Uno sguardo alle tendenze attuali e alle problematiche della catena di fornitura per il settore automobilistico
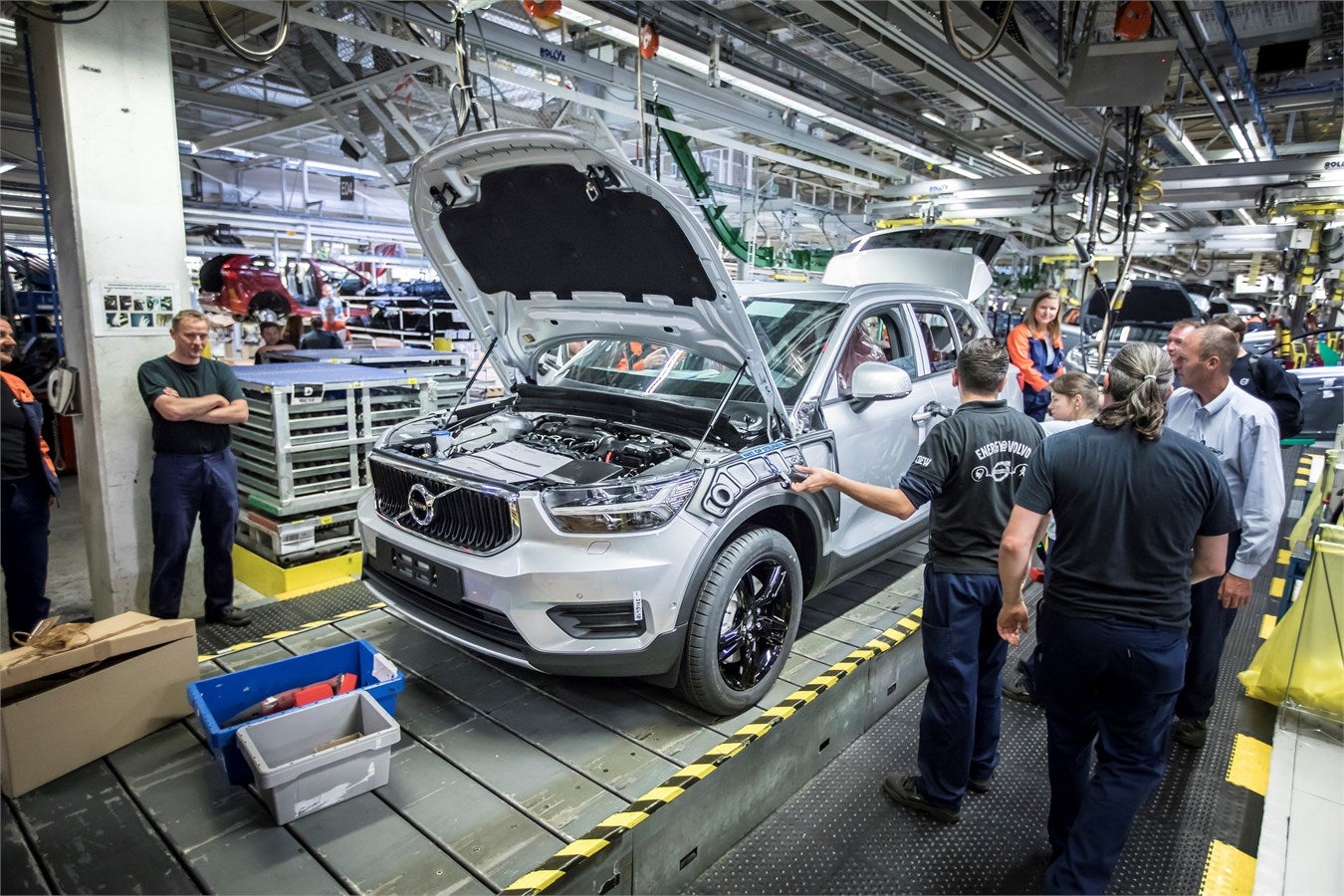
Un veicolo a motore atipico può contenere tra 15,000 e 25,000 componenti, a seconda di come vengono misurati e dell'ingegneria di progettazione dei suoi sistemi principali. Si tratta di molto materiale da mettere insieme e fornire integrità al prodotto finale. In effetti, non è un’impresa da poco mettere insieme tutte queste parti nel giusto ordine. Ogni automobile esistente è un omaggio alla pianificazione dei processi, all'organizzazione, all'ingegneria della produzione e alla logistica della produzione. Un tempo, i produttori di veicoli erano altamente integrati verticalmente, ma questo approccio ha lasciato il posto a fornitori dismessi (qualcuno ricorda da dove proveniva Visteon e l'intricata rete di aziende che comprendeva il gruppo Automotive Components di General Motors?) e fornitori di componenti specializzati che potevano concentrarsi su sviluppo del prodotto e operare in modo più efficiente su scala più ampia per più di un cliente.
