Selecting the right hydraulic press is crucial for staying competitive in today’s fast-paced industrial landscape. In 2025, the market continues to evolve with innovations in automation and efficiency. This article provides an in-depth analysis of the key factors to consider, helping professional buyers make informed decisions that align with their operational goals and budget constraints.
Daftar Isi:
– Market Overview of Hydraulic Press Machines
– Detailed Market Analysis of Hydraulic Press Machines
– Strategic Insights and Future Trends
– Key Factors When Selecting a Hydraulic Press
– Advanced Technology Integration in Hydraulic Presses
– Maintenance and Longevity of Hydraulic Presses
– Pikiran Terakhir
Market Overview of Hydraulic Press Machines
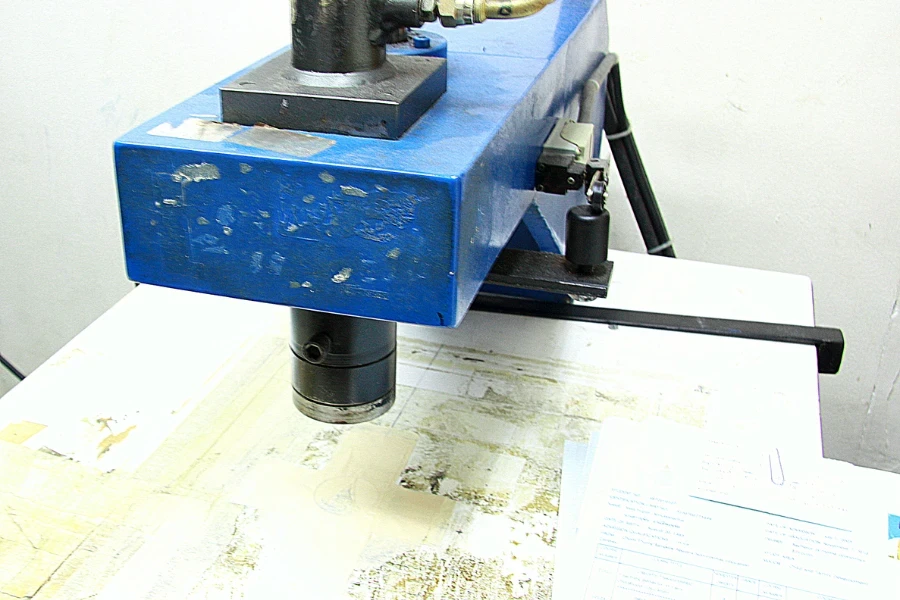
The global market for hydraulic press machines was valued at USD 13.9 billion in 2023 and is projected to reach USD 18.3 billion by 2030, growing at a compound annual growth rate (CAGR) of 4.0% from 2023 to 2030. This growth is driven by the increasing demand for fabricated metal products and advancements in automotive manufacturing. The market is expanding due to the rising adoption of automation across various industrial processes.
In the United States, the market was valued at USD 3.8 billion in 2023. Meanwhile, China is forecasted to grow at an impressive CAGR of 7.6%, reaching USD 3.9 billion by 2030. Other key regions, such as Japan, Canada, and Germany, also contribute significantly, reflecting a global trend towards enhanced manufacturing capabilities and technological adoption.
Segment-wise, the C-Frame Machines segment is expected to grow robustly, reaching USD 7.5 billion by 2030 with a CAGR of 4.7%. Similarly, the H-Frame Machines segment is projected to maintain a steady growth rate of 4.0% CAGR over the analysis period. These segments are crucial to the overall market dynamics due to their extensive application in various industrial processes.
