自動車分野の現在のトレンドとサプライチェーンの問題を概観
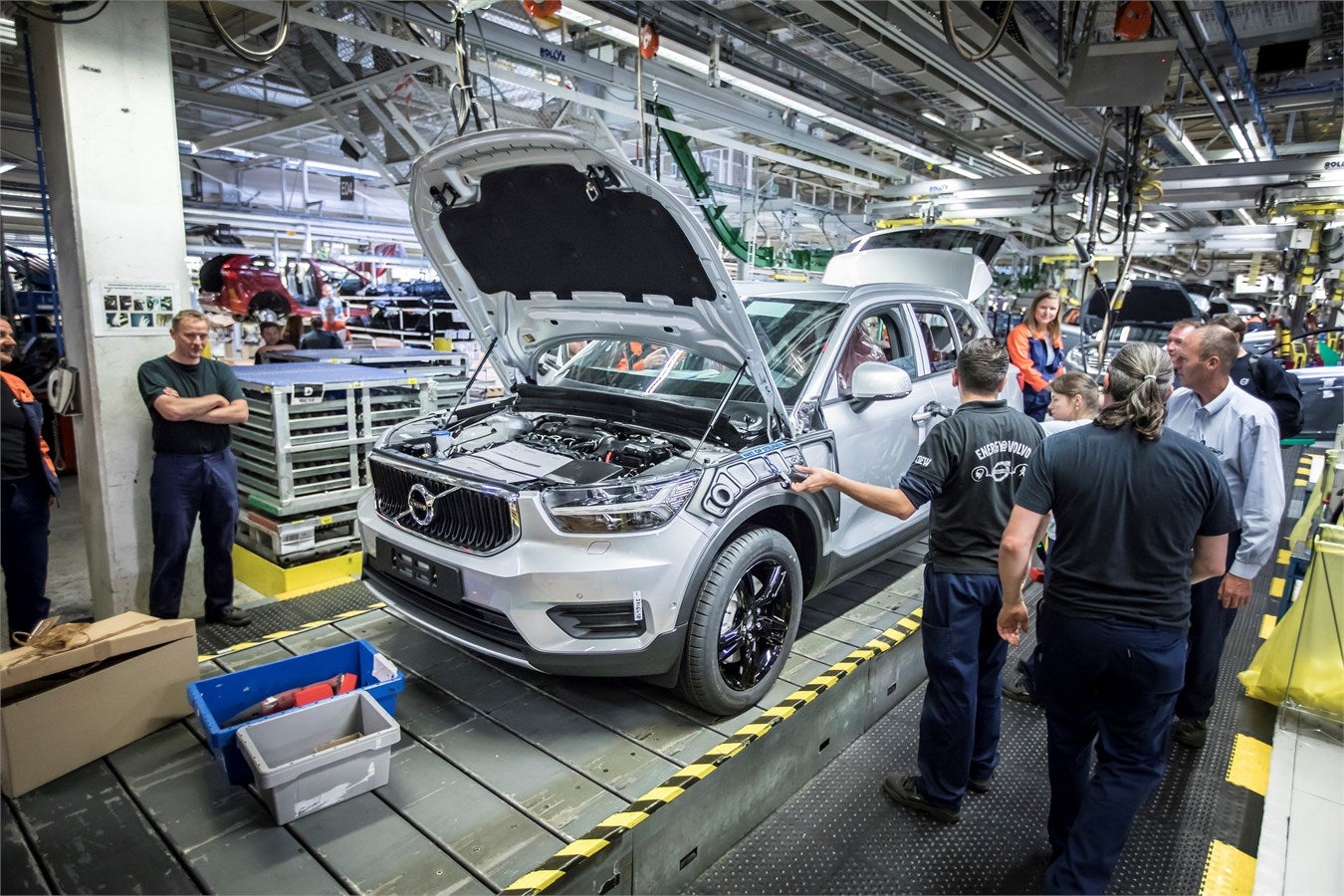
典型的な自動車には、測定方法と主要システムの設計エンジニアリングに応じて、15,000 ~ 25,000 個のコンポーネント部品が含まれることがあります。これには、最終製品の整合性を提供するために収集すべき多くの資料が含まれます。実際、これらすべてのパーツを正しい順序で組み合わせるのは並大抵のことではありません。存在するすべての自動車は、プロセス計画、組織化、生産エンジニアリング、製造物流への敬意を表しています。かつて、自動車メーカーは高度に垂直統合されていましたが、そのアプローチは売却され(ビステオンの起源と、ゼネラルモーターズの自動車部品グループを構成する複雑な企業の網の目を覚えている人はいますか?)、専門部品サプライヤーに道を譲り、製品開発を行い、複数の顧客に対してより大規模に効率的に運用することができます。
大手の Tier 1 システム インテグレーターは、多くの場合、車両の組立および製造施設に近い便利な位置にあるサプライヤー パークから自動車メーカーに直接供給していますが、最上位層の下には複数の小規模サプライヤーがあり、それぞれが原料からの長い道のりで重要な役割を果たしています。材料から完成品まで。
OEM や大手サプライヤーが、必要な品質基準を満たす部品や材料を最低コストで世界市場で調達しようとしてきたため、コンポーネント部品の国際調達は、何十年にもわたって業界標準の運用方法となってきました。輸送の距離(およびコスト)や倉庫保管の手配も問題の一部ですが、国際貨物輸送の効率の向上と技術の進歩が、国際部品出荷の驚異的な成長を支えています。
過去 2000 年間にわたる中国の自動車産業の成長も、自動車部品、特に主に原価で販売されるユニバーサルまたはコモディティ化された部品と呼ばれる部品の世界的な調達において大きな要因となっています。中国のサプライヤーは、規模の経済を促進する現地の大規模契約と、OEM親会社、国営企業、多様な株式保有が関与する複雑な所有構造から流れる隠れた補助金の恩恵を受けてきた。 XNUMX年代初頭、特に米国の自動車メーカーはアジアからより低コストの部品を調達するようになり、その過程で米国のサプライヤー基盤の一部の老舗企業が弱体化した。
現在、完成車と構成部品の両方を含む自動車製品の国際貿易の流れは世界中で膨大になっています。によってまとめられた推定値 沿革 ドイツが自動車産業製品の海外向け出荷において世界の圧倒的な国際的リーダーであることを示しています。これらの輸出は、輸入と、製造プロセスのさまざまな段階で精製および設計され、国境を越えて何度も輸送できるコンポーネントシステムへの入力として使用される中間財の絡み合った網によって反映されます。
自動車産業のサプライチェーンのさらに重要な構造的特徴は、在庫コストを最小限に抑え、品質基準を高めるためのプロセス効率とフィードバック通信ループを強化するサプライチェーン管理哲学の重要性です。 「リーン製造」として知られるこれはトヨタから始まり、その本質はリーン供給の方法と原則を表す「ジャストインタイム」という言葉に要約されています。製造および小売プロセスのすべての部分を統合するデジタルおよびコネクテッド テクノロジーの台頭により、過去 10 年ほどにわたってこうした働き方がさらに強化されました。
