In 2025, the plasma cutting table market is booming, driven by automation and digitalization trends. This article explores key selection factors, advanced features, and maintenance for professional buyers, ensuring informed decisions and enhanced inventory management.
Table of Contents:
-Market Overview of Plasma Cutting Table Industry
-In-Depth Analysis of the Plasma Cutting Table Market
-Key Factors When Selecting a Plasma Cutting Table
-Advanced Features and Technology in Plasma Cutting Tables
-Plasma Cutting Table Maintenance and Durability
-Plasma Cutting Table Applications
-Summary
Market Overview of Plasma Cutting Table Industry
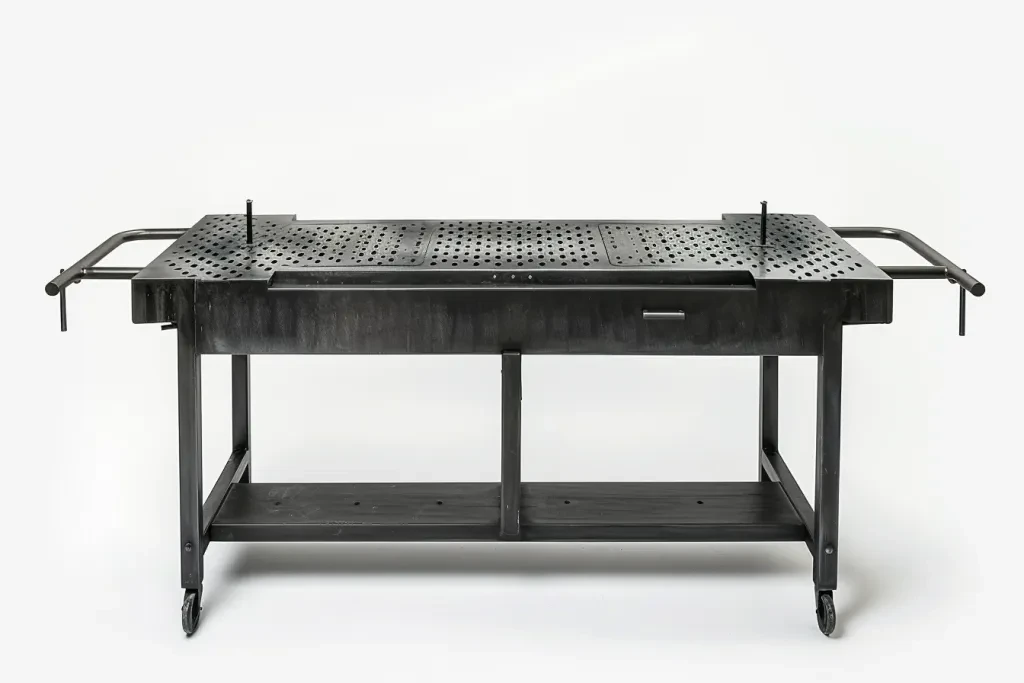
As of 2025, the global plasma cutting machine market has shown significant growth, reaching a valuation of USD 1.4 billion in 2023. This market is projected to grow at a CAGR of 4.61%, potentially reaching USD 2.1 billion by 2032. The wide adoption of plasma cutting tables across various industries, including automotive, construction, and metal fabrication, is a key driver of this expansion. The Asia-Pacific region, particularly China, Japan, and India, has emerged as the largest market due to rapid industrialization and infrastructure development.
Single flow plasma cutting machines dominate the product type category. In terms of control, mechanized systems hold the largest market share, reflecting a shift towards automation in manufacturing processes. Configuration-wise, 2D plasma cutting machines are most prevalent, catering to the demand for precise and efficient metal cutting solutions.
The automotive sector accounts for the majority of the market share, driven by the need for high-precision metal components. The aerospace and defense sectors also contribute significantly, leveraging plasma cutting technology for manufacturing complex parts. Additionally, the construction industry continues to adopt plasma cutting tables for structural applications, further propelling market growth.
