En 2025, la demande de contrôle de mouvement précis dans l'automatisation industrielle continue d'augmenter, stimulée par les progrès de la technologie et des matériaux. Cet article fournit une analyse approfondie des facteurs clés à prendre en compte lors de la sélection des mécanismes à crémaillère et pignon, offrant des informations précieuses aux acheteurs professionnels. Des spécifications de performance à la qualité des matériaux, ce guide vous aidera à prendre des décisions d'achat éclairées.
Sommaire :
-Aperçu du marché des mécanismes à crémaillère et pignon
-Analyse approfondie du marché des crémaillères et pignons
- Tendances et innovations clés
-Facteurs clés lors de la sélection des mécanismes à crémaillère et pignon
-Applications avancées des mécanismes à crémaillère et pignon
-Progrès technologiques dans les systèmes à crémaillère et pignon
-Normes réglementaires et conformité
-Réflexions finales
Aperçu du marché des mécanismes à crémaillère et pignon
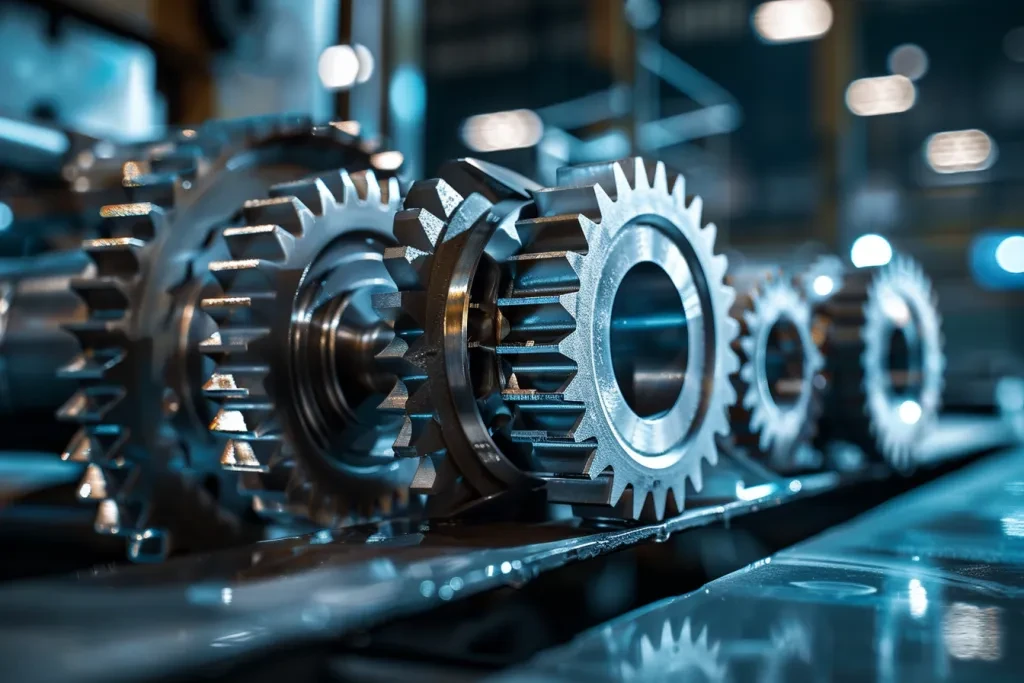
Le marché mondial des crémaillères et pignons industriels était évalué à environ 1.7 milliard USD en 2023 et devrait atteindre 2.7 milliards USD d'ici 2030, ce qui reflète un taux de croissance annuel composé (TCAC) de 6.5 % entre 2023 et 2030. Cette croissance est tirée par la demande croissante d'automatisation et de précision dans divers processus industriels. Le marché américain à lui seul était estimé à 470.4 millions USD en 2023, tandis que la Chine devrait croître à un TCAC impressionnant de 10.4 %, pour atteindre 579.8 millions USD d'ici 2030.
La segmentation du marché indique que les crémaillères et pignons en acier allié devraient atteindre 1.1 milliard USD d'ici 2030, avec un TCAC de 6.5 %. Le segment des crémaillères et pignons en acier au carbone devrait croître à un TCAC de 5.1 % sur la même période. Les principales régions contribuant à cette croissance sont le Japon, le Canada, l'Allemagne et la région Asie-Pacifique au sens large. L'adoption croissante de matériaux avancés, tels que les alliages à haute résistance et les plastiques techniques, améliore considérablement la durabilité et les performances des crémaillères et pignons, en particulier dans les environnements difficiles.
