The increasing demand for precision cutting in industries like aerospace and automotive has propelled the Water Pressure Cutter market to new heights in 2025. This article provides a comprehensive analysis, helping professional buyers make informed decisions by highlighting key selection factors, market trends, and future advancements in water pressure cutting technology.
Daftar Isi:
– Market Overview of Water Pressure Cutters
– Detailed Introduction and Analysis of the Water Pressure Cutter Market
– Evidence for Market Trends and Phenomena
– Key Factors When Selecting a Water Pressure Cutter
– Material Compatibility and Performance
– Maintenance and Operational Considerations
– Future Trends in Water Pressure Cutting Technology
– Pikiran Terakhir
Market Overview of Water Pressure Cutters
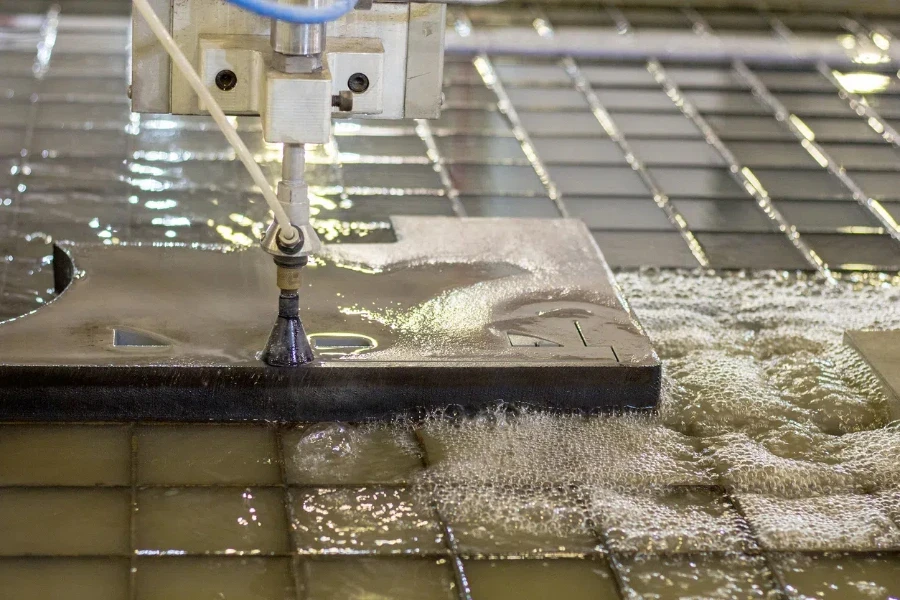
The global market for water pressure cutters, also known as water jet cutters, has been experiencing significant growth. As of 2024, the market was valued at USD 3.13 billion and is projected to reach USD 4.34 billion by 2030, growing at a compound annual growth rate (CAGR) of 5.58%. This growth is driven by increasing demand across sectors such as automotive, aerospace, electronics, and construction, where precision cutting is crucial.
The Asia-Pacific region is expected to be the fastest-growing market, driven by rapid industrialization and urbanization in countries like China and India. North America and Europe continue to hold significant market shares due to their advanced manufacturing sectors and high adoption rates of cutting-edge technologies. These regions benefit from the need for high-precision cutting tools in industries such as automotive and aerospace.
The market is segmented by type, including pure waterjet cutters and abrasive waterjet cutters. Abrasive waterjet cutters hold a larger market share due to their ability to cut through harder materials like metal and stone. The industrial segment dominates end-user applications, with significant demand from the automotive, aerospace, and electronics industries.
