In 2025, the spur gear market continues to thrive, driven by innovations and increasing demand in various sectors. This article provides an in-depth analysis of key selection factors for professional buyers, ensuring the best choices for business success.
Sommario:
-Spur Gear Market Overview
-Detailed Introduction and Analysis of the Spur Gear Market
-Key Factors When Selecting Spur Gears
-Applications of Spur Gears in Modern Machinery
-Advances in Spur Gear Manufacturing Technologies
-Environmental Considerations and Sustainability
-Future Trends in Spur Gear Development
-Considerazioni finali
Spur Gear Market Overview
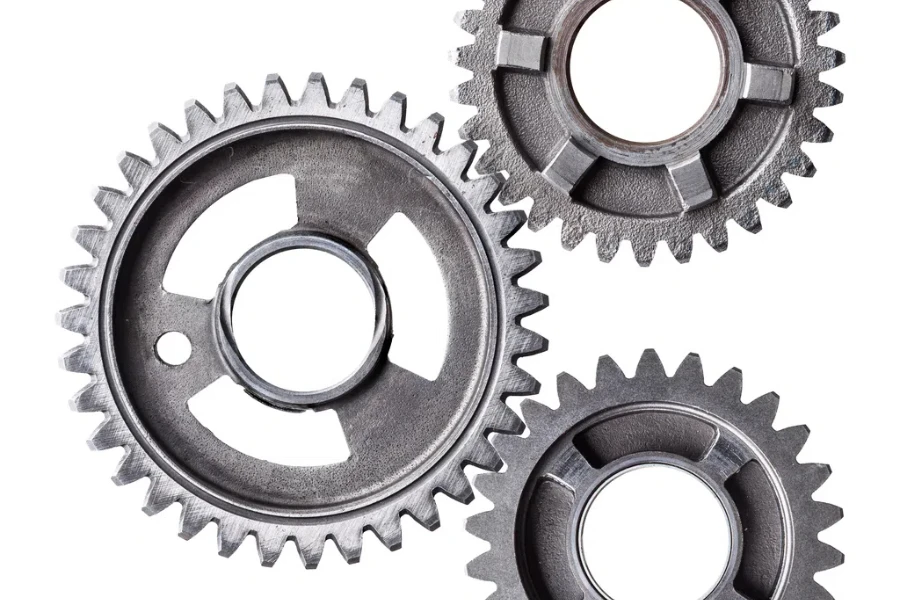
The global spur gear market has shown robust growth in recent years and is set to continue this trend. In 2024, the market was valued at around USD 6.5 billion and is projected to reach USD 8.2 billion by 2030, with a compound annual growth rate (CAGR) of 4.1%. Spur gears are in demand across various industries such as automotive, aerospace, industrial machinery, and robotics. The automotive sector holds the largest market share, with spur gears commonly used in transmission systems and differential systems.
The Asia-Pacific region leads the global spur gear market, accounting for over 40% of the share. This dominance is due to the growing automotive and industrial sectors in countries like China, Japan, and India. North America and Europe also have significant market shares, driven by advancements in manufacturing technologies and the presence of major automotive and industrial machinery manufacturers.
