Recent advancements in pallet wrapping technology, such as IoT integration and eco-friendly films, have revolutionized the industry. This article provides an in-depth analysis of the pallet wrapper market, highlighting key factors to consider when selecting a pallet wrapper. Professional buyers will find valuable insights to make informed decisions that align with their operational goals.
Table of Contents:
-Market Overview: Pallet Wrapper Industry
-Detailed Introduction and Analysis of the Pallet Wrapper Market
-Key Factors When Selecting a Pallet Wrapper
-Understanding the Benefits of Different Pallet Wrapper Types
-Advanced Features and Technologies in Modern Pallet Wrappers
-Ensuring Compliance with Safety Standards and Certifications
-Conclusion
Market Overview: Pallet Wrapper Industry
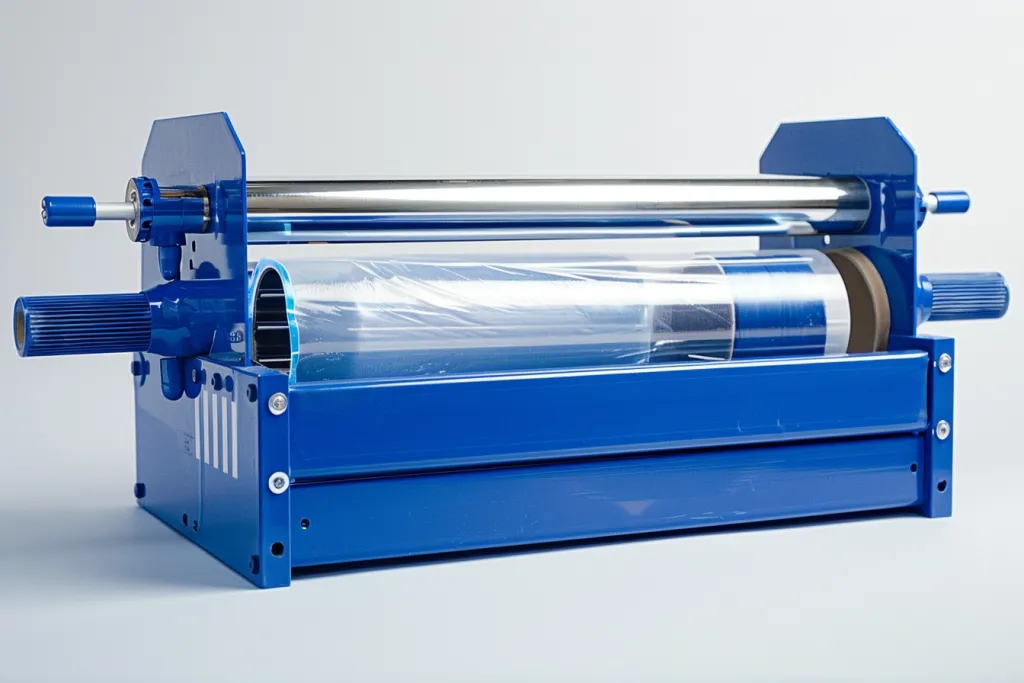
The global pallet wrapper market has shown significant growth in recent years, driven by the rising demand for efficient packaging solutions across various industries. In 2024, the market was worth around $5.2 billion and is projected to reach $6.9 billion by 2030, with a compound annual growth rate (CAGR) of 4.2%. This growth is due to factors such as increased e-commerce activities, the expansion of manufacturing sectors, and the need for improved logistics and supply chain efficiency.
The market is segmented by product types, including semi-automatic and fully automatic pallet wrappers. The fully automatic segment is expected to see the highest growth due to its productivity and labor cost reduction benefits. Additionally, the adoption of advanced technologies like the Internet of Things (IoT) and automation has significantly contributed to market expansion. Key regions leading the market include North America, Europe, and the Asia-Pacific, with the latter expected to grow the fastest due to increasing industrialization and urbanization.
The competitive landscape features prominent players such as Robopac, Lantech, and Aetna Group, who continue to innovate and invest in research and development to maintain their market positions. Furthermore, the growing focus on sustainable packaging solutions and the integration of smart technologies are anticipated to drive future market trends.