Analyse approfondie du marché des crémaillères et pignons
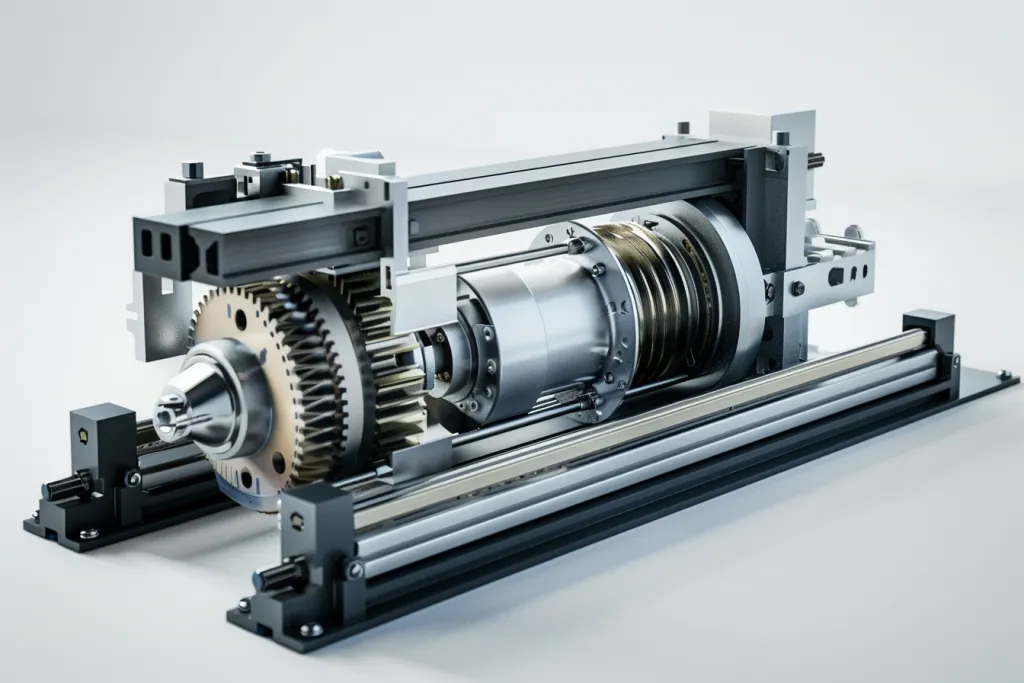
Les mécanismes à crémaillère et pignon sont essentiels pour convertir un mouvement de rotation en mouvement linéaire et vice versa. Ils sont essentiels dans les machines, la robotique et les systèmes d'automatisation pour un contrôle précis des mouvements. Initialement utilisés dans les machines de base et les opérations manuelles, ces composants prennent désormais en charge des systèmes sophistiqués et performants.
Les critères de performance clés des crémaillères et pignons comprennent la précision, la durabilité et les capacités de manutention de charges. Les crémaillères et pignons de haute précision offrent une précision et une répétabilité améliorées, essentielles pour les machines CNC et la robotique. L'intégration de capteurs et de systèmes de contrôle avancés permet une surveillance et un réglage en temps réel du mouvement, améliorant ainsi les performances et la fiabilité du système.
Le comportement des consommateurs évolue vers des solutions de contrôle de mouvement plus efficaces et plus fiables, notamment dans les secteurs de l'automobile, de l'aéronautique et de la fabrication. L'essor de l'industrie 4.0 et l'utilisation croissante de la robotique et de l'automatisation stimulent la demande de systèmes à crémaillère et pignon avancés. Les entreprises se concentrent sur l'innovation et la différenciation, en particulier sur les marchés de niche nécessitant des solutions personnalisées.
