Tinjauan tren terkini dan masalah rantai pasokan untuk sektor otomotif
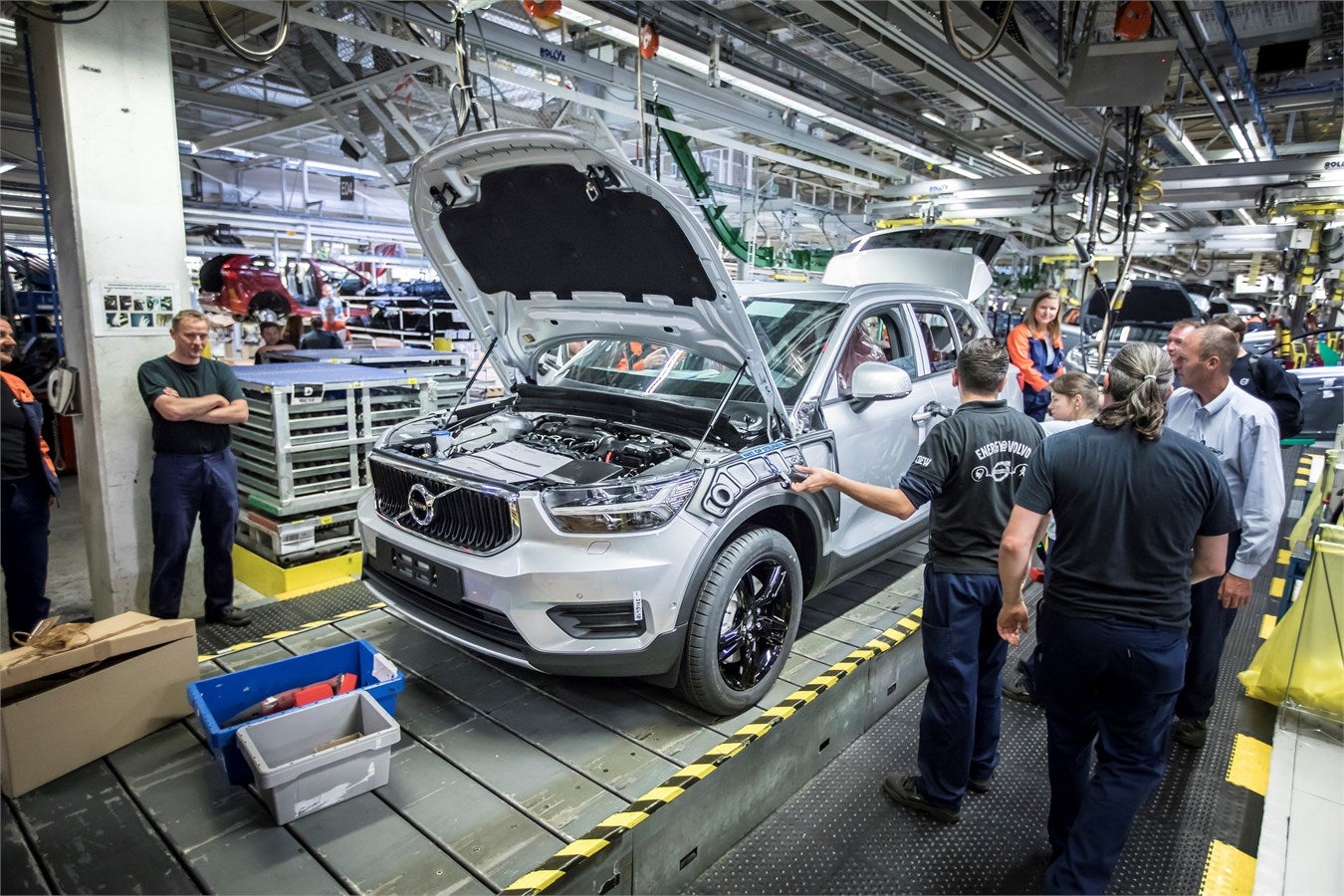
Kendaraan bermotor yang tidak lazim dapat memuat antara 15,000 dan 25,000 komponen – bergantung pada cara pengukurannya dan rekayasa desain sistem utamanya. Banyak sekali bahan yang bisa disatukan dan memberikan integritas pada produk akhir. Memang benar bahwa menyusun semua bagian tersebut dalam urutan yang benar bukanlah hal yang mudah. Setiap mobil yang ada merupakan penghargaan terhadap perencanaan proses, pengorganisasian, teknik produksi, dan logistik manufaktur. Dahulu kala, produsen kendaraan sangat terintegrasi secara vertikal, namun pendekatan tersebut memberi jalan bagi divestasi (ada yang ingat dari mana Visteon berasal dan jaringan perusahaan yang terdiri dari Grup Komponen Otomotif General Motors?) dan pemasok suku cadang spesialis yang dapat fokus pada pengembangan produk dan beroperasi secara lebih efisien pada skala yang lebih tinggi ke lebih dari satu pelanggan.