I grandi integratori di sistemi di livello 1 forniscono direttamente ai produttori di veicoli, spesso da parchi fornitori convenientemente situati vicino agli impianti di assemblaggio e produzione dei veicoli, ma ci sono più livelli di fornitori più piccoli al di sotto del livello più alto, ciascuno dei quali svolge un ruolo vitale nel lungo percorso dal grezzo materiali al prodotto finito.
L'approvvigionamento internazionale di componenti è diventato per molti decenni una modalità operativa standard del settore poiché gli OEM e i fornitori più grandi hanno cercato di cercare nel mercato globale parti e input di materiali che soddisfacessero le soglie di qualità necessarie al costo più basso. Anche le distanze (e i costi) per il trasporto e le modalità di stoccaggio fanno parte del quadro, ma la maggiore efficienza e i progressi tecnologici nelle spedizioni internazionali di merci hanno sostenuto una crescita fenomenale delle spedizioni internazionali di componenti.
La crescita dell’industria automobilistica cinese negli ultimi vent’anni è stata anche un fattore importante nell’approvvigionamento globale di componenti automobilistici, in particolare di quelli che potrebbero essere definiti componenti universali o di consumo venduti principalmente a prezzo di costo. I fornitori cinesi hanno beneficiato di grandi contratti locali che stimolano le economie di scala, nonché di sussidi nascosti che derivano da complesse strutture proprietarie che coinvolgono case madri OEM, imprese statali e partecipazioni azionarie diversificate. All’inizio degli anni 2000, i produttori di veicoli statunitensi, in particolare, iniziarono a procurarsi componenti a basso costo dall’Asia, minando così alcune aziende di lunga data nella base di fornitori statunitense.
In tutto il mondo, i flussi commerciali internazionali di prodotti automobilistici – sia veicoli finiti che componenti – sono ormai enormi. Stime compilate da GlobalData mostrano che la Germania è di gran lunga il leader internazionale in termini di spedizioni in uscita di prodotti dell'industria automobilistica. Tali esportazioni si rispecchiano nelle importazioni e in una rete intricata di beni intermedi che vengono utilizzati come input per sistemi di componenti che vengono perfezionati e progettati in diverse fasi del processo di produzione e possono essere spediti più volte attraverso i confini internazionali.
Un’altra caratteristica strutturale importante per le catene di fornitura nell’industria automobilistica è l’importanza di una filosofia di gestione della catena di fornitura che riduca al minimo i costi di inventario e migliori l’efficienza dei processi e i cicli di comunicazione di feedback per migliorare gli standard di qualità. Conosciuta come "produzione snella", è iniziata con Toyota e la sua essenza è racchiusa nel termine "just-in-time" per descrivere i metodi e i principi di fornitura snella. L’ascesa delle tecnologie digitali e connesse che riuniscono tutte le parti del processo di produzione e vendita al dettaglio ha ulteriormente sostenuto queste modalità di lavoro negli ultimi dieci anni circa.
