O mercado de engrenagens de roda sem-fim está evoluindo dinamicamente, com avanços recentes em materiais e tecnologias digitais. Este artigo se aprofunda em aspectos críticos da seleção de engrenagens de roda sem-fim, oferecendo insights valiosos para compradores profissionais tomarem decisões informadas. Ao entender fatores-chave como seleção de material, geometria de design e eficiência, os compradores podem garantir que estocam produtos confiáveis e de alta qualidade.
Sumário:
– Visão geral do mercado de engrenagens de roda sem-fim
– Análise aprofundada do mercado de engrenagens de roda sem-fim
– Fatores-chave na seleção de engrenagens de roda sem-fim
– Aplicações e inovações avançadas em engrenagens de roda sem-fim
- Pensamentos finais
Visão geral do mercado de engrenagens de roda sem-fim
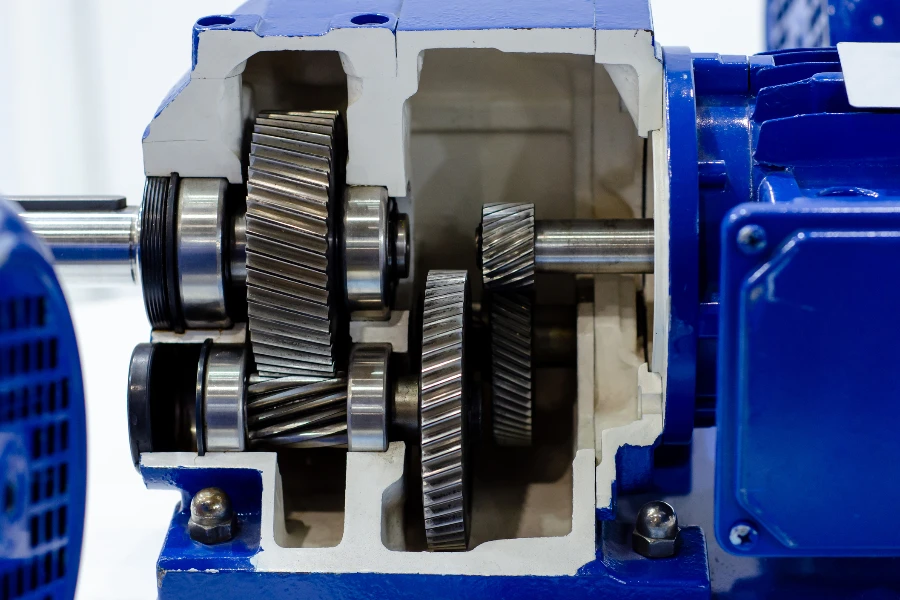
O mercado global de engrenagens de roda sem-fim deve experimentar um crescimento substancial nos próximos anos. O mercado de fabricação de engrenagens, que inclui engrenagens sem-fim, atingiu aproximadamente US$ 80 bilhões em 2023. As previsões preveem que esse mercado se expandirá para US$ 131.4 bilhões até 2032, com uma taxa de crescimento anual composta (CAGR) de 5.7% de 2023 a 2032. Esse crescimento é alimentado pela crescente demanda por engrenagens de alto desempenho em vários setores, incluindo automotivo, automação industrial e energia renovável.
Engrenagens sem-fim são valorizadas por suas altas taxas de redução e multiplicação de torque em uma forma compacta. Elas são amplamente utilizadas em aplicações que exigem redução significativa de velocidade e alto torque, como sistemas de transporte, elevadores e maquinário pesado. A região Ásia-Pacífico lidera o mercado de fabricação de engrenagens devido à sua forte base industrial e rápida adoção de tecnologias de automação. América do Norte e Europa também detêm fatias de mercado significativas, impulsionadas por avanços nos processos de fabricação e foco em eficiência energética.
