With the demand for bottles rising in the food and beverage, pharmaceutical, and personal care industries, the significance of high-quality bottle-making machines cannot be overstated. These machines are utilized to produce a diverse range of bottles in various shapes and sizes, making the process of choosing the ideal machine for your specific requirements a challenging task.
In this article, we will delve into the process of selecting the perfect bottle-making machine so that you can make the optimal decision for your enterprise. We will also discuss the different types of bottle-making machines available and provide a market overview.
Table of Contents
Overview of the bottling line machinery market
Types of bottle-making machines
How to buy the ideal bottle-making machine
Summary
Overview of the bottling line machinery market
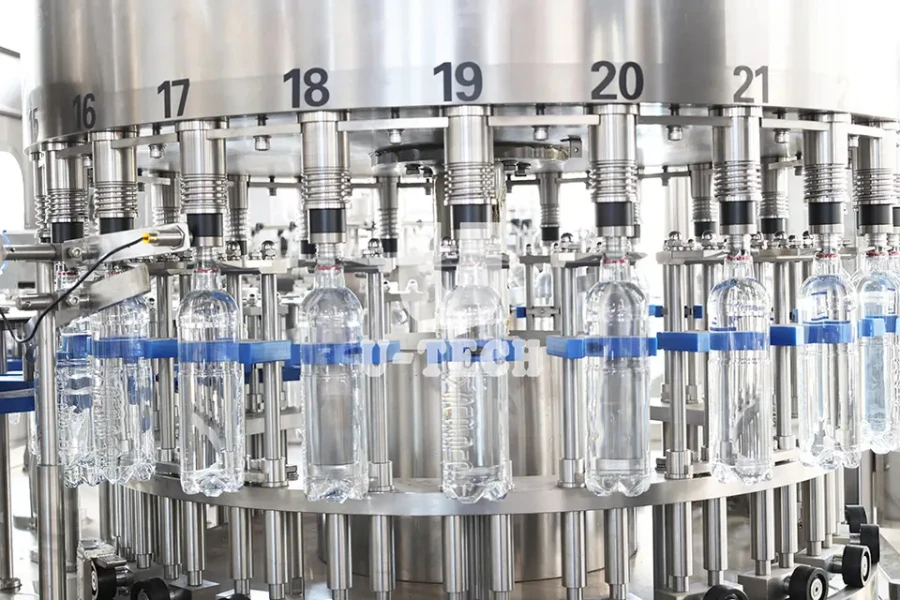
According to reports published by Grand View Research, as of 2021, the bottling machinery market was valued at US $4.33 billion worldwide. This figure is expected to grow at a compound annual growth rate of 4.6% from 2022 to 2030.
Some of the factors leading to the increase in demand for bottle-making machines include the rising prominence of beverage products that have unique tastes and colors, the rise in e-commerce, which has increased the demand for bottles used to shop for products, and technological advancements in the bottle-making machines industry, which have helped to produce productive and efficient machines.
Regions with a high demand for bottle-making machines include Asia-Pacific, North America, Europe, Latin America, Africa, and the Middle East. The cause of the high demand of bottle-making machines in the Asia-Pacific region is the growth of various industries like food and beverage, personal care, and pharmaceuticals. China, Japan, and India are among the countries with the largest demand for bottle-making machines.
Types of bottle-making machines
1. Extrusion blow molding machines
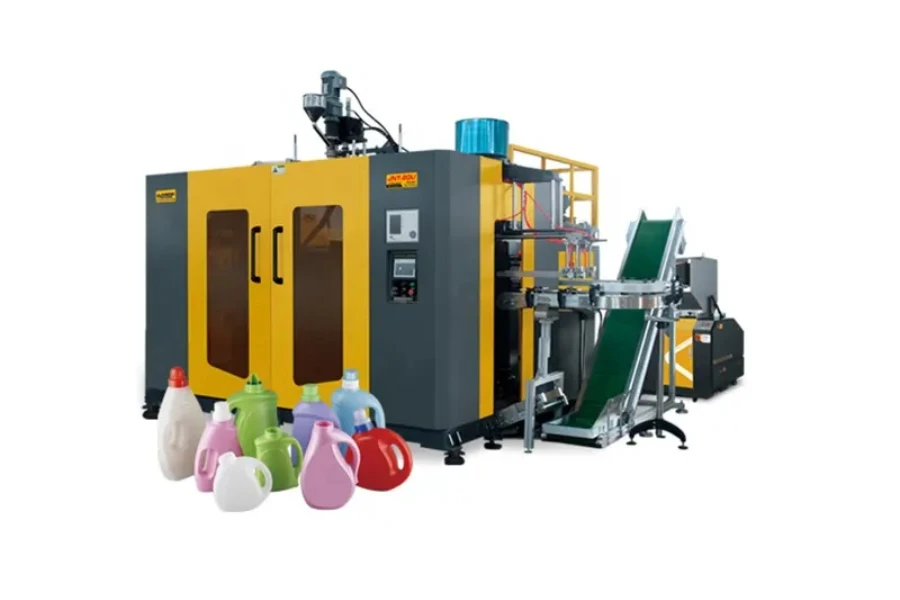
Extrusion blow molding machines utilize melted plastic that is forced through a die and then inflated using compressed air to achieve the desired shape for the bottle. This method is commonly employed for manufacturing liquid bottles, including water, juice, and oil containers.
