W 2025 r. rynek maszyn do wytaczania przeżywa rozkwit, napędzany postępem technologicznym i rosnącym popytem przemysłowym. Niniejszy artykuł zawiera dogłębną analizę kluczowych czynników wyboru, w tym specyfikę zastosowania, specyfikacje maszyn i kwestie kosztów. Oferuje on cenne wskazówki profesjonalnym nabywcom w podejmowaniu świadomych decyzji, zapewniając optymalną wydajność i rentowność.
Spis treści:
-Przegląd rynku maszyn do wytaczania
-Szczegółowe wprowadzenie i analiza rynku maszyn do wytaczania
-Kluczowe czynniki przy wyborze wytaczarki
-Innowacje w technologii maszyn wytaczających
-Rozważania o środowisku w eksploatacji maszyn wiertniczych
-Przyszłe trendy w technologii maszyn wiertniczych
-Podsumowanie
Przegląd rynku maszyn do wytaczania
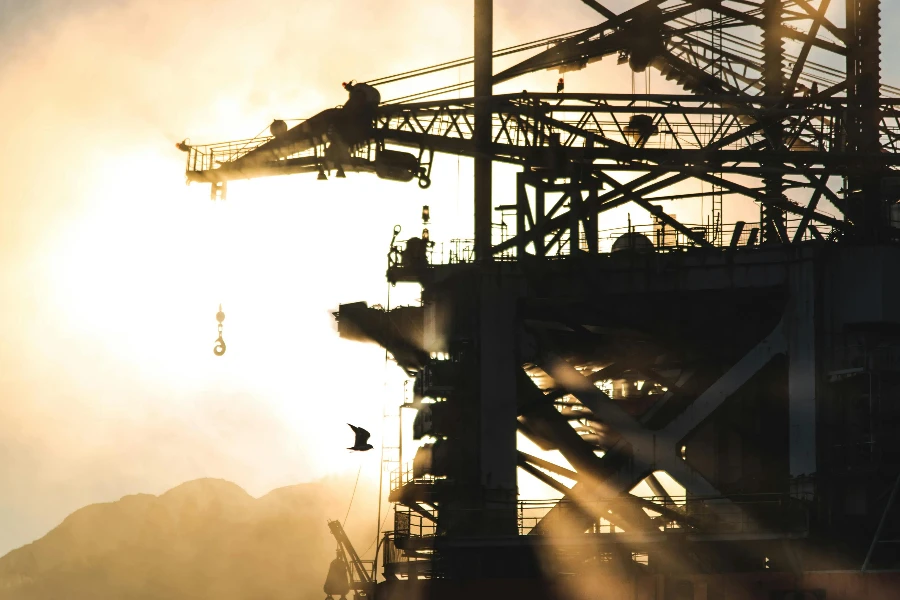
Globalny rynek maszyn do wytaczania odnotował znaczny wzrost w ostatnich latach. W 2023 r. rynek był wart około 4.4 mld USD i przewiduje się, że do 6.2 r. osiągnie wartość 2030 mld USD, rosnąc ze średniorocznym tempem wzrostu (CAGR) na poziomie 5.0%. Wzrost ten jest napędzany przez postęp w technologiach produkcyjnych i rosnący popyt ze strony takich branż jak motoryzacja, lotnictwo i maszyny ciężkie. Oczekuje się, że segment końcowego zastosowania transportu odnotuje największy wzrost, osiągając 2.9 mld USD do 2030 r. ze średniorocznym tempem wzrostu (CAGR) na poziomie 5.3%, podczas gdy segment maszyn ogólnych ma rosnąć ze średniorocznym tempem wzrostu (CAGR) na poziomie 4.4%.
Regionalnie rynek amerykański szacowano na 1.2 mld USD w 2023 r., a prognozuje się, że rynek chiński będzie rósł w imponującym tempie CAGR wynoszącym 7.6%, osiągając 1.4 mld USD do 2030 r. Inne znaczące rynki obejmują Japonię, Kanadę, Niemcy i szerszy region Azji i Pacyfiku, z których wszystkie powinny przyczynić się do ogólnego wzrostu rynku maszyn wiertniczych.
