strength, flexibility, and thermal insulation. Foam machinery must be capable of precise mixing and dispersion of nanocomposites to achieve uniform properties.
Eco-Friendly Additives: The demand for sustainable and eco-friendly foam products is increasing. Foam machinery that can process bio-based and recyclable materials can meet this demand while reducing environmental impact. These machines should offer precise control over the production process to ensure consistent quality.
Regulatory Compliance and Safety Standards
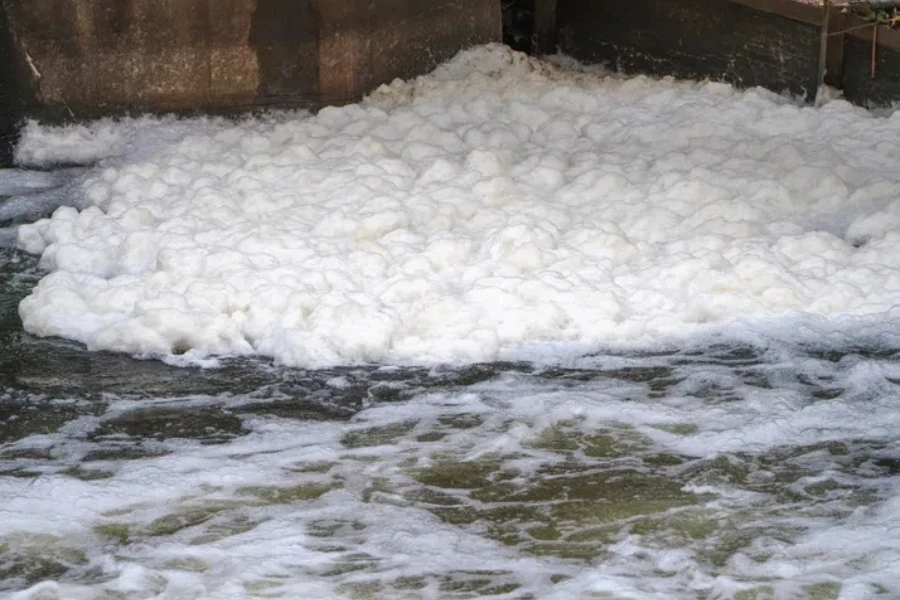
Regulatory compliance and adherence to safety standards are critical considerations when selecting foam machinery. Ensuring that the machinery meets industry regulations can prevent legal issues and ensure safe operation.
Industry Standards
Foam machinery must comply with industry standards to ensure safety, quality, and performance. Key standards to consider include CE, UL, and ISO certifications.
CE Certification: CE certification indicates that the machinery meets European safety, health, and environmental protection standards. This certification is essential for exporting foam machinery to European markets.
UL Certification: UL certification ensures that the machinery meets safety standards set by Underwriters Laboratories. This certification is widely recognized in North America and is essential for ensuring safe operation.
ISO Certification: ISO certification indicates that the machinery meets international standards for quality management and production processes. ISO-certified machinery is recognized globally for its reliability and performance.
Safety Features
Safety features in foam machinery are essential for protecting operators and preventing accidents. Modern machines are equipped with various safety mechanisms to ensure safe operation.
Emergency Stop Systems: Emergency stop systems allow operators to quickly halt the machine in case of an emergency. These systems are crucial for preventing accidents and minimizing damage to the machinery.
Safety Guards and Enclosures: Safety guards and enclosures protect operators from moving parts and hazardous materials. These features are essential for preventing injuries and ensuring safe operation.
Interlock Systems: Interlock systems prevent the machine from operating if safety guards are not in place. This ensures that operators cannot bypass safety mechanisms, reducing the risk of accidents.
Cost and Budget Considerations
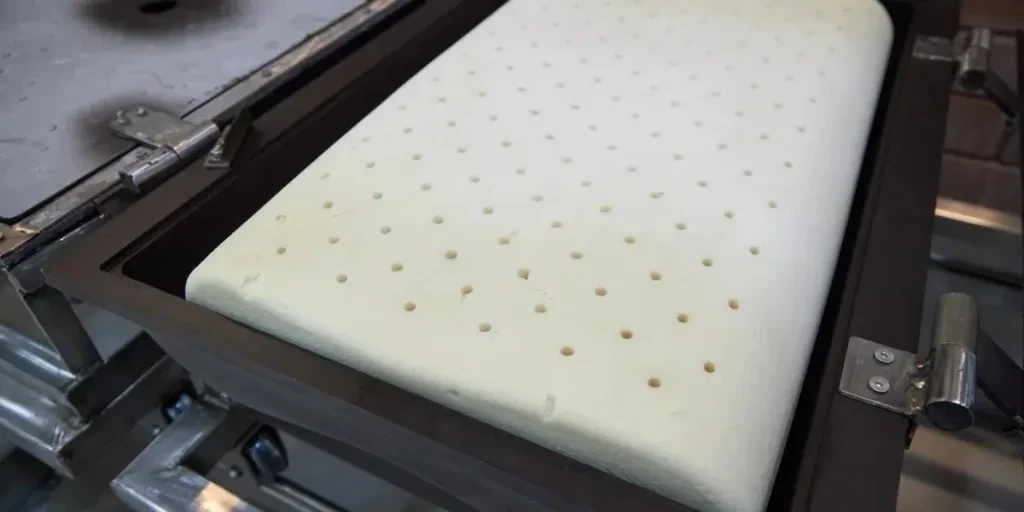
The cost of foam machinery is a significant factor in the decision-making process. It is essential to balance the initial investment with long-term operational costs and potential return on investment (ROI).
