BMW グループは、オーバーシュライスハイムの積層造形キャンパスで、アルミニウムなどで作られたワイヤーをアークを使って溶かすワイヤー アーク積層造形 (WAAM) を試行しています。次に、ソフトウェア制御のロボットが多数の溶接継ぎ目を正確に重ね合わせて、完全なコンポーネントが完成します。
圧力をかけることで層ごとに離型性を考慮する必要がないため、剛性と重量の最適な比率を備えた中空構造が可能です。
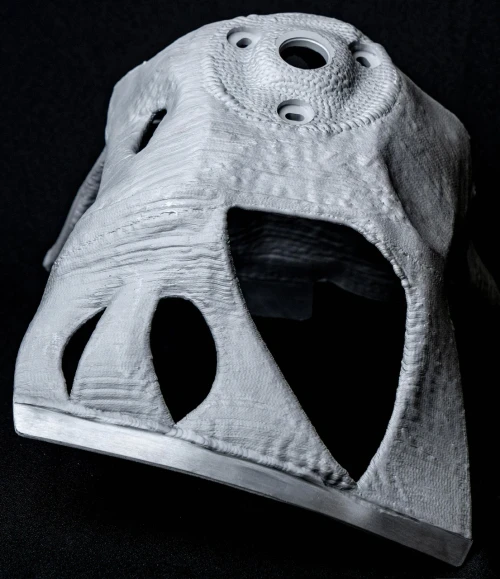
これは、現在連続生産されている同等のダイカスト部品よりもコンポーネントを軽量かつ高剛性にできることを意味します。また、エネルギー要件が低くなり、材料廃棄物が少なくなるため、より持続可能な方法で生産することもできます。将来的には、WAAM プロセスを使用して製造されたコンポーネントを BMW グループの量産車に使用する計画です。
単一の溶接シームの幅と高さが大きいということは、WAAM を使用してコンポーネントを非常に迅速に製造できることを意味します。 BMW グループのプロトタイプや少量の量産ですでに使用されているレーザー ビーム溶解とは対照的に、WAAM は特に大型コンポーネントに適しています。一般的な壁の厚さは、本体、ドライブ、シャーシ領域のコンポーネントに適しています。ただし、航空業界でも使用されているこのハイテクプロセスを使用してツールやデバイスを製造することもできます。
BMW グループの従業員は、2015 年以来、肉盛溶接としても知られる WAAM プロセスに注力してきました。テスト コンポーネントの製造用の WAAM セルは、2021 年からアディティブ マニュファクチャリング キャンパスで使用されています。これらのアプリケーション例の XNUMX つが、サスペンション ストラット サポートは、テストベンチでの広範なテストにおいて、アルミニウム圧力ダイカストで作られた量産コンポーネントと比較されています。
この初期段階では、WAAM プロセスにより生産プロセスにおける排出量の削減が可能であることはすでに明らかです。コンポーネントの軽量化、有利な材料使用率、および再生可能エネルギーの使用のオプションは、コンポーネントをより効率的に生産できることを意味します。
—BMW アディティブ マニュファクチャリング責任者、イェンス アーテル氏
量産に向けた開発の次の段階は、車両内のコンポーネントのテストであり、近い将来に開始される予定です。
WAAM プロセスでは溶接線が広いため、コンポーネントの表面は滑らかではなく、わずかに波状になっており、重要な領域を仕上げる必要があります。しかし、BMW グループのエンジニアは、表面の後処理を行わなくても、WAAM コンポーネントが周期的荷重を含む高荷重に使用できることを実証できました。
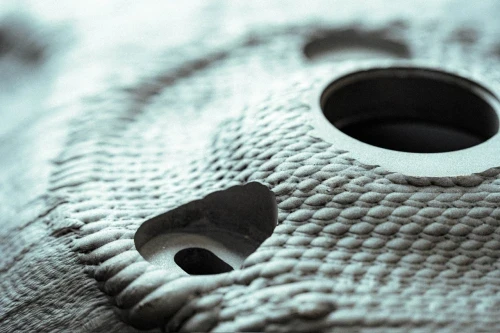
生産から直接耐久性を確保するには、最適化されたプロセスパラメータが重要であるため、溶接プロセスとロボットのパス計画の組み合わせを最適に調整する必要があります。
WAAM プロセスで製造されるコンポーネントを最大限に活用するには、製造プロセスと一般的な新しいコンポーネント設計の組み合わせが最も重要です。この目的を達成するために、BMW グループはジェネレーティブ デザインの利用を加速し続けています。ここでは、コンピューターはアルゴリズムを使用して、特定の要件に基づいて最適化されたコンポーネントを設計します。
これらのアルゴリズムは、学際的なチームとの緊密な連携によって開発されており、自然界の進化のプロセスから一部インスピレーションを受けています。バイオニック構造の場合と同様、最初のステップでは、コンポーネントのトポロジーに実際に必要な材料のみを使用し、2 番目のステップでの微調整中に、必要な箇所のみコンポーネントが強化されます。これにより、最終的にコンポーネントの軽量化と剛性の向上、効率の向上と車両のダイナミクスの向上が実現します。
異なる添加剤製造プロセスは必ずしも互いに競合するわけではなく、むしろ補完的であると見なすべきです。たとえば、最高レベルの詳細解像度に関しては、レーザー ビーム溶解は WAAM プロセスよりも有利であり続けるでしょう。ただし、可能なコンポーネントのサイズと堆積速度の点では、ワイヤー アーク積層造形の方が優れています。
BMW グループは当初、オーバーシュライスハイムで WAAM コンポーネントの集中生産を計画していますが、将来的には他の場所での生産やサプライヤーによるテクノロジーの使用も可能です。さらに、このプロセスを使用して個々のコンポーネントを組立ラインで直接製造したり、ソフトウェアを変更するだけで新しいツールを使用せずにさまざまな部品を製造したりすることも考えられます。リサイクル金属の使用を増やすことで、持続可能性をさらに向上させることもできます。
ソースから グリーンカー会議
免責事項: 上記の情報は、Chovm.com とは独立して、greencarcongress.com によって提供されます。 Chovm.com は、販売者および製品の品質と信頼性についていかなる表明も保証も行いません。