Szczegółowe wprowadzenie i analiza rynku maszyn do wytaczania
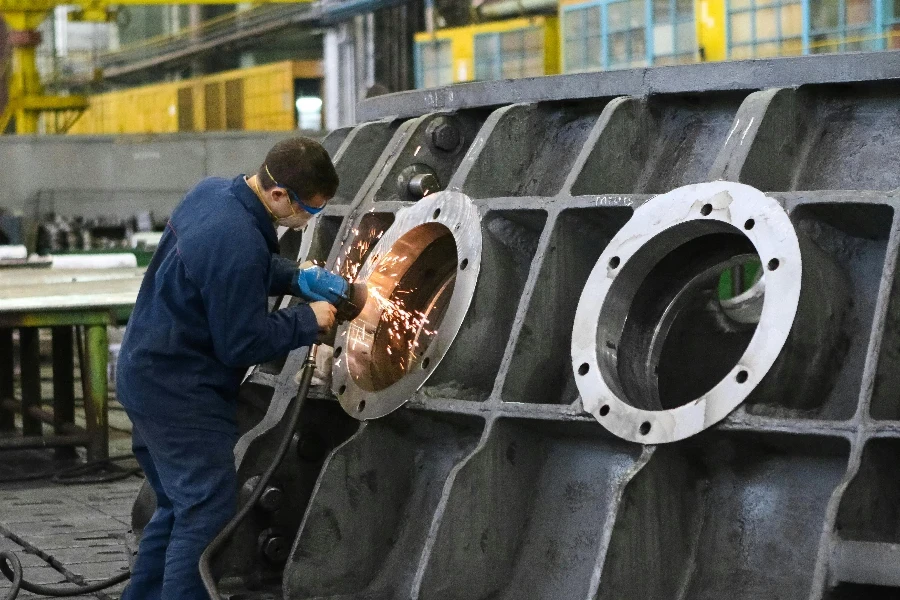
Maszyny do wytaczania są kluczowe w precyzyjnej obróbce, szczególnie w branżach wymagających wysokiej dokładności i gładkich wykończeń, takich jak motoryzacja, lotnictwo i maszyny ciężkie. Maszyny te są zaprojektowane do powiększania i wykańczania wstępnie wywierconych lub odlanych otworów z wysoką precyzją, zapewniając, że średnica, wykończenie powierzchni i tolerancja spełniają dokładne specyfikacje. Rynek jest podzielony na typy do wytaczania precyzyjnego i zgrubnego, z których każdy zaspokaja różne potrzeby w zależności od materiału i warunków cięcia.
Postęp technologiczny znacznie zwiększył wydajność i wszechstronność wytaczarek. Innowacje, takie jak zaawansowane powłoki i materiały na krawędzie skrawające, w tym diament polikrystaliczny (PCD) i sześcienny azotek boru (CBN), oferują doskonałą odporność na zużycie i dłuższą żywotność narzędzia. Ponadto sterowane cyfrowo głowice wytaczające umożliwiają regulację w czasie rzeczywistym podczas obróbki, zapewniając niezrównaną precyzję i redukując błędy. Integracja technologii czujników do konserwacji predykcyjnej dodatkowo zoptymalizowała proces obróbki i skróciła przestoje.
Pomimo tych postępów rynek maszyn do wiercenia stoi przed wyzwaniami. Utrzymanie dokładności w szerokim zakresie materiałów, zarządzanie generowaniem ciepła i reagowanie na trend miniaturyzacji w branżach takich jak elektronika i urządzenia medyczne to ciągłe problemy. Producenci badają zaawansowane techniki chłodzenia i opracowują bardziej wytrzymałe i wszechstronne narzędzia, aby sprostać tym wyzwaniom. Presja kosztów w produkcji również napędza potrzebę bardziej wydajnych maszyn do wiercenia, które mogą zapewnić wysoką wydajność przy jednoczesnym zminimalizowaniu przestojów i odpadów.