Detailed Introduction and Analysis of the Pallet Wrapper Market
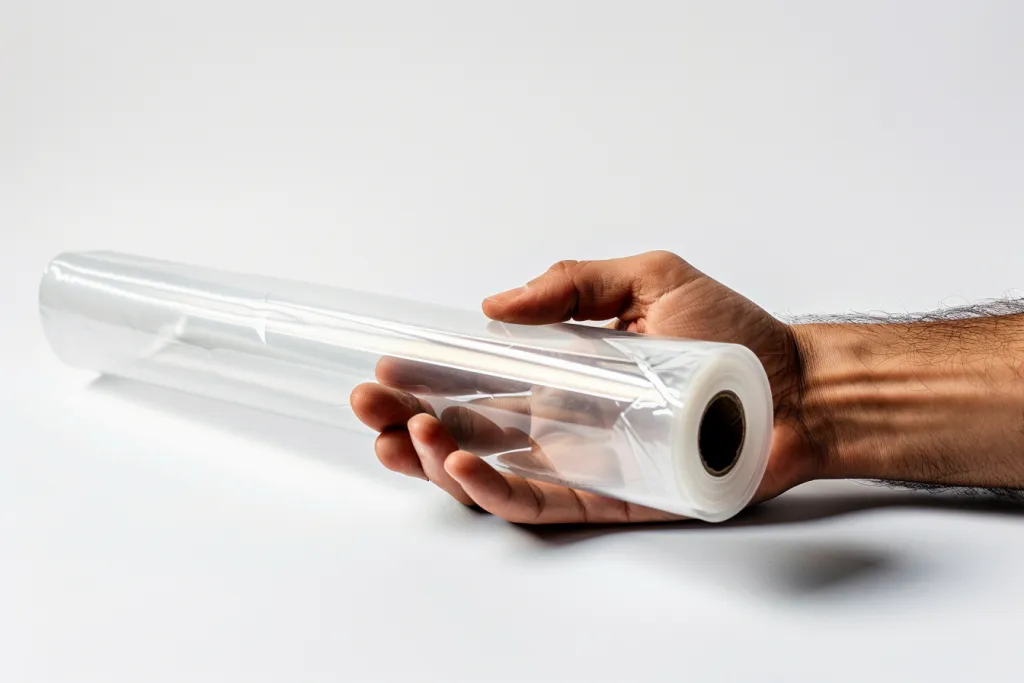
Pallet wrappers are essential for securing goods during transportation and storage in industries like food and beverage, pharmaceuticals, and retail. These machines wrap plastic film around palletized goods, ensuring stability and protection against environmental factors. Key performance benchmarks for pallet wrappers include wrapping speed, film efficiency, and load containment force. Modern pallet wrappers feature pre-stretch technology to maximize film usage and reduce waste, and programmable logic controllers (PLCs) for better operational control.
Fully automatic pallet wrappers hold a significant market share due to their efficiency in handling high-volume operations. Economic influences such as raw material price fluctuations and labor costs have impacted market growth. However, technological advancements have improved operational efficiency and reduced manual labor dependency. Consumer preference has shifted towards automated solutions for increased productivity and cost savings.
Distribution channel preferences vary by region, with direct sales being predominant in North America and Europe, while the Asia-Pacific region relies more on distributors and integrators. Recent innovations in the market include eco-friendly stretch films and IoT integration for real-time monitoring and maintenance. Product lifecycle stages indicate that pallet wrappers are moving towards maturity, with continuous technological and design improvements to meet evolving industry demands.
Digitalization has played a crucial role in the market, with smart pallet wrappers offering features like remote diagnostics, predictive maintenance, and data analytics to optimize wrapping processes. Social trends emphasize sustainability, driving the adoption of biodegradable and recyclable films. Customer pain points, such as high initial investment costs and maintenance requirements, are being addressed through leasing options and comprehensive service packages.
Brand positioning strategies focus on reliability, efficiency, and sustainability, with companies differentiating themselves through innovative features and customer-centric solutions. Differentiation strategies include offering customizable solutions tailored to specific industry needs and enhancing user experience through intuitive interfaces and automated functions. Niche markets, such as the pharmaceutical and electronics sectors, require specialized pallet wrappers with stringent hygiene and anti-static properties, presenting opportunities for targeted product development.
