In 2025, the worm drive mechanics market continues to grow, driven by technological advancements and increased industrial demand. This article provides an in-depth analysis of the key factors to consider when selecting worm drive mechanics, including material selection, efficiency, gear ratio, and lubrication. Professional buyers will find valuable insights to assist in making informed purchasing decisions for optimal performance and reliability.
目次:
– Understanding the Worm Drive Mechanics Market
– Key Factors When Selecting Worm Drive Mechanics
– Latest Technological Advancements in Worm Drive Mechanics
– Applications and Industry Use Cases
– Ensuring Compliance with Industry Standards
– 要点をまとめる
Understanding the Worm Drive Mechanics Market
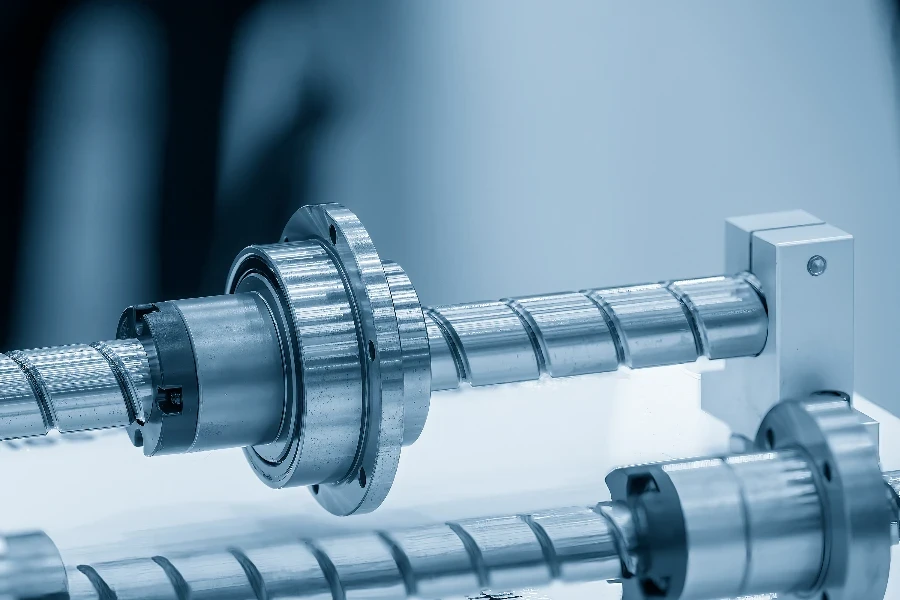
市場概観
The worm drive mechanics market is experiencing significant growth, driven by advancements in industrial applications and the continuous demand for precision gear systems. The global geared motors and drives market, which includes worm drives, was valued at USD 7.53 billion in 2023 and is projected to reach USD 10.73 billion by 2030, growing at a compound annual growth rate (CAGR) of 5.17%. This growth is attributed to the increasing use of worm drives in sectors like manufacturing, automotive, and material handling.
While the helical gear segment holds a significant share, the demand for worm gears is rising due to their unique advantages. Worm gears are preferred in applications requiring high torque and low speed, such as conveyor systems and heavy machinery. The Asia-Pacific region, particularly China, Japan, and South Korea, is leading the market due to robust manufacturing and industrial activities. Europe and North America also show substantial market shares, driven by advancements in automation and renewable energy sectors.
Detailed Analysis of Worm Drive Mechanics Market
Worm drives are crucial in various industrial applications, offering significant advantages in torque multiplication and speed reduction. These drives consist of a worm (a screw) and a worm wheel (a gear), which engage to provide substantial torque output with minimal space requirements. This makes them ideal for elevators, conveyor belts, and heavy machinery.
Key performance benchmarks for worm drives include efficiency, load capacity, and durability. Known for their smooth and quiet operation, worm drives are essential in noise-sensitive environments. Recent innovations in materials and lubrication technologies have further enhanced their performance and lifespan. For instance, high-grade alloys and synthetic lubricants have significantly reduced wear and increased efficiency.
Market share dynamics indicate that companies like Siemens AG, ABB Ltd., and Bonfiglioli Riduttori S.p.A. lead the market due to their extensive product portfolios and technological innovations. Economic influences such as the increasing focus on energy efficiency and the adoption of Industry 4.0 practices are driving the demand for advanced worm drive systems. Consumer behavior is shifting towards more reliable and maintenance-free solutions, evident from the rising sales of self-lubricating worm drives.