Kluczowe czynniki przy wyborze wytaczarki
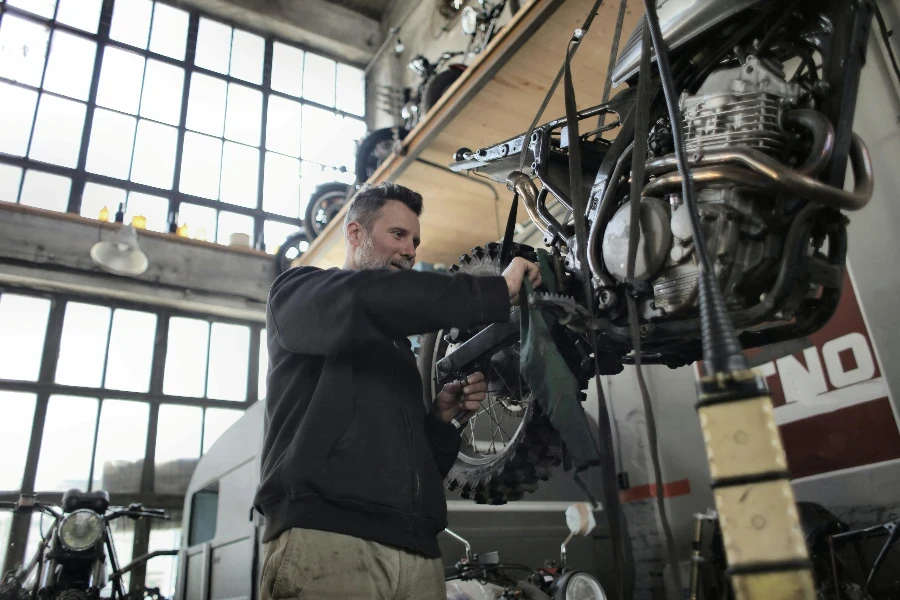
Specyfika aplikacji
Przy wyborze wytaczarki, pierwszym czynnikiem, który należy wziąć pod uwagę, jest konkretne zastosowanie, do którego będzie używana. Różne wytaczarki są zaprojektowane do wykonywania różnych zadań, takich jak precyzyjne wytaczanie, wytaczanie przyrządowe, wytaczanie tokarskie, wytaczanie pionowe i wytaczanie poziome. Na przykład, precyzyjne wytaczarki są idealne do produkcji wysoce dokładnych wewnętrznych powierzchni cylindrycznych, podczas gdy wytaczarki przyrządowe są odpowiednie do tworzenia otworów o precyzyjnych wymiarach i położeniach. Zrozumienie konkretnych wymagań zadania pomoże w wyborze odpowiedniego typu maszyny.
Precyzyjne maszyny do wytaczania zazwyczaj wykorzystują operacje cięcia jednopunktowego, aby osiągnąć dokładność w granicach ±0.0001 cala, co czyni je odpowiednimi do zadań wymagających wysokiej precyzji, takich jak wykańczanie wewnętrznych powierzchni łożysk. Natomiast poziome maszyny do wytaczania, które mogą obsługiwać większe elementy obrabiane i oferują wielofunkcyjne możliwości, takie jak frezowanie i wiercenie, są lepsze do ciężkich zastosowań wymagających wszechstronności.
Złożoność przedmiotu obrabianego, wymagane tolerancje i obrabiany materiał są krytycznymi czynnikami. Na przykład materiały o wyższej twardości, takie jak stal nierdzewna, mogą wymagać maszyn wyposażonych w narzędzia węglikowe lub diamentowe w celu zachowania precyzji i wydajności.
Dane techniczne maszyny
Specyfikacje techniczne wytaczarki są niezbędne, aby zapewnić, że spełni ona wymagania Twojej aplikacji. Kluczowe specyfikacje obejmują prędkość wrzeciona, szybkość posuwu, prędkość skrawania i moc maszyny. Prędkość wrzeciona, mierzona w obrotach na minutę (RPM), określa, jak szybko obraca się narzędzie skrawające i może mieć wpływ na jakość wykończenia i wydajność procesu obróbki. Wyższe prędkości wrzeciona są zazwyczaj wymagane w przypadku drobniejszych wykończeń i twardszych materiałów.