Análise aprofundada do mercado de engrenagens de roda sem-fim
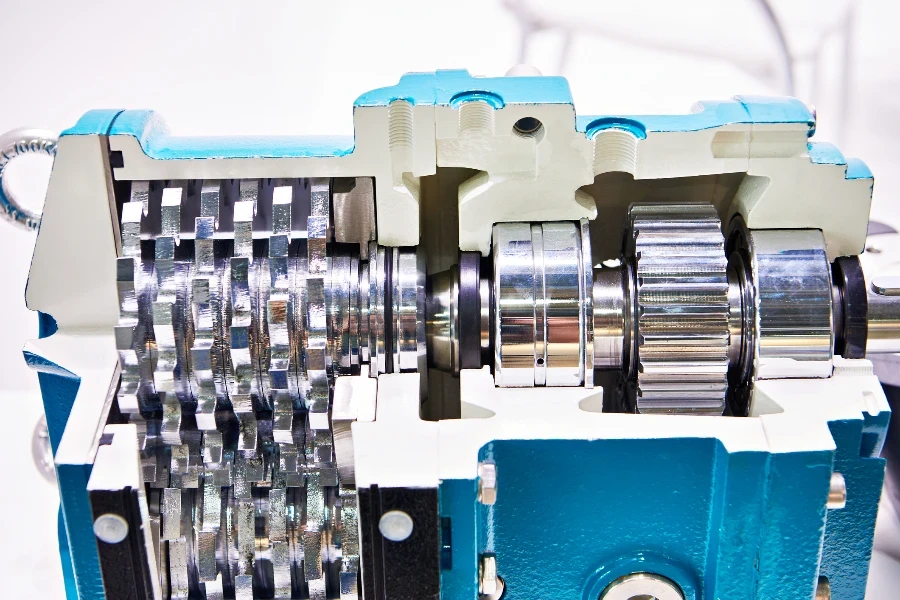
Engrenagens de roda sem-fim são componentes cruciais em vários sistemas mecânicos, conhecidos por atingir alto torque e redução significativa de velocidade. Essas engrenagens consistem em um sem-fim (um componente semelhante a um parafuso) e uma roda sem-fim (uma engrenagem engrenada com o sem-fim), permitindo uma operação suave e silenciosa. O mercado de engrenagens de roda sem-fim é impulsionado por sua ampla aplicação em indústrias como automotiva, máquinas industriais e energia renovável.
Principais benchmarks de desempenho
Engrenagens sem-fim são eficientes e confiáveis na transmissão de potência e torque. Os principais benchmarks de desempenho incluem alta capacidade de carga, controle preciso de velocidade e folga mínima. Essas engrenagens são projetadas para operar sob cargas pesadas, tornando-as adequadas para aplicações como movimentação de materiais, elevadores e máquinas pesadas. Além disso, o recurso de autotravamento das engrenagens sem-fim aumenta a segurança em aplicações onde o movimento reverso deve ser evitado.
Dinâmica de participação de mercado e mudanças no comportamento do consumidor
A indústria automotiva detém uma fatia significativa do mercado de engrenagens de roda sem-fim, impulsionada pelo aumento da produção de veículos e pela demanda por transmissão de energia eficiente. A automação industrial e a robótica também contribuem para o crescimento do mercado, pois as engrenagens sem-fim são essenciais para o controle preciso do movimento em sistemas automatizados. Os consumidores estão mudando para produtos duráveis e com eficiência energética, levando os fabricantes a desenvolver engrenagens sem-fim de alto desempenho com materiais e revestimentos avançados.
Inovações Recentes e Digitalização
Inovações recentes na tecnologia de engrenagens sem-fim incluem o uso de materiais avançados como aços de liga e compostos, que aumentam a resistência e a durabilidade das engrenagens. A integração de tecnologias digitais, como manutenção preditiva e sistemas de monitoramento habilitados para IoT, está revolucionando o mercado de engrenagens sem-fim. Esses avanços permitem o monitoramento em tempo real do desempenho das engrenagens, reduzindo o tempo de inatividade e os custos de manutenção.
Estágios do ciclo de vida do produto e preferências do canal de distribuição
Engrenagens sem-fim normalmente passam por vários estágios no ciclo de vida do produto: design, fabricação, teste e implementação. A fase de design envolve a especificação das dimensões da engrenagem, perfis de dentes e seleção de material para atender aos requisitos da aplicação. Durante a fabricação, processos como fresagem, modelagem e retificação atingem a precisão e o acabamento desejados da engrenagem. Testes rigorosos garantem que as engrenagens atendam aos padrões de desempenho antes da implantação.
