無駄のない製造法は、世界中の産業に変革をもたらした方法論であり、無駄の削減と効率性を重視しています。日本の製造業から生まれたこのアプローチは、オペレーショナルエクセレンスの世界標準となっています。この記事では、リーン マニュファクチャリングの中核原則、その利点、導入戦略、一般的な課題について検討し、この極めて重要な方法論についての包括的な理解を提供します。
目次:
– リーン生産とは何ですか?
– 無駄のない製造の 5 つの基本原則
– 無駄のない製造を導入する主な利点
– リーンマニュファクチャリングの導入を成功させるための戦略
– 無駄のない製造における共通の課題
無駄のない製造とは何ですか?
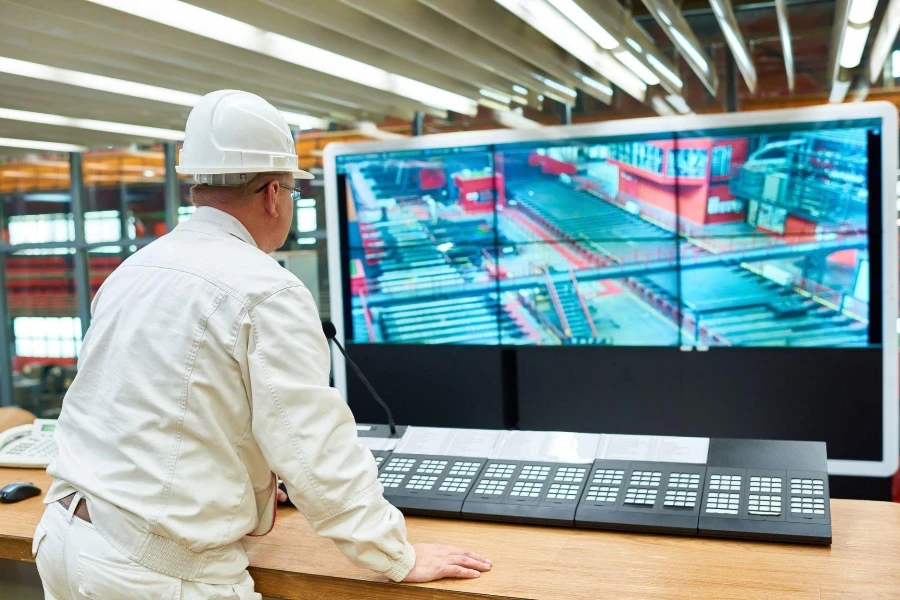
リーン マニュファクチャリングの核心は、生産性を犠牲にすることなく製造システム内の無駄を最小限に抑える体系的な方法です。顧客の視点からの価値を重視し、価値を付加しないプロセスをすべて排除します。このコンセプトは、少ない労力でより多くのことを実現するというものではありません。それは、より少ない労力でより多くの重要なことを行うことです。これは、継続的な改善の文化を奨励する哲学であり、小さな漸進的な変更が定期的に大幅な改善につながります。
リーン マニュファクチャリングの起源は、バリュー ストリームを通じた製品とサービスの流れの最適化の重要性を強調したトヨタ生産システムに遡ります。その後、このアプローチはさまざまな業界で採用および適応され、その多用途性と有効性が証明されています。
リーン マニュファクチャリングを理解するには、従来の製造慣行から考え方を変える必要があります。それは単なるツールやテクニックのセットではありません。それは効率、適応性、そして人々の尊重を優先する考え方です。
無駄のない製造の 5 つの基本原則
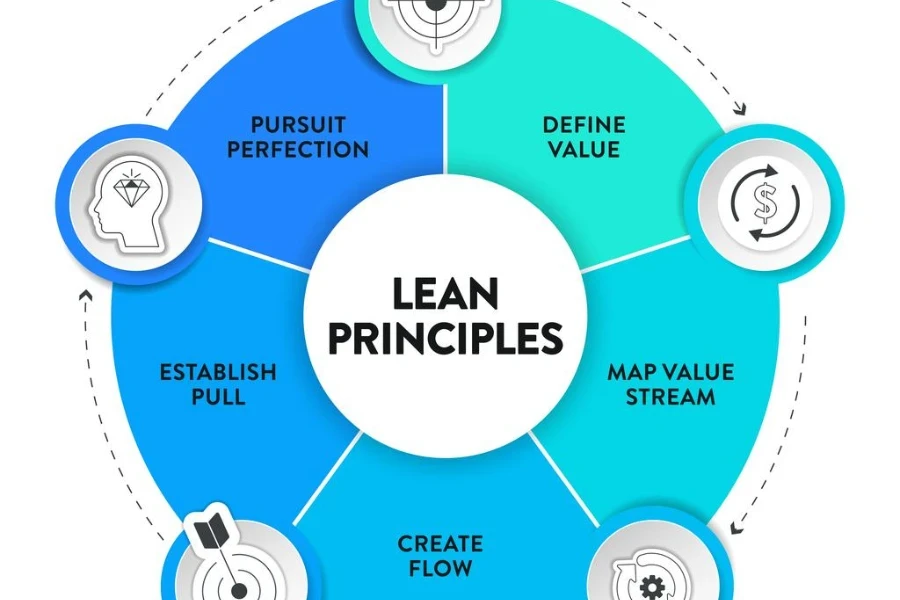
リーン マニュファクチャリングは、組織が優れたオペレーションを実現するための指針となる 5 つの基本原則に基づいて構築されています。これらの原則は次のとおりです。