In terms of distribution channels, direct sales and online platforms are gaining traction, offering customers easier access to a wide range of products and custom solutions. The product lifecycle of worm drives is also evolving, with manufacturers focusing on sustainability and recyclability to meet stringent environmental regulations. Digitalization trends, such as IoT integration for predictive maintenance, are becoming prevalent, further enhancing the operational efficiency of worm drives.
Innovations and Trends in Worm Drive Mechanics
Recent innovations in worm drive mechanics include the development of hybrid worm gear systems that combine the benefits of worm gears with other gear types to enhance efficiency and load capacity. The adoption of smart manufacturing technologies and IoT-enabled monitoring systems is revolutionizing maintenance practices, allowing for real-time performance tracking and predictive maintenance.
The trend towards miniaturization in various industries is also influencing the worm drive market. Compact and high-performance worm drives are being developed for robotics, aerospace, and medical equipment industries. The focus on energy-efficient solutions is driving the development of worm drives with improved design and materials that reduce energy consumption and operational costs.
Customer pain points such as high maintenance costs and downtime are being addressed through innovations in self-lubricating materials and advanced sealing technologies. These advancements extend the lifespan of worm drives and reduce the total cost of ownership, making them more attractive to end-users.
Key Factors When Selecting Worm Drive Mechanics
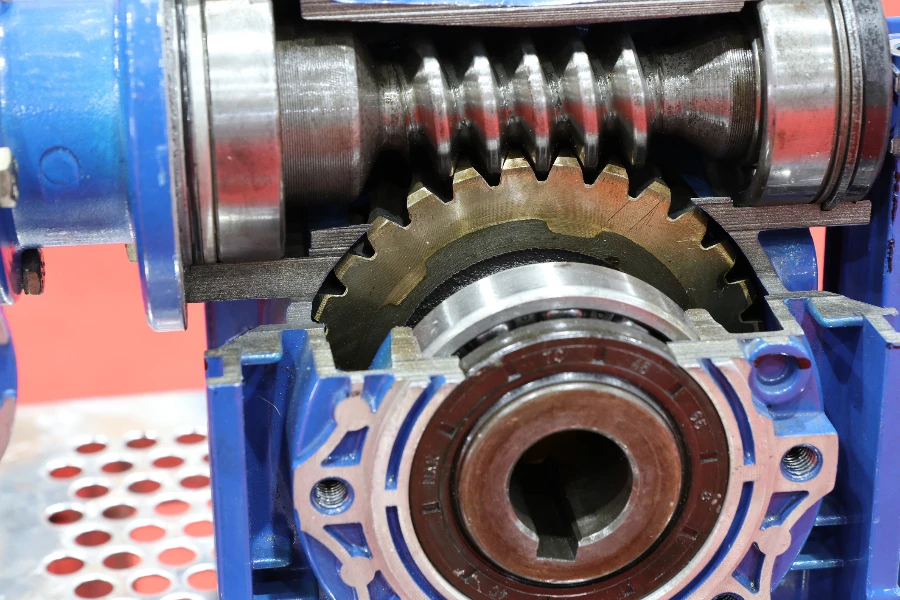
材料の選択
When choosing worm drive mechanics, the material of both the worm and worm gear is crucial. The material impacts durability, efficiency, and longevity. Common materials include cast iron, alloy steel, carbon steel, aluminum, brass, and plastic. Cast iron is durable and easy to manufacture, making it a popular choice. Alloy steel offers superior strength and corrosion resistance, suitable for high-stress applications. Carbon steel is cost-effective but prone to corrosion. Aluminum is lightweight and suitable for low inertia applications. Brass and plastic are used for corrosion resistance and quiet operation, respectively, but may not suit high-load applications.
Lead Angle and Efficiency
The lead angle of the worm significantly affects the efficiency of the worm drive. A high lead angle reduces frictional losses and heat generation, improving efficiency. Conversely, a low lead angle increases torque output but may result in higher friction and heat. For instance, a worm drive with a 20-degree lead angle may achieve around 80% efficiency, while a 5-degree lead angle might only reach 40-50% efficiency. The lead angle should balance torque and efficiency based on specific application needs.
Gear Ratio and Torque
Worm drives are known for high gear reduction and torque multiplication. The gear ratio, determined by the number of teeth on the worm gear relative to the number of threads on the worm, directly influences torque output and speed reduction. For example, a 50:1 ratio means the worm gear turns once for every 50 turns of the worm. This high reduction ratio is beneficial for applications requiring significant torque and precise control, such as lifting mechanisms and conveyors. However, higher ratios may result in lower efficiency due to increased friction.