Prędkość posuwu, często mierzona w calach na minutę (IPM), wskazuje prędkość, z jaką narzędzie skrawające przesuwa się w materiale. Właściwa równowaga między prędkością wrzeciona a prędkością posuwu jest kluczowa, aby uniknąć zużycia narzędzia i uzyskać pożądane wykończenie powierzchni. Prędkość skrawania, prędkość, z jaką ostrze narzędzia przesuwa się po powierzchni przedmiotu obrabianego, również odgrywa znaczącą rolę w określaniu wydajności i jakości procesu rozwiercania.
Wymagania dotyczące mocy maszyny, zwykle określane w koniach mechanicznych (HP), powinny być zgodne z szybkością usuwania materiału i twardością obrabianego materiału. Na przykład, maszyny do wiercenia pracujące z materiałami takimi jak stal nierdzewna i żeliwo, które mają wyższe wymagania dotyczące mocy jednostkowej, będą potrzebować mocniejszych silników, aby utrzymać wydajność.
Tolerancja i precyzja
Tolerancja i precyzja są kluczowymi czynnikami przy wyborze wytaczarki, szczególnie w zastosowaniach wymagających wysokiej dokładności. Tolerancja wytaczarki odnosi się do dopuszczalnego odchylenia od określonych wymiarów, które może się różnić w zależności od rodzaju maszyny i zastosowania. Na przykład precyzyjne wytaczarki mogą osiągać tolerancje tak ścisłe, jak ±0.0001 cala, co czyni je odpowiednimi do zastosowań, w których dokładność wymiarowa ma pierwszorzędne znaczenie.
Warunki środowiskowe, geometria narzędzia oraz wyrównanie komponentów i osprzętu maszyny również wpływają na precyzję procesu rozwiercania. Stosowanie płynów obróbkowych może pomóc utrzymać temperaturę narzędzia, zmniejszyć zużycie i umożliwić wyższe prędkości skrawania i posuwy, zwiększając tym samym precyzję.
Ponadto sztywność maszyny, przedmiotu obrabianego i ustawienia narzędzia ma kluczowe znaczenie dla zachowania dokładności podczas procesu rozwiercania. Maszyny o solidnej konstrukcji i wysokiej jakości komponentach są mniej narażone na ugięcie lub drgania, które mogą wpłynąć na precyzję.
Kompatybilność materiałowa
Zgodność wytaczarki z różnymi materiałami to kolejny ważny czynnik. Narzędzia do wytaczania są zazwyczaj wykonane ze stali szybkotnącej (HSS), węglika, ceramiki lub diamentów, z których każdy nadaje się do różnych materiałów i zastosowań. Na przykład narzędzia węglikowe i diamentowe są preferowane do obróbki twardych materiałów, takich jak stal nierdzewna, podczas gdy narzędzia HSS nadają się do miękkich materiałów, takich jak aluminium i mosiądz.
Zrozumienie właściwości materiału, takich jak twardość i obrabialność, jest niezbędne do wyboru odpowiedniej maszyny i narzędzi do wytaczania. Na przykład materiały o wysokiej twardości, takie jak żeliwo i stal nierdzewna, wymagają narzędzi o wyższej odporności na zużycie i prędkości skrawania, aby zachować wydajność i precyzję.
Ponadto wybór płynu obróbkowego może mieć wpływ na proces obróbki, szczególnie podczas pracy z materiałami generującymi znaczną ilość ciepła. Płyny obróbkowe pomagają zmniejszyć zużycie narzędzi, poprawić wykończenie powierzchni i zwiększyć prędkość skrawania, co czyni je kluczowym elementem operacji rozwiercania.