In passato, i disastri naturali e il loro impatto concentrato sui luoghi hanno avuto un impatto sulle aziende automobilistiche e hanno evidenziato la fragilità delle catene di fornitura automobilistiche. Dopo il terremoto e lo tsunami del 2011 in Giappone, si sono verificati diversi esempi notevoli di disagi. Un produttore globale di auto premium ha avuto problemi in termini di fornitura o di un pigmento per vernice rossa acquistato esclusivamente in Giappone. Le inondazioni in Tailandia nello stesso anno causarono una carenza di fornitura di schermi LCD per la visualizzazione delle informazioni sui veicoli. OEM e concessionari hanno dovuto adeguarsi di conseguenza alle carenze. La guerra in Ucraina illustra come anche eventi geopolitici inaspettati possano interrompere le catene di approvvigionamento.
La sfida dei semiconduttori
Tutte le aziende sono state colpite direttamente dalla crisi sanitaria pubblica del 2020 e indirettamente da molti altri effetti sulle catene di approvvigionamento globali. Inoltre, la ripresa delle vendite globali nel 2021 è stata gravemente compromessa da una conseguenza imprevista della crisi Covid un anno prima. Mentre i produttori di veicoli hanno chiuso le fabbriche per ordine del governo e ridotto drasticamente gli ordini di componenti nel 2020, i produttori di semiconduttori hanno trovato attività alternative in settori come l’elettronica di consumo.
Quando gli stabilimenti automobilistici in ripresa hanno aumentato gli ordini di chip nel primo trimestre del 2021, è diventato rapidamente evidente un problema di scarsità dell’offerta.
Inoltre, le carenze di semiconduttori non sarebbero state facilmente superabili a causa dei lunghi tempi di attesa per l’aggiunta a monte della capacità della fonderia di chip. L'assenza di una parte critica per la sicurezza o ritenuta in qualche modo necessaria per il prodotto finito ha fatto sì che alcune linee di modelli subissero un impatto più grave di altre. In alcuni casi i produttori di veicoli potevano mescolare il mix del mercato, ma un vecchio adagio si stava avverando di nuovo: le catene di fornitura sono buone/robuste solo quanto il loro punto più debole.
In tutto il settore, i metodi e i processi di approvvigionamento vengono messi sotto esame come mai prima d’ora.
Vale anche la pena notare che esiste un elemento strutturale in gioco, il che significa che alcune pressioni sulla fornitura di semiconduttori probabilmente rimarranno un rischio in futuro: il contenuto elettronico avanzato dei veicoli è in aumento a causa della crescente dotazione di caratteristiche tecnologiche più sofisticate. Ciò sta spingendo alcune aziende a stringere alleanze strategiche con i produttori di chip. Ciò non solo può aiutare a garantire le forniture future di microprocessori critici, ma può anche facilitare vantaggiose relazioni collaborative future per lo sviluppo di prodotti in quella che sta diventando evidente essere un'area di componenti strategicamente preziosa.
Altre pressioni sulle catene di approvvigionamento provengono da altre fonti, come la carenza di manodopera imprevista e i prezzi molto più alti delle spedizioni internazionali di container a seguito dell’impennata dei prezzi dell’energia.
Il dibattito tra dual-sourcing e multi-sourcing
La fragilità nelle catene di fornitura automobilistiche deriva dalla prevalenza di livelli multipli, da flussi di approvvigionamento internazionali e dalla tendenza all’approvvigionamento unico per massimizzare le economie di scala nei programmi globali di veicoli. In molti casi, questa struttura tradizionale è anche radicata e radicata in una cultura di partner privilegiati a tutti i livelli di fornitura. I vantaggi possono includere anche sistemi condivisi e costi logistici, con costi ripartiti tra volumi anche su altri modelli e sistemi.
Anche la tecnologia ha contribuito a incoraggiare il single sourcing poiché le aziende, comprese quelle di livello 3 e 4, sono state in genere in grado di centralizzare competenze e investimenti in un’unica struttura dedicata alla produzione di grandi volumi. I problemi arrivano quando qualcosa va storto e fa naufragare i piani (l’incendio in uno stabilimento di microprocessori Renesas l’anno scorso, per esempio).