潤滑とメンテナンス
Proper lubrication is essential for smooth operation and longevity of worm drives. The high contact stress and sliding action between the worm and worm gear generate significant heat and wear, necessitating effective lubrication. Lubricants with high viscosity and extreme pressure additives are recommended to reduce friction and wear. Regular maintenance, including checking lubricant levels and replacing worn components, is crucial to prevent premature failure and ensure optimal performance.
取り付けと位置合わせ
The mounting and alignment of worm drives are critical to their performance and lifespan. Misalignment can lead to uneven wear, increased friction, and potential failure. Worm gears must be mounted to ensure multiple points of contact between the worm and gear teeth to distribute the load evenly. Considerations include the gear center, bore diameter, and shaft diameter. Proper alignment tools and techniques should be used during installation to ensure correct meshing. The housing should be robust enough to maintain alignment under operating conditions.
Latest Technological Advancements in Worm Drive Mechanics
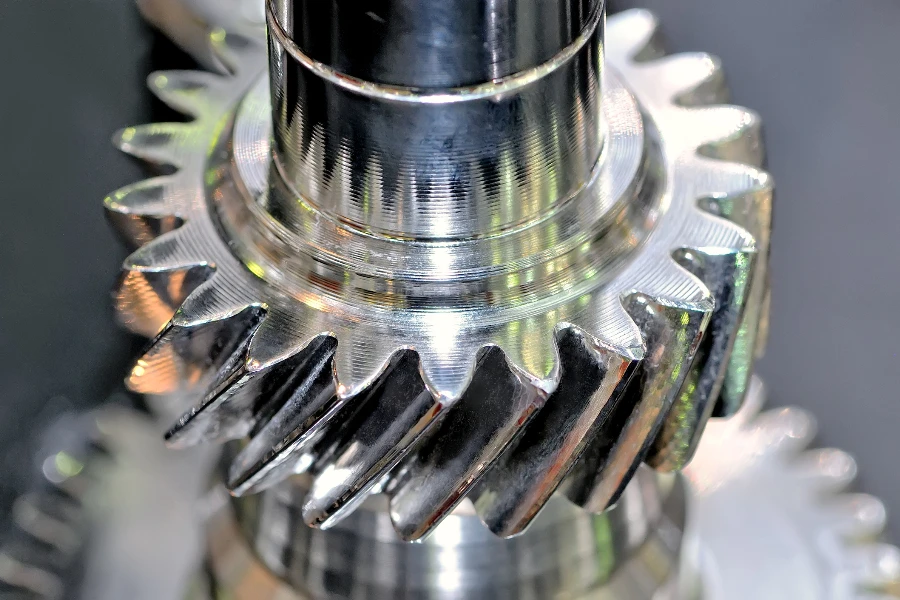
先端材料とコーティング
Advancements in materials science have led to new alloys and coatings that enhance the performance and durability of worm drives. Composite materials and advanced coatings such as diamond-like carbon (DLC) can significantly reduce friction and wear, extending the lifespan of the worm drive.
スマート潤滑システム
Innovations in lubrication technology have introduced smart lubrication systems that continuously monitor the condition of the lubricant and automatically dispense the appropriate amount. These systems help maintain optimal lubrication conditions, reducing maintenance requirements and preventing failures due to inadequate lubrication.
IoTと予測メンテナンスの統合
Integrating worm drives with the Internet of Things (IoT) and predictive maintenance technologies allows for real-time monitoring of performance parameters such as temperature, vibration, and load. This data can be used to predict potential failures and schedule maintenance proactively, reducing downtime and improving overall reliability.