Detailed Market Analysis of Hydraulic Press Machines
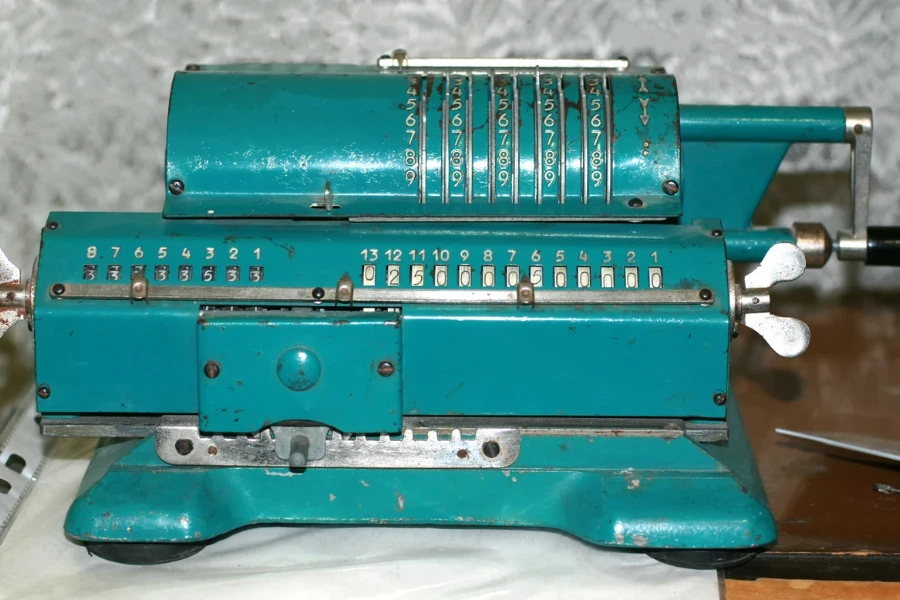
The hydraulic press machines market is characterized by key performance benchmarks that shape its growth. Technological innovations have significantly enhanced machine performance and energy efficiency, making hydraulic presses more appealing to a broader range of industries. The integration of advanced control and monitoring systems, driven by the trend towards smart manufacturing and Industry 4.0, is a notable development in this sector.
Major players such as Amino North America Corporation, Beckwood Press, and Betenbender Manufacturing Inc. continue to dominate the landscape. These companies leverage technological advancements and strategic partnerships to maintain their competitive edge. Economic influences, particularly the expansion of the automotive sector, have driven the demand for high-precision components, thereby increasing the need for advanced hydraulic press machines.
Consumer behavior is shifting towards automated and efficient forming processes. This shift is evident in the increasing adoption of hydraulic press machines in automotive, aerospace, and manufacturing sectors. Distribution channel preferences indicate a growing inclination towards direct sales and online platforms, facilitating easier access to advanced machinery. Recent innovations, such as eco-friendly hydraulic fluids and systems, address rising environmental concerns and regulatory standards.
Strategic Insights and Future Trends
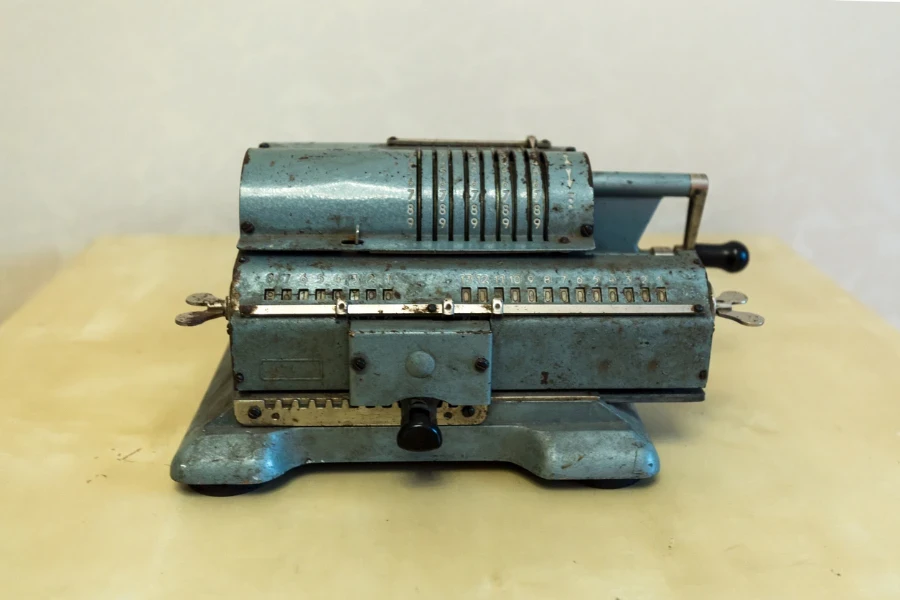
The hydraulic press machines market is poised to capitalize on several emerging opportunities. The continuous development of new applications and the need for efficient and reliable forming processes are expected to drive significant growth. The adoption of hydraulic press machines in renewable energy systems and advancements in hydraulic technology, such as electro-hydraulic systems, are shaping the future of the market.