Detailed Introduction and Analysis of the Water Pressure Cutter Market
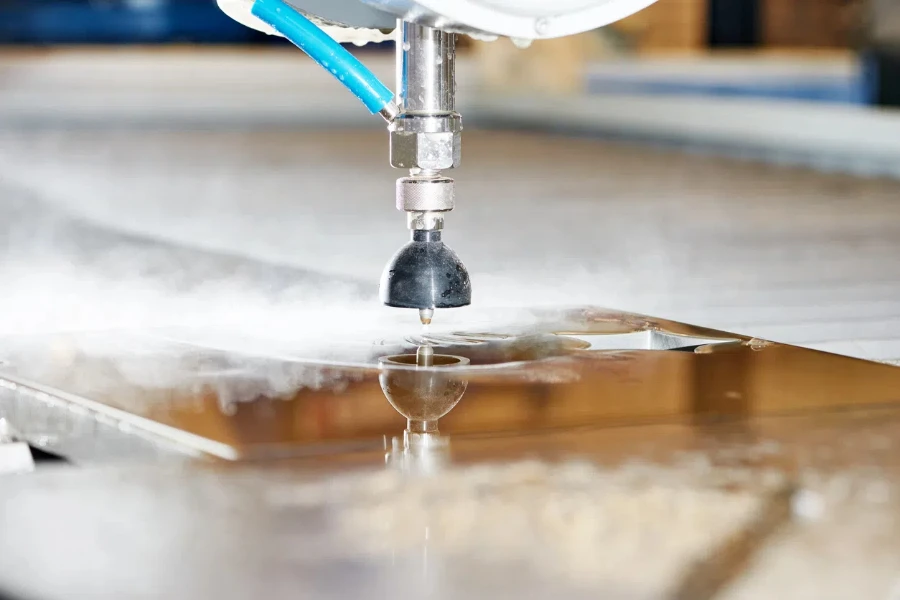
Water pressure cutters are essential tools in modern manufacturing, known for their ability to cut a wide range of materials with exceptional precision. These machines use a high-pressure water stream, often mixed with abrasive materials, to slice through metals, composites, glass, and ceramics. Key performance benchmarks for water pressure cutters include cutting speed, precision, operational cost, and maintenance requirements.
Leading companies like Flow International Corporation, OMAX Corporation, and KMT Waterjet Systems dominate the market. These companies continuously innovate to enhance the efficiency and capabilities of their machines, integrating advanced technologies such as IoT and AI for better operational control and predictive maintenance.
Economic influences, such as the rising cost of raw materials and energy, impact the market. However, the increasing emphasis on precision manufacturing and the ability to cut complex shapes without thermal distortion make water pressure cutters indispensable in industries requiring high precision. Consumer behavior is shifting towards eco-friendly and energy-efficient solutions, driving the demand for water pressure cutters that minimize waste and reduce environmental impact.
Distribution channels for water pressure cutters include direct sales, distributors, and online platforms. Large industrial buyers who require customized solutions and after-sales support often prefer direct sales. Recent innovations in the market include the development of portable and compact water pressure cutters, making them more accessible for small and medium-sized enterprises.
Evidence for Market Trends and Phenomena
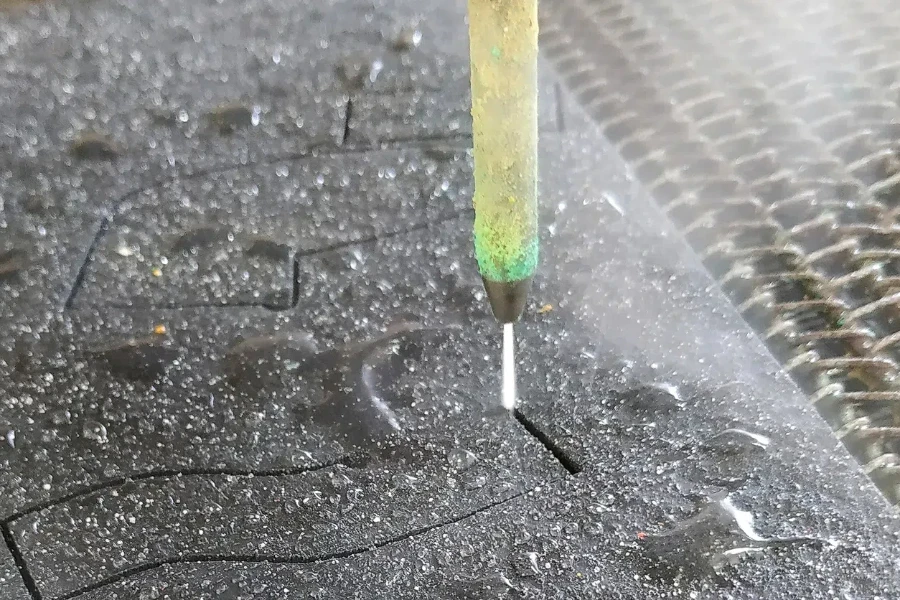
- Kemajuan Teknologi: Companies like Flow International have introduced waterjet cutters with integrated IoT capabilities, enabling real-time monitoring and predictive maintenance. This reduces downtime and enhances operational efficiency, crucial for industries with high production volumes.