Detailed Introduction and Analysis of the Spur Gear Market
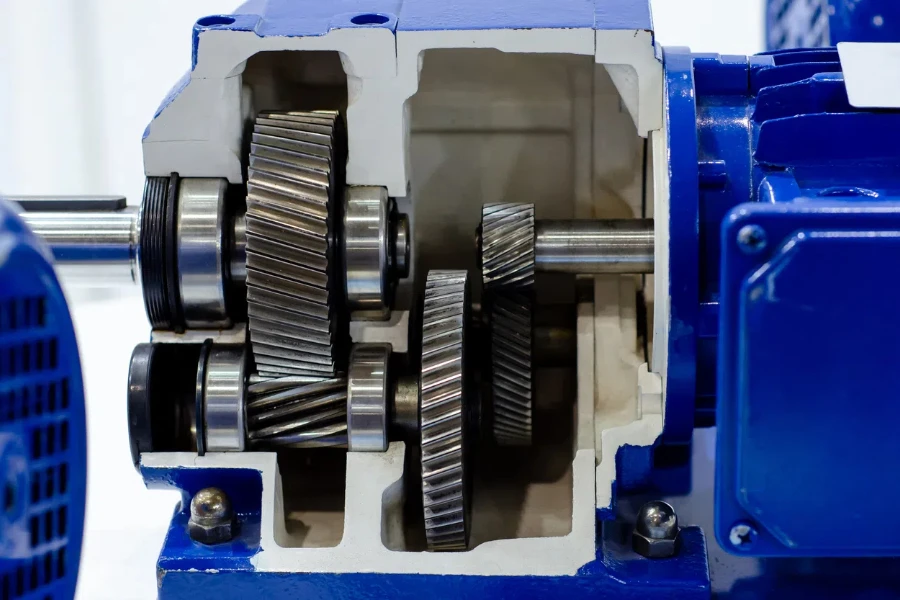
Spur gears are the simplest type of gear, characterized by their straight teeth parallel to the gear’s axis. They transmit motion and power between parallel shafts, known for their efficiency, reliability, and ability to handle high torque loads. These features make them essential in automotive transmissions, industrial machinery, and robotics.
Key performance benchmarks for spur gears include high load-carrying capacity, precision, durability, and minimal noise. Market dynamics are influenced by the rising demand for high-performance gears in automotive and industrial applications, advancements in gear manufacturing, and the growing use of automation and robotics.
Recent innovations in spur gear design and manufacturing have improved performance. Advanced materials like carbon fiber composites and high-strength alloys enhance strength and durability. Digital technologies such as computer-aided design (CAD) and computer-aided manufacturing (CAM) have increased precision and efficiency in gear production.
The market is segmented by material type, application, and region. Metallic spur gears, made from steel, aluminum, and brass, dominate due to their strength and durability. Non-metallic gears, made from polycarbonate and nylon, are gaining popularity in applications where weight reduction and noise minimization are crucial.
Customer challenges include the high cost of advanced materials and technologies, as well as the need for regular maintenance and lubrication. Manufacturers are developing cost-effective solutions and enhancing durability and reliability through innovative design and material selection.
Brand positioning strategies in the spur gear market focus on quality, performance, and reliability. Leading manufacturers invest in research and development to create advanced gear solutions that meet evolving industry needs. Differentiation strategies include customized gear solutions, comprehensive after-sales support, and leveraging digital technologies to enhance performance and customer satisfaction.
Niche markets for spur gears include aerospace and robotics, where precision and reliability are critical. In these sectors, spur gears are used in actuators, control mechanisms, and robotic arms. The increasing adoption of automation and robotics in various industries is expected to drive the demand for high-performance spur gears in the coming years.
Key Factors When Selecting Spur Gears
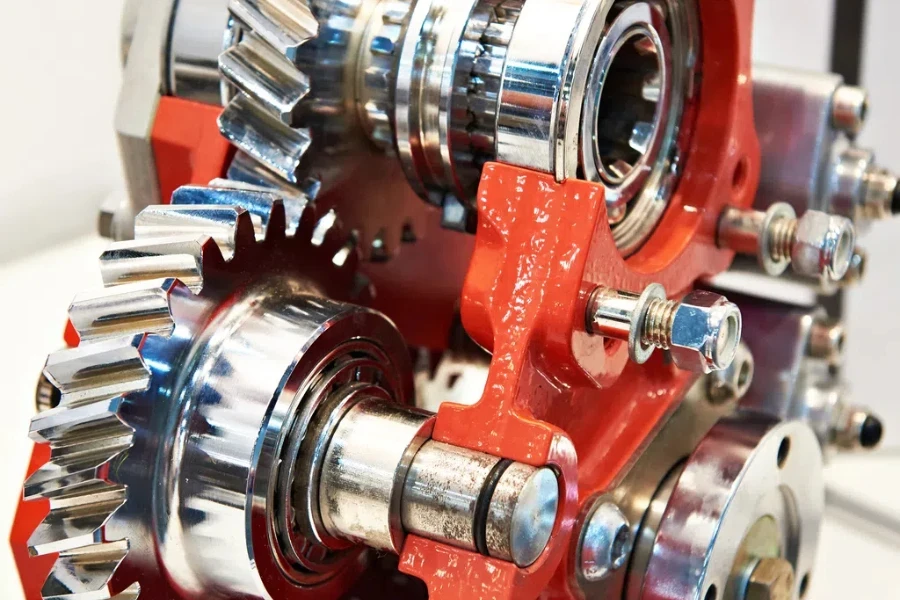
Material Composition
Material composition is crucial in spur gear selection, impacting durability, performance, and cost. Common materials include cast iron, alloy steel, and plastics. Cast iron is durable and easy to manufacture, making it suitable for heavy-duty uses. Alloy steel offers superior durability and corrosion resistance, ideal for environments prone to wear. Plastics like acetal and nylon are lightweight and corrosion-resistant, perfect for quieter operations and lower inertia.