Principales tendances et innovations
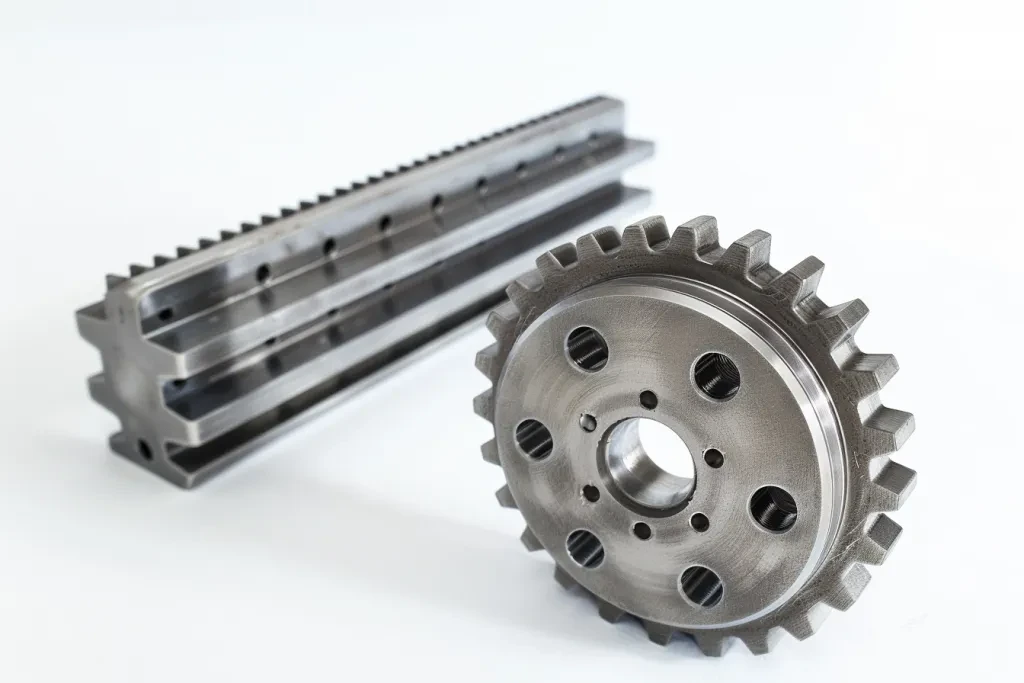
Le marché a connu des tendances et des innovations importantes, notamment le développement de crémaillères et pignons de haute précision et l'utilisation de matériaux avancés pour améliorer la durabilité. L'intégration de systèmes à crémaillère et pignon avec des capteurs et des systèmes de contrôle avancés permet une surveillance et un réglage en temps réel du mouvement. Les actionneurs et servomoteurs électriques combinés aux systèmes à crémaillère et pignon élargissent leurs applications, notamment dans les systèmes automatisés et robotisés.
Les influences économiques telles que la poussée mondiale vers l'automatisation et le besoin de précision dans les processus industriels sont des moteurs majeurs de la croissance du marché. La transition vers la numérisation et l'adoption des technologies de l'industrie 4.0 remodèlent la dynamique du marché, mettant l'accent sur la fabrication intelligente. Les besoins des clients en matière de précision et de fiabilité élevées dans le contrôle des mouvements sont satisfaits par l'innovation continue et le développement de produits hautes performances.