- 値の定義:リーンマニュファクチャリングの最初のステップは、顧客の視点から価値を定義することです。顧客はあなたの製品やサービスの何を正確に評価しますか?これを理解することで、企業は本当に重要なことに注力できるようになります。
- バリューストリームをマッピングする: 価値が定義されたら、次のステップは、この価値に寄与するすべてのステップを計画し、価値を付加しないプロセスを特定して排除することです。
- フローの作成: 無駄を取り除いた後は、残りのステップが中断、遅延、ボトルネックなくスムーズに進むようにすることに重点が移ります。
- プルを確立する: この原則は、必要なときに必要なものだけを生産し、過剰生産と在庫を削減することを中心に展開しています。
- 完璧を追求する: 最後の原則は、プロセス、製品、サービスを完璧にするための継続的な努力であり、継続的改善の文化を促進します。
無駄のない製造を導入する主な利点
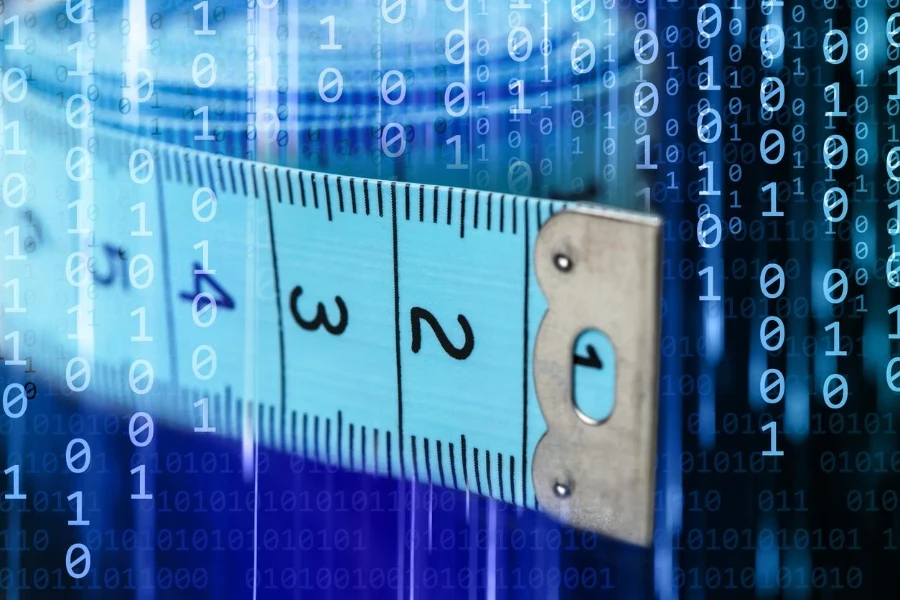
リーン マニュファクチャリングを導入すると、次のような多くのメリットがもたらされます。
- コスト削減:無駄を排除することで、企業は生産コストを大幅に削減でき、収益性の向上につながります。
- シミュレーションの質の向上: 無駄のない製造では、欠陥の検出よりも欠陥の予防を重視し、製品の品質を高め、返品や修理を減らします。
- 効率の向上: プロセスを合理化し、付加価値のないステップを削除することで、効率と生産性が向上します。
- 顧客満足度の向上:顧客の視点からの価値に焦点を当てることで、企業は顧客のニーズをより適切に満たすことができ、より高い満足度とロイヤルティにつながります。
- 継続的改善の文化を育む: リーン マニュファクチャリングでは、あらゆるレベルの従業員が改善のためのアイデアを提出することを奨励し、ダイナミックで順応性の高い組織を実現します。
リーンマニュファクチャリングの導入を成功させるための戦略