Koszt i budżet
Na koniec należy wziąć pod uwagę koszt i budżet na zakup wytaczarki. Wytaczarki różnią się znacznie ceną w zależności od rodzaju, specyfikacji i funkcji. Zautomatyzowane i sterowane CNC wytaczarki, które oferują większą precyzję i wydajność, są zazwyczaj droższe niż maszyny ręczne lub półautomatyczne.
Inwestycja w maszynę wiertniczą powinna być dostosowana do oczekiwanego zwrotu z inwestycji (ROI) i konkretnych potrzeb operacji. W przypadku operacji na małą skalę lub rzadziej wykonywanych może wystarczyć tańsza maszyna z podstawowymi funkcjami. Jednak w przypadku produkcji wielkoseryjnej lub zastosowań wymagających wysokiej precyzji inwestycja w bardziej zaawansowaną i droższą maszynę może skutkować długoterminowymi oszczędnościami kosztów dzięki zwiększonej wydajności i skróceniu przestojów.
Koszty konserwacji, wymiany narzędzi i zużycia energii również powinny być uwzględnione w ogólnym budżecie. Maszyny o wyższej efektywności energetycznej i niższych wymaganiach konserwacyjnych mogą znacznie obniżyć koszty operacyjne w czasie.
Innowacje w technologii maszyn wytaczających
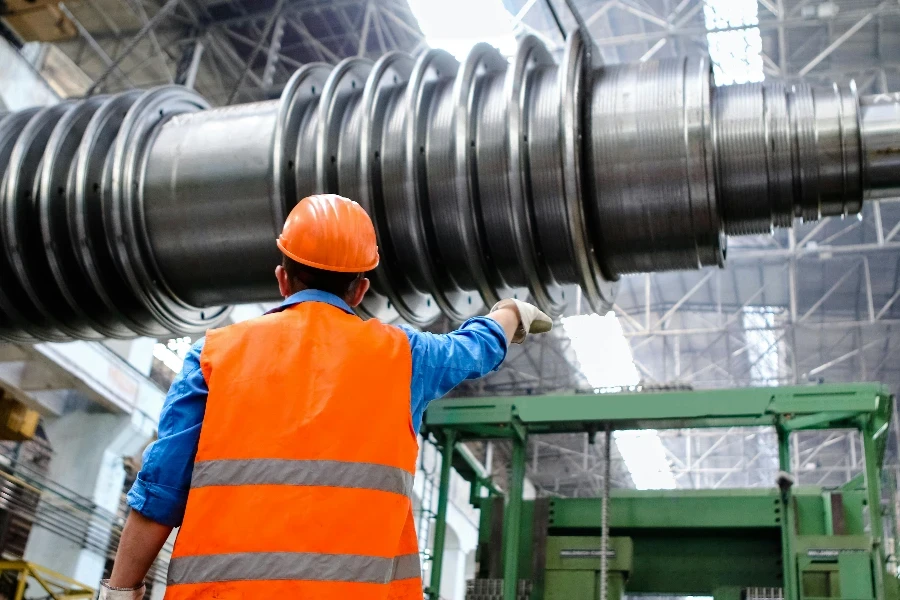
Integracja CNC
Integracja technologii komputerowego sterowania numerycznego (CNC) w wytaczarkach zrewolucjonizowała branżę, zwiększając precyzję, wydajność i automatyzację. Wytaczarki CNC są programowane przy użyciu kodu G, co pozwala na precyzyjną kontrolę nad ruchem, prędkością i szybkością posuwu narzędzia skrawającego. Technologia ta umożliwia wykonywanie złożonych i powtarzalnych zadań przy minimalnej ingerencji człowieka, zmniejszając prawdopodobieństwo błędów i zwiększając produktywność.
Maszyny do wytaczania CNC mogą być wyposażone w zaawansowane funkcje, takie jak automatyczne zmieniacze narzędzi, które umożliwiają użycie wielu narzędzi w jednej operacji bez ręcznej interwencji. Ta możliwość jest szczególnie korzystna w przypadku zastosowań wymagających różnych narzędzi skrawających na różnych etapach procesu wytaczania, takich jak obróbka zgrubna i wykańczająca.