In-Depth Analysis of the Plasma Cutting Table Market
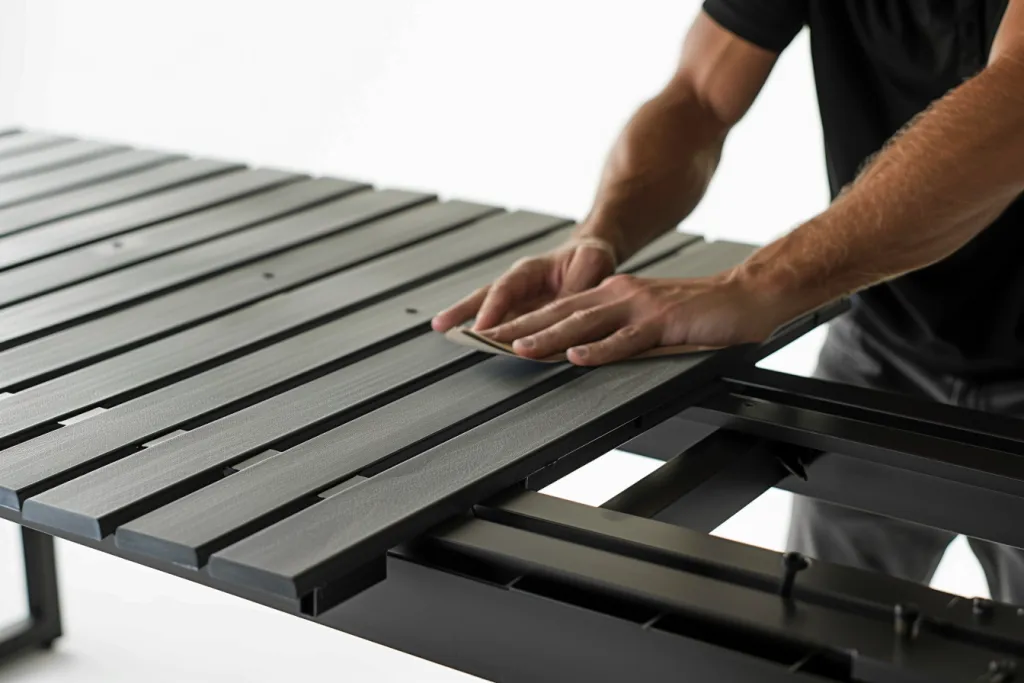
The plasma cutting table market is characterized by high precision and efficiency in cutting various metals, including steel, aluminum, and copper. The ability to handle thicker materials and produce clean, precise cuts has resulted in increased adoption across multiple industries.
Asia-Pacific leads in market size, driven by industrialization and the growth of the automotive and construction sectors. North America and Europe also hold significant shares, owing to technological advancements and the presence of major manufacturing hubs. Government investments in infrastructure and manufacturing are pivotal in shaping market trends.
Consumer behavior is shifting towards automation and digitalization, with a preference for CNC (Computer Numerical Control) and automated plasma cutting systems. These systems enhance productivity and reduce human error, aligning with the industry’s move towards smart manufacturing. Recent innovations include more efficient and accurate plasma cutting machines, integrating advanced software for better control and precision.
The product lifecycle of plasma cutting tables typically involves stages of introduction, growth, maturity, and decline. However, continuous technological advancements and the integration of digital solutions are extending the maturity phase, ensuring sustained demand. Social trends, such as the increasing focus on sustainability and eco-friendly manufacturing processes, are also influencing market growth. Plasma cutting machines, known for minimal waste production and reduced emissions, align with these trends.
Customer pain points primarily revolve around the high initial investment and maintenance costs associated with advanced plasma cutting systems. To address these concerns, manufacturers are focusing on offering cost-effective solutions and comprehensive after-sales services. Brand positioning strategies emphasize reliability, precision, and technological innovation, differentiating their products in a competitive market.
Niche markets within the plasma cutting table industry include DIY enthusiasts and small-scale metal workshops. These segments require affordable and user-friendly machines capable of handling various metal cutting tasks. Differentiation strategies for these markets involve offering compact, portable plasma cutting tables with easy-to-use interfaces and robust customer support.