Os canais de distribuição para engrenagens sem-fim incluem vendas diretas para OEMs (fabricantes de equipamentos originais), distribuidores e plataformas online. Os OEMs preferem vendas diretas para soluções de engrenagens personalizadas, enquanto os distribuidores oferecem uma ampla gama de engrenagens padrão para vários setores. A ascensão das plataformas de comércio eletrônico também facilitou a aquisição fácil de engrenagens sem-fim, atendendo à crescente demanda de pequenas e médias empresas.
Pontos problemáticos do cliente e estratégias de posicionamento da marca
Um ponto crítico do cliente no mercado de engrenagens sem-fim é a necessidade de alta precisão e confiabilidade em aplicações exigentes. Os fabricantes abordam isso investindo em tecnologias avançadas de fabricação e processos rigorosos de controle de qualidade. Além disso, o alto custo inicial das engrenagens sem-fim pode ser uma preocupação. As empresas oferecem soluções econômicas e enfatizam os benefícios de longo prazo do uso de engrenagens sem-fim de alta qualidade, como manutenção reduzida e vida útil estendida.
As estratégias de posicionamento de marca focam em destacar expertise técnica, inovação e confiabilidade do produto. Empresas líderes se diferenciam ao oferecer soluções personalizadas, serviços abrangentes de pós-venda e suporte técnico robusto. Ao alavancar sua expertise e reputação, essas marcas constroem confiança e lealdade entre seus clientes.
Nichos de Mercado e Estratégias de Diferenciação
Os nichos de mercado para engrenagens sem-fim incluem equipamentos aeroespaciais, de defesa e médicos, onde alta precisão e confiabilidade são cruciais. Nesses mercados, os fabricantes oferecem soluções de engrenagens especializadas adaptadas a requisitos de aplicação exclusivos. Por exemplo, no setor médico, as engrenagens sem-fim são usadas em robôs cirúrgicos e dispositivos de imagem, onde o controle preciso do movimento é crítico.
Estratégias de diferenciação envolvem inovação contínua e adoção de tecnologias de ponta. As empresas investem em pesquisa e desenvolvimento para criar projetos avançados de engrenagens, melhorar as propriedades dos materiais e aprimorar os processos de fabricação. Ao permanecer na vanguarda da tecnologia, os fabricantes podem oferecer produtos superiores que atendem às necessidades em evolução de seus clientes.
Fatores-chave ao selecionar engrenagens de roda sem-fim
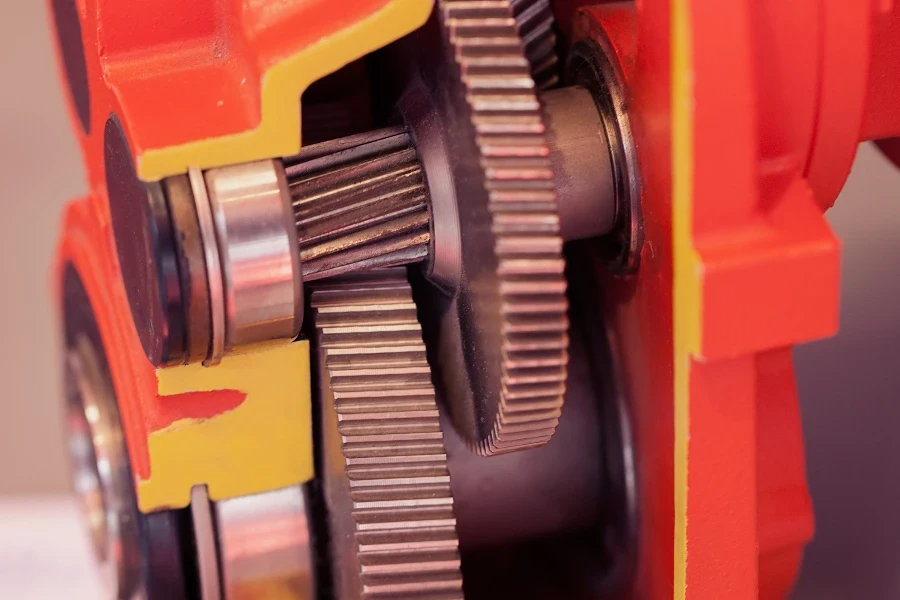
Seleção de material
Escolher o material certo para engrenagens de roda sem-fim é crucial para garantir durabilidade, eficiência e desempenho. Materiais comuns incluem ferro fundido, aço de liga e bronze.