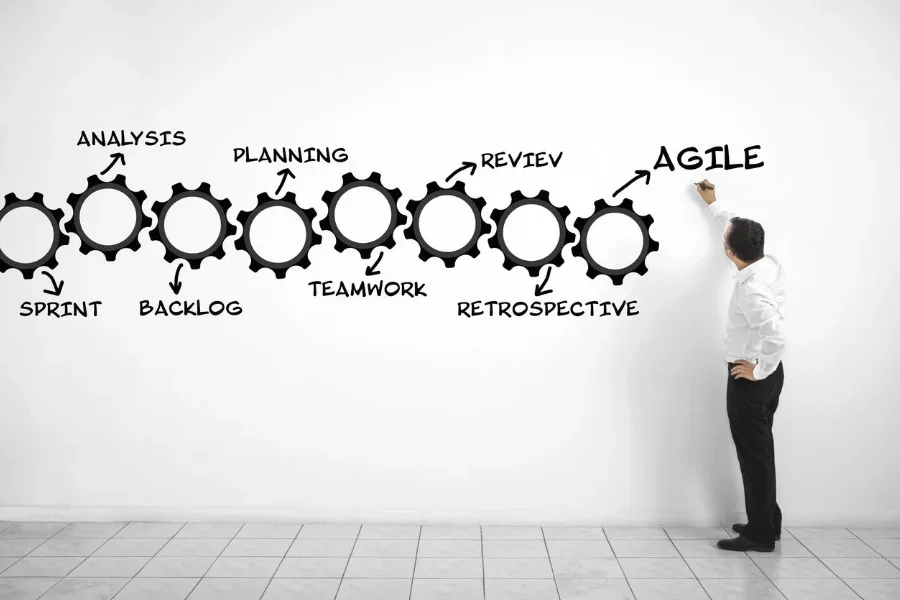
リーン マニュファクチャリングの導入には、次のような戦略的アプローチが必要です。
- 包括的なトレーニング: 継続的な改善の文化を育むには、リーンの原則とツールについて全従業員を教育することが重要です。
- 値ストリームマッピング: プロセスを分析および視覚化して無駄と改善の機会を特定することは、リーン導入の基礎となるステップです。
- 従業員に権限を与える: 従業員に非効率性を特定し、改善を提案するよう奨励することで、リーン原則が効果的に適用されるようになります。
リーン マニュファクチャリングの導入は 1 回限りのイベントではなく、継続的な取り組みです。成功には、組織のあらゆるレベルのコミットメントと、適応して変化する意欲が必要です。
無駄のない製造における一般的な課題
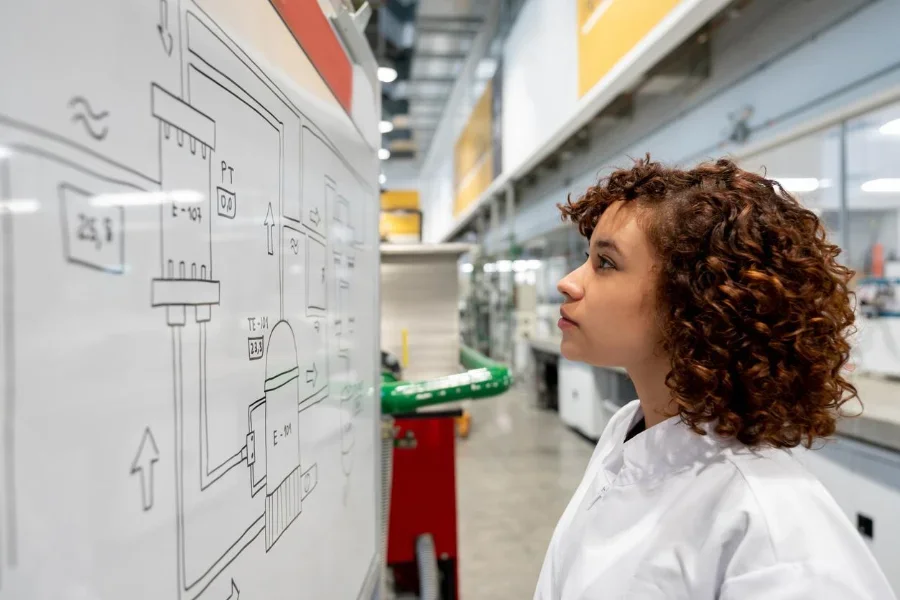
メリットにもかかわらず、リーン マニュファクチャリングの導入には次のような課題が生じる可能性があります。
- 変化に対する耐性:長年の習慣や考え方を変えるのは難しい場合があります。抵抗を克服するには、強力なリーダーシップと明確なコミュニケーションが必要です。
- 理解の欠如:リーン原則を深く理解していないと、努力の方向が間違ってしまい、フラストレーションや限定的な結果につながる可能性があります。
- 継続的な改善: 勢いを維持して改善を続けるには、継続的な改善に対する献身と構造化されたアプローチが必要です。
これらの課題を克服するには、明確な戦略、強力なリーダーシップ、教育と権限付与への取り組みが必要です。
結論:
リーン・マニュファクチャリングは単なるツールのセットではありません。これは、効率、品質、顧客満足度の大幅な向上につながる革新的な哲学です。その中心原則を理解して適用することで、企業は課題を乗り越え、この強力なアプローチのメリットを享受できます。業界が進化し続ける中、リーンマニュファクチャリングは競争力を維持し、常に変化する顧客の要求に応えるための重要な戦略であり続けています。