Con l’introduzione di un veicolo di trasporto autonomo presso il suo stabilimento di presse, lo stabilimento del BMW Group di Regensburg sta facendo passi avanti verso la digitalizzazione e l’automazione dei suoi processi di produzione, compiendo così un ulteriore passo verso la BMW iFACTORY digitale e connessa in modo intelligente.
Il camion con piattaforma senza conducente, dotato di propulsione elettrica, gestirà in modo autonomo il trasporto interno di utensili di pressatura e pezzi grezzi in acciaio per le linee di pressatura, con un carico utile fino a 55 tonnellate. Utilizzando la tecnologia dei sensori, il sistema di trasporto si muove in modo preciso e completamente autonomo attraverso gli impianti di produzione dello stabilimento di Ratisbona ad una velocità di quattro chilometri all'ora. BMW afferma che attualmente la soluzione non esiste in nessun'altra parte del mondo.
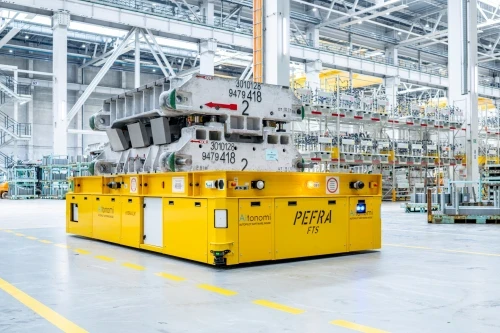
Vediamo un enorme potenziale nell’implementazione di soluzioni logistiche autonome. Il veicolo elettrico a zero emissioni ci consentirà di rendere i processi produttivi presso il nostro stabilimento di presse ancora più efficienti e flessibili, oltre a ridurre i viaggi di trasporto e i tempi di consegna. Ciò non solo aumenterà la produttività, ma farà anche risparmiare energia e migliorerà la sicurezza sul lavoro per i nostri dipendenti.
—Tobias Müller, responsabile della manutenzione dell'impianto di stampa presso lo stabilimento del BMW Group a Ratisbona
Il nuovo veicolo da trasporto senza conducente utilizza l'innovativa tecnologia LiDAR (Light Detection And Ranging) del produttore Pefra. Insieme a telecamere e sensori radar, monitorano l'ambiente circostante, aiutando nell'orientamento, nel rilevamento degli ostacoli e nella misurazione della distanza, offrendo maggiore sicurezza ed efficienza in un ambiente complesso, sia su strade trafficate che in ambienti industriali automatizzati, come nella stampa del BMW Group stabilimento di Ratisbona. Il processo LiDAR 3D prevede la scansione dell’ambiente circostante, utilizzando numerose misurazioni individuali della distanza ottica che vengono poi combinate per generare un grafico a dispersione 3D dell’ambiente catturato dal sensore LiDAR.
L'impianto di pressatura dello stabilimento del BMW Group a Ratisbona lavora ogni giorno lavorativo circa 1,100 tonnellate di acciaio, equivalenti a una produzione giornaliera di 131,000 pezzi stampati. L'ambito di produzione comprende 113 diversi componenti della carrozzeria. Oltre alle parti strutturali e di rinforzo, l'impianto di pressatura forma anche grandi sezioni di pannelli esterni, come telai laterali, rivestimenti esterni di porte e cofani, da lamiere d'acciaio che possono misurare fino a 4.5 metri di lunghezza.
I rotoli di acciaio lavorati possono pesare fino a 33 tonnellate. La più potente delle quattro linee di stampa del reparto stampa di Ratisbona sfrutta la tecnologia servo ad alta velocità, rendendola una delle macchine da stampa più veloci al mondo, con una forza di stampa di 9,000 tonnellate, equivalente al peso della Torre Eiffel. La pressa raggiunge una velocità fino a 23 colpi al minuto. I componenti della carrozzeria prodotti nello stabilimento di pressatura vengono poi assemblati nelle carrozzerie dei veicoli presso la vicina carrozzeria del BMW Group Plant di Ratisbona.
Ogni anno nel reparto presse di Ratisbona vengono prodotte circa 80,000 tonnellate di scarti, che vengono poi riciclate in un ciclo chiuso. Il primo passaggio prevede che gli scarti vengano lavorati da una pressa di riciclaggio, che li modella in cubi di acciaio di 40 x 40 centimetri e del peso di 220 chilogrammi ciascuno. Questi vengono poi rispediti al fornitore di acciaio, dove vengono trasformati in quello che è noto come acciaio secondario.
L'utilizzo di acciaio secondario nello stabilimento di presse del BMW Group a Ratisbona genera due tonnellate di CO in meno2 per tonnellata di acciaio, rispetto alla produzione di acciaio primario. Ciò riduce la CO2 della pianta2 impronta di circa 160,000 tonnellate all’anno. Per proteggere i dipendenti, i residenti e l'ambiente dalle emissioni di rumore e dalle vibrazioni, gli impianti di produzione e riciclaggio dello stabilimento di Ratisbona sono dotati di isolamento acustico. Inoltre, tutti i sistemi di produzione funzionano con vibrazioni minime.
Fonte da Congresso Green Car
Dichiarazione di non responsabilità: le informazioni sopra riportate sono fornite da greencarcongress.com indipendentemente da Chovm.com. Chovm.com non rilascia alcuna dichiarazione o garanzia in merito alla qualità e all'affidabilità del venditore e dei prodotti.