Ponadto technologia CNC ułatwia korzystanie z oprogramowania symulacyjnego do modelowania procesu rozwiercania przed faktyczną obróbką, identyfikując potencjalne problemy i optymalizując parametry w celu zwiększenia wydajności i dokładności. Ta zdolność predykcyjna skraca czas konfiguracji i minimalizuje marnotrawstwo materiałów, przyczyniając się do oszczędności kosztów i zrównoważonego rozwoju środowiska.
Zaawansowane materiały narzędziowe
Rozwój zaawansowanych materiałów narzędziowych znacząco wpłynął na wydajność i trwałość wytaczarek. Materiały o wysokiej wydajności, takie jak polikrystaliczny diament (PCD) i sześcienny azotek boru (CBN), oferują wyższą twardość i odporność na zużycie w porównaniu z tradycyjnymi narzędziami HSS i węglikowymi. Materiały te umożliwiają wyższe prędkości skrawania, dłuższą żywotność narzędzia i lepsze wykończenie powierzchni, szczególnie podczas obróbki twardych i ściernych materiałów.
Narzędzia PCD są idealne do materiałów nieżelaznych, takich jak aluminium i kompozyty, zapewniając wysoką precyzję i wydłużoną żywotność narzędzia. Narzędzia CBN są natomiast odpowiednie do materiałów żelaznych, takich jak hartowana stal i żeliwo, oferując doskonałą stabilność termiczną i odporność na zużycie.
Zastosowanie zaawansowanych powłok, takich jak azotek tytanu (TiN) i tlenek glinu (Al2O3), dodatkowo zwiększa wydajność narzędzia poprzez redukcję tarcia i generowania ciepła podczas procesu cięcia. Powłoki te poprawiają odprowadzanie wiórów, zmniejszają zużycie narzędzia i umożliwiają wyższe prędkości cięcia, co przekłada się na zwiększoną produktywność i oszczędności kosztów.
Automatyka i robotyka
Automatyzacja i robotyka odgrywają coraz ważniejszą rolę w przemyśle maszyn wiertniczych, zwiększając wydajność, precyzję i bezpieczeństwo. Zautomatyzowane maszyny wiertnicze mogą wykonywać złożone zadania przy minimalnej ingerencji człowieka, zmniejszając koszty pracy i ryzyko błędów. Systemy robotyczne można integrować z maszynami wiertniczymi w celu automatyzacji obsługi materiałów, wymiany narzędzi i kontroli jakości, co jeszcze bardziej usprawnia proces produkcyjny.
Na przykład ramiona robota mogą ładować i rozładowywać elementy obrabiane, dokładnie je pozycjonować na maszynie i wykonywać operacje wtórne, takie jak gratowanie i czyszczenie. Ten poziom automatyzacji nie tylko zwiększa produktywność, ale także poprawia bezpieczeństwo w miejscu pracy, zmniejszając potrzebę ręcznego przenoszenia ciężkich i niebezpiecznych materiałów.
Systemy robotyczne mogą być również wyposażone w zaawansowane czujniki i algorytmy uczenia maszynowego, aby monitorować proces rozwiercania w czasie rzeczywistym, wykrywać anomalie i wprowadzać zmiany w celu optymalizacji wydajności. Ta możliwość zwiększa ogólną wydajność i niezawodność procesu obróbki, zmniejszając przestoje i koszty konserwacji.