Key Factors When Selecting a Pallet Wrapper
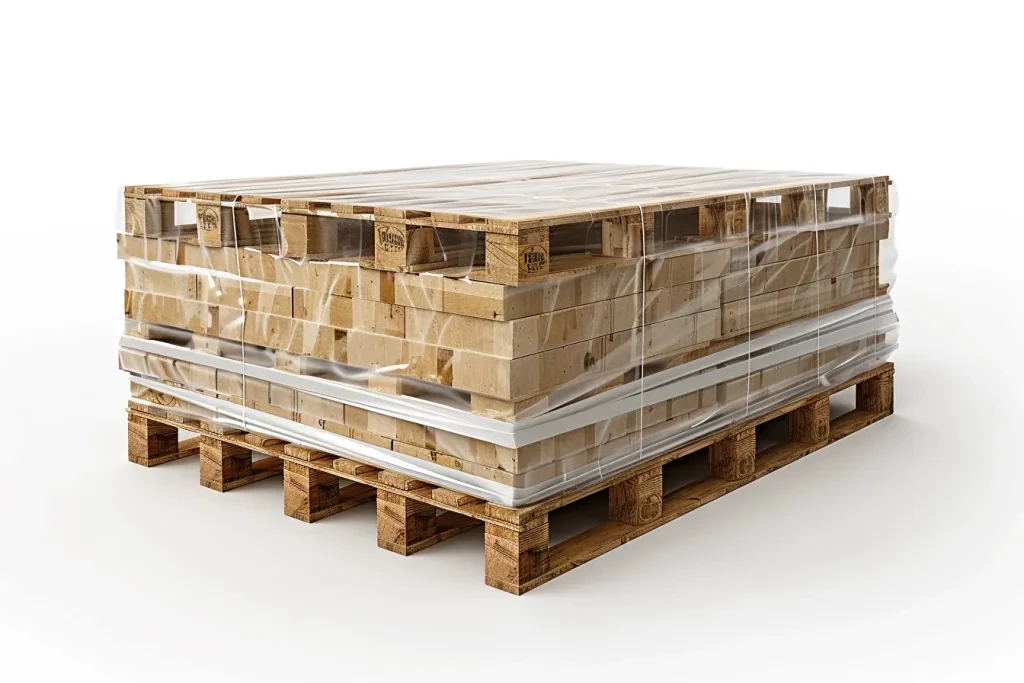
When choosing a pallet wrapper for your business, several critical considerations come into play. These factors can significantly influence the efficiency, cost-effectiveness, and overall performance of your warehouse operations. Understanding these elements will help you make an informed decision that aligns with your specific needs and goals.
Types of Pallet Wrappers
The type of pallet wrapper is one of the most fundamental considerations. There are various types of pallet wrappers, including turntable stretch wrappers, rotary arm stretch wrappers, and horizontal stretch wrappers. Each type has unique advantages and is suitable for different applications.
Turntable Stretch Wrappers: These machines feature a rotating turntable that spins the pallet while a stationary film dispenser wraps the load. Ideal for standard loads, they offer an efficient solution for most warehousing needs. Turntable wrappers are particularly effective for facilities that handle uniform and stable loads.
Rotary Arm Stretch Wrappers: In these machines, the arm rotates around the stationary pallet, making them suitable for unstable or heavy loads that might topple on a turntable. They are often used in high-speed applications where stability is a concern.
Horizontal Stretch Wrappers: These are designed for elongated items such as lumber, pipes, or textiles. The film dispenser moves horizontally around the product, ensuring secure wrapping for items that cannot be easily stacked.
Automation Level
The automation level of a pallet wrapper can significantly impact its operational efficiency. Machines range from manual to fully automatic, and the right choice depends on the volume of pallets being wrapped and the available labor.
Manual Wrappers: These require significant human intervention, making them suitable for low-volume operations. They are cost-effective but can be labor-intensive and time-consuming.
Semi-Automatic Wrappers: These machines automate part of the wrapping process, reducing labor while still requiring some operator involvement. They strike a balance between cost and efficiency, making them suitable for medium-volume operations.
Fully Automatic Wrappers: These machines handle the entire wrapping process with minimal human intervention, ideal for high-volume operations. They offer the highest efficiency but come with a higher initial investment.
Film Type and Specifications
The type and specifications of the stretch film used can affect the wrapping process’s efficiency and effectiveness. The film’s gauge (thickness), pre-stretch capability, and puncture resistance are critical factors to consider.
Film Gauge: The gauge of the film determines its strength and stretch capacity. Higher gauge films offer better puncture resistance and are suitable for heavier loads, while lower gauge films are more cost-effective for lighter loads.