Integrator sistem Tier 1 yang besar memasok langsung ke produsen kendaraan, seringkali dari lokasi pemasok yang berlokasi dekat dengan fasilitas perakitan dan manufaktur kendaraan, namun ada beberapa tingkatan pemasok kecil di bawah tingkat atas – masing-masing memainkan peran penting dalam jalur panjang dari bahan mentah bahan menjadi produk jadi.
Pengadaan suku cadang komponen secara internasional telah menjadi mode operasi standar industri selama beberapa dekade karena OEM dan pemasok besar berupaya berbelanja di pasar global untuk suku cadang dan masukan material yang memenuhi ambang batas kualitas yang diperlukan dengan biaya terendah. Jarak (dan biaya) untuk transportasi dan pengaturan pergudangan juga merupakan bagian dari gambaran tersebut, namun efisiensi yang lebih tinggi dan kemajuan teknologi dalam pengiriman barang internasional telah mendukung pertumbuhan fenomenal dalam pengiriman suku cadang internasional.
Pertumbuhan industri otomotif Tiongkok selama dua dekade terakhir juga menjadi faktor besar dalam pengadaan komponen otomotif secara global, terutama suku cadang universal atau komoditas yang dijual berdasarkan harga pokok. Pemasok Tiongkok mendapat manfaat dari kontrak lokal besar yang meningkatkan skala ekonomi serta subsidi tersembunyi yang mengalir dari struktur kepemilikan kompleks yang melibatkan perusahaan induk OEM, perusahaan negara, dan kepemilikan saham yang terdiversifikasi. Pada awal tahun 2000-an, para pembuat kendaraan asal AS, khususnya, beralih ke sumber suku cadang yang lebih murah dari Asia, sehingga melemahkan beberapa perusahaan yang sudah lama berdiri di basis pemasok AS.
Di seluruh dunia, arus perdagangan internasional untuk produk otomotif – baik kendaraan jadi maupun suku cadang – kini sangat besar. Perkiraan disusun oleh GlobalData menunjukkan Jerman sebagai pemimpin internasional dalam hal pengiriman produk industri otomotif ke luar negeri. Ekspor tersebut tercermin dari impor dan jaringan barang setengah jadi yang digunakan sebagai masukan ke sistem komponen yang disempurnakan dan direkayasa pada berbagai tahap proses manufaktur dan dapat dikirim melintasi perbatasan internasional beberapa kali.
Karakteristik struktural penting lainnya pada rantai pasokan di industri otomotif adalah pentingnya filosofi manajemen rantai pasokan yang meminimalkan biaya inventaris dan meningkatkan efisiensi proses dan putaran komunikasi umpan balik untuk meningkatkan standar kualitas. Dikenal sebagai 'lean manufacturing', hal ini dimulai oleh Toyota dan esensinya dirangkum dalam istilah 'just-in-time' untuk menggambarkan metode dan prinsip lean supply. Munculnya teknologi digital dan terhubung yang menyatukan seluruh bagian proses manufaktur dan ritel semakin mendukung cara kerja ini selama sekitar satu dekade terakhir.
Di masa lalu, bencana alam dan dampaknya yang terkonsentrasi pada lokasi telah berdampak pada perusahaan otomotif dan menggambarkan rapuhnya rantai pasokan otomotif. Setelah gempa bumi dan tsunami tahun 2011 di Jepang, terdapat beberapa contoh gangguan yang penting. Sebuah produsen mobil premium global mengalami kendala dalam hal pasokan pigmen cat merah tunggal yang bersumber dari Jepang. Banjir di Thailand pada akhir tahun itu menyebabkan kekurangan pasokan layar LCD untuk menampilkan info kendaraan. OEM dan dealer harus menyesuaikan diri dengan kekurangan tersebut. Perang di Ukraina menggambarkan bagaimana peristiwa geopolitik yang tidak terduga juga dapat mengganggu rantai pasokan.