Gear Dimensions and Specifications
The dimensions of a spur gear directly affect its performance. Key specifications include diametral pitch (DP), circular pitch (CP), and module (M). Diametral pitch denotes the number of teeth per inch of the pitch diameter, with a higher DP indicating finer tooth spacing. Circular pitch measures the distance between adjacent teeth, while the module is a metric measurement of gear size. Accurate dimensions ensure proper meshing and efficient power transmission.
Pressure Angle and Tooth Profile
The pressure angle, typically 14.5° or 20°, influences the gear’s load distribution and noise levels. A higher pressure angle results in stronger teeth capable of handling higher loads but may increase noise. The tooth profile, including involute and cycloidal shapes, determines smoothness and efficiency. Involute profiles are common due to their consistent velocity ratio and ease of manufacture.
Mounting and Shaft Alignment
Proper mounting and shaft alignment are essential for reliable spur gear operation. Mounting options include hub, keyway, set screw, and split designs. The gear center, bore diameter, and shaft diameter must be compatible for secure attachment. Misalignment can lead to increased wear, noise, and reduced efficiency, necessitating precise alignment during installation.
Lubrificazione e Manutenzione
Lubrication is vital for reducing friction, wear, and heat generation in spur gears. The type of lubricant and lubrication method, such as oil baths or grease, depends on the operating environment and load conditions. Regular maintenance, including inspection and re-lubrication, extends the gear’s lifespan and ensures optimal performance. In corrosive or high-temperature environments, specialized lubricants may be required to maintain gear integrity.
Applications of Spur Gears in Modern Machinery
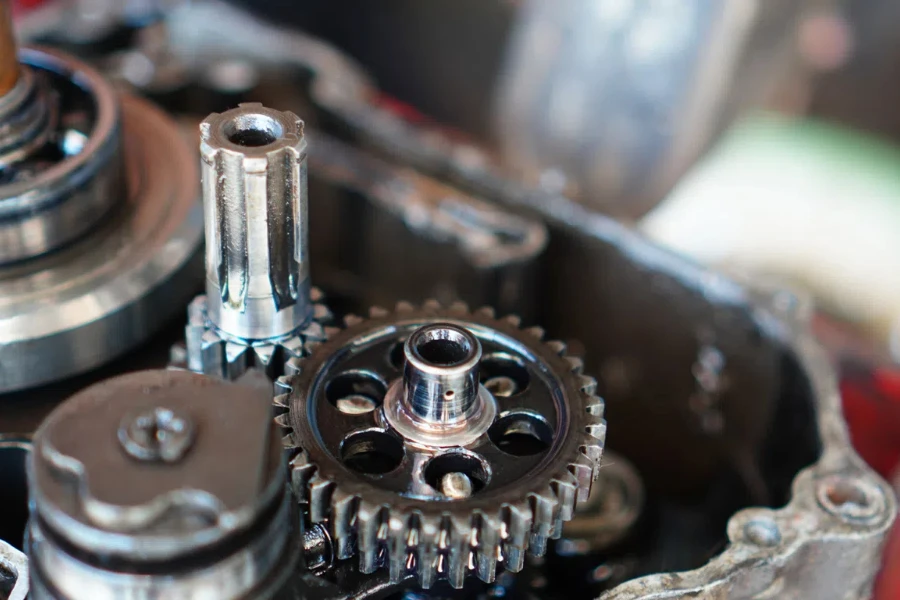
Spur gears are widely used across various industries due to their simplicity and efficiency. In automotive applications, they are integral to transmission systems, providing reliable power transfer between parallel shafts. Industrial machinery, such as conveyor systems and packaging equipment, utilizes spur gears for their ability to handle high loads and precise positioning. Additionally, robotics and automation systems employ spur gears for accurate motion control and speed reduction.