Pre-Stretch Capability: Films with high pre-stretch capabilities can be stretched to a greater extent before application, reducing film usage and costs. This feature is particularly beneficial for high-volume operations.
Puncture Resistance: Puncture-resistant films are essential for loads with sharp edges or irregular shapes. Choosing the right film can prevent tears and ensure the load remains secure during transit.
Safety Features
Safety is a paramount concern in any warehouse operation. Pallet wrappers come with various safety features designed to protect operators and ensure the safe handling of loads.
Emergency Stop Buttons: These are standard on most machines, allowing operators to halt the wrapping process immediately in case of an emergency.
Safety Fences and Light Curtains: These features prevent operators from entering the wrapping area while the machine is in operation, reducing the risk of accidents.
Load Sensors: These sensors detect the presence and weight of the load, ensuring the machine operates within safe parameters and preventing overloading.
Cost and Budget Considerations
The cost of a pallet wrapper includes the initial purchase price, installation, maintenance, and operational costs. It’s essential to consider the total cost of ownership rather than just the upfront cost.
Initial Purchase Price: This varies widely depending on the type and automation level of the machine. While manual wrappers are cheaper, fully automatic machines offer better long-term value for high-volume operations.
Maintenance Costs: Regular maintenance is crucial for ensuring the longevity and reliability of the machine. Consider the availability of spare parts and the manufacturer’s support services.
Operational Costs: These include the cost of stretch film, energy consumption, and labor. Machines with higher efficiency and lower film usage can offer significant cost savings over time.
Understanding the Benefits of Different Pallet Wrapper Types
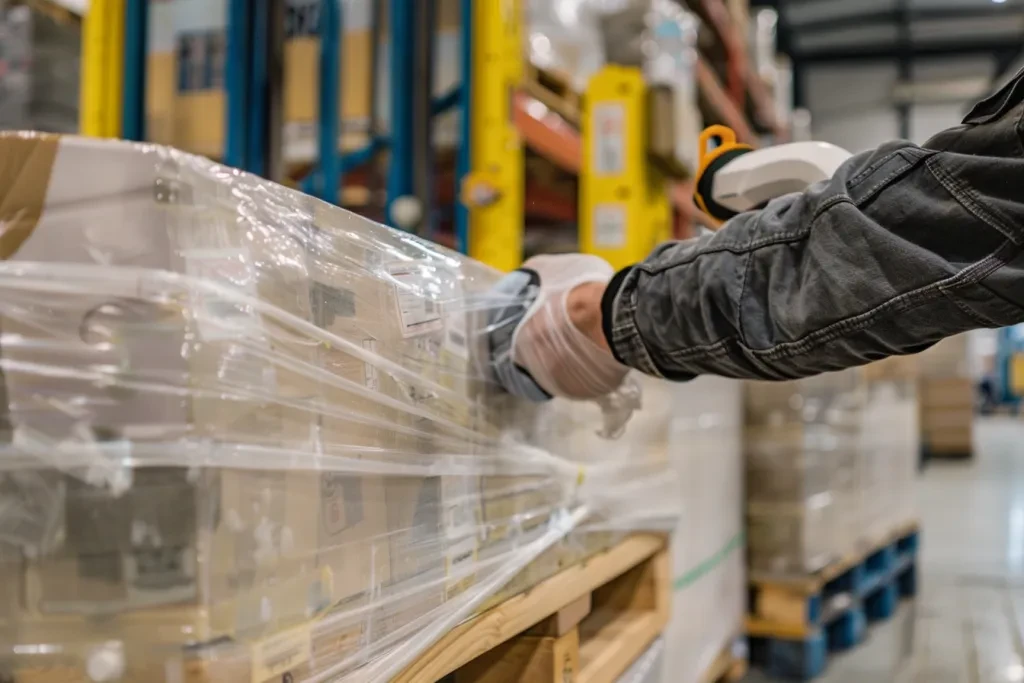
The benefits of different types of pallet wrappers can significantly impact your decision-making process. Each type offers unique advantages that cater to specific operational needs.
Turntable Stretch Wrappers
Turntable stretch wrappers are widely used due to their versatility and efficiency. They are ideal for operations with a high volume of uniform loads. These machines are cost-effective and relatively easy to operate, making them a popular choice for many warehouses.
Versatility: Suitable for a wide range of load sizes and shapes, turntable stretch wrappers can handle most standard palletizing tasks. Their adaptability makes them a go-to option for various industries.