Customer pain points, such as the need for high operational efficiency and reduced maintenance costs, are being addressed through technological innovations and enhanced machine capabilities. Brand positioning strategies that emphasize reliability, efficiency, and environmental compatibility are likely to resonate well with the target audience. Differentiation strategies focusing on advanced features and customization options will be crucial for companies aiming to capture niche markets and maintain a competitive edge.
Key Factors When Selecting a Hydraulic Press
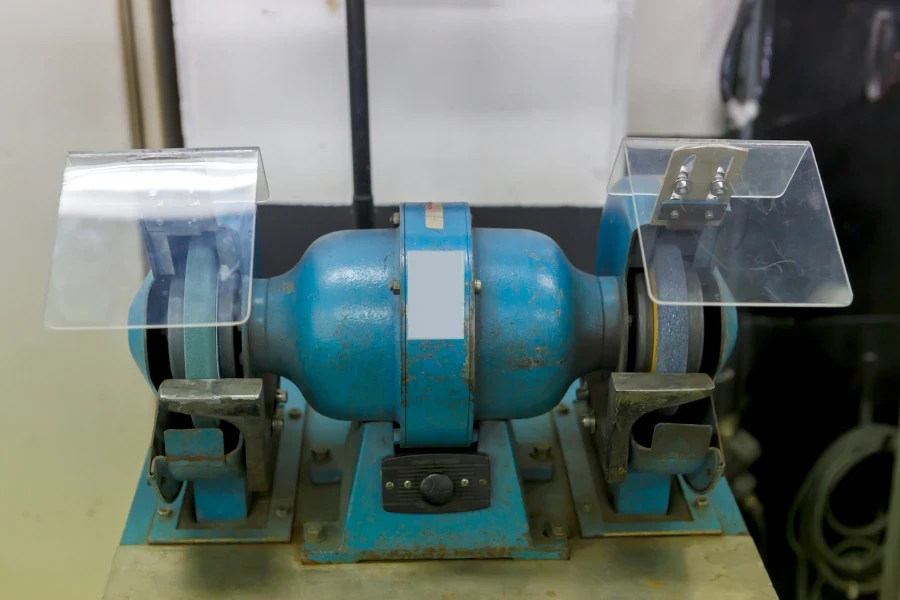
Types of Hydraulic Presses
Hydraulic presses come in various types, each designed for specific applications. Common types include C-frame presses, H-frame presses, and four-post presses. C-frame presses, with their open-front design, are suitable for operations requiring easy access to the workpiece. H-frame presses provide a more robust structure, ideal for heavy-duty applications. Four-post presses offer excellent precision and stability, making them suitable for applications requiring uniform pressure distribution.
Hydraulic presses can also be categorized based on their drive mechanism. Manual hydraulic presses, operated by hand, are suitable for low-volume production or applications requiring fine control. Pneumatic hydraulic presses use compressed air to generate force, making them ideal for medium-duty applications. Hydraulic presses, powered by a hydraulic pump, can generate very high forces, suitable for heavy-duty applications such as metal forming and assembly.
When selecting a hydraulic press, consider the specific requirements of the application. For instance, a C-frame press may be preferred for its accessibility, while an H-frame press might be chosen for its strength and rigidity. Additionally, the choice between manual, pneumatic, and hydraulic drives will depend on the required force and production volume.
Kinerja dan Fungsionalitas
The performance of a hydraulic press is determined by key parameters, including force, stroke length, and speed. The force generated by the press, typically measured in tons, determines its ability to deform or assemble materials. Stroke length, the distance the ram travels, is critical for applications requiring deep drawing or significant material deformation.
Speed affects production efficiency. Higher speeds can increase throughput but may require more robust components to handle the increased stress. It’s essential to balance speed with the specific requirements of the application to ensure optimal performance.