- Growing Industrial Applications: The automotive industry extensively uses water pressure cutters for cutting metal parts with high precision. The increasing production of electric vehicles has driven the demand for precise cutting tools to manufacture battery components and lightweight materials.
- Pertimbangan Lingkungan: Water pressure cutters are preferred over traditional cutting methods as they do not produce hazardous fumes or waste. The shift towards sustainable manufacturing practices is evident in the increasing adoption of waterjet cutting technology, aligning with global environmental regulations.
- Ekonomi Dampak: The ongoing conflict between Russia and Ukraine has affected the supply chain for critical raw materials like nickel and aluminum, impacting the production costs of water pressure cutters. However, the market continues to grow due to the essential nature of these tools in high-precision manufacturing.
Key Factors When Selecting a Water Pressure Cutter
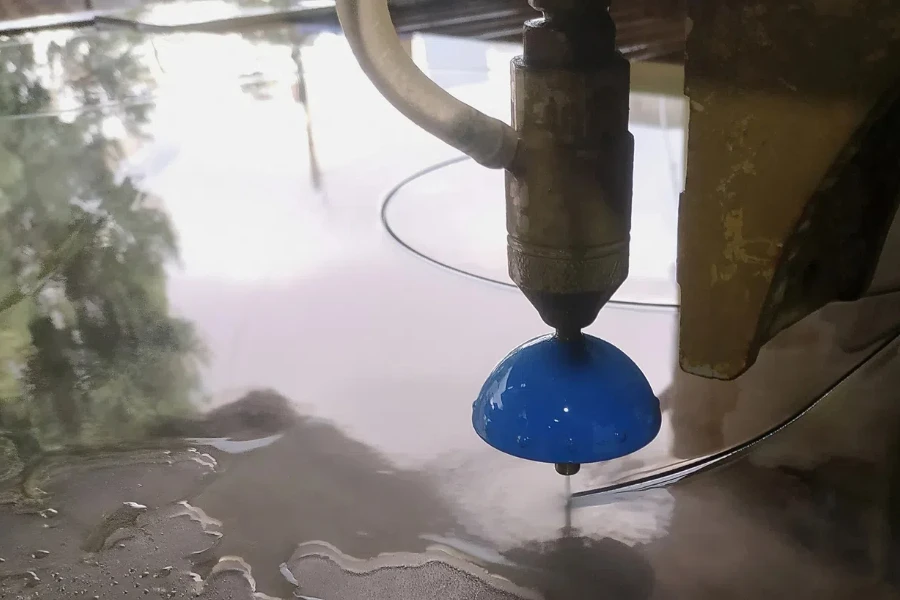
When choosing a water pressure cutter, several key factors must be considered to ensure optimal performance and compatibility with your specific application. Understanding these factors can help you make an informed decision, leading to improved efficiency and productivity in your operations.
Persyaratan Tekanan
The pressure rating of a water pressure cutter is crucial. These cutters typically operate within a range of 20,000 psi to 60,000 psi. Higher pressures are needed for cutting harder materials like metals and ceramics. For example, cutting through titanium or stainless steel might require pressures close to 60,000 psi, while softer materials like foam or rubber can be cut effectively at lower pressures around 20,000 psi.
Selecting a cutter with the right pressure rating ensures the machine can handle the material’s hardness and thickness without excessive wear or inefficiency. Maintaining consistent pressure is essential for achieving precise and clean cuts, minimizing the need for secondary finishing.
Nozzle and Orifice Specifications
The nozzle and orifice size directly impact the cutting performance and efficiency of a water pressure cutter. Orifice diameters typically range from 0.007 inches to 0.015 inches. Smaller orifices produce more concentrated and higher velocity water streams, ideal for intricate and detailed cuts. Conversely, larger orifices are suited for broader and faster cuts.
The material of the nozzle also plays a significant role. Tungsten carbide and diamond nozzles are preferred for their durability and wear resistance. Diamond nozzles can last up to 10 times longer than standard metal nozzles, reducing downtime and maintenance costs.
Pump Type and Efficiency
The type of pump used in a water pressure cutter affects both its performance and operational costs. Intensifier pumps and crankshaft-driven plunger pumps are the two primary types. Intensifier pumps can generate extremely high pressures but may require more frequent maintenance due to seal wear. Crankshaft-driven plunger pumps, on the other hand, offer more consistent pressure and are generally more energy-efficient, albeit with a lower maximum pressure rating.
