Recent advancements in packaging technology have revolutionized the Shrink Wrap Machine market. This article provides an in-depth analysis of the latest trends, key factors in selecting the right machine, and the value it offers to professional buyers. Learn how to make informed decisions that align with your business objectives.
目次:
– The Shrink Wrap Machine Market: Current State and Predictions
– Key Factors When Selecting a Shrink Wrap Machine
– Importance of Build Quality and Materials
– Latest Technological Advancements
– 規制遵守と認証
– Versatility and Upgrade Potential
- 最終的な考え
The Shrink Wrap Machine Market: Current State and Predictions
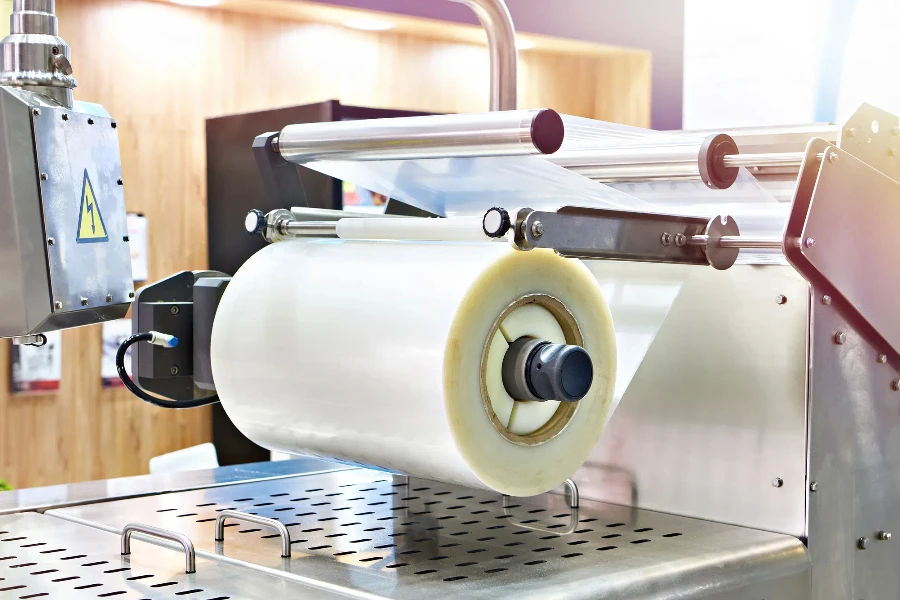
Market Overview: A Detailed Examination
The Shrink Wrap Machine market has experienced notable growth in recent years. As of 2024, its market size is estimated at USD 843.47 million and is projected to reach USD 1,118.51 million by 2030, with a compound annual growth rate (CAGR) of 5.00%. This growth is fueled by the rising demand for efficient packaging solutions across industries such as food and beverage, pharmaceuticals, and consumer goods.
The market is segmented by type, including orbital stretch wrappers, ring straddle stretch wrappers, and straddle stretch wrappers. Each type addresses specific packaging needs, contributing to market expansion. For instance, the turntable stretch wrapper is particularly favored in the food and beverage sector due to its efficiency and cost-effectiveness.
The Asia-Pacific region is expected to witness the highest growth rate, driven by the expanding manufacturing sector and increasing demand for packaged goods. Key players in this region include China, India, and Japan, supported by rising urbanization and industrialization.
In-Depth Market Analysis: Drivers and Challenges
Several factors influence the Shrink Wrap Machine market, including technological advancements, economic conditions, and consumer preferences. A primary driver is the increasing demand for packaged goods, which requires efficient and reliable packaging solutions. This is especially true in the food and beverage industry, where extended shelf life and improved product presentation are crucial.
Technological innovations are crucial in shaping the market. Recent advancements include automated wrapping solutions that enhance operational efficiency and reduce film waste. These innovations cater to various industries, from pharmaceuticals to consumer electronics. For example, the integration of real-time monitoring and IoT technology in shrink wrap machines has significantly improved their functionality and performance.