Zagadnienia środowiskowe w eksploatacji maszyn wiertniczych
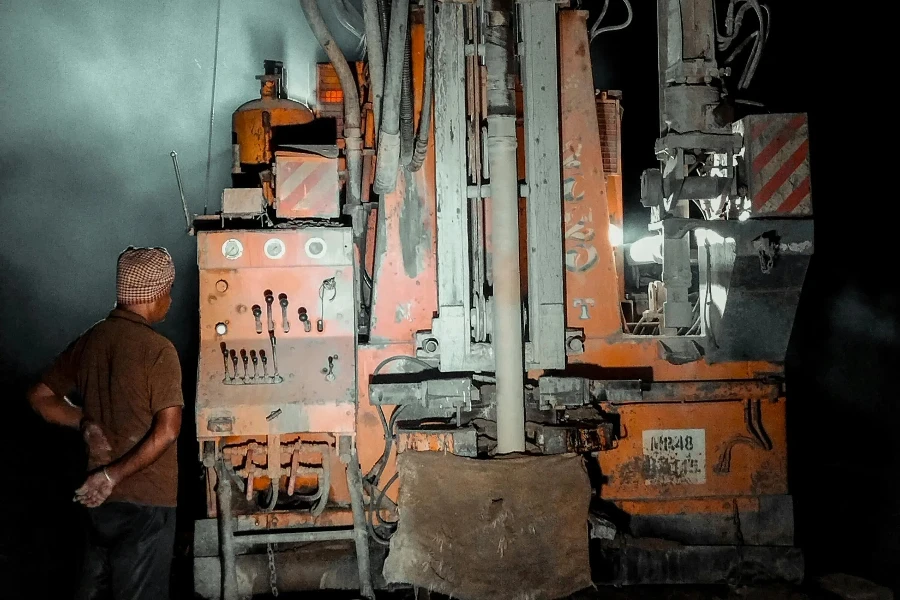
Efektywności energetycznej
Efektywność energetyczna jest krytycznym czynnikiem w nowoczesnych operacjach wiertniczych, napędzanym potrzebą redukcji kosztów operacyjnych i wpływu na środowisko. Postęp w technologii silników, takich jak wysokowydajne silniki elektryczne i napędy o zmiennej częstotliwości (VFD), znacznie poprawił efektywność energetyczną wiertarek. Technologie te umożliwiają precyzyjną kontrolę prędkości i momentu obrotowego silnika, zmniejszając zużycie energii i optymalizując wydajność.
Ponadto wykorzystanie energooszczędnych komponentów, takich jak oświetlenie LED i elektronika o niskim poborze mocy, dodatkowo przyczynia się do ogólnych oszczędności energii. Wdrożenie systemów zarządzania energią w celu monitorowania i kontrolowania zużycia energii w czasie rzeczywistym może pomóc w identyfikacji nieefektywności i wdrożeniu środków naprawczych, co skutkuje znacznymi oszczędnościami kosztów i zmniejszeniem śladu węglowego.
Redukcja odpadów
Redukcja odpadów to kolejny ważny aspekt zrównoważonych operacji maszyn wiertniczych. Efektywne wykorzystanie materiałów i zoptymalizowane procesy obróbki mogą zminimalizować odpady materiałowe i zmniejszyć wpływ produkcji na środowisko. Zaawansowane oprogramowanie symulacyjne i technologia CNC umożliwiają precyzyjną kontrolę procesu wiercenia, zmniejszając liczbę odpadów i poprawiając wydajność materiałów.
Recykling i ponowne wykorzystanie płynów do cięcia, wiórów i innych materiałów odpadowych może również przyczynić się do redukcji odpadów. Wdrożenie systemów zamkniętych do zarządzania płynem do cięcia i recyklingu wiórów może zminimalizować koszty utylizacji odpadów i zmniejszyć wpływ operacji obróbki na środowisko.
Kontrola emisji
Kontrola emisji z operacji maszyn wiertniczych jest niezbędna do utrzymania bezpiecznego i przyjaznego dla środowiska miejsca pracy. Zastosowanie zaawansowanych systemów filtracji, takich jak kolektory mgły i oczyszczacze powietrza, może skutecznie wychwytywać i usuwać zanieczyszczenia unoszące się w powietrzu, w tym mgłę olejową, opary chłodziwa i cząstki stałe. Systemy te pomagają utrzymać jakość powietrza i są zgodne z przepisami dotyczącymi ochrony środowiska, chroniąc zdrowie pracowników i okolicznej społeczności.