Functionality includes the press’s ability to perform various operations such as punching, forming, and assembly. Advanced hydraulic presses may feature programmable controls, allowing precise control over force, speed, and stroke length. This level of control can enhance the versatility and efficiency of the press, making it suitable for a wider range of applications.
Desain dan Kualitas Bangun
The design and build quality of a hydraulic press are critical factors influencing its durability and performance. The frame design, whether C-frame, H-frame, or four-post, affects the press’s rigidity and stability. A robust frame design can withstand higher forces and provide more consistent results, reducing the risk of deformation or misalignment.
Materials used in the construction of the press play a significant role in its durability. High-quality steel or cast iron frames offer excellent strength and resistance to wear, ensuring the press can handle demanding applications over extended periods. Additionally, components such as the ram, cylinder, and pump should be made from durable materials to ensure reliable performance.
Attention to details such as weld quality, machining tolerances, and surface finishes can further enhance the press’s build quality. High-quality construction ensures the press can operate smoothly and reliably, reducing downtime and maintenance costs.
Standar dan Sertifikasi Keamanan
Safety is a paramount concern when selecting a hydraulic press. Compliance with industry safety standards and certifications ensures the press meets stringent safety requirements, protecting operators and equipment. Common safety standards for hydraulic presses include BS EN 14673, which outlines safety requirements for hydraulic presses, and SAA AS 4024.3002, which covers safety for hydraulic power presses.
Hydraulic presses should be equipped with safety features such as emergency stop buttons, safety guards, and overload protection. These features help prevent accidents and ensure safe operation. Additionally, presses with programmable controls may include safety interlocks that prevent operation if safety conditions are not met.
Certifications from recognized organizations, such as ISO or CE, provide assurance that the press meets high-quality and safety standards. When selecting a hydraulic press, verify that it complies with relevant safety standards and has the necessary certifications.
Efisiensi Energi dan Dampak Lingkungan
Energy efficiency is an important consideration for modern hydraulic presses, as it affects both operating costs and environmental impact. Hydraulic presses can consume significant amounts of energy, so selecting an energy-efficient model can result in substantial savings. Features such as variable speed drives and energy recovery systems can enhance the press’s efficiency by reducing energy consumption during idle periods or recovering energy during deceleration.
The environmental impact of a hydraulic press is also influenced by factors such as noise levels, emissions, and the use of environmentally friendly materials and fluids. Presses with low-noise hydraulic pumps and energy-efficient motors can reduce the overall environmental footprint. Additionally, using biodegradable hydraulic fluids and ensuring proper disposal of waste materials can further minimize the press’s environmental impact.
Considering energy efficiency and environmental impact when selecting a hydraulic press not only aligns with sustainability goals but can also result in long-term cost savings and compliance with environmental regulations.
Advanced Technology Integration in Hydraulic Presses
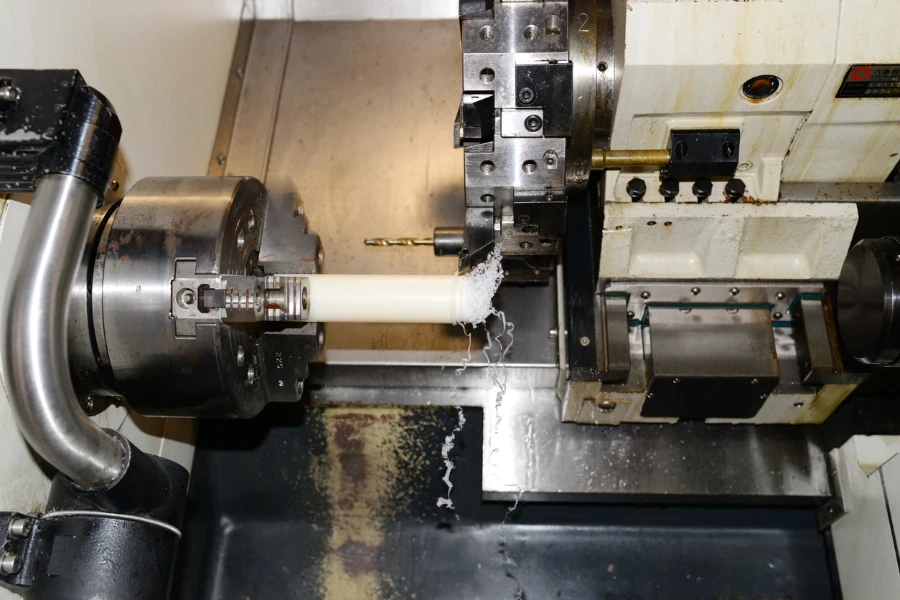
Pengontrol Logika yang Dapat Diprogram (PLC)
Modern hydraulic presses often incorporate Programmable Logic Controllers (PLCs) to enhance automation and precision. PLCs allow for the programming of complex operations, enabling the press to perform multiple tasks with high accuracy. For instance, a PLC can control the force, speed, and stroke length with precision, ensuring consistent results.