Evaluating the energy consumption and maintenance requirements of the pump can help in selecting a cutter that balances performance with long-term operational costs. Businesses in regions with high electricity costs might prefer crankshaft-driven plunger pumps for their efficiency.
Abrasive Material Compatibility
For applications requiring abrasive water jet cutting, the compatibility of the cutter with various abrasive materials is crucial. Common abrasives include garnet, aluminum oxide, and silicon carbide. Garnet is widely used due to its balance of hardness and cost-effectiveness, making it suitable for cutting metals, stone, and composites.
The abrasive feed system should allow precise control of abrasive flow to optimize cutting speed and quality. Systems with adjustable flow rates can accommodate different materials and cutting requirements, enhancing versatility. A higher flow rate might be necessary for cutting thick steel, while a lower rate would suffice for delicate glass.
Sistem Kontrol dan Otomasi
Modern water pressure cutters often come with advanced control systems that enhance precision and ease of use. CNC (Computer Numerical Control) systems allow for intricate and repeatable cuts, which are essential in industries such as aerospace and automotive manufacturing.
Automation features such as programmable cutting paths and real-time monitoring can significantly reduce manual intervention, improving productivity and reducing errors. An automated system can adjust cutting parameters on the fly to compensate for material inconsistencies, ensuring consistent quality.
Considering these factors when selecting a water pressure cutter will help you choose a machine that meets your operational needs and enhances your manufacturing capabilities.
Material Compatibility and Performance
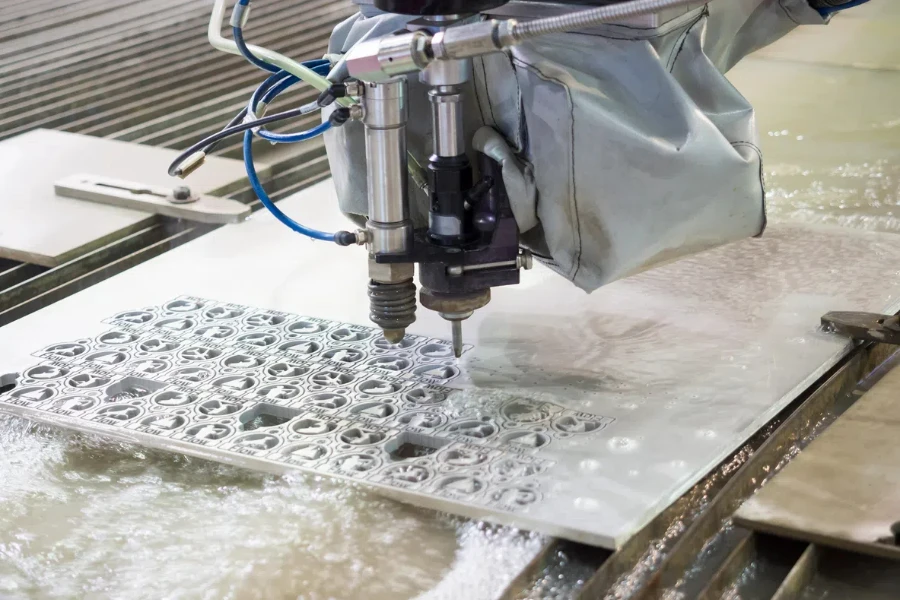
Material compatibility is a fundamental aspect to consider when selecting a water pressure cutter. Different materials require varying levels of pressure, abrasive types, and cutting speeds to achieve optimal results.
Logam dan Paduan
Water pressure cutters are highly effective for cutting metals and alloys, including steel, aluminum, and titanium. The high-pressure water stream, often combined with abrasives like garnet, can cut through thick metal sheets with precision. Cutting a 2-inch thick steel plate typically requires pressures around 55,000 psi and a consistent abrasive flow to ensure a clean cut.
The ability to cut without generating heat-affected zones (HAZ) is a significant advantage, as it preserves the material properties and reduces the need for secondary processes like grinding or heat treatment.
Composites and Laminates
Cutting composites and laminates, such as carbon fiber-reinforced polymers (CFRP), requires careful control of the cutting parameters to avoid delamination or fiber pull-out. Water pressure cutters excel in this area due to their precise and controlled cutting action. Aerospace manufacturers often use water jet cutting to fabricate complex shapes from composite panels, ensuring high accuracy and minimal material waste.