Key Factors When Selecting a Plasma Cutting Table
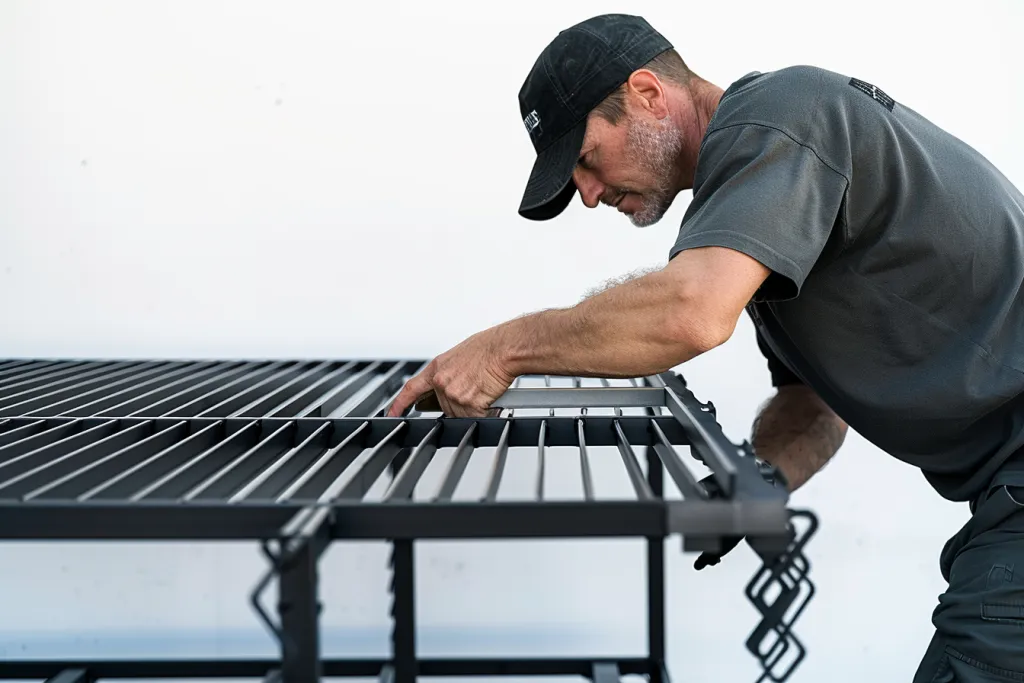
Choosing the right plasma cutting table is crucial for maximizing productivity and ensuring high-quality cuts. Here are the key factors to consider:
Material Thickness and Type
The thickness and type of material you plan to cut significantly influence the selection of a plasma cutting table. Higher amperage machines are better suited for thicker materials, while lower amperage machines provide better control for thinner materials. For instance, a machine with a 100-amp output can efficiently cut through steel plates up to 1 inch thick. In contrast, a 45-amp machine would be more appropriate for cutting thinner sheets of aluminum or stainless steel. Different materials such as carbon steel, stainless steel, aluminum, nickel, and titanium require specific settings and capabilities, so ensure the plasma table you choose can handle your most commonly used materials.
Cutting Speed and Precision
Cutting speed and precision are critical for operational efficiency and quality output. Plasma cutting tables with higher cutting speeds can significantly reduce production time, especially for large-scale operations. However, faster cutting speeds should not compromise the precision of the cuts. Modern plasma cutting tables equipped with CNC (Computer Numerical Control) systems offer precise control over the cutting process, ensuring clean and accurate cuts. For example, tables with a cutting speed of 500 inches per minute (IPM) are suitable for high-volume production environments, whereas slower speeds may be acceptable for detailed or intricate work.
Table Size and Workspace
The size of the plasma cutting table should match your workspace and the dimensions of the materials you will be cutting. Plasma tables come in various sizes, ranging from compact models for small workshops to large industrial tables for extensive manufacturing operations. A standard 4×4 or 4×8 foot table is ideal for small to medium-sized operations, providing ample space for most cutting tasks. Larger tables, such as 5×10 or 6×12 feet, are necessary for cutting larger sheets or handling multiple smaller pieces simultaneously. Ensure your workspace can accommodate the table size, including room for material handling and operator movement.
Power Supply and Energy Efficiency
The power supply of a plasma cutting table determines its cutting capabilities and operational costs. Plasma cutters typically require a three-phase power supply for industrial applications, ensuring consistent performance and the ability to cut thicker materials. Energy efficiency is another important consideration, as it impacts operating costs and environmental sustainability. Modern plasma cutting tables are designed to be more energy-efficient, utilizing advanced technologies such as inverter power supplies. These systems reduce power consumption and provide stable output, leading to lower energy bills and a smaller carbon footprint.
Safety Features and Compliance
Safety is paramount in any industrial setting. Plasma cutting tables operate at high temperatures and generate intense light and fumes, necessitating robust safety features. Look for tables equipped with safety sensors, such as those that prevent the arc from starting if the nozzle is not correctly positioned. Compliance with safety standards, such as BS EN 50192 for manual plasma cutting systems, ensures the equipment meets essential safety requirements. Additionally, consider tables with integrated fume extraction systems to maintain a clean and safe working environment by removing harmful fumes and particulate matter generated during the cutting process.
