Le recenti innovazioni nei tagliatori al plasma CNC hanno rivoluzionato l'industria manifatturiera, stimolando la domanda e la crescita del mercato. Questo articolo fornisce un'analisi approfondita del mercato dei tagliatori al plasma CNC, evidenziando fattori critici quali tipo di materiale, requisiti di potenza, facilità d'uso, standard di sicurezza e considerazioni sui costi. Gli acquirenti professionisti troveranno spunti preziosi per prendere decisioni di acquisto consapevoli e migliorare l'efficienza operativa.
Sommario:
- Panoramica del mercato dei tagliatori al plasma CNC
-Introduzione dettagliata e analisi del mercato del taglio al plasma CNC
-Fattori chiave nella scelta di un taglierino al plasma CNC
-Progressi tecnologici nei tagliatori al plasma CNC
-Considerazioni sui costi e budget
- Durevole e affidabile: durata della taglierina al plasma CNC
-Riepilogo
Panoramica del mercato dei tagliatori al plasma CNC
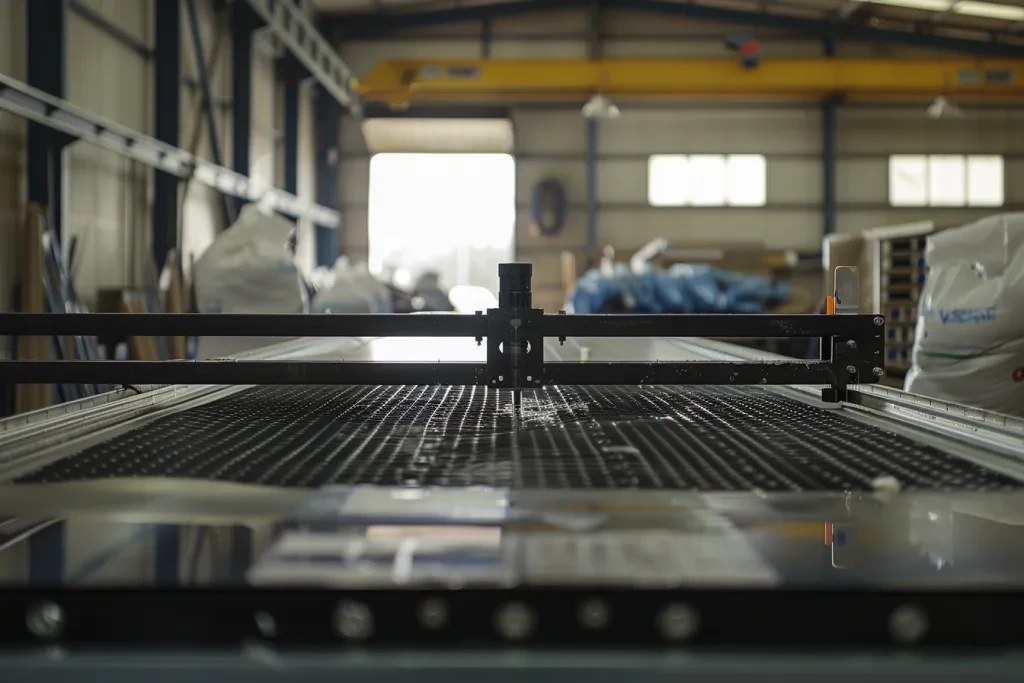
Il mercato globale del taglio al plasma CNC ha mostrato una crescita significativa ed è pronto per un'ulteriore espansione. Nel 2023, le dimensioni del mercato hanno raggiunto 1.4 miliardi di $ e si prevede che saliranno a 2.1 miliardi di $ entro il 2032, crescendo a un tasso di crescita annuale composto (CAGR) del 4.61%. Questa crescita è guidata dalla crescente domanda di applicazioni di taglio dei metalli in vari settori, tra cui aerospaziale, automobilistico e delle costruzioni. La regione Asia-Pacifico è emersa come il mercato più grande, attribuito alla rapida industrializzazione e allo sviluppo delle infrastrutture in paesi come Cina, Giappone e India.