Programmable CNC systems allow for intricate cutting paths, essential for producing complex components used in high-performance applications.
Kaca dan Keramik
Water pressure cutters are also effective for cutting brittle materials like glass and ceramics. The fine water stream, often mixed with abrasives, can produce smooth edges without causing cracks or chips. Cutting a 1-inch thick ceramic tile might require a pressure of around 40,000 psi with a fine abrasive to achieve a clean edge.
The ability to cut these materials without generating heat is particularly beneficial, as it reduces the risk of thermal stress and subsequent cracking.
Plastik dan Karet
Cutting plastics and rubber materials with a water pressure cutter is straightforward due to the relatively low hardness of these materials. Pure water jets, without abrasives, are often sufficient for cutting soft materials like foam, rubber, and thin plastic sheets. Cutting a 0.5-inch thick rubber gasket typically requires pressures around 20,000 psi, ensuring a smooth and precise cut.
The versatility of water pressure cutters in handling a wide range of materials makes them indispensable tools in various industries, from automotive to electronics manufacturing.
Pertimbangan Pemeliharaan dan Operasional
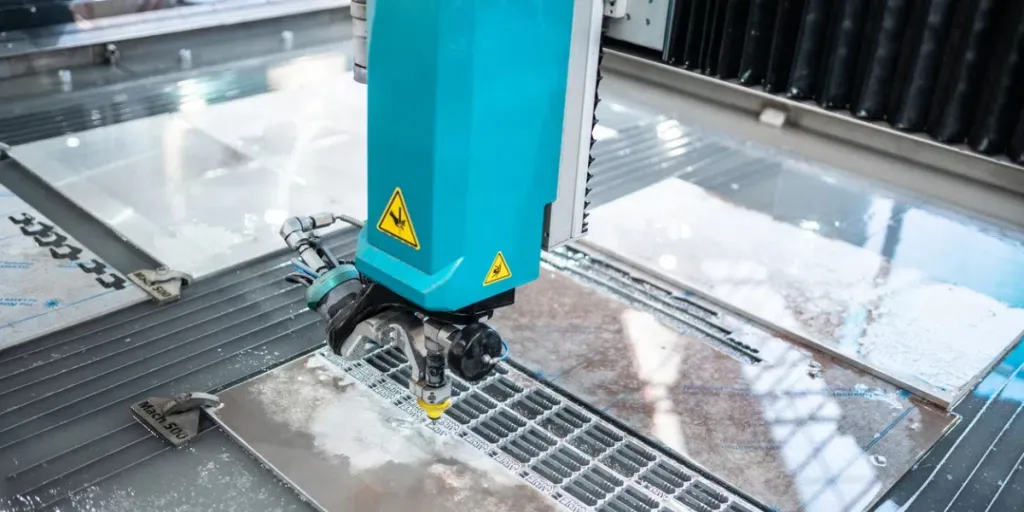
Regular maintenance and operational considerations are critical for ensuring the longevity and efficiency of water pressure cutters. Proper upkeep can prevent costly downtime and extend the machine’s lifespan.
Perawatan rutin
Routine maintenance tasks include checking and replacing worn nozzles, seals, and hoses. Nozzles made from tungsten carbide or diamond should be inspected regularly for wear and replaced as needed to maintain cutting accuracy. Similarly, seals and hoses should be checked for leaks or damage, as these components are subjected to high pressures and can degrade over time.
Lubricating moving parts and cleaning filters are also essential maintenance tasks that help prevent premature wear and ensure smooth operation. Regularly flushing the system with clean water can prevent abrasive buildup, which can cause blockages and reduce cutting efficiency.
Konsumsi Energi
Energy consumption is a significant operational consideration, especially for businesses looking to minimize operating costs. Crankshaft-driven plunger pumps are generally more energy-efficient compared to intensifier pumps, making them a preferred choice for operations with high electricity costs. Monitoring energy usage and optimizing cutting parameters can further reduce energy consumption and operational costs.
Pelatihan dan Keamanan
Proper training for operators is crucial to ensure safe and efficient use of water pressure cutters. Operators should be familiar with the machine’s controls, maintenance procedures, and safety protocols. Understanding how to safely handle high-pressure hoses and nozzles can prevent accidents and injuries.