However, the market also faces challenges. The high initial investment for advanced shrink wrap machines can be a barrier for small and medium-sized enterprises. Additionally, the need for skilled operators and regular maintenance can increase operational costs. Despite these challenges, the market is expected to continue growing, driven by the demand for efficient and sustainable packaging solutions.
主なトレンドとイノベーション
Recent trends in the Shrink Wrap Machine market show a shift towards more sustainable and eco-friendly packaging solutions. Manufacturers are focusing on developing machines that reduce film waste and are compatible with biodegradable materials. This trend is driven by environmental concerns and regulatory requirements aimed at reducing plastic waste.
Digitalization is another significant trend. The integration of digital technologies, such as IoT and AI, in shrink wrap machines has enhanced efficiency and reliability. These technologies enable real-time monitoring and predictive maintenance, reducing downtime and improving productivity. For instance, IoT-enabled shrink wrap machines can monitor performance and alert operators of potential issues, ensuring smooth operations.
Consumer behavior is also evolving, with a growing preference for convenience and ready-to-eat meals. This shift has increased the demand for efficient and reliable packaging solutions that ensure product safety and quality. In response, manufacturers are developing advanced shrink wrap machines that cater to the specific needs of the food and beverage industry, such as machines that provide airtight and tamper-evident packaging.
Key Factors When Selecting a Shrink Wrap Machine
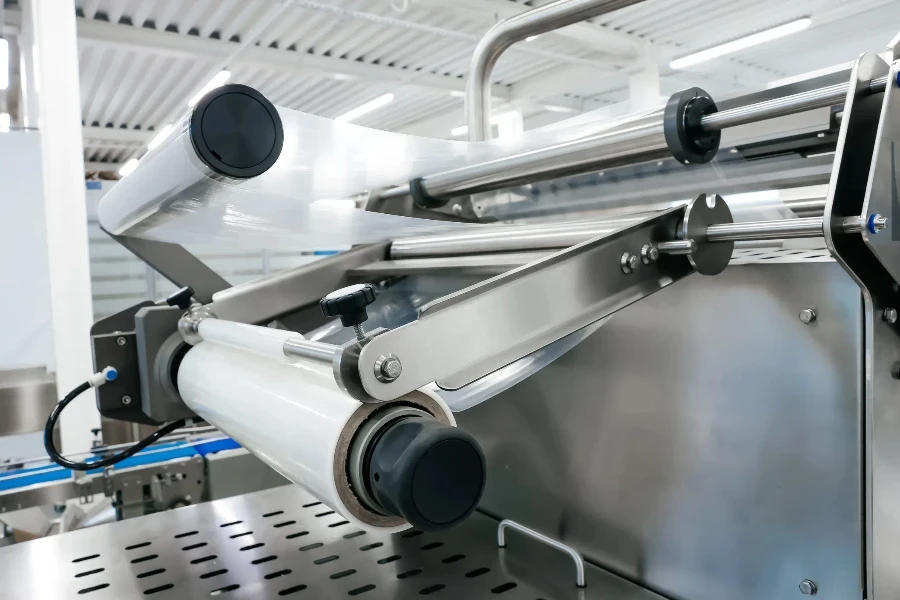
シュリンクラップマシンの種類
Understanding the different types of shrink wrap machines is essential for choosing the right equipment for your packaging needs. There are two main types: I-bar sealers and L-bar sealers. I-bar sealers are suitable for low-to-mid volume applications. They use a single bar to cut PVC or polyolefin film, which is then shrunk using a heat gun or heat tunnel. This type is ideal for smaller operations where flexibility and cost-efficiency are important.
L-bar sealers, on the other hand, are designed for medium to high-volume applications. They feature an L-shaped cutting bar that allows for a single pass around the product for cutting. These machines are often used with heat tunnels to achieve uniform shrinkage. L-bar sealers are more efficient for larger operations due to their higher volume capacity and greater automation capabilities.