La segmentazione del prodotto all'interno del mercato delle taglierine al plasma CNC include macchine a flusso singolo e a flusso doppio, con le macchine a flusso singolo che rappresentano la quota di mercato maggiore. Le taglierine al plasma CNC meccanizzate dominano il mercato grazie alla loro efficienza e precisione nei processi di produzione su larga scala. In termini di configurazione, le taglierine 2D hanno la più alta penetrazione di mercato, in gran parte a causa del loro ampio utilizzo nelle operazioni di taglio dei metalli standard.
Introduzione dettagliata e analisi del mercato del taglio al plasma CNC
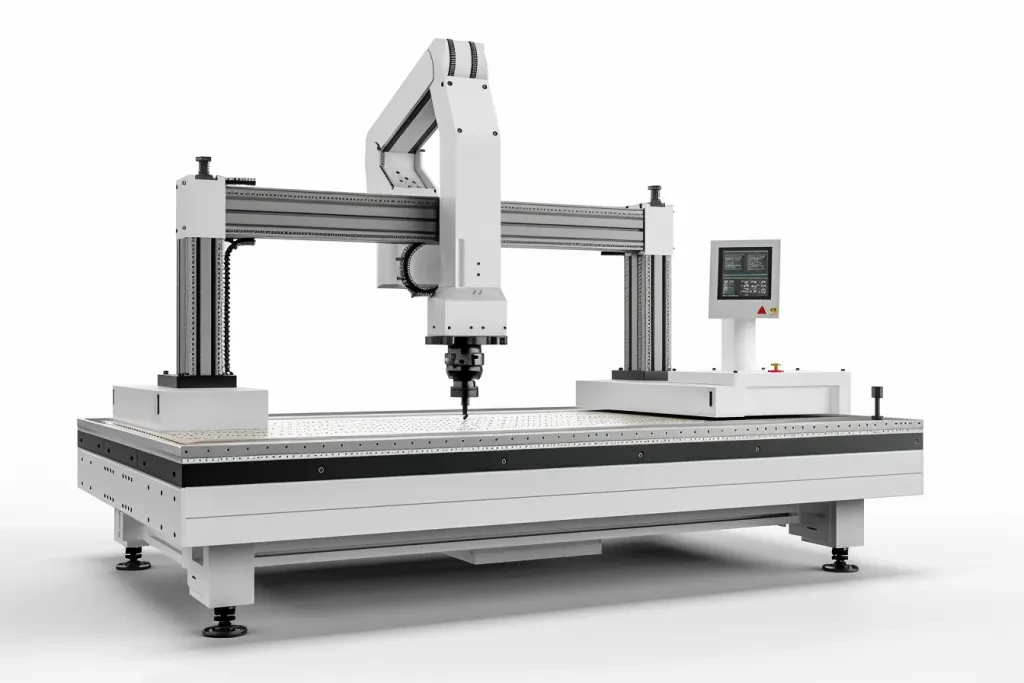
I tagliatori al plasma CNC sono strumenti essenziali nella produzione moderna, offrendo elevata precisione e velocità nel taglio di metalli come acciaio, alluminio e rame. Le dinamiche di mercato sono influenzate dai progressi tecnologici, dai fattori economici e dai cambiamenti nel comportamento dei consumatori. L'introduzione del controllo numerico computerizzato (CNC) e dei sistemi automatizzati ha notevolmente migliorato l'efficienza e la produttività delle macchine per il taglio al plasma, rendendole indispensabili nei settori che richiedono lavorazioni dei metalli complesse e precise.
L'industria automobilistica detiene la maggior parte della quota di mercato, spinta dalla necessità di componenti metallici di alta qualità. Anche il settore aerospaziale mostra una crescita sostanziale, con i tagliatori al plasma CNC ampiamente utilizzati per tagliare e modellare parti metalliche per aeromobili e veicoli spaziali. Fattori economici, come la crescente adozione di fonti di energia rinnovabili, alimentano ulteriormente la crescita del mercato, poiché queste macchine sono fondamentali nella produzione di componenti per turbine eoliche e pannelli solari.
