Sur le campus de fabrication additive d'Oberschleißheim, le groupe BMW teste la fabrication additive à arc filaire (WAAM), dans laquelle un fil en aluminium ou similaire est fondu à l'aide d'un arc. Ensuite, un robot contrôlé par logiciel superpose avec précision un grand nombre de cordons de soudure jusqu'à ce qu'un composant complet soit terminé.
Étant donné que la pression fait que couche par couche il n'est pas nécessaire de prêter attention à la démoulabilité, des structures creuses avec un rapport optimal entre rigidité et poids sont possibles.
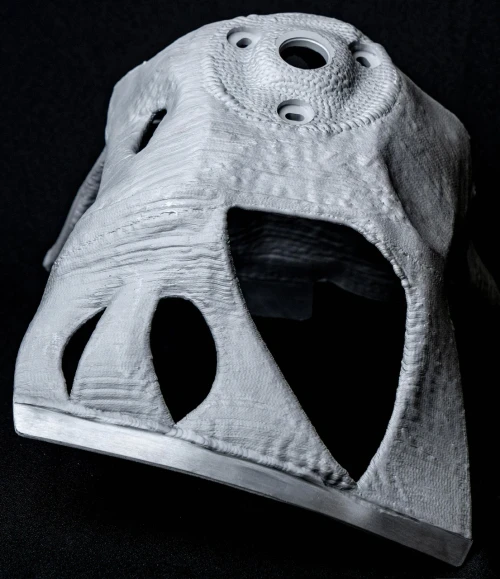
Cela signifie que les composants peuvent être plus légers et plus rigides que les pièces moulées sous pression comparables actuellement fabriquées en série. Ils peuvent également être produits de manière plus durable grâce à des besoins énergétiques moindres et à moins de déchets de matériaux. À l'avenir, il est prévu d'utiliser des composants fabriqués selon le procédé WAAM dans les véhicules de production du groupe BMW.
La grande largeur et hauteur d'un seul cordon de soudure permet de produire des composants extrêmement rapidement avec WAAM. Contrairement à la fusion par faisceau laser, déjà utilisée dans la production de prototypes et de petites séries du groupe BMW, le WAAM est particulièrement adapté aux composants de plus grande taille. Les épaisseurs de paroi typiques sont bien adaptées aux composants situés dans les zones de carrosserie, de transmission et de châssis. Cependant, des outils et des appareils peuvent également être fabriqués à l'aide de ce procédé de haute technologie, également utilisé dans l'industrie aéronautique.
Depuis 2015, les collaborateurs du groupe BMW se concentrent sur le procédé WAAM, également connu sous le nom de soudage par accumulation. Depuis 2021, une cellule WAAM pour la production de composants de test est utilisée sur le campus de fabrication additive. L'un de ces exemples d'application est un support de jambe de suspension qui, lors de tests approfondis sur banc d'essai, est comparé au composant de série fabriqué en aluminium moulé sous pression.
À ce stade précoce, il est déjà clair que le procédé WAAM peut entraîner une réduction des émissions dans le processus de production. Le poids réduit des composants, leur taux d'utilisation avantageux des matériaux et la possibilité d'utiliser des énergies renouvelables permettent de produire les composants de manière plus efficace.
—Jens Ertel, responsable de la fabrication additive BMW
La prochaine étape du développement vers la production en série consiste à tester les composants du véhicule, qui débutera dans un avenir proche.
Les cordons de soudure plus larges du procédé WAAM signifient que les surfaces des composants ne sont pas lisses, mais légèrement ondulées et doivent être finies dans les zones critiques. Cependant, les ingénieurs de BMW Group ont pu démontrer que les composants WAAM peuvent être utilisés pour des charges élevées, y compris des charges cycliques, même sans post-traitement de la surface.
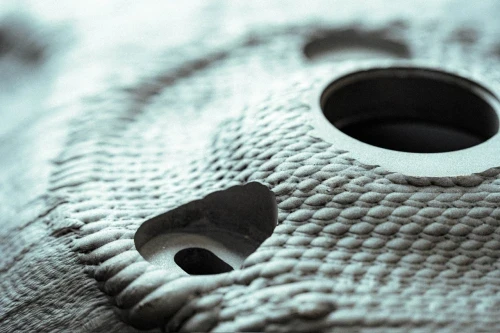
Des paramètres de processus optimisés sont cruciaux pour garantir la durabilité dès la production, c'est pourquoi la combinaison du processus de soudage et de la planification du parcours robotique doit être coordonnée de manière optimale.
Pour utiliser de manière optimale les composants produits dans le processus WAAM, la combinaison du processus de fabrication et d'une nouvelle conception générale des composants est primordiale. À cette fin, le groupe BMW continue d’accélérer l’utilisation du design génératif. Ici, l'ordinateur utilise des algorithmes pour concevoir des composants optimisés en fonction des exigences spécifiques.
Ces algorithmes sont développés en étroite collaboration avec des équipes interdisciplinaires et s’inspirent en partie des processus évolutifs de la nature. Comme pour les structures bioniques, la première étape consiste à utiliser uniquement le matériau réellement nécessaire à la topologie du composant, et lors du réglage fin de la deuxième étape, le composant n'est renforcé que là où cela est nécessaire. Cela se traduit finalement par des composants plus légers et plus rigides ainsi que par une plus grande efficacité et une dynamique améliorée du véhicule.
Les différents processus de production additive ne sont pas nécessairement en concurrence les uns avec les autres, mais doivent plutôt être considérés comme complémentaires. Par exemple, la fusion par faisceau laser continuera à être plus avantageuse que le procédé WAAM en ce qui concerne le plus haut niveau de résolution de détail. En revanche, en termes de taille possible du composant et de vitesse de dépôt, la fabrication additive à arc filaire est supérieure.
Le groupe BMW prévoit dans un premier temps une production centralisée de composants WAAM à Oberschleißheim. À l'avenir, une production sur d'autres sites et l'utilisation de la technologie par les fournisseurs seront également possibles. De plus, il serait même envisageable de produire des composants individuels directement sur la chaîne d'assemblage grâce à ce procédé et de fabriquer différentes pièces sans nouveaux outils, simplement en changeant de logiciel. La durabilité peut également être améliorée en augmentant l’utilisation de métaux recyclés.
Source à partir de Congrès des voitures vertes
Avis de non-responsabilité : les informations présentées ci-dessus sont fournies par greencarcongress.com indépendamment d'Chovm.com. Chovm.com ne fait aucune représentation ni garantie quant à la qualité et à la fiabilité du vendeur et des produits.