材料の互換性
The type of film used in shrink wrap machines greatly affects the final packaging quality. Common materials include PVC, polyolefin, and polyethylene. PVC film is cost-effective and offers good clarity, making it suitable for retail packaging. However, it releases more fumes during the shrinking process, which may require additional ventilation.
Polyolefin film is more expensive but provides better clarity, strength, and puncture resistance. It is also FDA-approved for direct food contact, making it ideal for food packaging. Polyethylene film is used for larger, heavier items due to its robust nature. Understanding the compatibility of your shrink wrap machine with these materials is key to achieving optimal packaging results.
自動化レベル
Shrink wrap machines come in manual, semi-automatic, and fully automatic variants. Manual machines are labor-intensive and suitable for low-volume operations, requiring an operator to manually cut and seal the film. This can be time-consuming but offers flexibility and control.
Semi-automatic machines balance manual and fully automatic systems. They need some operator intervention but automate the sealing and shrinking processes, increasing efficiency and throughput. Fully automatic machines are best for high-volume operations. They require minimal operator intervention and can handle large batches with consistent quality, making them suitable for industrial-scale packaging.
その他機能
Modern shrink wrap machines offer various additional features to enhance functionality and efficiency. Aseptic or sanitary options ensure easy cleaning and maintenance, crucial for food and pharmaceutical industries. Hazardous location protection is essential for operations involving flammable or explosive materials.
Portability is important for smaller operations or those needing frequent equipment relocation. Stainless steel construction offers durability and corrosion resistance, suitable for harsh environments. Advanced features like robotic automation and processor interfaces can significantly boost productivity and integration with other automated systems.
エネルギー効率
Energy efficiency is a critical consideration due to rising energy costs and environmental concerns. Modern shrink wrap machines are designed to consume less energy while maintaining high performance. Features like energy-saving modes, efficient heat tunnels, and advanced control systems can reduce energy consumption.
Energy-efficient machines lower operational costs and contribute to sustainability goals. Investing in such equipment can offer long-term savings and align with corporate social responsibility initiatives. It’s advisable to check the energy ratings and certifications of the shrink wrap machine before purchasing.
Importance of Build Quality and Materials
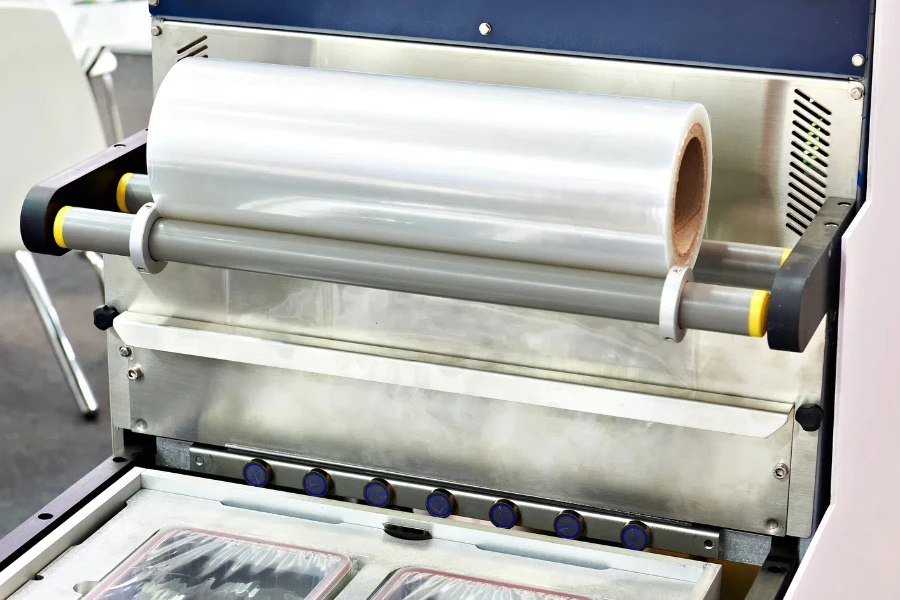
The build quality and materials used in shrink wrap machines greatly influence their durability and performance. High-quality stainless steel machines offer superior resistance to corrosion and wear, making them ideal for demanding industrial environments. Stainless steel construction also ensures easy cleaning and maintenance, crucial for maintaining hygiene standards in food and pharmaceutical packaging.