Le recenti innovazioni sul mercato includono lo sviluppo di taglierine al plasma CNC più efficienti e precise, che integrano funzionalità avanzate come sistemi di controllo migliorati e protocolli di sicurezza potenziati. Questi progressi soddisfano le esigenze dei clienti come maggiore precisione, riduzione degli sprechi e conformità alle normative ambientali. La crescente domanda di prodotti in metallo personalizzati rappresenta anche un'opportunità significativa, poiché le taglierine al plasma CNC consentono la produzione di design altamente personalizzati e complessi.
Fattori chiave nella scelta di un taglierino al plasma CNC
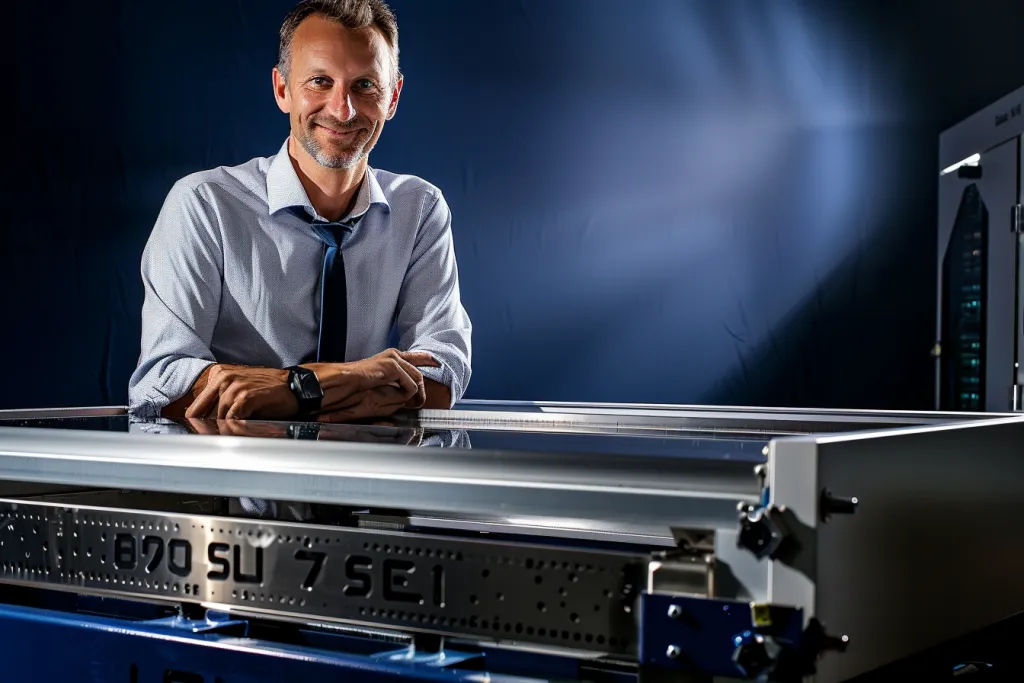
La scelta del giusto plasma cutter CNC comporta la valutazione di diversi fattori critici per garantire prestazioni ottimali e convenienza economica. Di seguito sono riportate considerazioni essenziali per gli acquirenti aziendali nel settore dei macchinari.
Spessore e tipo del materiale
Una delle considerazioni più cruciali è lo spessore e il tipo di materiale che intendi tagliare regolarmente. I tagliatori al plasma CNC possono gestire vari materiali, ma la loro efficienza varia in base alla conduttività e allo spessore del materiale.
Capacità di taglio
La capacità di taglio di un plasma cutter CNC si riferisce allo spessore massimo del materiale che può tagliare efficacemente. Ad esempio, alcune macchine di fascia alta possono tagliare materiali fino a 3 pollici di spessore. Per applicazioni che coinvolgono materiali più sottili, potrebbe essere sufficiente una macchina con amperaggio inferiore, che fornisce un controllo e una precisione migliori.
Varietà di materiali
I tagliatori al plasma CNC sono versatili, in grado di tagliare vari materiali elettricamente conduttivi come acciaio dolce, acciaio inossidabile, alluminio, ottone e rame. La scelta del gas utilizzato nel processo al plasma, come argon o azoto, può anche influire sulla qualità e sulla velocità del taglio, in particolare per le leghe reattive.