O ferro fundido é favorecido por sua durabilidade e custo-benefício. Ele fornece excelente resistência ao desgaste e é fácil de fabricar. No entanto, pode não ser adequado para aplicações de alta carga devido à sua fragilidade.
O aço de liga oferece durabilidade superior e resistência à corrosão. É ideal para aplicações de alto estresse, pois pode suportar cargas significativas sem deformar. Adicionar minerais ao aço de liga pode aumentar ainda mais sua dureza e resistência ao desgaste.
O bronze é popular para aplicações que exigem alta resistência ao desgaste e ao atrito. Ele também fornece boa resistência à corrosão, tornando-o adequado para ambientes severos. No entanto, rodas sem-fim de bronze são tipicamente mais caras do que aquelas feitas de ferro fundido ou aço de liga.
Design e geometria de engrenagens
O design e a geometria das engrenagens de roda sem-fim influenciam significativamente seu desempenho. Os principais parâmetros incluem passo diametral (DP), passo circular (CP), módulo (M), ângulo de pressão e ângulo de avanço.
Passo diametral (DP) é a razão entre o número de dentes e o diâmetro do passo de uma engrenagem. Um DP mais alto indica um espaçamento mais fino entre os dentes, impactando a capacidade de carga e a precisão da engrenagem.
Passo circular (CP) é a medida direta da distância do centro de um dente ao centro do dente adjacente. Em acionamentos sem-fim, isso é chamado de passo axial e é crítico para o engrenamento adequado.
O módulo (M) é uma medida de engrenagem padrão que indica o tamanho e o número de dentes. Ele garante a compatibilidade entre engrenagens em sistemas baseados em métricas.
Ângulo de pressão é o ângulo da ação de acionamento do dente, afetando a distribuição de carga e a eficiência. Ângulos de pressão comuns são 14.5° ou 20°, com ângulos maiores fornecendo melhor capacidade de carga.
Ângulo de avanço, também conhecido como ângulo de hélice, é o ângulo no qual os dentes da engrenagem são alinhados em relação ao eixo. Esse ângulo determina o padrão de contato entre o sem-fim e a roda sem-fim, influenciando a eficiência e a geração de calor.
Eficiência e atrito
A eficiência em engrenagens de roda sem-fim é determinada pelo ângulo de avanço e pelo número de roscas em contato com a engrenagem sem-fim. Um ângulo de avanço maior reduz perdas por atrito e geração de calor, melhorando a eficiência. Por outro lado, um ângulo de avanço menor aumenta o torque, mas pode resultar em maior atrito e calor.
O atrito é uma preocupação significativa em conjuntos de engrenagens sem-fim, levando ao aumento do desgaste e à redução da vida útil. A lubrificação adequada é essencial para minimizar o atrito e garantir uma operação suave. Selecionar o lubrificante certo e manter um cronograma de lubrificação apropriado pode melhorar o desempenho e a longevidade.
Dentes retificados podem ajudar a reduzir o atrito e o ruído, contribuindo para uma operação mais silenciosa e eficiente. A precisão na fabricação desses dentes garante melhor engrenamento e distribuição de carga, melhorando ainda mais o desempenho.
Capacidade de carga e torque
Engrenagens de roda sem-fim são conhecidas por suas altas capacidades de multiplicação de torque e redução de engrenagem. Ao selecionar uma engrenagem de roda sem-fim, considere a capacidade de carga e os requisitos de torque da aplicação.