過去には、自然災害とその拠点への集中的な影響が自動車会社に影響を与え、自動車サプライチェーンの脆弱性を浮き彫りにしました。 2011 年の日本の地震と津波の後、いくつかの顕著な混乱の例がありました。世界的な高級車メーカーは、日本で唯一調達されている赤色塗料顔料の供給に関して問題を抱えていました。同年後半にタイで発生した洪水により、車両情報ディスプレイ用の LCD スクリーンの供給が不足しました。 OEM とディーラーは、不足に応じて調整する必要がありました。ウクライナ戦争は、予期せぬ地政学的な出来事がいかにサプライチェーンにも混乱をもたらす可能性があるかを示している。
半導体の挑戦
すべての企業は、2020 年の公衆衛生危機によって直接的に悪影響を受けましたが、間接的には世界のサプライチェーンに対するさらに多くの影響によって悪影響を受けました。さらに、2021年の世界売上高の回復は、前年の新型コロナウイルス危機による予期せぬ結果によって大きく損なわれた。 2020年に自動車メーカーが政府の命令に基づいて工場を閉鎖し、部品の注文を大幅に削減したため、半導体メーカーは家電製品などの分野に代替ビジネスが見つかることに気づいた。
回復中の自動車工場が2021年第XNUMX四半期にチップの発注を増やした際、供給不足の問題が急速に明らかになった。
上流のチップファウンドリの能力を追加するには長いリードタイムがかかるため、半導体不足も簡単には克服できませんでした。安全上重要な部品、または最終製品に必要と思われる部品が欠落しているため、一部のモデルラインが他のモデルラインよりも深刻な影響を受けました。場合によっては自動車メーカーが市場構成を入れ替える可能性もあるが、サプライチェーンの良さ/堅牢さはその最も弱い部分に応じて決まるという古い格言が再び現実となりつつある。
業界全体で、調達方法とプロセスがこれまでにないほど精査されています。
また、半導体の供給圧力が将来的にもリスクとして残る可能性が高いことを意味する構造的要素が働いていることも注目に値する。つまり、より洗練された技術的特徴の装備が増え続けているため、車両の高度なエレクトロニクスの内容が増加しているということである。このため、一部の企業はチップメーカーとの戦略的提携に移行している。これは、重要なマイクロプロセッサの将来の供給を確保するのに役立つだけでなく、戦略的に価値のあるコンポーネント分野であることが明らかになりつつある将来の有益な製品開発関係を促進することもできます。
サプライチェーンに対するその他の圧力は、予期せぬ労働力不足や、エネルギー価格の高騰に伴う国際コンテナ輸送価格の大幅な高騰など、他の原因からも生じている。
デュアルソースとマルチソースの議論
自動車サプライチェーンの脆弱性は、複数の階層、国際的な調達フローの蔓延、および世界的な自動車プログラム全体で規模の経済性を最大化するための単一調達の傾向に伴います。多くの場合、この伝統的な構造は、供給層全体にわたる優先パートナーの文化にも組み込まれ、根付いています。利点には、共有システムや物流コストも含まれ、コストは他のモデルやシステムのボリュームにも分散されます。
企業(ティア 3 および 4 の企業を含む)は通常、専門知識と投資を大量生産専用の XNUMX つの施設に集中させることができたため、テクノロジーも単一調達の促進に貢献してきました。問題は、排水処理業者が計画した何か問題が発生したときに発生します(たとえば、昨年のルネサスのマイクロプロセッサ工場での火災)。
電子機器やセンサーは、上流で何らかの混乱が生じた場合、自動車製造の下流で大きな影響を与える可能性があるサブアセンブリの重要なコンポーネントの例です。余力のある代替サプライヤーを急遽見つけることは大きな課題です。
部品の一部を在庫として保持するとコストがかかり、無駄のない製造の基本原則に反します。もちろん、異常値の混乱コストが発生したときにそのコストを吸収するか償却するかの決定は、最終的にはリスク評価の定量化によって決まります。