The integration of PLCs also facilitates better monitoring and diagnostics. Operators can receive real-time data on the press’s performance, including metrics such as cycle time, force applied, and energy consumption. This data can be used to optimize operations, perform predictive maintenance, and reduce downtime.
Furthermore, PLCs enable the integration of hydraulic presses into larger automated systems. For example, a hydraulic press equipped with a PLC can be part of an automated assembly line, where it communicates with other machines and systems to coordinate operations. This level of integration can significantly enhance productivity and efficiency.
Kontrol Numerik Komputer (CNC)
In addition to PLCs, some advanced hydraulic presses feature Computer Numerical Control (CNC) systems. CNC systems provide even greater control over the press’s operations, allowing for the programming of highly complex tasks. With CNC, operators can create detailed programs that specify the exact movements and operations of the press, ensuring high precision and repeatability.
CNC systems are particularly beneficial for applications requiring intricate shapes or tight tolerances. For example, in metal forming, a CNC-controlled hydraulic press can produce complex components with precise dimensions, reducing the need for secondary operations. Additionally, CNC systems can store multiple programs, allowing for quick changeovers between different tasks or products.
The use of CNC systems in hydraulic presses also enhances flexibility. Operators can easily modify programs to accommodate changes in product design or production requirements, making the press adaptable to a wide range of applications.
IoT and Industry 4.0 Integration
The integration of Internet of Things (IoT) technology and Industry 4.0 principles is transforming the capabilities of hydraulic presses. IoT-enabled hydraulic presses can connect to a network, allowing for remote monitoring and control. Operators can access the press’s data from anywhere, using devices such as smartphones or tablets.
This connectivity facilitates predictive maintenance, as IoT sensors can monitor the condition of critical components and alert operators to potential issues before they lead to downtime. For example, sensors can detect changes in hydraulic fluid pressure or temperature, indicating the need for maintenance. This proactive approach can reduce unplanned downtime and extend the press’s lifespan.
Industry 4.0 integration also enables the use of data analytics and machine learning. By analyzing data from the press, operators can identify patterns and trends that can be used to optimize operations. For instance, data analysis can reveal opportunities to improve cycle times, reduce energy consumption, or enhance product quality.
Fitur Keamanan Lanjutan
Safety is a top priority in modern hydraulic presses, and advanced technology is enhancing safety measures. In addition to traditional safety features such as emergency stops and safety guards, modern presses may include advanced safety systems such as light curtains and laser scanners. These systems create a protective barrier around the press, stopping its operation if an object or person enters the danger zone.
Advanced presses may also feature safety interlocks that prevent the press from operating unless certain conditions are met. For example, the press may require confirmation that safety guards are in place and that the workpiece is properly positioned before it can start.
The use of advanced safety features not only protects operators but also ensures compliance with stringent safety regulations. This is particularly important in industries with high safety standards, such as automotive and aerospace manufacturing.