The choice of materials for internal components like seals, cutters, and heat elements is equally important. High-grade materials ensure longevity and reduce the frequency of maintenance and part replacements. Investing in a machine with robust build quality can lead to lower total cost of ownership and higher operational efficiency.
最新の技術の進歩
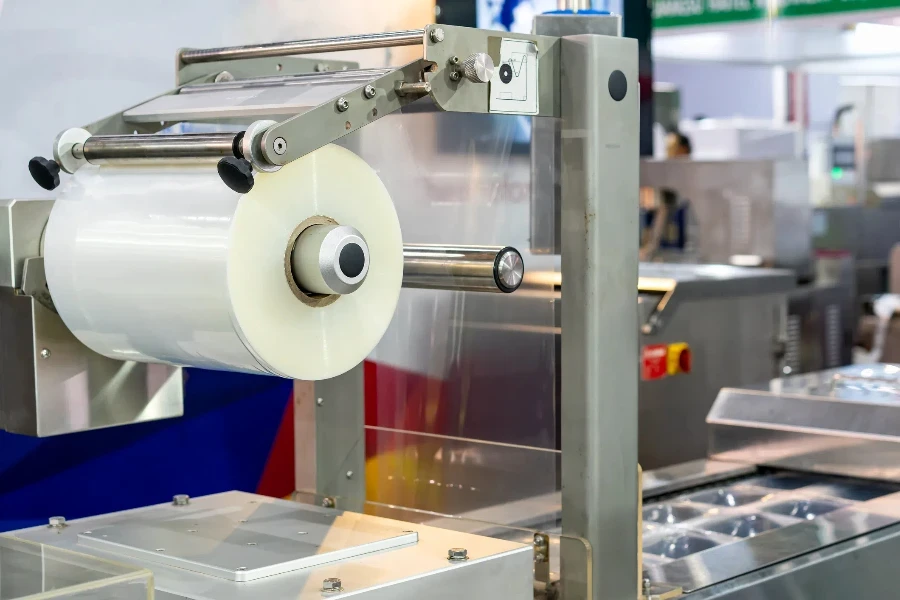
The shrink wrap machine industry has seen significant technological advancements recently. Integration with IoT (Internet of Things) allows real-time monitoring and control of the packaging process. IoT-enabled machines provide valuable data on machine performance, maintenance needs, and operational efficiency, enabling predictive maintenance and reducing downtime.
Another advancement is the use of AI (Artificial Intelligence) for optimizing the packaging process. AI algorithms can analyze data from the packaging line to identify inefficiencies and suggest improvements. These technologies enhance productivity and contribute to better quality control and reduced operational costs.