L'elettronica e i sensori sono esempi di componenti critici per sottoinsiemi che possono avere grandi implicazioni a valle nella produzione di veicoli in caso di interruzione a monte. Trovare fornitori alternativi con capacità inutilizzata con brevissimo preavviso è una grande sfida.
Mantenere alcune riserve di componenti in magazzino comporta un costo e va contro i principi guida della produzione snella. Naturalmente si può decidere di assorbire o ammortizzare eventuali costi di interruzione anomali man mano che si verificano: ciò dipende in ultima analisi dalla quantificazione della valutazione del rischio.
L’esperienza degli ultimi anni indica almeno che le aziende si chiedono sempre più spesso se il single-sourcing sia desiderabile come lo era una volta. Un mondo afflitto da rischi e incertezze più elevati richiede forse un nuovo approccio. La duplicazione all’interno della catena di fornitura, anche se significa avvicinarsi alla condivisione con un concorrente, può offrire una soluzione migliore – almeno per alcuni componenti – rispetto al single sourcing. Una maggiore sicurezza del prodotto sarebbe il vantaggio del doppio approvvigionamento. Come sempre, è una questione di costo complessivo.
Elettrificazione e nuovi modelli di filiera
L’elettrificazione comporta nuove sfide per le future catene di fornitura del settore automobilistico. Gli OEM si trovano ad affrontare notevoli incertezze sulla fornitura di componenti nuovi e chiave – in particolare le batterie dei gruppi propulsori – che stanno cercando di risolvere. Esistono anche questioni strategiche sul grado di integrazione verticale auspicabile per mitigare i rischi futuri ed esercitare il controllo sugli aspetti commerciali degli accordi di fornitura. Sono state create joint venture con specialisti di batterie. Anche altri componenti chiave per i veicoli elettrici – come motori, parti del sistema di trasmissione, inverter ad alta tensione – saranno soggetti a crescenti investimenti insieme alle considerazioni sulla catena di fornitura.
Strategie ambiziose di elettrificazione vedranno salire alle stelle la domanda di batterie agli ioni di litio. I produttori di batterie di tutto il mondo si stanno impegnando in strategie di espansione multimiliardarie, aprendo nuove “gigafabbriche” per fornire celle alle case automobilistiche.
Un esempio notevole di profonda collaborazione OEM-Tier 1 in quest’area è fornito dalla firma di un protocollo d’intesa tra Volkswagen e Bosch. Le due società prevedono di fornire sistemi integrati di produzione di batterie, accelerazione in loco e supporto per la manutenzione ai produttori di celle e sistemi batteria. Dichiarano di puntare alla leadership tecnologica e in termini di costi nella tecnologia delle batterie su scala industriale e alla produzione in volume di "batterie sostenibili e all'avanguardia".
Solo in Europa, il Gruppo Volkswagen prevede di costruire sei fabbriche di celle entro il 2030 e altri produttori stanno adottando misure simili per garantire le future forniture di celle e pacchi batteria. La regione dovrebbe raggiungere una capacità annua totale delle batterie di circa 700 gigawattora entro il 2030.
Guardando a monte, Toyota ha formato una JV con Panasonic (Prime Planet Energy & Solutions – PPES) che ha firmato un accordo con il colosso minerario BHP per la futura fornitura di solfato di nichel, la base del nichel presente nel catodo della maggior parte degli ioni di litio celle della batteria. Tesla ha anche firmato un accordo simile con BHP, dimostrando che anche le materie prime sono molto importanti per la futura sicurezza dell’approvvigionamento.
Questi accordi evidenziano la necessità per gli operatori del settore automobilistico di guardare più in alto nella catena di fornitura delle batterie, per assicurarsi di avere accesso a materie prime sufficienti per soddisfare l’enorme crescita di capacità necessaria nel settore delle batterie agli ioni di litio per la nuova ondata di veicoli elettrici a batteria lanciati nel mercato. prossimi anni. Anche il riciclaggio è un elemento chiave in molti degli accordi conclusi.
Blockchain per la visibilità della supply chain
Sempre più spesso, le aziende automobilistiche utilizzano la tecnologia blockchain per ottenere trasparenza su questioni relative alla catena di approvvigionamento come le emissioni di CO2 e la fonte di cobalto per le batterie (che possono comportare questioni etiche relative all’estrazione di minerali preziosi).