Tantangan semikonduktor
Semua perusahaan terkena dampak buruk secara langsung dari krisis kesehatan masyarakat pada tahun 2020 dan secara tidak langsung oleh dampak lainnya terhadap rantai pasokan global. Selain itu, pemulihan penjualan global pada tahun 2021 sangat terhambat oleh dampak krisis Covid yang tidak terduga pada tahun sebelumnya. Ketika pembuat kendaraan menutup pabriknya berdasarkan perintah pemerintah dan mengurangi pesanan suku cadang secara drastis pada tahun 2020, produsen semikonduktor menemukan bisnis alternatif di bidang-bidang seperti elektronik konsumen.
Ketika pabrik otomotif yang mulai pulih meningkatkan pesanan chip mereka pada kuartal pertama tahun 2021, masalah ketatnya pasokan dengan cepat menjadi nyata.
Kekurangan semikonduktor juga tidak akan mudah diatasi karena lamanya waktu penambahan kapasitas pengecoran chip di hulu. Hilangnya suku cadang yang penting bagi keselamatan atau dengan cara lain dianggap perlu untuk produk jadi berarti bahwa beberapa lini model terkena dampak yang lebih parah dibandingkan yang lain. Produsen kendaraan dapat mengubah bauran pasar dalam beberapa kasus, namun pepatah lama kembali menjadi kenyataan: Rantai pasokan hanya akan sama bagusnya/kuatnya dengan titik terlemahnya.
Di seluruh industri, metode dan proses pengadaan kini mendapat sorotan yang belum pernah terjadi sebelumnya.
Perlu dicatat juga bahwa ada elemen struktural yang berperan yang berarti beberapa tekanan pasokan semikonduktor kemungkinan akan tetap menjadi risiko di masa depan: konten elektronik canggih pada kendaraan meningkat karena pemasangan fitur-fitur teknologi yang lebih canggih yang terus meningkat. Hal ini membuat beberapa perusahaan beralih ke aliansi strategis dengan pembuat chip. Hal ini tidak hanya dapat membantu mengamankan pasokan mikroprosesor penting di masa depan, namun juga dapat memfasilitasi hubungan kolaboratif pengembangan produk masa depan yang bermanfaat dalam bidang komponen yang bernilai strategis.
Tekanan lain terhadap rantai pasokan datang dari sumber lain seperti kekurangan tenaga kerja yang tidak terduga dan harga pengiriman peti kemas internasional yang jauh lebih tinggi seiring dengan melonjaknya harga energi.
Perdebatan dual-versus multi-sumber
Kerapuhan dalam rantai pasokan otomotif disebabkan oleh banyaknya tingkatan, aliran pengadaan internasional, dan kecenderungan pengadaan tunggal untuk memaksimalkan skala ekonomi di seluruh program kendaraan global. Dalam banyak kasus, struktur tradisional ini juga tertanam dan tertanam dalam budaya mitra pilihan di seluruh tingkatan pemasok. Keuntungannya juga mencakup sistem bersama dan biaya logistik, dengan biaya yang tersebar di seluruh volume pada model dan sistem lain juga.
Teknologi juga berperan dalam mendorong sumber tunggal (single sourcing) karena perusahaan – termasuk perusahaan di tingkat 3 dan 4 – biasanya mampu memusatkan keahlian dan investasi di satu fasilitas yang didedikasikan untuk manufaktur bervolume tinggi. Masalah muncul ketika terjadi kesalahan yang mengacaukan rencana (kebakaran di pabrik mikroprosesor Renesas tahun lalu, misalnya).
Elektronik dan sensor adalah contoh komponen penting untuk sub-rakitan yang dapat berdampak besar pada sektor hilir dalam produksi kendaraan jika terjadi gangguan di bagian hulu. Menemukan pemasok alternatif dengan kapasitas cadangan dalam waktu yang sangat singkat merupakan sebuah tantangan besar.
Menyimpan sejumlah cadangan suku cadang dalam stok memerlukan biaya dan bertentangan dengan prinsip panduan lean manufacturing. Keputusan yang dapat diambil, tentu saja, adalah untuk menyerap atau menghapuskan biaya-biaya gangguan yang tidak biasa ketika hal tersebut terjadi – hal ini pada akhirnya bergantung pada kuantifikasi penilaian risiko.