近年の経験は、少なくとも企業が単一調達が以前と同じように望ましいかどうかという質問をますますしていることを示しています。より高いリスクと不確実性に悩まされている世界では、おそらくアプローチのリセットが必要です。サプライチェーン内での重複は、たとえ競合他社との共有に近づくことを意味するとしても、少なくとも一部のコンポーネントに関しては、単一調達よりも優れたソリューションを提供する可能性があります。製品の安全性が向上すると、二重調達の利点が得られます。いつものように、それは全体的なコストの問題です。
電化と新しいサプライチェーンパターン
電動化は、自動車の将来のサプライチェーンに新たな課題をもたらします。 OEM 各社は、新しい主要コンポーネント、特にパワートレインのバッテリーの供給に関してかなりの不確実性に直面しており、その解決に努めています。将来のリスクを軽減し、供給取り決めの商業的側面を制御するために望ましい垂直統合の程度については、戦略的な問題もある。バッテリー専門家との合弁事業が設立されました。モーター、駆動システム部品、高電圧インバーターなどの電気自動車の他の主要コンポーネントも、サプライチェーンの考慮とともに投資増加の対象となるでしょう。
野心的な電動化戦略により、リチウムイオン電池セルの需要は急増すると予想されます。世界中の電池メーカーは、自動車メーカーに電池を供給するための新しい「ギガファクトリー」を開設し、数十億ドル規模の拡大戦略に取り組んでいる。
この分野における OEM と Tier 1 の緊密な連携の注目すべき例の XNUMX つは、フォルクスワーゲンとボッシュの間で覚書を締結したことです。両社は、バッテリーセルおよびバッテリーシステムメーカーに統合バッテリー生産システム、オンサイト立ち上げ、メンテナンスサポートを提供する予定です。彼らは、産業規模の電池技術と「持続可能な最先端電池」の量産においてコストと技術面でのリーダーシップを目指していると述べている。
欧州だけでも、フォルクスワーゲングループは2030年までに700つのセル工場を建設する計画であり、他のメーカーも将来のセルとバッテリーパックの供給を確保するために同様の措置を講じている。この地域では、2030 年までにバッテリーパックの年間総容量が約 XNUMX ギガワット時になる見込みです。
上流に目を向けると、トヨタはパナソニックと合弁会社を結成し(プライムプラネットエネルギー&ソリューションズ – PPES)、ほとんどのリチウムイオン電池の正極に存在するニッケルの基礎となる硫酸ニッケルの将来供給に関して鉱山大手BHPと契約を締結した。バッテリーセル。テスラはBHPとも同様の契約を締結しており、将来の供給の安全性を確保するために原材料も非常に重要であることを示しています。
これらの取引は、自動車業界がバッテリーのサプライチェーンをさらに検討し、2016年に発売されるバッテリーEVの新しい波に向けてリチウムイオン電池部門内で必要とされる膨大な容量増加を供給するのに十分な原材料に確実にアクセスできるようにする必要性を浮き彫りにしている。今後数年。これまでに行われた取引の多くでは、リサイクルも重要な考慮事項となっています。
サプライチェーンの可視化のためのブロックチェーン
CO2排出量やバッテリー用のコバルト源(貴重な鉱物の採掘には倫理的な問題が伴う可能性がある)などのサプライチェーンの問題に関する透明性を確保するために、自動車会社がブロックチェーン技術を活用するケースが増えている。