Implementing safety measures such as protective guards, emergency shut-off switches, and regular safety inspections can further enhance workplace safety. Ensuring compliance with industry safety standards and regulations is also essential to avoid legal liabilities and ensure a safe working environment.
Future Trends in Water Pressure Cutting Technology
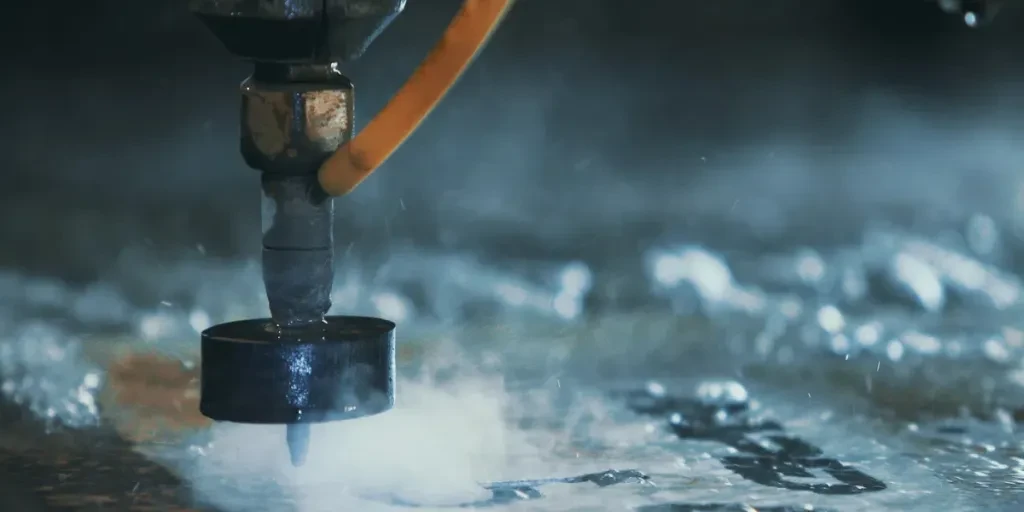
The future of water pressure cutting technology is marked by advancements in automation, precision, and sustainability. These trends are expected to enhance the capabilities and efficiency of water pressure cutters in various industries.
Otomasi dan Teknologi Cerdas
Automation and smart technology are set to revolutionize water pressure cutting by integrating advanced control systems and real-time monitoring. The use of AI-powered systems can optimize cutting paths, adjust parameters on-the-fly, and predict maintenance needs, reducing downtime and improving efficiency.
Smart sensors and IoT (Internet of Things) connectivity can provide real-time data on machine performance, allowing for predictive maintenance and remote monitoring. These advancements enable manufacturers to achieve higher precision and consistency in their cutting processes.
Praktik Berkelanjutan
Sustainability is becoming increasingly important in the manufacturing industry, and water pressure cutting technology is no exception. Innovations in water recycling and filtration systems can reduce water consumption and minimize environmental impact. Closed-loop water systems can filter and reuse water, significantly reducing the amount of water required for cutting operations.
The development of eco-friendly abrasives and the reduction of waste through precise cutting techniques also contribute to more sustainable manufacturing practices.
advanced Material
The ability to cut advanced materials such as carbon composites, ceramics, and high-strength alloys will continue to drive the demand for water pressure cutters. Research and development in new abrasive materials and cutting techniques will enhance the capabilities of water pressure cutters, enabling them to handle even more challenging materials with greater efficiency and precision.
Inovasi dalam Teknologi Pompa
Advancements in pump technology, such as the development of more efficient and durable pumps, will further improve the performance and reliability of water pressure cutters. New materials and designs for seals and pistons can extend the lifespan of pumps and reduce maintenance requirements.
These future trends in water pressure cutting technology promise to enhance the capabilities, efficiency, and sustainability of these machines, making them indispensable tools in modern manufacturing.
Final Thoughts
Selecting the right water pressure cutter involves considering various factors such as pressure requirements, nozzle specifications, pump efficiency, material compatibility, and maintenance needs. By understanding these key aspects, you can choose a cutter that meets your specific needs and enhances your operational efficiency.
Ensuring proper maintenance and staying informed about future trends in water pressure cutting technology will help you maximize the performance and longevity of your machine. As technology continues to evolve, water pressure cutters will become even more versatile and efficient, driving innovation and productivity in various industries.