Facteurs clés lors de la sélection des mécanismes à crémaillère et pignon
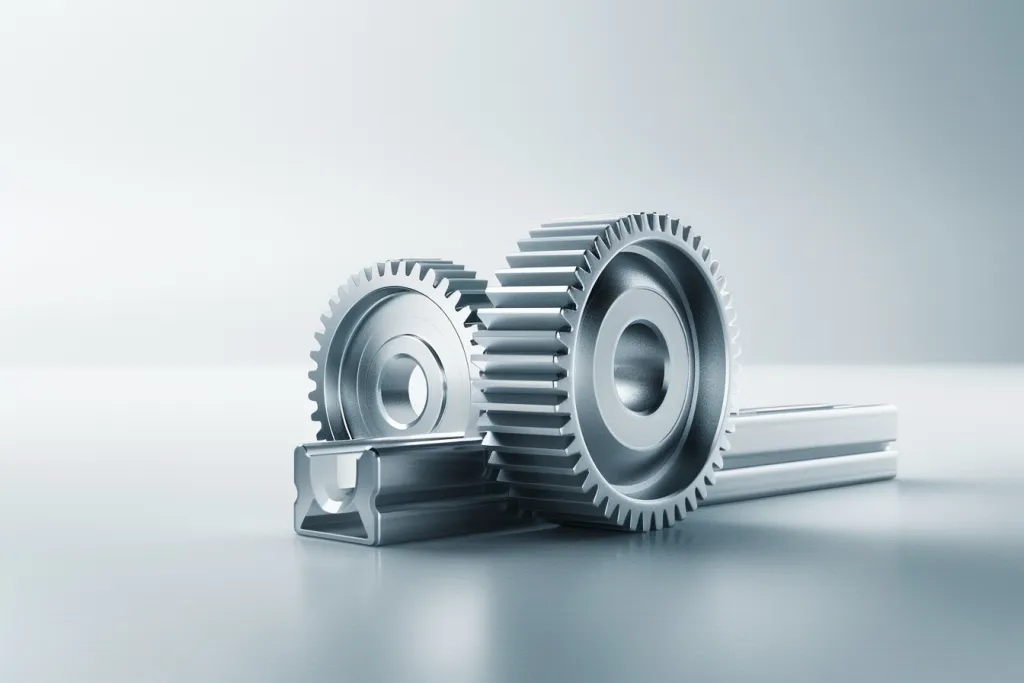
Types de mécanismes à crémaillère et pignon
Les mécanismes à crémaillère et pignon sont disponibles en plusieurs types, chacun adapté à des applications et des exigences de performance spécifiques. Les types les plus courants comprennent les crémaillères à dents droites, les crémaillères à dents hélicoïdales et les entraînements à pignon à rouleaux. Les crémaillères à dents droites ont des dents qui sont parallèles à l'axe de l'engrenage, adaptées aux mouvements de charge manuels simples. Cependant, elles peuvent être bruyantes et moins efficaces. Les crémaillères à dents hélicoïdales ont des dents torsadées le long d'un chemin hélicoïdal, offrant un engagement continu sur toute la longueur de la dent, ce qui se traduit par un fonctionnement plus silencieux et plus efficace, idéal pour les applications de haute précision et à grande vitesse. Les entraînements à pignon à rouleaux utilisent des rouleaux supportés par des roulements qui s'engrènent avec les dents de la crémaillère, offrant un jeu minimal voire nul, essentiel pour une précision et une répétabilité élevées.
Performances et fonctionnalités
Lors de la sélection d'un mécanisme à crémaillère et pignon, tenez compte des spécifications de performances telles que la force d'entraînement de l'axe, le poids nominal de l'axe et l'angle de pression. La force d'entraînement de l'axe est la force maximale que le mécanisme peut supporter, déterminée par le couple du moteur transmis par le pignon à la crémaillère. Le poids nominal de l'axe indique la charge maximale que l'axe entraîné peut supporter. L'angle de pression décrit la forme des dents et l'angle qu'elles forment avec les espaces de la crémaillère, ce qui affecte la fluidité avec laquelle le pignon roulera. Un angle de pression plus large entraîne généralement un fonctionnement plus fluide. De plus, la vitesse à laquelle la crémaillère se déplace lorsque le pignon tourne est influencée par le diamètre de l'engrenage, ce qui rend essentiel d'adapter la taille de l'engrenage à la vitesse et à la précision requises par l'application.
Qualité des matériaux et de la construction
Le matériau et la qualité de fabrication des mécanismes à crémaillère sont essentiels pour garantir la durabilité et les performances à long terme. Les matériaux courants comprennent l'acier trempé, l'acier inoxydable et divers alliages. L'acier trempé est souvent utilisé pour sa solidité et sa résistance à l'usure, adapté aux applications à forte charge. L'acier inoxydable offre une résistance à la corrosion, bénéfique dans les environnements exposés à l'humidité ou aux produits chimiques. Les alliages peuvent offrir un équilibre entre résistance, durabilité et résistance à la corrosion. La qualité des dents, qu'elles soient fraisées, taillées avec précision ou rectifiées, affecte également les performances. Les dents fraisées sont utilisées pour des applications générales, tandis que les dents taillées avec précision et rectifiées sont réservées aux applications de haute précision et de haute performance.