Pros
- Efficient production process
- High production output
- Versatility in producing various shapes and sizes
- Cost-effective for large-scale production
- Wide range of compatible materials
Cons
- Initial setup and tooling costs can be high
- Limited to producing hollow plastic products
- Requires skilled operators for setup and maintenance
2. Injection blow molding machines
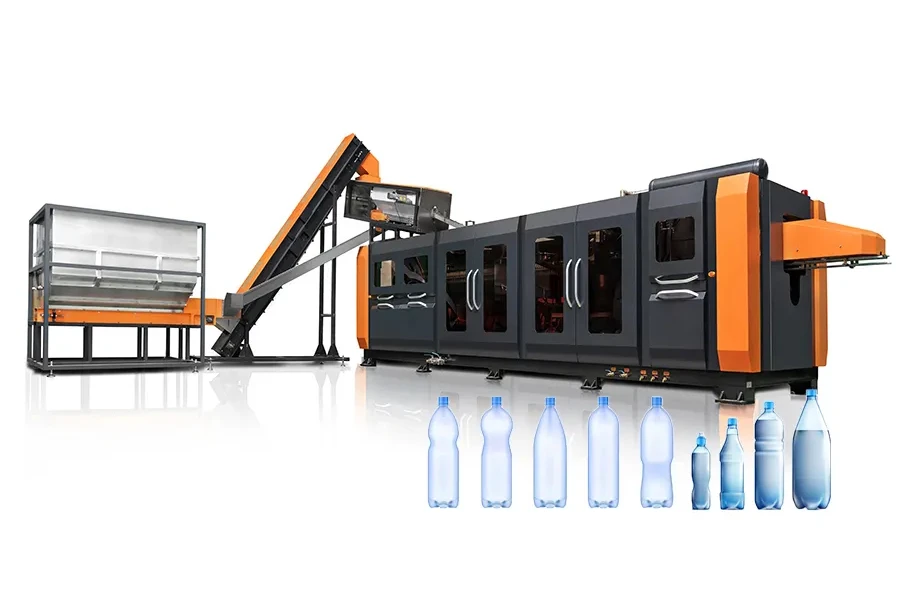
Injection blow molding machines inject molten plastic into a preform mold and then stretch and inflate it to form the final shape of the bottle. The process is particularly suitable for creating small to medium-sized bottles commonly used in pharmaceuticals, cosmetics, and personal care products.
Pros
- Precise and consistent production of complex shapes and sizes
- Ability to produce high-quality, seamless, and uniform products
- Wide range of compatible materials, including specialized resins
- Efficient production process with high production output
- Suitable for both small-scale and large-scale production
Cons
- Higher initial setup and tooling costs compared to other molding processes
- Limited to producing smaller-sized products
- Requires skilled operators for setup, maintenance, and troubleshooting
3. Stretch blow molding machines
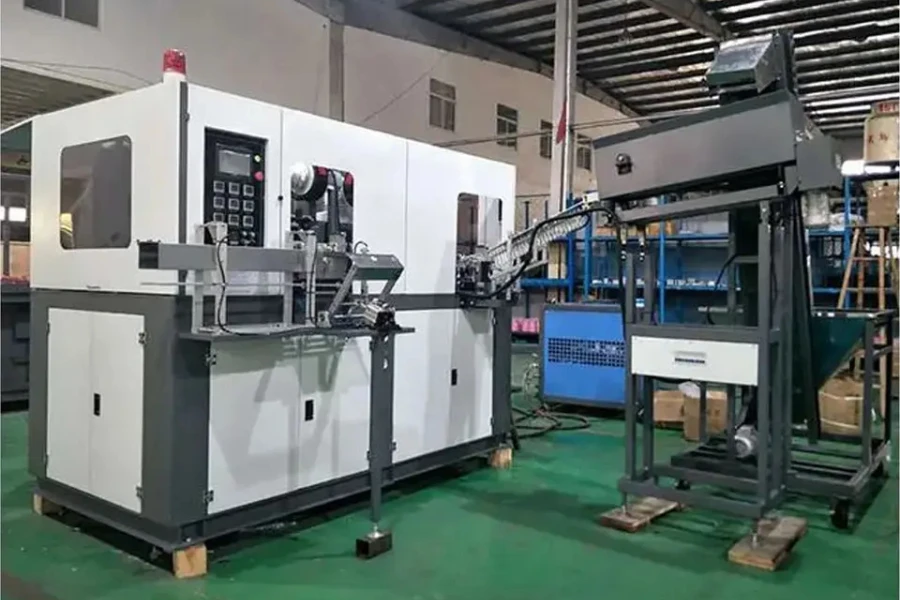
Stretch blow molding machines create bottles by stretching preform molds and inflating them to their final shape using compressed air. This technique is especially advantageous for producing premium-quality bottles, including carbonated beverages, water, and other liquids.