Il concetto originale di blockchain, come suggerisce il nome, è una catena di blocchi o record con timestamp (blocco = informazioni digitali; catena = database pubblico/comunitario). I blocchi memorizzano informazioni sulle transazioni. Quando un blocco memorizza nuovi dati – una transazione – viene aggiunto alla blockchain e, una volta verificato da una rete di computer peer-to-peer, chiunque può vederlo (o può essere soggetto al permesso di una rete privata come catena di fornitura di un OEM – il "registro distribuito").
Tuttavia, tutte le parti hanno accesso solo alle informazioni che sono autorizzate a vedere. Ogni computer nella rete blockchain ha la propria copia della blockchain. In linea di principio, però, l’idea è quella di creare un sistema altamente trasparente con costi di transazione pari a zero tra le due parti creando un blocco.
Possiamo aspettarci di vedere sempre più aziende automobilistiche adottare processi blockchain – in particolare del tipo registro distribuito (ovvero rete privata) – come mezzo per mitigare il rischio di “interruzioni” della catena di fornitura e comprendere i punti di forza e di debolezza lungo la catena, ma anche come un modo per modo per dimostrare le crescenti richieste di conformità in aree normative come la sostenibilità.
Lezioni da Toyota
Toyota è generalmente considerata una delle aziende con le migliori prestazioni nel settore automobilistico per quanto riguarda la gestione della catena di fornitura. Oltre ad essere l'ideatore dei metodi di produzione snella che in seguito sono diventati le migliori pratiche diffuse adottate dalla maggior parte degli OEM e dai principali fornitori, ha anche perfezionato i propri sistemi e processi in base alle mutevoli circostanze relative alle misure di mitigazione del rischio. Inoltre, ha lavorato a stretto contatto con i suoi fornitori, a volte e nell'interesse di obiettivi settoriali più ampi, di fronte alle emergenze.
Dopo il terremoto e lo tsunami di Kyoto del 2011, Toyota ha collaborato con i fornitori giapponesi per produrre un database completo di informazioni sulla catena di fornitura per supportare il settore manifatturiero giapponese. Toyota ha inoltre introdotto una strategia per l’approvvigionamento multiplo di componenti chiave, il che significherebbe organizzare la fornitura da tre diverse fonti, ma con il fornitore principale impegnato a realizzare quasi i due terzi dell’ordine per garantire economie di scala. La presenza di più fornitori compromette le economie di scala, ma significa anche che esistono alternative se necessario.
Toyota dispone inoltre di un sistema ben sviluppato per monitorare la sua vasta rete di fornitori e di un sistema di allarme tempestivo in caso di carenze. In effetti, alcune aziende si rivolgono all’intelligenza artificiale per valutare gli sviluppi nelle loro catene di fornitura, anche se ciò presuppone innanzitutto il possesso di un database affidabile, ampio e dettagliato.
Un’altra opzione per le aziende è intraprendere il mantenimento di scorte di emergenza o di scorta di componenti chiave, in particolare di quelli che possono causare l’arresto di una linea di produzione. Ancora una volta, ciò comporta costi aggiuntivi per lo stoccaggio o il magazzinaggio, ma è una questione di stabilire quale livello di costo o "premio assicurativo" vale la pena pagare. Inoltre, non sarà una soluzione permanente. La Toyota potrebbe aver accumulato alcuni semiconduttori, ma la gravità della carenza globale di chip ha fatto sì che, alla fine, anche lei sia stata costretta a tagliare la produzione. Forse l’apprendimento più significativo tratto da Toyota è la necessità di costante revisione e adattabilità al cambiamento delle circostanze e delle incertezze.
Fonte da Solo auto
Dichiarazione di non responsabilità: le informazioni sopra riportate sono fornite da just-auto.com indipendentemente da Chovm.com. Chovm.com non rilascia alcuna dichiarazione o garanzia in merito alla qualità e all'affidabilità del venditore e dei prodotti.