В кампусе аддитивного производства в Обершлайсхайме BMW Group испытывает аддитивное производство с проволокой (WAAM), при котором проволока из алюминия или аналогичного материала плавится с помощью дуги. Затем робот с программным управлением с точностью накладывает большое количество сварных швов друг на друга, пока не будет закончена готовая деталь.
Поскольку давление означает, что слой за слоем нет необходимости обращать внимание на возможность разборки, возможны полые конструкции с оптимальным соотношением жесткости и веса.
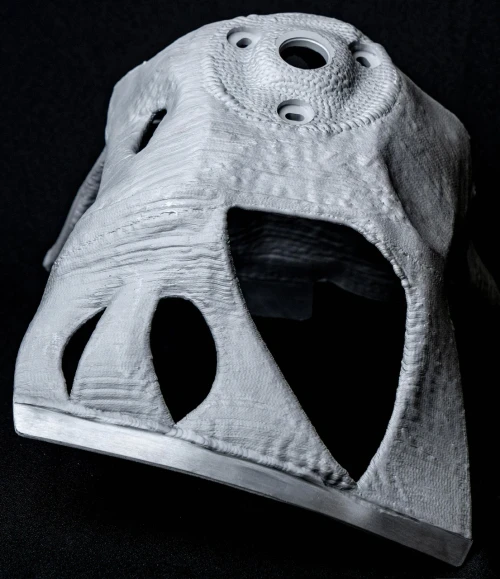
Это означает, что компоненты могут быть легче и жестче, чем аналогичные детали, отлитые под давлением, которые в настоящее время производятся серийно. Их также можно производить более экологично благодаря более низким потребностям в энергии и меньшему количеству отходов материала. В будущем планируется использовать компоненты, изготовленные с использованием процесса WAAM, в серийных автомобилях BMW Group.
Большая ширина и высота одного сварочного шва означает, что с помощью WAAM можно производить компоненты очень быстро. В отличие от плавки лазерным лучом, которая уже используется в прототипах и мелкосерийном производстве BMW Group, WAAM особенно подходит для более крупных компонентов. Типичная толщина стенок хорошо подходит для компонентов корпуса, привода и шасси. Однако инструменты и устройства также могут быть изготовлены с использованием этого высокотехнологичного процесса, который также используется в авиационной промышленности.
Сотрудники BMW Group с 2015 года занимаются процессом WAAM, также известным как наплавка. С 2021 года в Кампусе аддитивного производства используется ячейка WAAM для производства тестовых компонентов. Одним из таких примеров применения является Опора стойки подвески, которая в ходе всесторонних испытаний на испытательном стенде сравнивается с серийно выпускаемым компонентом, изготовленным из алюминия, литого под давлением.
На этой ранней стадии уже ясно, что процесс WAAM может привести к снижению выбросов в производственном процессе. Меньший вес компонентов, выгодное соотношение использования материалов и возможность использования возобновляемых источников энергии означают, что компоненты можно производить более эффективно.
— Йенс Эртель, руководитель подразделения аддитивного производства BMW
Следующим этапом разработки на пути к серийному производству являются испытания комплектующих автомобиля, которые начнутся в обозримом будущем.
Более широкие сварные швы в процессе WAAM означают, что поверхности компонентов не гладкие, а слегка волнистые и их необходимо обрабатывать в критических местах. Однако инженерам BMW Group удалось продемонстрировать, что компоненты WAAM могут использоваться при высоких нагрузках, в том числе циклических, даже без последующей обработки поверхности.
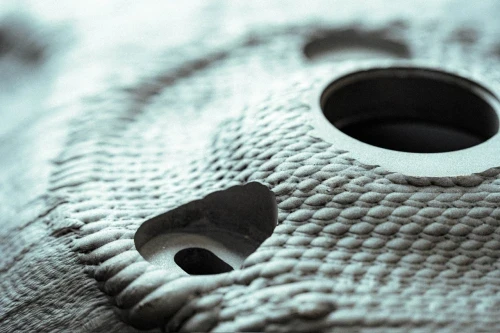
Оптимизированные параметры процесса имеют решающее значение для обеспечения долговечности непосредственно на производстве, поэтому сочетание сварочного процесса и роботизированного планирования пути должно быть оптимально скоординировано.
Чтобы оптимально использовать компоненты, произведенные в процессе WAAM, сочетание производственного процесса и общей конструкции новых компонентов имеет первостепенное значение. С этой целью BMW Group продолжает ускорять использование генеративного дизайна. Здесь компьютер использует алгоритмы для разработки оптимизированных компонентов на основе конкретных требований.
Эти алгоритмы разрабатываются в тесном сотрудничестве с междисциплинарными группами и частично вдохновлены эволюционными процессами в природе. Как и в случае с бионическими структурами, на первом этапе используется только тот материал, который действительно необходим для топологии компонента, а при доводке на втором этапе компонент усиливается только там, где это необходимо. В конечном итоге это приводит к созданию более легких и жестких компонентов, а также к повышению эффективности и улучшению динамики автомобиля.
Различные процессы аддитивного производства не обязательно конкурируют друг с другом, их следует рассматривать как взаимодополняющие. Например, плавление лазерным лучом по-прежнему будет более выгодным, чем процесс WAAM, когда речь идет о высочайшем уровне детализации. Однако с точки зрения возможного размера компонента и скорости осаждения аддитивное производство с проволочной дугой превосходит его.
BMW Group изначально планирует централизованное производство компонентов WAAM в Обершлайсхайме, в будущем производство будет осуществляться и в других местах, а также возможно использование технологии поставщиками. Более того, можно было бы даже производить отдельные компоненты непосредственно на сборочной линии, используя этот процесс, и изготавливать различные детали без новых инструментов, просто меняя программное обеспечение. Устойчивость также можно улучшить за счет увеличения использования переработанных металлов.
Источник из Зеленый автомобильный конгресс
Отказ от ответственности: информация, изложенная выше, предоставлена greencarcongress.com независимо от Chovm.com. Chovm.com не делает никаких заявлений и не дает никаких гарантий относительно качества и надежности продавца и продукции.