Compatibilité et intégration
La compatibilité avec les systèmes existants et les futures mises à niveau est cruciale. Les mécanismes à crémaillère et pignon doivent être compatibles avec les moteurs et les systèmes de commande utilisés dans l'application. Cela implique de s'assurer que le diamètre d'alésage du pignon correspond à l'arbre du moteur et que les configurations de montage correspondent aux exigences du système. Tenir compte du potentiel de mise à niveau, comme le passage à un mécanisme de plus grande précision ou à plus grande capacité de charge, peut permettre de gagner du temps et de réduire les coûts à long terme. Assurer une intégration transparente avec d'autres composants, tels que les guides linéaires et les actionneurs, est essentiel pour des performances et une fiabilité optimales.
Considérations de coût et de budget
Le coût des mécanismes à crémaillère et pignon peut varier considérablement en fonction du type, du matériau et de la précision requise. Les crémaillères à dents droites sont généralement l'option la plus rentable, tandis que les entraînements à dents hélicoïdales et à pignon à rouleaux ont tendance à être plus chers en raison de leurs performances et de leur précision supérieures. Il est important d'équilibrer le coût initial avec les avantages à long terme, tels qu'une maintenance et des temps d'arrêt réduits, une efficacité accrue et une durée de vie plus longue. Les considérations budgétaires doivent également inclure le coût d'installation, les temps d'arrêt potentiels pendant la configuration et tous les composants supplémentaires requis pour l'intégration. L'évaluation du coût total de possession, plutôt que du simple prix d'achat initial, peut aider à prendre une décision plus éclairée.
Applications avancées des mécanismes à crémaillère et pignon
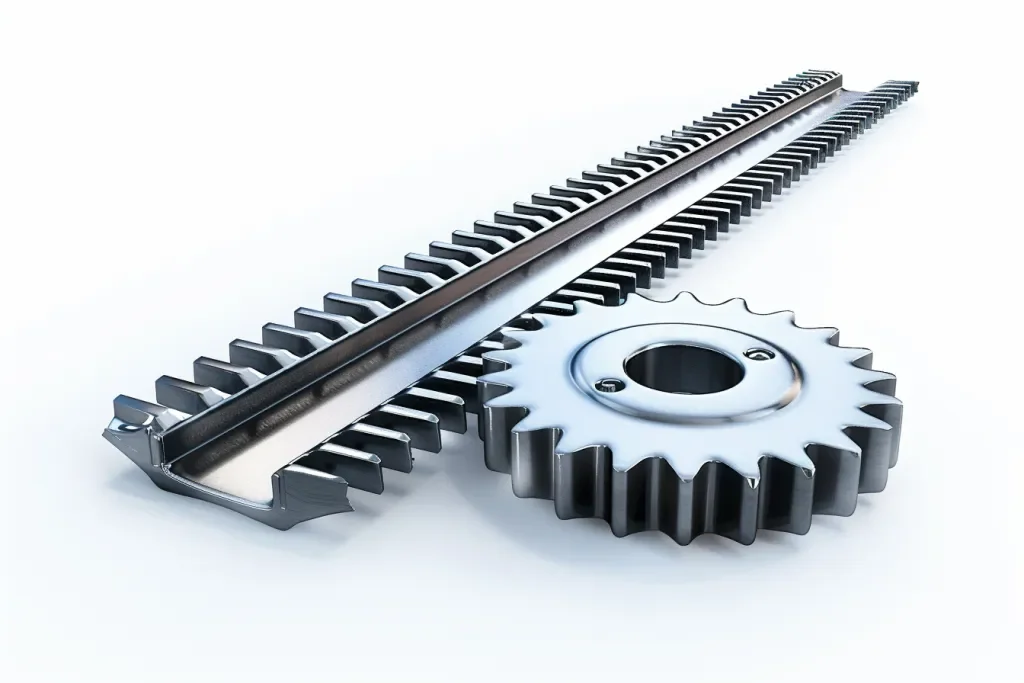
Les mécanismes à crémaillère et pignon sont largement utilisés dans diverses industries en raison de leur capacité à convertir efficacement le mouvement de rotation en mouvement linéaire. Dans l'industrie automobile, ils font partie intégrante des systèmes de direction, offrant un contrôle et un retour d'information précis au conducteur, essentiels à la sécurité et aux performances du véhicule. Dans l'automatisation industrielle, les entraînements à crémaillère et pignon sont utilisés pour positionner les tables des machines-outils, permettant des mouvements précis et répétables essentiels aux processus de fabrication de haute précision. Ils sont également utilisés en robotique pour l'actionnement linéaire, offrant un contrôle de mouvement fiable et efficace dans les bras robotisés et les véhicules à guidage automatique.