アプリケーションと業界のユースケース
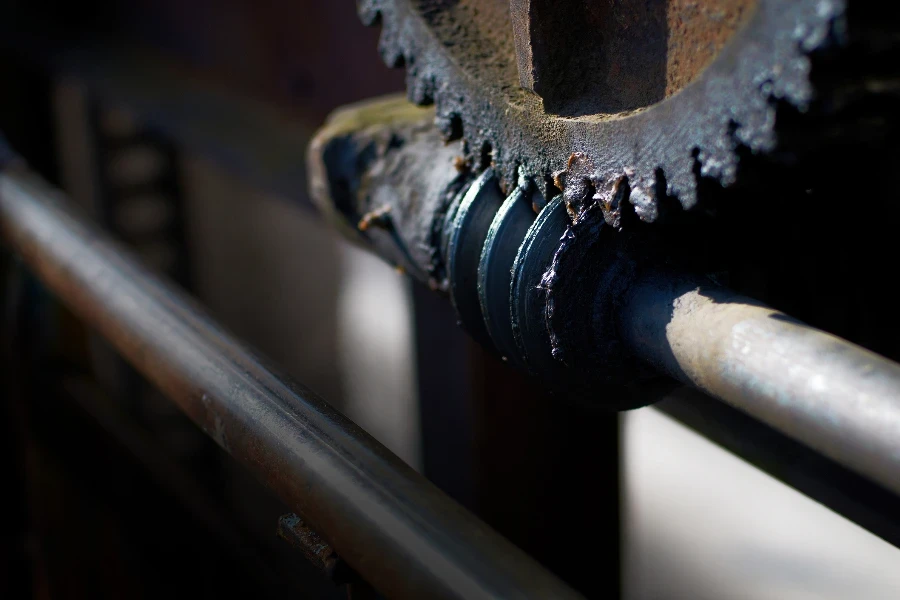
マテリアルハンドリングとコンベア
Worm drives are extensively used in material handling and conveyor systems due to their high torque and precise control capabilities. They are ideal for applications requiring smooth and quiet operation, such as in automated warehouses and manufacturing plants.
ロボットとオートメーション
In robotics and automation, worm drives provide the necessary torque and precision for various movements, including lifting, rotating, and positioning. Their compact design and high reduction ratios make them suitable for space-constrained applications.
自動車および航空宇宙
The automotive and aerospace industries utilize worm drives in various applications, including steering mechanisms, seat adjustments, and landing gear systems. The ability to provide high torque in a compact form factor makes worm drives an essential component in these industries.
業界標準への準拠の確保
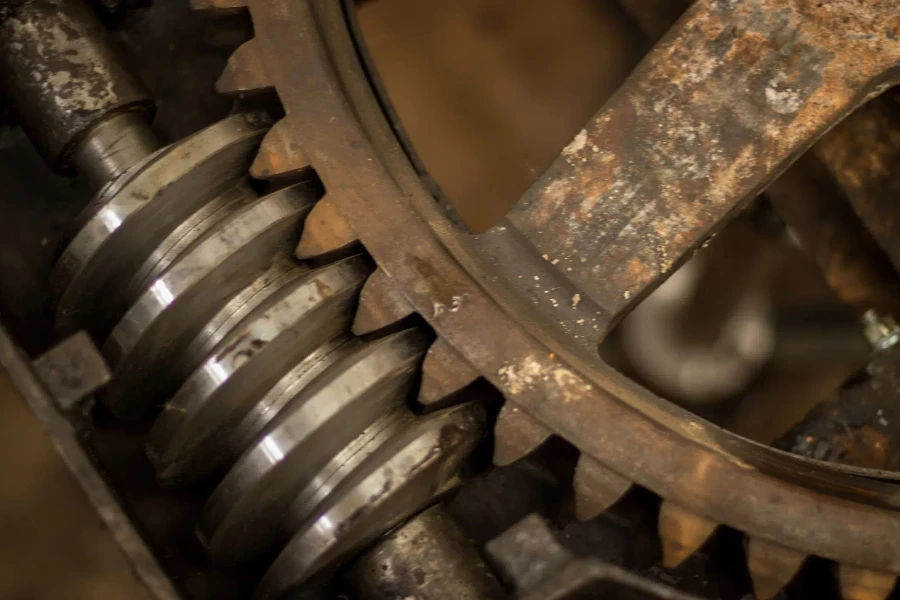
AGMA Standards
The American Gear Manufacturers Association (AGMA) provides standards for the design, manufacturing, and testing of worm gear sets. Compliance with AGMA standards ensures the reliability and performance of worm drives in various applications.
ISO認定書
ISO certifications, such as ISO 9001 for quality management and ISO 14001 for environmental management, are essential for manufacturers of worm drives. These certifications demonstrate a commitment to quality and sustainability, providing assurance to customers regarding the reliability and environmental impact of the products.
要点のまとめ
Selecting the right worm drive mechanics requires a thorough understanding of various factors, including material selection, lead angle and efficiency, gear ratio and torque, lubrication, and mounting. Keeping abreast of the latest technological advancements and ensuring compliance with industry standards are also crucial for optimal performance and reliability. By considering these factors, businesses can make informed decisions and achieve the desired outcomes in their applications.