Advanced Features and Technology in Plasma Cutting Tables
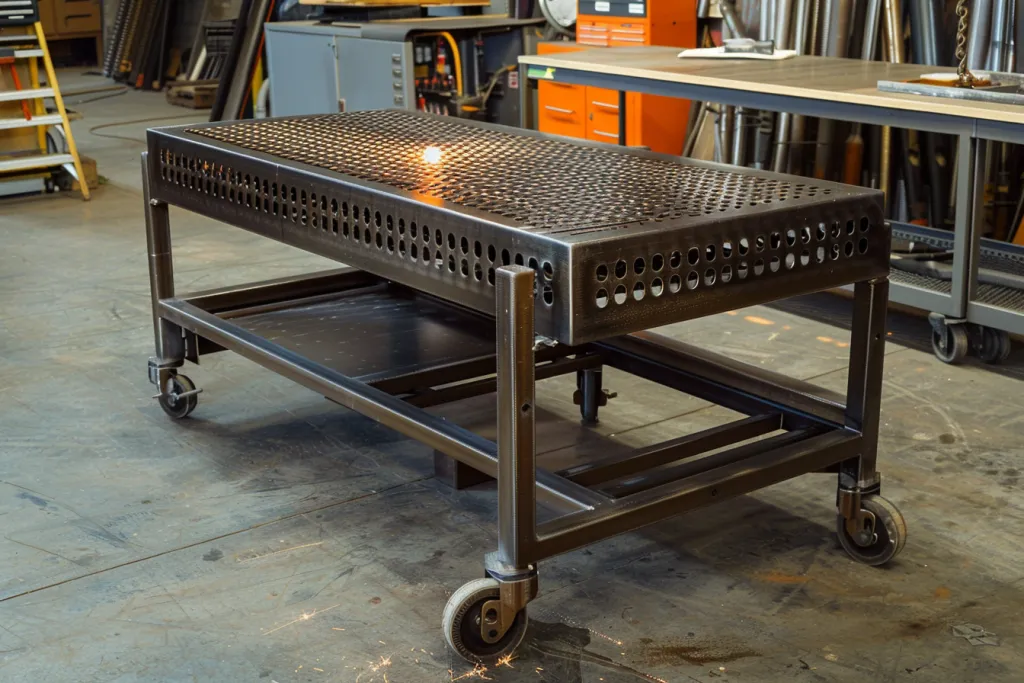
Plasma cutting technology has evolved significantly, incorporating various advanced features that enhance performance and usability.
CNC Functionality
CNC (Computer Numerical Control) technology revolutionizes plasma cutting by providing automated control over the cutting process. CNC plasma cutting tables can execute complex patterns and designs with high precision, making them ideal for detailed and repetitive tasks. These systems use pre-programmed software to control the movement of the cutting torch, ensuring consistent and accurate cuts. CNC plasma cutters can store multiple cutting programs, allowing operators to switch between tasks quickly and efficiently.
Touch Screen Controllers
Modern plasma cutting tables often feature touch screen controllers, providing a user-friendly interface for operators. These controllers simplify the setup and operation of the cutting table, allowing for easy adjustments to cutting parameters such as speed, power, and gas flow. Touch screen controllers can also display real-time data, such as cutting progress and system diagnostics, enabling operators to monitor performance and address issues promptly. This technology enhances the overall efficiency and ease of use of plasma cutting tables.
Torch Height Control
Maintaining the correct torch height is crucial for achieving high-quality cuts and prolonging the life of the consumables. Advanced plasma cutting tables are equipped with automatic torch height control systems that adjust the height of the torch in real-time based on the material’s surface. These systems use sensors to detect the distance between the torch and the workpiece, ensuring optimal cutting conditions. Automatic torch height control minimizes the risk of torch collisions and ensures consistent cut quality across the entire workpiece.
Motorized Lifters and Extended Stroke
Motorized lifters and extended stroke capabilities enhance the flexibility and range of plasma cutting tables. Motorized lifters allow for precise vertical adjustments of the cutting head, accommodating various material thicknesses and cutting angles. Extended stroke systems increase the vertical travel of the cutting head, enabling the table to handle larger and more complex workpieces. These features are particularly beneficial for cutting tubular or irregularly shaped materials, providing greater versatility in cutting applications.