Pros
- Excellent production efficiency and high-speed operation
- Ability to produce high-quality, clear, and transparent bottles
- Wide range of compatible materials, including PET (polyethylene terephthalate)
- Ideal for producing bottles with complex shapes, such as handles or unique contours
- Well-suited for large-scale production due to its high output capabilities
Cons
- Limited to producing bottles and containers; not suitable for other shapes
- The initial setup and tooling costs are high when compared to simpler molding processes
- Requires precise control of temperature and stretching parameters, demanding skilled operators and maintenance personnel
4. Compression blow molding machines
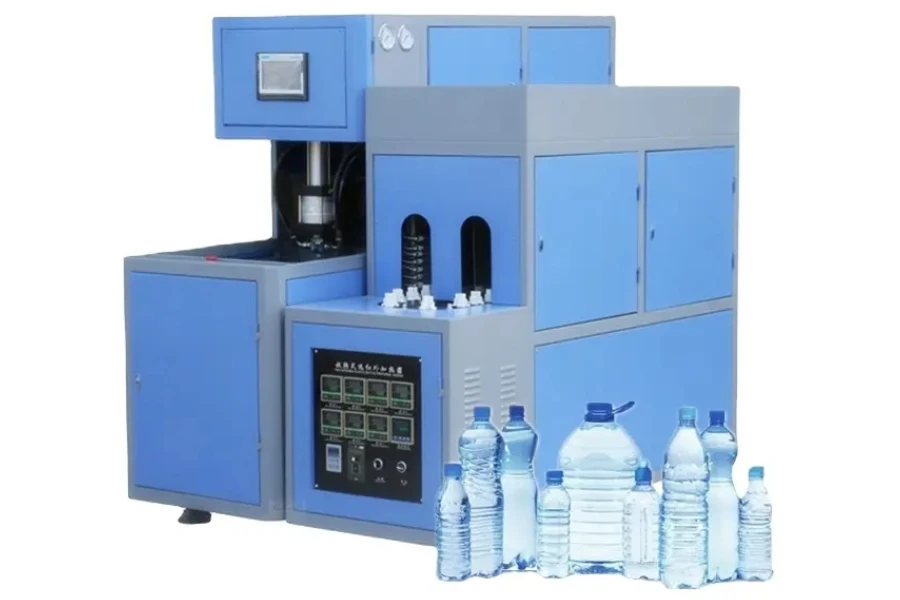
Compression blow molding machines produce bottles by heating a plastic preform and then compressing it into the desired shape with a mold. The method is particularly suitable for creating larger bottles, commonly utilized in industrial chemicals and automotive fluids industries.