Aplicações de alto torque se beneficiam de engrenagens sem-fim devido à sua capacidade de fornecer redução significativa de engrenagem em uma forma compacta. Material, design e lubrificação contribuem para lidar com altas cargas sem desgaste excessivo ou falha.
Considere a inércia da engrenagem durante a aceleração e desaceleração. Engrenagens mais pesadas podem fornecer melhor estabilidade e manuseio de carga, mas podem ser mais difíceis de parar ou reverter. Equilibrar o peso da engrenagem com os requisitos de desempenho é crucial para uma operação ideal.
Ruído e vibração
Ruído e vibração são críticos em muitas aplicações comerciais e industriais. Engrenagens de roda sem-fim são geralmente mais silenciosas do que outros tipos de engrenagens devido à sua ação de engrenamento contínua. No entanto, os níveis de ruído podem variar dependendo do material, design e lubrificação.
Para minimizar o ruído, selecione engrenagens com dentes retificados com precisão e garanta a lubrificação adequada. Lubrificantes de alta qualidade podem reduzir o atrito e o ruído, contribuindo para uma operação mais suave.
A vibração pode impactar o desempenho e a vida útil. Cargas pesadas da máquina ou folga podem causar desalinhamento, levando ao aumento do desgaste e potencial falha da engrenagem. Garantir a montagem e o alinhamento adequados e usar materiais resistentes à vibração pode ajudar a mitigar esses problemas.
Aplicações e inovações avançadas em engrenagens de roda sem-fim
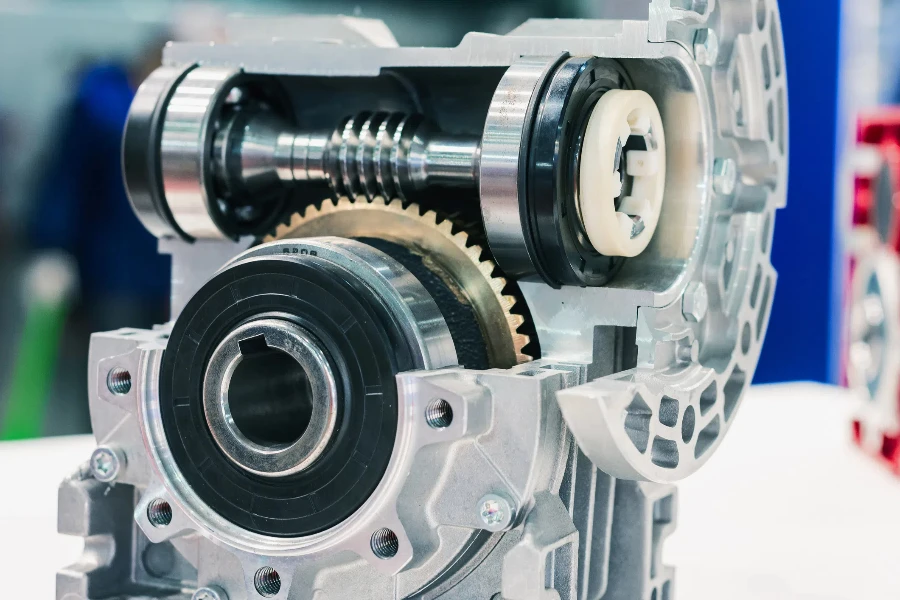
Avanços tecnológicos
A indústria de engrenagens de roda sem-fim tem visto avanços tecnológicos significativos, levando a melhor desempenho e eficiência. Técnicas modernas de fabricação, como usinagem CNC e retificação de precisão, permitem a produção de engrenagens com maior precisão e tolerâncias mais rígidas.
Inovações na ciência dos materiais levaram a engrenagens mais fortes e duráveis. Ligas avançadas e materiais compostos oferecem resistência superior ao desgaste e capacidade de carga, tornando-os adequados para aplicações exigentes.
A integração de tecnologias inteligentes, como monitoramento de condições e manutenção preditiva, permite o monitoramento em tempo real do desempenho do equipamento. Essas tecnologias podem detectar problemas potenciais antes que eles levem a falhas, reduzindo o tempo de inatividade e os custos de manutenção.