Dans le secteur de la construction, les mécanismes à crémaillère sont utilisés dans les ascenseurs et les systèmes de levage temporaires, facilitant le déplacement vertical des matériaux et du personnel. Ces mécanismes offrent robustesse et fiabilité, essentielles pour les conditions exigeantes des chantiers de construction. De plus, ils sont utilisés dans les manèges de parcs d'attractions, où un contrôle précis et sûr du mouvement est primordial. La capacité des entraînements à crémaillère à supporter des charges élevées et à assurer un positionnement précis les rend idéaux pour de telles applications.
Progrès technologiques dans les systèmes à crémaillère et pignon
Les progrès technologiques ont considérablement amélioré les performances et la polyvalence des systèmes à crémaillère et pignon. L'intégration de mécanismes de préchargement électroniques, qui utilisent un deuxième moteur pour appliquer une force opposée, élimine le jeu et améliore la précision, constitue une avancée notable. Cette technologie est particulièrement avantageuse dans les applications nécessitant une grande précision, telles que les machines CNC et les équipements de fabrication de semi-conducteurs. Une autre avancée réside dans l'utilisation de matériaux avancés, tels que les composites en fibre de carbone, qui réduisent le poids tout en conservant la résistance et la rigidité, ce qui permet un contrôle de mouvement plus rapide et plus efficace, en particulier dans les applications à grande vitesse.
L'intégration de capteurs intelligents et de la connectivité IoT permet une surveillance en temps réel et une maintenance prédictive. Ces capteurs peuvent détecter l'usure et le désalignement, fournissant des avertissements précoces et réduisant le risque de pannes inattendues. Les données collectées peuvent être analysées pour optimiser les performances et prolonger la durée de vie du mécanisme. De plus, les progrès des techniques de fabrication, telles que la fabrication additive, permettent la production de composants de crémaillère et de pignon complexes et personnalisés avec une grande précision et des délais de livraison réduits.
Normes réglementaires et conformité
Le respect des normes réglementaires est essentiel pour garantir la sécurité et la fiabilité des mécanismes à crémaillère. L'American Gear Manufacturers Association (AGMA) définit des normes de niveau de qualité pour les engrenages, y compris les systèmes à crémaillère. Ces normes couvrent des aspects tels que la variation de pas, l'erreur de profil et la précision de l'alignement des dents. Les niveaux de qualité supérieurs, tels que AGMA 10 et AGMA 11, indiquent des engrenages à dents trempées et rectifiées, adaptés aux applications de haute précision. Le respect de ces normes garantit que les mécanismes répondent aux critères de performance et de durabilité requis.
Outre les normes AGMA, il est nécessaire de respecter les réglementations spécifiques à chaque secteur. Par exemple, dans l'industrie automobile, les systèmes de direction à crémaillère doivent répondre à des normes de sécurité strictes fixées par des organismes de réglementation tels que la National Highway Traffic Safety Administration (NHTSA) et le programme européen d'évaluation des nouveaux véhicules (Euro NCAP). Ces normes garantissent que les systèmes de direction offrent des performances fiables et sûres dans diverses conditions de fonctionnement. De même, dans le secteur de la construction, les systèmes de levage utilisant des mécanismes à crémaillère doivent être conformes aux réglementations de sécurité au travail pour protéger les travailleurs et garantir un fonctionnement sûr.
Réflexions finales
En résumé, le choix du mécanisme à crémaillère approprié implique de prendre en compte divers facteurs, notamment le type de mécanisme, les spécifications de performance, la qualité des matériaux et de la fabrication, la compatibilité et le coût. Les progrès technologiques continuent d'améliorer les performances et la polyvalence de ces systèmes, les rendant ainsi adaptés à une large gamme d'applications. Le respect des normes réglementaires garantit la sécurité et la fiabilité, qui sont essentielles pour les applications industrielles. En évaluant soigneusement ces facteurs, les entreprises peuvent choisir le mécanisme à crémaillère le plus adapté à leurs besoins spécifiques, garantissant ainsi des performances, une efficacité et une longévité optimales.