Pros
- Versatility in producing various shapes and sizes, including complex designs and irregular geometries
- Ability to manufacture bottles with consistent wall thickness and excellent dimensional accuracy
- Cost-effective for small to medium-scale production, as it requires simpler tooling and lower initial setup costs compared to other molding processes
- It is suitable for producing high-quality bottles and durable bottles, making them ideal for packaging applications
- Offers flexibility in material selection, allowing for compatibility with various plastic resins
Cons
- Relatively slower production cycle compared to other blow molding processes, resulting in lower production output
- Requires more energy consumption due to the compression step in the process
- Limited to producing smaller to medium-sized bottles and containers, unsuitable for large-scale production
5. Injection stretch blow molding machines
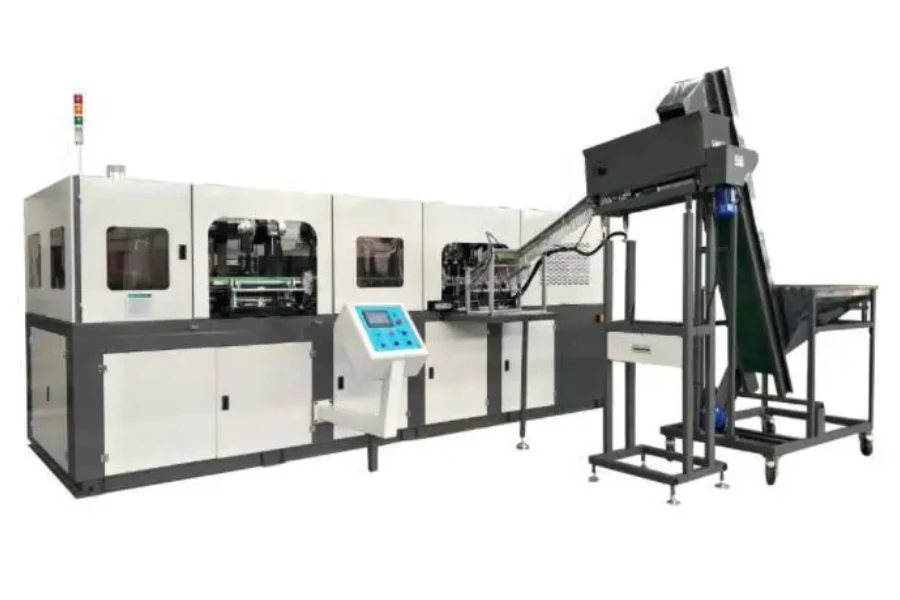
The injection stretch blow molding machine incorporates the advantages of both injection and stretch blow molding processes, allowing the creation of high-quality bottles with intricate shapes and features. It benefits manufacturing bottles used in the cosmetics, personal care products, and pharmaceutical industries.
Pros
- Exceptional production of high-quality, crystal-clear bottles with excellent clarity and transparency
- Enables production of bottles with precise neck finishes, threads, and intricate designs
- Versatility in producing various bottle sizes and shapes, including complex geometries and lightweight designs
- Efficient and streamlined production process with reduced cycle times, leading to higher production output
- Offers the ability to incorporate multi-layer constructions, allowing for enhanced barrier properties and product integrity
Cons
- There are higher initial setup and tooling costs than other blow molding processes due to the combination of injection and stretch blow molding steps
- Requires skilled operators to ensure proper setup, programming, and maintenance of the machine
- Only limited to producing bottles and containers, unsuitable for manufacturing other product types or shapes
How to buy the ideal bottle-making machine
1. Production capacity
Bottle-making machines have varying capacities, which is the number of bottles they can produce in a given period. The average capacity range of these machines is between 1,000 to 8,000 bottles per hour, depending on the type of machine and its specifications.
To choose the right machine for your needs, it is important to consider current and future production needs and the demand for a product. it will help you avoid purchasing a machine that is either too small or too large for your requirements.
2. Cost
The cost of a bottle-making machine can vary significantly depending on factors such as production capacity, technology, and features. On average, a basic bottle-making machine can cost anywhere from US $20,000 to US $50,000, while more advanced machines with higher production capacities and additional features can cost upwards of US $100,000 or more.
It’s important to remember that the initial purchase cost is not the only cost to consider, as maintenance, repairs, and operational expenses can also add up over time.
3. Speed
The speed required depends on the production needs and the demand for a product. While a faster bottle-making machine may be more expensive, it may also result in greater efficiency and productivity, reducing overall production costs in the long term. It is essential to balance speed and cost and consider the potential benefits of faster production rates when deciding on a bottle-making machine.
The average speed range for bottle-making machines varies between 1,000 and 12,000 bottles per hour.
4. Durability
It is essential to opt for a machine with durable construction and high-quality materials, as it can significantly impact the longevity of the machine and its maintenance costs. The average lifespan of a bottle-making machine can vary depending on its quality, usage, and maintenance. Investing in a durable machine can minimize unexpected downtime and repair costs, ultimately improving the ROI of the machine.
5. Types of bottles
The type of bottle the machine manufactures can influence your choice of machine. Various bottle-making machines are engineered to create specific types of bottles, including those with intricate shapes, sizes, or features. Therefore, it is vital to factor in the type of bottles you require and confirm that your desired machine can fulfill them.
6. Quality
Producing high-quality bottles is crucial for maintaining a positive brand image and ensuring customer satisfaction. Thus, when purchasing a bottle-making machine, it is essential to consider its ability to produce bottles of high quality consistently.
Low-quality bottles can negatively impact your brand reputation and lead to a decrease in sales and revenue. It is recommended to research and read reviews on the machines you are considering to ensure that they have a track record of producing high-quality bottles consistently.
Summary
Purchasing the perfect bottle-making machine involves considering several factors, such as production capacity, cost, speed, durability, applicable materials, types of bottles, and quality. Each of these factors plays a significant role in determining the suitability of a machine for your business needs. To find a range of bottle-making machines that fit your requirements, visit Chovm.com.