Pengalaman beberapa tahun terakhir setidaknya menunjukkan bahwa perusahaan semakin mempertanyakan apakah sumber daya tunggal (singe-sourcing) masih diminati seperti dulu. Dunia yang dilanda risiko dan ketidakpastian yang lebih tinggi mungkin memerlukan pendekatan yang berbeda. Duplikasi dalam rantai pasokan, bahkan jika itu berarti hampir berbagi dengan pesaing, mungkin menawarkan solusi yang lebih baik – setidaknya untuk beberapa komponen – dibandingkan dengan pengadaan tunggal. Keamanan produk yang lebih baik akan menjadi manfaat dari dual sourcing. Seperti biasa, ini adalah pertanyaan tentang biaya keseluruhan.
Elektrifikasi dan pola rantai pasokan baru
Elektrifikasi menghadirkan tantangan baru bagi rantai pasokan otomotif di masa depan. Para OEM menghadapi ketidakpastian besar mengenai pasokan komponen-komponen baru dan penting – terutama baterai powertrain – yang sedang mereka coba selesaikan. Terdapat juga pertanyaan strategis mengenai tingkat integrasi vertikal yang diinginkan untuk memitigasi risiko di masa depan dan melakukan pengendalian terhadap aspek komersial pengaturan pasokan. Usaha patungan dengan spesialis baterai telah dibentuk. Komponen penting lainnya untuk kendaraan listrik – seperti motor, komponen sistem penggerak, inverter tegangan tinggi – juga akan mengalami peningkatan investasi seiring dengan pertimbangan rantai pasokan.
Strategi elektrifikasi yang ambisius akan menyebabkan permintaan sel baterai lithium-ion meroket. Produsen baterai di seluruh dunia berkomitmen terhadap strategi ekspansi bernilai miliaran dolar, dengan membuka 'gigafactories' baru untuk memasok sel ke produsen mobil.
Salah satu contoh penting kolaborasi mendalam OEM-Tier 1 di bidang ini adalah penandatanganan MoU antara Volkswagen dan Bosch. Kedua perusahaan berencana untuk memasok sistem produksi baterai terintegrasi, peningkatan di lokasi, dan dukungan pemeliharaan untuk produsen sel baterai dan sistem baterai. Mereka mengatakan mereka bertujuan untuk menjadi yang terdepan dalam hal biaya dan teknologi dalam teknologi baterai skala industri dan produksi massal 'baterai mutakhir dan berkelanjutan'.
Di Eropa saja, Grup Volkswagen berencana membangun enam pabrik sel pada tahun 2030 dan produsen lain juga mengambil langkah serupa untuk mengamankan pasokan sel dan baterai di masa depan. Wilayah ini diperkirakan akan memiliki total kapasitas paket baterai tahunan sekitar 700 gigawatt-jam pada tahun 2030.
Di sektor hulu, Toyota telah membentuk JV dengan Panasonic (Prime Planet Energy & Solutions – PPES) yang telah menandatangani perjanjian dengan raksasa pertambangan BHP untuk pasokan nikel sulfat di masa depan, bahan dasar nikel yang ada di katoda sebagian besar lithium-ion. sel baterai. Tesla juga telah menandatangani perjanjian serupa dengan BHP, yang menggambarkan bahwa bahan mentah juga banyak digunakan untuk keamanan pasokan di masa depan.
Kesepakatan ini menyoroti perlunya pemain otomotif untuk melihat lebih jauh rantai pasokan baterai, untuk memastikan mereka memiliki akses terhadap bahan mentah yang cukup untuk memasok pertumbuhan kapasitas besar yang dibutuhkan dalam sektor baterai lithium-ion untuk gelombang baru kendaraan listrik baterai yang diluncurkan pada tahun 2018. tahun-tahun yang akan datang. Daur ulang juga menjadi pertimbangan utama dalam banyak kesepakatan yang telah dilakukan.
Blockchain untuk visibilitas rantai pasokan
Semakin banyak perusahaan otomotif yang memanfaatkan teknologi blockchain untuk mendapatkan transparansi mengenai masalah rantai pasokan seperti emisi CO2 dan sumber kobalt untuk baterai (yang dapat menimbulkan pertanyaan etis seputar penambangan mineral berharga).