Prestazioni e precisione
Le prestazioni di un plasma cutter CNC sono spesso misurate dalla sua velocità di taglio e precisione. I modelli ad alte prestazioni offrono velocità di taglio e perforazione superiori, che sono fondamentali per mantenere la produttività nelle operazioni ad alto volume.
Requisiti di alimentazione ed efficienza
Conoscere i requisiti di potenza e l'efficienza di un sistema di taglio al plasma CNC è essenziale per garantire che soddisfi le proprie esigenze operative senza comportare costi energetici eccessivi.
Alimentazione di laboratorio
I tagliatori al plasma CNC in genere richiedono un'alimentazione sostanziale, con macchine ad amperaggio più elevato che necessitano di più potenza. È importante assicurarsi che l'infrastruttura elettrica della tua struttura possa supportare i requisiti della macchina per evitare interruzioni operative.
Energy Efficiency
I moderni tagliatori al plasma CNC sono progettati tenendo a mente l'efficienza energetica. Caratteristiche come regolazioni automatiche della potenza e sistemi di raffreddamento avanzati aiutano a ridurre al minimo il consumo energetico, rendendoli più convenienti a lungo termine.
Facilità d'uso e automazione
La facilità d'uso e il livello di automazione offerti da un sistema di taglio al plasma CNC possono avere un impatto significativo sulla produttività e sul comfort dell'operatore.
Interfaccia utente
Un'interfaccia user-friendly con controlli intuitivi può ridurre la curva di apprendimento per gli operatori. I modelli avanzati sono dotati di controller touch screen, porte USB per un facile trasferimento dei dati e software che semplifica la programmazione di schemi di taglio complessi.
Caratteristiche di automazione
Le funzionalità di automazione come il controllo automatico dell'altezza della torcia, i sollevatori motorizzati e la funzionalità CNC consentono tagli precisi e uniformi con un intervento manuale minimo. Queste funzionalità non solo migliorano la qualità del taglio, ma aumentano anche la sicurezza riducendo la necessità per gli operatori di trovarsi nelle immediate vicinanze dell'area di taglio.
Standard di sicurezza e certificazioni
Il rispetto degli standard e delle certificazioni di sicurezza è fondamentale per garantire un ambiente di lavoro sicuro e la conformità alle normative del settore.
Funzioni di sicurezza integrate
I tagliatori al plasma CNC funzionano ad alte temperature e utilizzano alta tensione per avviare l'arco al plasma. Le caratteristiche di sicurezza, come i sensori che impediscono l'avvio dell'arco se l'ugello non è in posizione, e i meccanismi di spegnimento automatico in caso di malfunzionamento, sono fondamentali per proteggere gli operatori.
Le Certificazioni
Cercate macchine conformi agli standard di sicurezza riconosciuti, come BS EN 50192 per i sistemi di taglio al plasma. Le certificazioni di organizzazioni affidabili garantiscono che l'attrezzatura soddisfi rigorosi criteri di sicurezza e prestazioni.
Manutenzione e durata
La longevità e l'affidabilità di un dispositivo di taglio al plasma CNC dipendono dalla qualità della sua costruzione e dalla facilità di manutenzione.
Qualità
I tagliatori al plasma CNC di alta qualità sono realizzati con materiali durevoli come l'alluminio anodizzato, che può resistere ai rigori dell'uso industriale. Componenti come guide lineari di precisione e robusti ugelli del gas contribuiscono alla durata complessiva della macchina.
Requisiti di manutenzione
Una manutenzione regolare è essenziale per mantenere il plasma cutter CNC in condizioni ottimali. Le macchine con caratteristiche come torce a sgancio rapido senza utensili e teste di taglio rimovibili semplificano le attività di manutenzione, riducendo i tempi di fermo e prolungando la durata dell'attrezzatura.