Ponadto wybór przyjaznych dla środowiska płynów do cięcia i środków smarnych może zmniejszyć szkodliwe emisje i poprawić bezpieczeństwo w miejscu pracy. Płyny do cięcia na bazie wody i biodegradowalne oferują bezpieczniejszą i bardziej zrównoważoną alternatywę dla tradycyjnych płynów na bazie oleju, minimalizując wpływ operacji obróbki na środowisko.
Przyszłe trendy w technologii maszyn wiertniczych
Inteligentna produkcja
Rozwój Przemysłu 4.0 i inteligentnej produkcji ma przekształcić branżę maszyn do wytaczania, a zwiększona łączność, analiza danych i automatyzacja napędzają poprawę wydajności i precyzji. Inteligentne maszyny do wytaczania wyposażone w czujniki i łączność IoT mogą zbierać i analizować dane w czasie rzeczywistym, zapewniając cenne informacje na temat wydajności maszyny, zużycia narzędzi i parametrów procesu.
To podejście oparte na danych umożliwia konserwację predykcyjną, skracając przestoje i wydłużając żywotność maszyn i narzędzi. Poprzez identyfikację potencjalnych problemów, zanim doprowadzą one do awarii maszyn, producenci mogą optymalizować harmonogramy konserwacji i zmniejszać ryzyko nieoczekiwanych awarii, poprawiając ogólną produktywność i efektywność kosztową.
Integracja wytwarzania przyrostowego
Integracja wytwarzania addytywnego (AM) z tradycyjnymi procesami rozwiercania oferuje nowe możliwości produkcji i dostosowywania złożonych części. Maszyny hybrydowe, które łączą możliwości wytwarzania addytywnego i subtraktywnego, mogą wytwarzać skomplikowane geometrie i cechy wewnętrzne, które są trudne lub niemożliwe do osiągnięcia przy użyciu samej obróbki konwencjonalnej.
Produkcja addytywna umożliwia tworzenie części o kształcie zbliżonym do kształtu netto, co zmniejsza ilość odpadów materiałowych i minimalizuje potrzebę rozległej obróbki. Łącząc AM z precyzyjnym rozwiercaniem, producenci mogą uzyskać wysokiej jakości wykończenia i ścisłe tolerancje w przypadku złożonych części, rozszerzając zakres zastosowań i poprawiając ogólną wydajność.
Zrównoważony rozwój i gospodarka o obiegu zamkniętym
Zrównoważony rozwój i gospodarka o obiegu zamkniętym stają się coraz ważniejsze w przemyśle wytwórczym, napędzając rozwój bardziej przyjaznych dla środowiska technologii maszyn wiertniczych. Producenci skupiają się na redukcji zużycia energii, minimalizacji odpadów i promowaniu ponownego użycia i recyklingu materiałów.
Wdrożenie zrównoważonych praktyk, takich jak korzystanie z odnawialnych źródeł energii, wdrażanie zamkniętych systemów zarządzania płynem obróbkowym i projektowanie maszyn w sposób umożliwiający łatwy demontaż i recykling, odegra kluczową rolę w ograniczeniu wpływu eksploatacji maszyn wiertniczych na środowisko.
Owijanie w górę
Podsumowując, wybór odpowiedniej wytaczarki wymaga starannego rozważenia specyfiki zastosowania, specyfikacji maszyny, tolerancji i precyzji, kompatybilności materiałów i kosztów. Postęp technologiczny, taki jak integracja CNC, zaawansowane materiały narzędziowe i automatyzacja, przyczyniają się do poprawy wydajności, precyzji i zrównoważonego rozwoju. Względy środowiskowe, w tym efektywność energetyczna, redukcja odpadów i kontrola emisji, stają się coraz ważniejsze w przypadku nowoczesnych operacji wytaczarek. Przyszłe trendy, takie jak inteligentna produkcja, integracja produkcji addytywnej i zrównoważony rozwój, będą nadal kształtować branżę, oferując nowe możliwości i wyzwania dla producentów.