名前が示すように、元のブロックチェーンの概念は、タイムスタンプが付けられたブロックまたはレコードのチェーンです (ブロック = デジタル情報、チェーン = 公共/コミュニティ データベース)。ブロックにはトランザクションに関する情報が保存されます。ブロックに新しいデータ (トランザクション) が保存されると、そのデータはブロックチェーンに追加され、コンピューターのピアツーピア ネットワークによって検証されると、誰でもそれを見ることができます (または、次のようなプライベート ネットワークの許可が必要な場合もあります)。 OEM のサプライ チェーン – 「分散台帳」)。
ただし、すべての関係者は、閲覧権限のある情報にのみアクセスできます。ブロックチェーン ネットワーク内の各コンピューターには、独自のブロックチェーンのコピーがあります。ただし、原則として、ブロックを作成する 2 者間でトランザクションコストがゼロの、透明性の高いシステムを作成するという考えがあります。
サプライチェーンの「分断」のリスクを軽減し、チェーンに沿った強みと弱みを理解する手段として、特に分散型台帳(つまりプライベートネットワーク)タイプのブロックチェーンプロセスを採用する自動車会社がさらに増えることが予想されます。持続可能性などの規制分野におけるコンプライアンスへの要求の高まりを実証する方法。
トヨタからの教訓
トヨタは一般に、サプライチェーン管理に関して自動車業界で優れた業績をあげている企業の一つとみなされている。同社は、後にほとんどの OEM や主要サプライヤーが採用するベスト プラクティスとして広く採用されるリーン生産方式の創始者であるだけでなく、リスク軽減策に関する状況の変化に応じてシステムとプロセスを改良してきました。さらに、緊急事態に直面した場合には、より広範な分野の目的のために、時にはサプライヤーと非常に緊密に連携してきました。
2011 年の京都地震と津波の後、トヨタは日本のサプライヤーと協力して、日本の製造業をサポートするためのサプライチェーン情報の包括的なデータベースを作成しました。トヨタはまた、主要部品の複数調達戦略も導入した。これは、XNUMXつの異なる供給元からの供給を組織することを意味するが、規模の経済を確保するために、主要サプライヤーが注文のほぼXNUMX分のXNUMXを生産するように調整されている。複数のサプライヤーが規模の経済性を犠牲にしていることもありますが、それは必要に応じて代替手段が用意されていることも意味します。
トヨタはまた、サプライヤーの広大なネットワークを監視するための十分に開発されたシステムと、不足品の早期警告システムを導入しています。実際、一部の企業は自社のサプライチェーンの発展を評価するために AI に注目していますが、それはそもそも信頼性が高く、広範かつ詳細なデータベースを所有していることが前提となります。
企業にとってのもう 1 つの選択肢は、重要な部品、特に生産ラインの停止を引き起こす可能性のある部品の緊急在庫または緩衝在庫の維持に着手することです。繰り返しますが、保管や倉庫保管に追加のコストがかかりますが、どのレベルのコストまたは「保険料」を支払う価値があるか判断するのは問題です。また、それは永続的な解決策にはなりません。トヨタは一部の半導体を備蓄していた可能性があるが、世界的なチップ不足の深刻さにより、最終的には生産削減を余儀なくされた。おそらく、トヨタから学んだ最も重要なことは、絶え間ない見直しと、変化する状況や不確実性に対する適応力の必要性である。
ソースから ただ自動
免責事項: 上記の情報は、Chovm.com とは独立して just-auto.com によって提供されます。 Chovm.com は、販売者および製品の品質と信頼性についていかなる表明も保証も行いません。