Progressi tecnologici nei tagliatori al plasma CNC
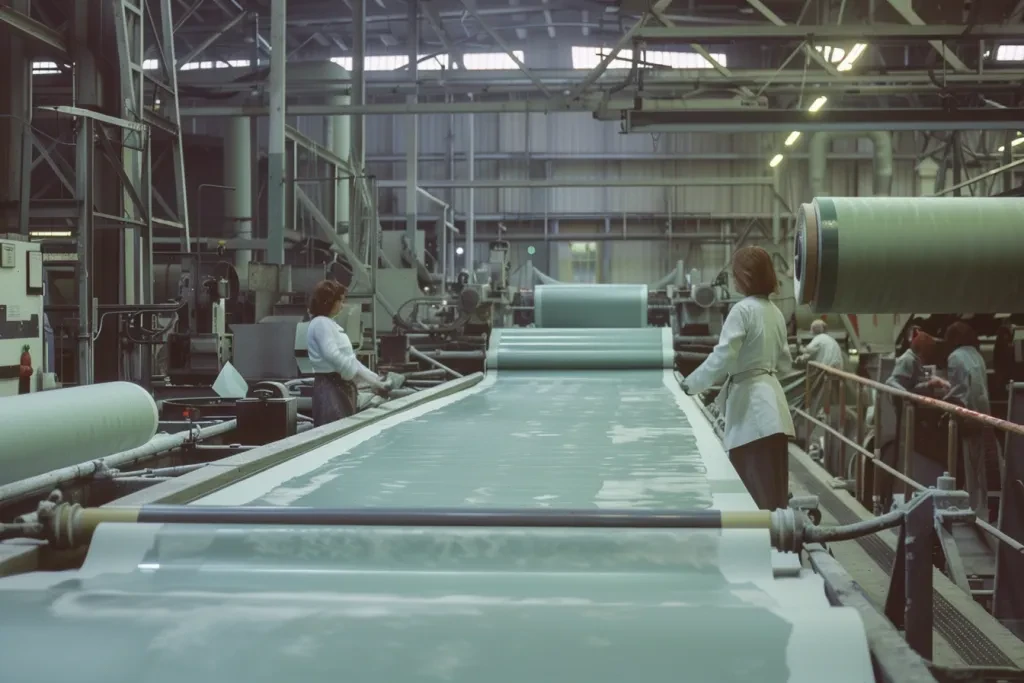
Il settore del taglio al plasma CNC ha assistito a notevoli progressi tecnologici, migliorando sia la funzionalità che l'efficienza di queste macchine.
Precisione di taglio migliorata
Gli sviluppi recenti nella tecnologia di taglio al plasma CNC si sono concentrati sul miglioramento della precisione di taglio. Innovazioni come i sistemi al plasma ad alta definizione e i meccanismi avanzati di controllo dell'altezza della torcia consentono tagli più puliti con scorie o scorie minime.
Soluzioni software integrate
I moderni tagliatori al plasma CNC sono dotati di soluzioni software integrate che semplificano il processo di taglio. Queste soluzioni software spesso includono funzionalità CAD/CAM, consentendo agli operatori di progettare ed eseguire schemi di taglio complessi con facilità.
Monitoraggio e diagnostica in tempo reale
I tagliatori al plasma CNC avanzati sono dotati di strumenti di monitoraggio e diagnostica in tempo reale. Questi strumenti forniscono agli operatori informazioni critiche sulle prestazioni della macchina, aiutando a identificare e risolvere i problemi prima che causino tempi di fermo significativi.
Considerazioni sui costi e budget
Il costo è un fattore critico quando si seleziona un plasma cutter CNC. È importante bilanciare l'investimento iniziale con i costi operativi a lungo termine e il potenziale ritorno sull'investimento.
Investimento iniziale
Il costo iniziale di un plasma cutter CNC può variare ampiamente in base alle sue capacità e caratteristiche. I modelli di fascia alta con automazione avanzata e caratteristiche di precisione tendono a essere più costosi, ma offrono maggiore efficienza e produttività.
Costi operativi
I costi operativi includono il consumo energetico, la manutenzione e i materiali di consumo come elettrodi e ugelli. Le macchine con maggiore efficienza energetica e componenti durevoli possono aiutare a ridurre questi costi nel tempo.
Return on Investment
La valutazione del potenziale ritorno sull'investimento (ROI) implica la considerazione della capacità della macchina di migliorare la produttività, ridurre gli sprechi e migliorare la qualità del taglio. Un plasma cutter CNC che offre miglioramenti significativi in queste aree può fornire un ROI favorevole nonostante un costo iniziale più elevato.