Efficiency: Turntable wrappers can wrap loads quickly and consistently, improving overall productivity. They are particularly effective for operations that require fast turnaround times.
Cost-Effectiveness: With a lower initial investment compared to more complex machines, turntable wrappers offer a good balance between cost and functionality. They are an excellent choice for businesses looking to optimize their budget.
Rotary Arm Stretch Wrappers
Rotary arm stretch wrappers are designed for stability and safety, making them ideal for handling unstable or heavy loads. These machines are particularly beneficial in high-speed applications where load stability is a concern.
Stability: By keeping the load stationary and rotating the wrapping arm around it, rotary arm wrappers minimize the risk of load toppling. This feature is crucial for handling delicate or irregularly shaped items.
High-Speed Applications: Rotary arm wrappers can operate at high speeds without compromising load stability, making them suitable for high-volume operations. They are often used in industries where speed and efficiency are paramount.
Safety: These machines come equipped with advanced safety features to protect operators and ensure safe handling of loads. The stationary load design reduces the risk of accidents during the wrapping process.
Horizontal Stretch Wrappers
Horizontal stretch wrappers are specialized machines designed for wrapping elongated items. They offer a unique solution for industries that handle products such as lumber, pipes, or textiles.
Specialization: Horizontal wrappers are tailored for specific applications, providing a secure wrapping solution for items that cannot be easily stacked. This specialization ensures that even the most challenging loads are wrapped securely.
Efficiency: These machines can handle long and irregularly shaped items efficiently, reducing the need for manual wrapping. They are particularly beneficial for operations that deal with non-standard loads.
Customization: Horizontal wrappers can be customized to fit the specific needs of your operation, ensuring optimal performance and load security. This flexibility makes them a valuable asset for specialized industries.
Advanced Features and Technologies in Modern Pallet Wrappers
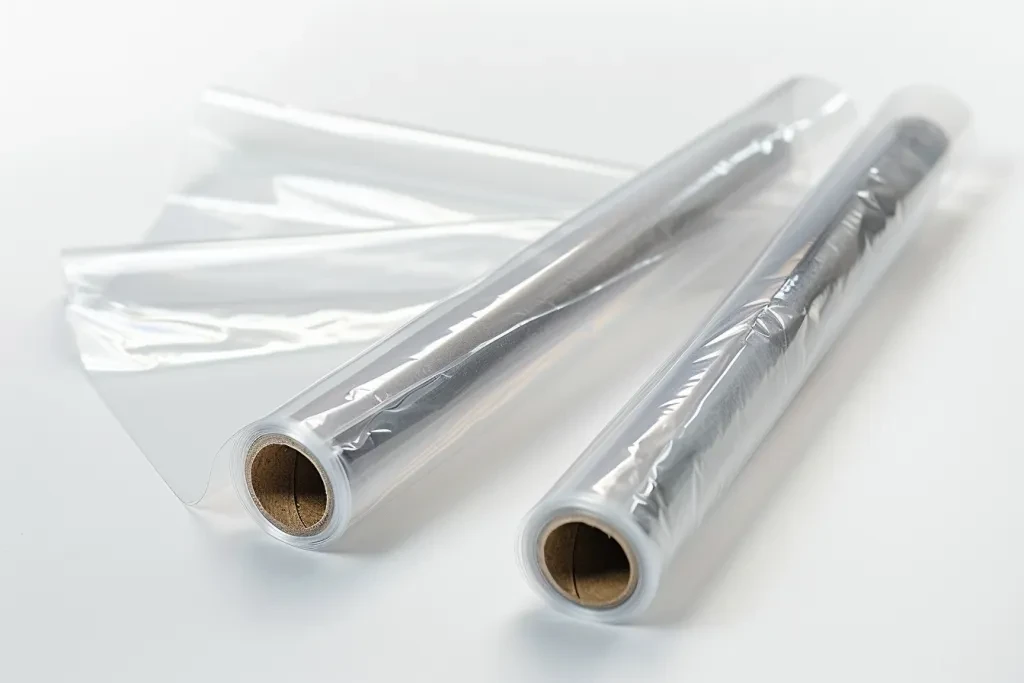
The pallet wrapping industry has seen significant advancements in technology and features, enhancing the efficiency and effectiveness of modern pallet wrappers. Understanding these innovations can help you choose a machine that offers the best value and performance for your operation.