Advances in Spur Gear Manufacturing Technologies
Advancements in manufacturing technologies have significantly improved the quality and performance of spur gears. Computer-aided design (CAD) and computer-aided manufacturing (CAM) enable precise gear modeling and production, reducing errors and enhancing efficiency. Additive manufacturing, or 3D printing, allows for rapid prototyping and custom gear designs, catering to specific application requirements. Advanced materials, including composites and high-performance plastics, offer improved strength and durability while reducing weight.
Considerazioni ambientali e sostenibilità
Sustainability is becoming increasingly important in gear manufacturing. The use of eco-friendly materials and lubricants, along with energy-efficient production processes, reduces the environmental impact of gear production. Recycling and reconditioning of gears extend their lifecycle, minimizing waste. Manufacturers are also exploring biodegradable lubricants and materials to further enhance the sustainability of gear systems.
Future Trends in Spur Gear Development
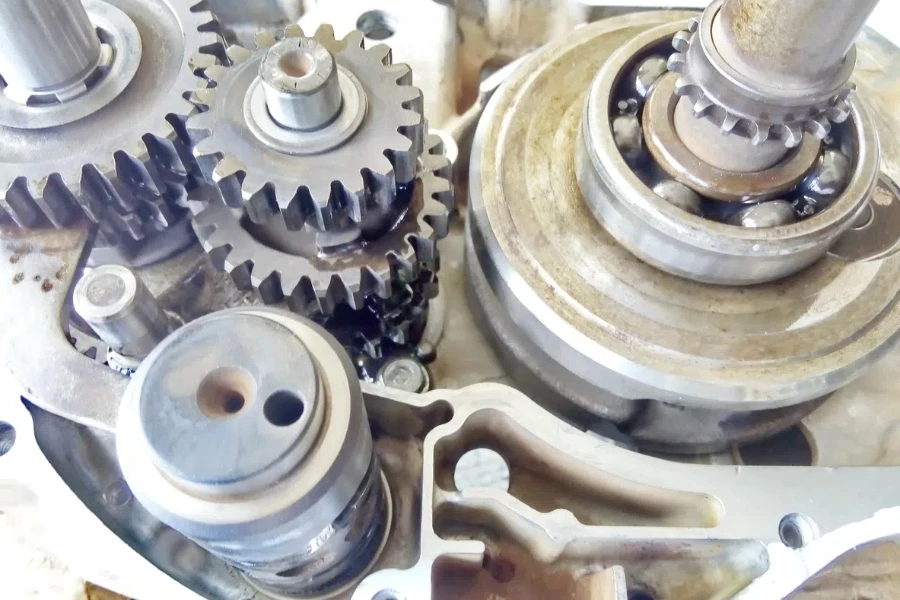
The future of spur gear development is likely to focus on enhancing efficiency, durability, and customization. Innovations in material science, such as the development of nanomaterials and advanced composites, will lead to stronger and lighter gears. Smart manufacturing technologies, including the Internet of Things (IoT) and Industry 4.0, will enable real-time monitoring and predictive maintenance, improving gear reliability and reducing downtime. Customization through advanced manufacturing techniques will allow for gears tailored to specific applications, optimizing performance and efficiency.
Considerazioni finali
In summary, selecting the right spur gear involves considering factors such as material composition, dimensions, pressure angle, mounting, and lubrication. Understanding the specific requirements of your application and staying informed about the latest advancements in gear technology will ensure optimal performance and longevity. By prioritizing these key aspects, you can make informed decisions that enhance the efficiency and reliability of your machinery systems.