Eficiência Energética e Sustentabilidade
A eficiência energética é uma preocupação crescente na indústria de máquinas, e as engrenagens de roda sem-fim não são exceção. Os fabricantes se concentram em reduzir o atrito e melhorar a lubrificação para aumentar a eficiência e reduzir o consumo de energia.
Lubrificantes e revestimentos de alta eficiência podem reduzir significativamente as perdas por atrito, diminuindo o consumo de energia e estendendo a vida útil da engrenagem. Lubrificantes e materiais ecologicamente corretos apoiam os esforços de sustentabilidade na indústria.
A reciclagem e a remanufatura de engrenagens de roda sem-fim também estão ganhando força como práticas sustentáveis. Ao reformar engrenagens usadas, os fabricantes podem reduzir o desperdício e minimizar o impacto ambiental.
Aplicações Específicas da Indústria
Engrenagens de roda sem-fim são usadas em várias indústrias, cada uma com requisitos e desafios específicos. Na indústria automotiva, engrenagens sem-fim são comuns em sistemas de direção e vidros elétricos devido ao seu tamanho compacto e alta capacidade de torque.
Na indústria aeroespacial, engrenagens sem-fim são usadas em sistemas de controle, onde precisão e confiabilidade são críticas. Materiais e revestimentos avançados garantem que essas engrenagens possam suportar condições operacionais severas.
No setor industrial, engrenagens sem-fim são usadas em transportadores, elevadores e máquinas pesadas, onde sua capacidade de lidar com altas cargas e fornecer redução significativa de engrenagens é essencial. Soluções de engrenagens personalizadas adaptadas a aplicações industriais específicas impulsionam a inovação neste campo.
Considerações Finais
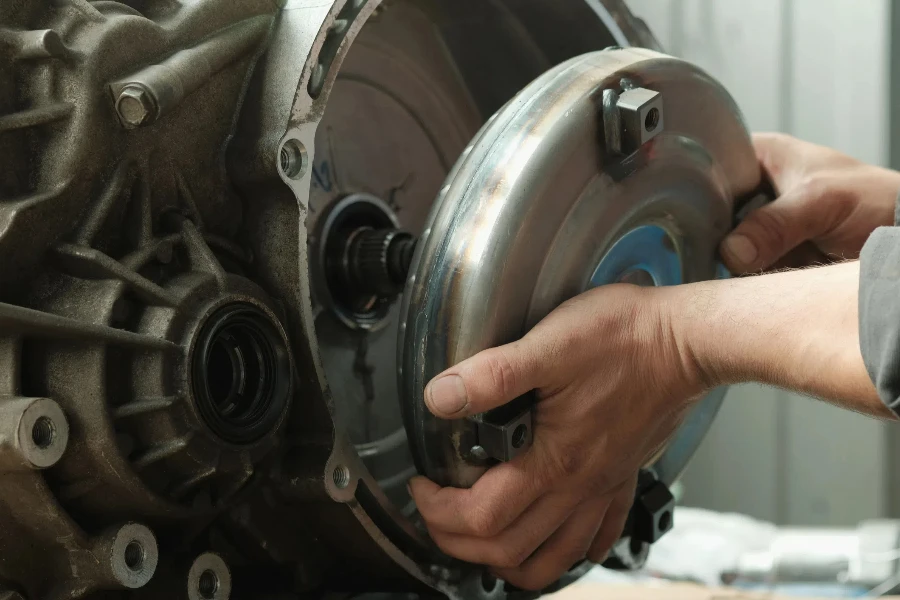
Em resumo, selecionar engrenagens de roda sem-fim envolve avaliar vários fatores, incluindo escolha de material, design e geometria, eficiência, capacidade de carga, ruído e vibração. Avanços tecnológicos e esforços de sustentabilidade estão impulsionando melhorias no desempenho e eficiência das engrenagens, enquanto aplicações específicas da indústria destacam a versatilidade e a importância das engrenagens de roda sem-fim em máquinas modernas.