Maintenance and Longevity of Hydraulic Presses
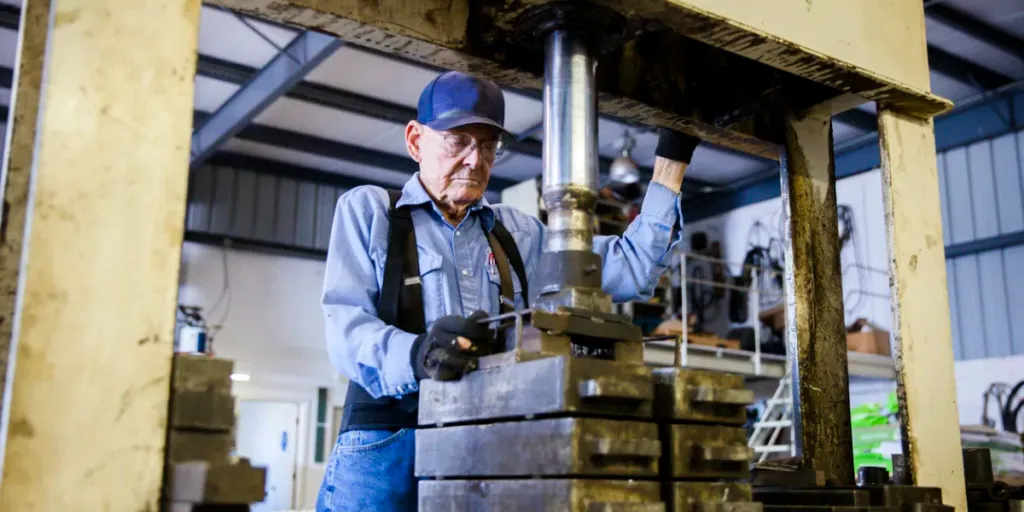
Preventive Maintenance
Preventive maintenance is essential for ensuring the longevity and reliable operation of hydraulic presses. Regular maintenance tasks include checking and replacing hydraulic fluid, inspecting seals and hoses for wear, and ensuring that all components are properly lubricated. By performing these tasks regularly, operators can prevent common issues such as leaks, pressure drops, and component failure.
It’s also important to follow the manufacturer’s recommended maintenance schedule. This schedule is designed to address the specific needs of the press and ensure that all critical components are inspected and maintained at appropriate intervals. Adhering to the maintenance schedule can extend the press’s lifespan and reduce the risk of costly repairs.
In addition to routine maintenance, operators should be trained to recognize signs of potential issues. For example, unusual noises, vibrations, or changes in performance can indicate underlying problems that need to be addressed. Promptly addressing these issues can prevent more serious damage and reduce downtime.
Suku Cadang dan Peningkatan
Having access to spare parts is crucial for maintaining hydraulic presses. Common spare parts include seals, hoses, valves, and hydraulic fluid. Keeping these parts in stock ensures that operators can quickly address issues and reduce downtime. It’s also important to source spare parts from reputable suppliers to ensure compatibility and quality.
Upgrades can also enhance the performance and longevity of hydraulic presses. For example, upgrading to more efficient hydraulic pumps or adding advanced control systems can improve the press’s performance and reduce energy consumption. Additionally, upgrading safety features can ensure compliance with the latest safety standards and protect operators.
When considering upgrades, evaluate the potential benefits and costs. Upgrades should align with the specific needs and goals of the operation, and the return on investment should be carefully considered.
Resale Value and Lifespan
The resale value of a hydraulic press is influenced by several factors, including its condition, age, and the availability of spare parts. Regular maintenance and upgrades can enhance the press’s resale value by ensuring it remains in good condition and meets current performance standards. Additionally, having a well-documented maintenance history can provide potential buyers with confidence in the press’s reliability.
The lifespan of a hydraulic press is determined by factors such as build quality, usage, and maintenance. High-quality presses with robust construction and durable components can operate reliably for many years. Regular maintenance and timely repairs can further extend the press’s lifespan, ensuring it continues to perform effectively.
When selecting a hydraulic press, consider its potential lifespan and resale value. Investing in a high-quality press with a strong maintenance and support network can provide long-term value and reduce the total cost of ownership.
Final Thoughts
Selecting the right hydraulic press involves considering various factors, including the type of press, performance and functionality, design and build quality, safety standards, and energy efficiency. Advanced technology integration, such as PLCs, CNC systems, and IoT connectivity, can enhance the press’s capabilities and performance. Regular maintenance, access to spare parts, and potential upgrades are essential for ensuring the longevity and reliability of the press. By carefully evaluating these factors, operators can choose a hydraulic press that meets their specific needs and provides long-term value.