Avec l'introduction d'un véhicule de transport autonome dans son usine de presse, l'usine BMW Group de Regensburg avance dans la numérisation et l'automatisation de ses processus de fabrication, franchissant ainsi une nouvelle étape vers la BMW iFACTORY numérique et intelligemment connectée.
Le camion plate-forme sans conducteur, doté de sa transmission électrique, assurera de manière autonome le transport interne des outils de presse et des ébauches en acier pour les lignes de presse, avec une charge utile allant jusqu'à 55 tonnes. Grâce à la technologie des capteurs, le système de transport se déplace de manière précise et totalement autonome dans les installations de production de l'usine de presse de Ratisbonne à une vitesse de quatre kilomètres par heure. BMW affirme que la solution n'existe actuellement nulle part ailleurs dans le monde.
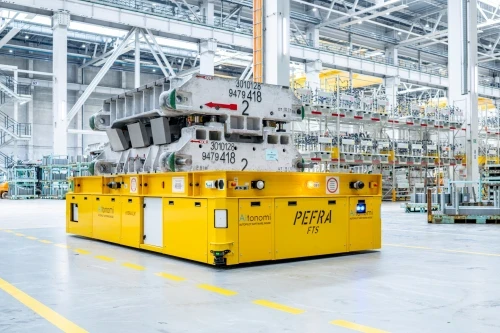
Nous voyons un énorme potentiel dans le déploiement de solutions logistiques autonomes. Le véhicule électrique sans émissions nous permettra de rendre les processus de fabrication de notre usine de presses encore plus efficaces et plus flexibles, ainsi que de réduire les trajets et les délais de transport. Cela permettra non seulement d’augmenter la productivité, mais également d’économiser de l’énergie et d’améliorer la sécurité au travail de nos collaborateurs.
—Tobias Müller, responsable de la maintenance de l'usine de presse de l'usine BMW Group de Ratisbonne
Le nouveau véhicule de transport sans conducteur utilise la technologie innovante LiDAR (Light Detection And Ranging) du fabricant Pefra. En conjonction avec des caméras et des capteurs radar, ils surveillent leur environnement, facilitant l'orientation, la détection des obstacles et la mesure de la distance, offrant ainsi une sécurité et une efficacité accrues dans un environnement complexe, que ce soit sur des routes très fréquentées ou dans des environnements industriels automatisés, comme dans la presse du groupe BMW. usine à Ratisbonne. Le processus LiDAR 3D consiste à scanner l'environnement, à l'aide de nombreuses mesures de distance optique individuelles qui sont ensuite combinées pour générer un nuage de points 3D de l'environnement capturé par le capteur LiDAR.
L'usine de presses de l'usine BMW Group de Regensburg traite environ 1,100 131,000 tonnes d'acier par jour ouvrable, ce qui équivaut à une production quotidienne de 113 4.5 pièces embouties. L'étendue de la production comprend XNUMX composants de carrosserie différents. Outre les pièces structurelles et de renforcement, l'usine de presse façonne également de grandes sections de panneaux extérieurs, tels que des cadres latéraux, des revêtements extérieurs de porte et des capots, à partir de tôle d'acier pouvant mesurer jusqu'à XNUMX mètres de longueur.
Les rouleaux d'acier traités peuvent peser jusqu'à 33 tonnes. La plus puissante des quatre lignes de presse de l'atelier de presse de Ratisbonne exploite la technologie d'asservissement à grande vitesse, ce qui en fait l'une des presses les plus rapides au monde, avec une force de presse de 9,000 23 tonnes, soit l'équivalent du poids de la Tour Eiffel. La presse atteint une cadence allant jusqu'à XNUMX coups par minute. Les composants de carrosserie fabriqués à l'usine de presse sont ensuite assemblés en carrosseries de véhicules dans l'atelier de carrosserie voisin de l'usine BMW Group de Regensburg.
L'exploitation de l'atelier d'imprimerie de Ratisbonne génère chaque année environ 80,000 40 tonnes de chutes, qui sont ensuite recyclées en boucle fermée. La première étape consiste à traiter les chutes dans une presse de recyclage, qui les transforme en cubes d'acier mesurant 40 x 220 centimètres et pesant chacun XNUMX kilogrammes. Ceux-ci sont ensuite renvoyés au fournisseur d'acier, où ils sont transformés en ce que l'on appelle de l'acier secondaire.
L'utilisation d'acier secondaire dans l'usine de presses du groupe BMW à Ratisbonne génère deux tonnes de CO en moins2 par tonne d'acier, par rapport à la production d'acier primaire. Cela réduit le CO de la plante2 empreinte écologique d'environ 160,000 XNUMX tonnes par an. Afin de protéger les employés, les résidents et l'environnement des émissions sonores et des vibrations, les installations de production et de recyclage de l'usine de presse de Ratisbonne sont équipées d'une isolation phonique. De plus, tous les systèmes de production fonctionnent avec un minimum de vibrations.
Source à partir de Congrès des voitures vertes
Avis de non-responsabilité : les informations présentées ci-dessus sont fournies par greencarcongress.com indépendamment d'Chovm.com. Chovm.com ne fait aucune représentation ni garantie quant à la qualité et à la fiabilité du vendeur et des produits.