Konsep blockchain asli, seperti namanya, adalah rangkaian blok atau catatan yang diberi cap waktu (blok = informasi digital; rantai = database publik/komunitas). Blok menyimpan informasi tentang transaksi. Ketika sebuah blok menyimpan data baru – sebuah transaksi – data tersebut ditambahkan ke blockchain dan, setelah diverifikasi oleh jaringan komputer peer-to-peer, siapa pun dapat melihatnya (atau mungkin harus mendapat izin dari jaringan pribadi seperti rantai pasokan OEM – 'buku besar terdistribusi').
Namun, semua pihak hanya memiliki akses terhadap informasi yang mereka punya izin untuk melihatnya. Setiap komputer di jaringan blockchain memiliki salinan blockchainnya sendiri. Pada prinsipnya, idenya adalah untuk menciptakan sistem yang sangat transparan tanpa biaya transaksi antara kedua pihak yang membuat blok.
Kita dapat berharap untuk melihat lebih banyak perusahaan otomotif yang mengadopsi proses blockchain – terutama jenis buku besar terdistribusi (yaitu jaringan pribadi) – sebagai sarana untuk memitigasi risiko 'putusnya' rantai pasokan dan memahami kekuatan dan kelemahan di sepanjang rantai, tetapi juga sebagai cara untuk mengatasi masalah tersebut. cara untuk menunjukkan meningkatnya tuntutan kepatuhan di bidang peraturan seperti keberlanjutan.
Pelajaran dari Toyota
Toyota secara umum dipandang sebagai salah satu industri otomotif yang berkinerja lebih baik dalam hal manajemen rantai pasokan. Selain menjadi pencetus metode lean manufacturing yang kemudian menjadi praktik terbaik yang diadopsi oleh sebagian besar OEM dan pemasok utama, perusahaan ini juga telah menyempurnakan sistem dan prosesnya sesuai dengan perubahan kondisi terkait langkah-langkah mitigasi risiko. Selain itu, mereka telah bekerja sangat erat dengan para pemasoknya pada waktu-waktu tertentu dan untuk kepentingan tujuan sektor yang lebih luas dalam menghadapi keadaan darurat.
Setelah gempa bumi dan tsunami Kyoto tahun 2011, Toyota bekerja sama dengan pemasok di Jepang untuk menghasilkan database informasi rantai pasokan yang komprehensif untuk mendukung sektor manufaktur Jepang. Toyota juga memperkenalkan strategi multi-sourcing suku cadang penting yang berarti mengatur pasokan dari tiga sumber berbeda – namun pemasok utama akan memproduksi hampir dua pertiga pesanan untuk memastikan skala ekonomi. Banyaknya pemasok memang mengkompromikan skala ekonomi, namun hal ini juga berarti bahwa terdapat alternatif lain jika diperlukan.
Toyota juga memiliki sistem yang dikembangkan dengan baik untuk memantau jaringan pemasoknya yang luas dan sistem peringatan dini terhadap kekurangan pasokan. Memang benar, beberapa perusahaan beralih ke AI untuk menilai perkembangan rantai pasokan mereka – meskipun hal ini harus didasarkan pada kepemilikan database yang andal, ekstensif, dan terperinci.
Pilihan lain bagi perusahaan adalah dengan mulai mempertahankan stok darurat atau cadangan untuk komponen-komponen penting – khususnya yang dapat menyebabkan terhentinya jalur produksi. Sekali lagi, hal ini melibatkan biaya tambahan dalam penyimpanan atau pergudangan, namun yang menjadi pertanyaan adalah menentukan tingkat biaya atau 'premi asuransi' yang layak dibayar. Selain itu, ini bukan solusi permanen. Toyota mungkin telah menimbun beberapa semikonduktor, namun parahnya kekurangan chip global menyebabkan Toyota terpaksa mengurangi produksinya. Mungkin pembelajaran paling signifikan dari Toyota adalah perlunya peninjauan terus-menerus dan kemampuan beradaptasi terhadap perubahan keadaan dan ketidakpastian.
Sumber dari Hanya Otomatis
Penafian: Informasi yang diuraikan di atas disediakan oleh just-auto.com secara independen dari Chovm.com. Chovm.com tidak membuat pernyataan dan jaminan mengenai kualitas dan keandalan penjual dan produk.