Pre-Stretch Technology
Pre-stretch technology is a game-changer in the pallet wrapping industry. This feature allows the film to be stretched before being applied to the load, reducing film usage and costs.
Cost Savings: By stretching the film up to 300%, pre-stretch technology reduces the amount of film needed for each load. This reduction translates to significant cost savings over time, especially in high-volume operations.
Improved Load Stability: Pre-stretched film provides better load containment, ensuring that the wrapped items remain secure during transit. This stability is crucial for preventing damage and ensuring safe delivery.
Environmental Benefits: Using less film reduces waste and the environmental impact of your packaging process. Pre-stretch technology aligns with sustainability goals and helps businesses reduce their carbon footprint.
Automated Film Cutting and Clamping
Automated film cutting and clamping features streamline the wrapping process, reducing the need for manual intervention and increasing efficiency.
Time Savings: Automated systems cut and clamp the film at the end of the wrapping cycle, eliminating the need for operators to perform these tasks manually. This automation speeds up the wrapping process and reduces downtime.
Consistency: Automated cutting and clamping ensure consistent film application, improving the overall quality of the wrap. Consistency is key to maintaining load stability and preventing film waste.
Operator Safety: Reducing manual intervention minimizes the risk of accidents and injuries, enhancing operator safety. Automated systems contribute to a safer working environment.
Touchscreen Controls and Programmable Settings
Modern pallet wrappers come equipped with advanced controls and programmable settings, allowing for greater customization and ease of use.
User-Friendly Interface: Touchscreen controls provide an intuitive interface for operators, simplifying the setup and operation of the machine. This ease of use reduces training time and increases productivity.
Customizable Settings: Programmable settings allow operators to customize wrapping parameters based on the specific needs of each load. This customization ensures optimal performance and load security.
Data Tracking: Advanced controls can track wrapping data, providing valuable insights into film usage, cycle times, and machine performance. This data helps businesses optimize their wrapping process and identify areas for improvement.
Ensuring Compliance with Safety Standards and Certifications
Compliance with safety standards and certifications is a critical consideration when selecting a pallet wrapper. Ensuring that your equipment meets industry regulations not only protects your employees but also enhances your operation’s credibility and reliability.
Industry Standards
Pallet wrappers must comply with various industry standards to ensure safe and efficient operation. These standards cover aspects such as machine design, operation, and maintenance.
ISO Standards: The International Organization for Standardization (ISO) sets global standards for machinery, including pallet wrappers. Compliance with ISO standards ensures that your equipment meets international safety and quality benchmarks.
OSHA Regulations: In the United States, the Occupational Safety and Health Administration (OSHA) sets regulations for workplace safety. Ensuring that your pallet wrapper complies with OSHA regulations helps prevent accidents and promotes a safe working environment.
CE Marking: In Europe, the CE marking indicates that a machine meets the essential health and safety requirements set out in European directives. CE marking is a critical certification for businesses operating in the European market.
Third-Party Certifications
Third-party certifications from recognized organizations provide additional assurance of a pallet wrapper’s safety and quality.
UL Certification: Underwriters Laboratories (UL) certification indicates that a machine has been tested and meets stringent safety standards. UL certification is widely recognized and trusted in the industry.
CSA Certification: The Canadian Standards Association (CSA) certification ensures that a machine meets Canadian safety standards. CSA certification is essential for businesses operating in the Canadian market.
Regular Maintenance and Inspections
Regular maintenance and inspections are crucial for ensuring that your pallet wrapper continues to operate safely and efficiently.
Scheduled Maintenance: Implementing a regular maintenance schedule helps identify and address potential issues before they become major problems. Routine maintenance ensures that your machine remains in optimal condition.
Safety Inspections: Regular safety inspections help identify and mitigate risks, ensuring that your equipment remains compliant with safety standards. Inspections should be conducted by qualified personnel to ensure thoroughness and accuracy.
Training and Certification: Providing operators with proper training and certification ensures that they understand how to operate the machine safely and effectively. Ongoing training helps keep operators up-to-date with the latest safety practices and regulations.
Conclusion
In conclusion, selecting the right pallet wrapper for your business involves considering various factors, including the type of machine, automation level, film specifications, safety features, and cost. By understanding these elements and their impact on your operations, you can make an informed decision that enhances efficiency, reduces costs, and ensures the safety of your employees.