Plasma Cutting Table Maintenance and Durability
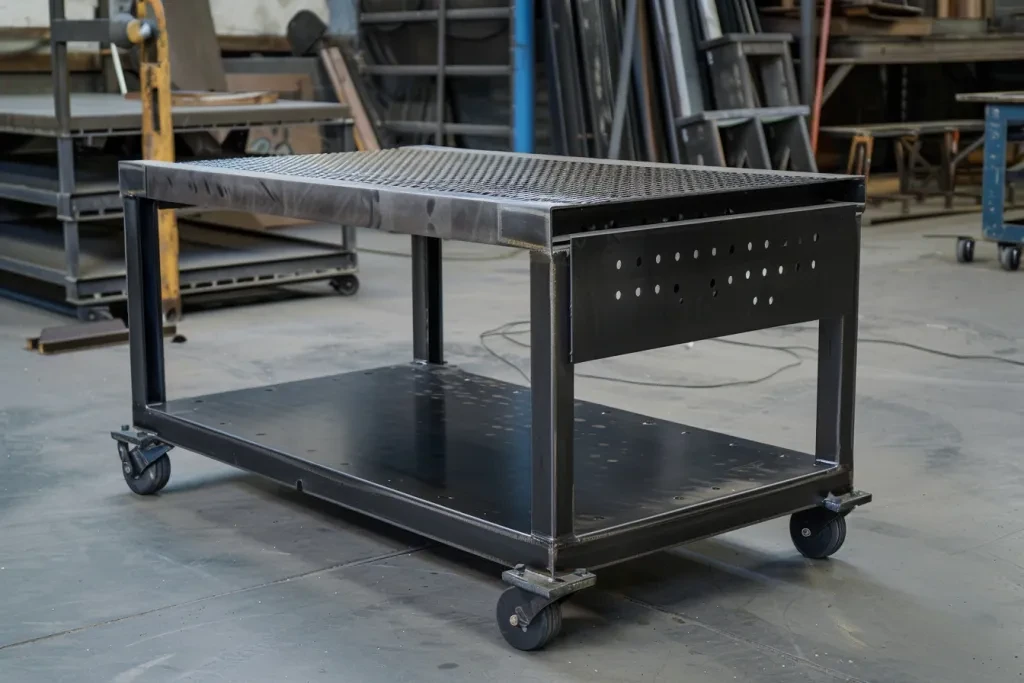
Regular maintenance is essential for ensuring the longevity and optimal performance of a plasma cutting table.
Consumable Management
Plasma cutting involves consumables such as electrodes, nozzles, and shields that wear out over time. Proper management and timely replacement of these consumables are crucial for maintaining cutting quality and preventing downtime. Using high-quality consumables from reputable manufacturers can extend the lifespan of the components and improve overall efficiency. Regular inspection and replacement of worn parts ensure consistent performance and reduce the risk of unexpected failures.
Table and Torch Maintenance
Keeping the cutting table and torch clean is vital for maintaining accuracy and preventing malfunctions. Regularly remove slag and debris from the cutting surface and torch components to ensure smooth operation. Lubricating moving parts and checking for any signs of wear or damage can prevent mechanical issues and extend the table’s lifespan. Follow the manufacturer’s maintenance guidelines and schedule regular servicing to keep the equipment in optimal condition.
Software and Firmware Updates
Plasma cutting tables with CNC functionality often rely on software and firmware to operate efficiently. Regular updates to the software and firmware ensure the system runs smoothly and incorporates the latest features and improvements. Manufacturers frequently release updates to address bugs, enhance performance, and add new capabilities. Keeping the system updated ensures the cutting table remains compatible with new technologies and maintains peak performance.
Plasma Cutting Table Applications
Plasma cutting tables are versatile tools used in various industries for cutting and shaping metal and other conductive materials.
Metal Fabrication
In metal fabrication, plasma cutting tables are used to create parts and components for various applications. The ability to cut through thick and thin materials with precision makes plasma cutters ideal for producing custom parts, structural components, and intricate designs.
Automotive and Aerospace
The automotive and aerospace industries rely on plasma cutting tables for manufacturing parts and components that require high precision and quality. Plasma cutting’s ability to handle different materials, including aluminum and stainless steel, makes it suitable for producing vehicle frames, engine components, and aircraft parts.
Construction and Infrastructure
Plasma cutting tables are used in the construction industry for cutting steel beams, girders, and other structural elements. The technology’s speed and accuracy enable efficient production of large-scale components used in buildings, bridges, and infrastructure projects.
Art and Design
Artists and designers use plasma cutting tables to create intricate metal sculptures, decorative panels, and custom signage. The precision and versatility of plasma cutting allow for the creation of detailed and unique designs that enhance aesthetic appeal.
Summary
Selecting the right plasma cutting table involves considering various factors such as material thickness, cutting speed, table size, power supply, and safety features. Advanced features like CNC functionality, touch screen controllers, and torch height control enhance performance and usability. Regular maintenance and consumable management ensure durability and optimal performance. Plasma cutting tables find applications in metal fabrication, automotive, aerospace, construction, and art industries, offering precision and versatility for various cutting tasks.