規制の遵守と認証
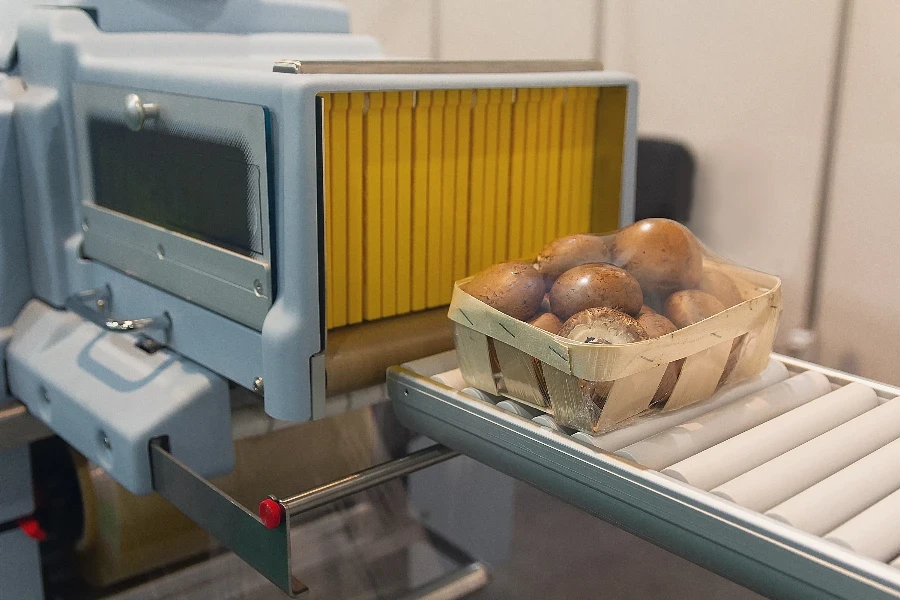
Compliance with industry standards and regulations is crucial for ensuring the safety and quality of packaged products. Shrink wrap machines used in food and pharmaceutical industries must adhere to FDA regulations and other relevant standards. Machines with certifications like CE, UL, and ISO ensure they meet stringent safety and quality requirements.
Regulatory compliance also extends to environmental standards. Machines designed to reduce energy consumption and minimize waste contribute to sustainability goals and may qualify for green certifications. Ensuring that your shrink wrap machine complies with relevant regulations and certifications is essential for avoiding legal issues and ensuring the safety and quality of your products.
Versatility and Upgrade Potential
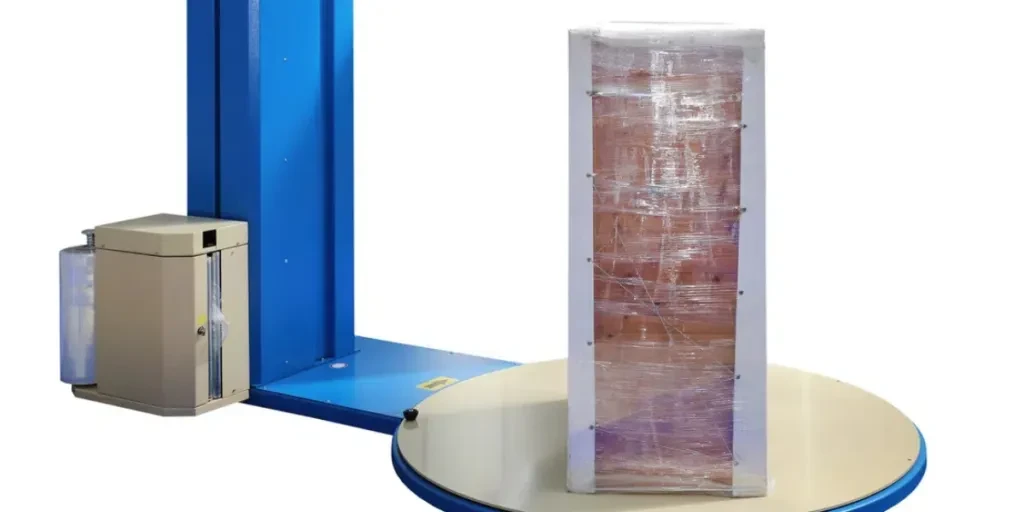
Versatility is important for businesses adapting to changing packaging needs. A versatile shrink wrap machine can handle a wide range of product sizes and shapes, making it suitable for diverse packaging applications. Machines with adjustable settings and interchangeable components offer greater flexibility and can accommodate future packaging requirements.
The upgrade potential of the machine is another crucial factor. Machines with modular components and compatibility with future upgrades can be easily adapted to incorporate new technologies and features. Investing in a machine with upgrade potential can extend its lifespan and protect your investment.
最終的な考え
Selecting the right shrink wrap machine involves careful consideration of various factors, including machine types, material compatibility, automation levels, additional features, energy efficiency, build quality, technological advancements, regulatory compliance, and versatility. By thoroughly evaluating these factors, businesses can make informed decisions that align with their packaging needs and operational goals.