Durevole e affidabile: durata della taglierina al plasma CNC
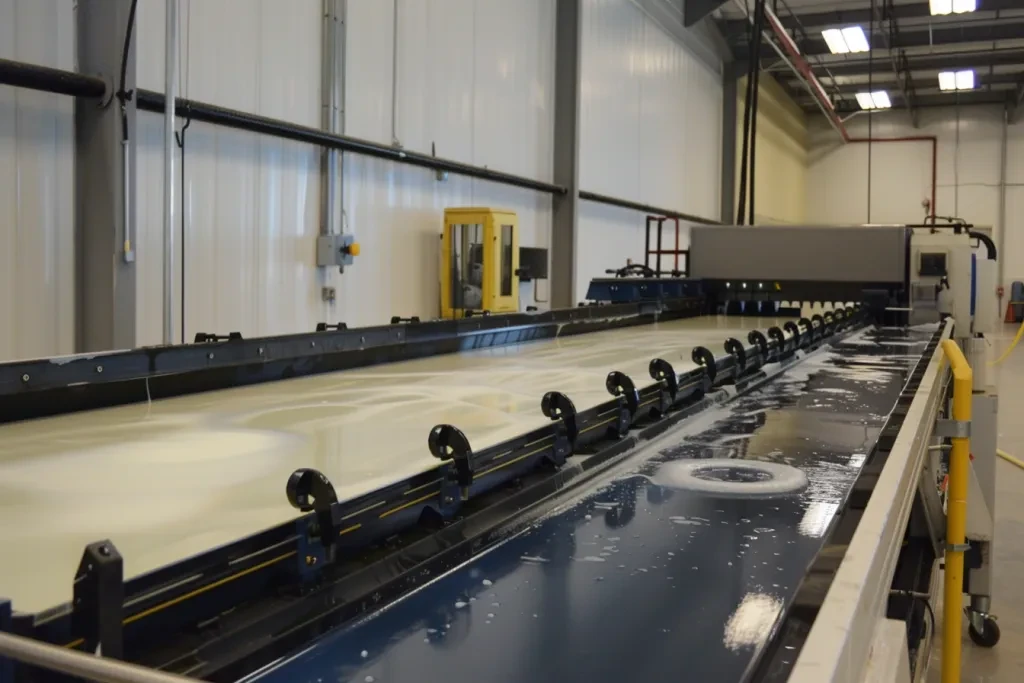
La durata di vita di un taglierino al plasma CNC è influenzata da diversi fattori, tra cui la qualità di costruzione, le pratiche di manutenzione e l'intensità di utilizzo.
Costruisci qualità e materiali
Le macchine realizzate con materiali di alta qualità, come alluminio anodizzato e acciaio inossidabile, tendono ad avere una durata maggiore. Anche la qualità dei componenti come la torcia da taglio e gli ugelli del gas gioca un ruolo cruciale nel determinare la durata della macchina.
Pratiche di manutenzione
Una manutenzione regolare, che include pulizia, controlli dei componenti e sostituzione tempestiva dei materiali di consumo, è essenziale per estendere la durata di vita di un plasma cutter CNC. Le macchine con caratteristiche di facile manutenzione possono semplificare queste attività e ridurre i tempi di fermo.
Intensità di utilizzo
L'intensità e la frequenza di utilizzo possono avere un impatto sulla durata di vita di un plasma cutter CNC. Le macchine progettate per applicazioni pesanti sono costruite per resistere a un uso continuo, mentre quelle destinate a compiti più leggeri potrebbero avere una durata di vita più breve se utilizzate oltre la loro capacità prevista.
Sommario
In sintesi, la scelta del giusto plasma cutter CNC comporta la valutazione di vari fattori, tra cui spessore e tipo di materiale, requisiti di potenza, facilità d'uso, standard di sicurezza, manutenzione e considerazioni sui costi. I progressi tecnologici e il potenziale per un ritorno favorevole sull'investimento influenzano ulteriormente il processo decisionale. Considerando attentamente questi fattori, gli acquirenti aziendali possono scegliere un plasma cutter CNC che soddisfi le loro esigenze specifiche e migliori la loro efficienza operativa.