Initial Investment
The initial investment in foam machinery includes the purchase price, installation costs, and any additional equipment required. It is essential to consider the machinery’s capabilities and features to ensure it meets production requirements.
Purchase Price: The purchase price of foam machinery varies depending on its type, capacity, and features. High-end machines with advanced features may have a higher upfront cost but can offer greater efficiency and quality.
Installation Costs: Installation costs include expenses for setting up the machinery, connecting utilities, and calibrating the equipment. Professional installation ensures that the machinery operates correctly and safely.
Additional Equipment: Additional equipment such as mixers, molds, and control systems may be required for specific applications. It is essential to factor in these costs when budgeting for foam machinery.
Operational Costs
Operational costs include expenses for energy, maintenance, and consumables. It is essential to consider these costs to ensure the machinery is cost-effective in the long term.
Energy Costs: Energy-efficient machines can significantly reduce operational costs by optimizing power consumption. It is essential to consider the machinery’s power requirements and energy-saving features.
Maintenance Costs: Regular maintenance is essential for ensuring the smooth operation of foam machinery. Machines with robust construction and advanced control systems may require less frequent maintenance, reducing downtime and costs.
Consumables: Consumables such as chemicals, additives, and molds are necessary for foam production. It is essential to consider the availability and cost of these consumables when budgeting for foam machinery.
Return on Investment (ROI)
Evaluating the potential ROI of foam machinery involves considering the initial investment, operational costs, and potential revenue generated. High-quality machinery with advanced features can offer a higher ROI by increasing production efficiency and product quality.
Production Efficiency: Machines with high production speeds and automation can increase throughput, reducing lead times and operational costs. This can lead to higher revenue and a faster ROI.
Product Quality: High-quality foam machinery can produce consistent and high-quality products, reducing the risk of defects and returns. This can enhance customer satisfaction and increase sales.
Market Demand: Understanding market demand and potential applications for foam products can help determine the ROI of foam machinery. Investing in machinery that meets market needs can lead to higher sales and profitability.
Selecting the Best Foam Machinery for Your Needs
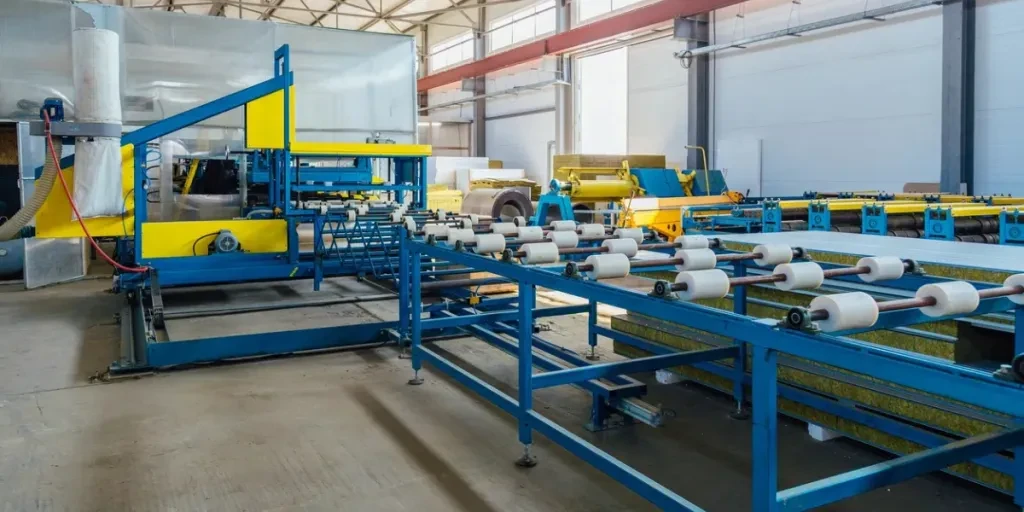
Selecting the best foam machinery requires careful consideration of various factors, including types, performance, technical specifications, materials, safety standards, and cost. By evaluating these factors, businesses can make informed decisions that meet their production needs and budget constraints.
Types and Applications
Understanding the types of foam machinery and their applications can help in selecting the most suitable equipment. For example, open cellular foam machinery is ideal for filtration applications, while closed cellular foam machinery is suitable for buoyancy and flotation.
Performance and Specifications
Evaluating the performance and technical specifications of foam machinery ensures that it meets production requirements. Key performance indicators include production speed, foam density, and cell structure uniformity. Technical specifications such as power requirements, mixing capacity, and control systems provide insights into the machinery’s capabilities.
Materials and Safety Standards
Considering the materials used in the construction of foam machinery and adherence to safety standards is essential for ensuring durability and safe operation. High-quality materials and compliance with industry standards such as CE, UL, and ISO certifications provide assurance of reliability and performance.
Cost and ROI
Balancing the initial investment with long-term operational costs and potential ROI is crucial for making cost-effective decisions. By evaluating the purchase price, installation costs, operational expenses, and potential revenue, businesses can select foam machinery that offers the best value for their investment.
Final Thoughts
In conclusion, selecting the right foam machinery involves a comprehensive evaluation of various factors, including types, performance, specifications, materials, safety standards, and cost. By considering these factors, businesses can make informed decisions that meet their production needs and budget constraints, ensuring optimal efficiency, quality, and profitability.