การพิจารณาแนวโน้มปัจจุบันและปัญหาห่วงโซ่อุปทานสำหรับภาคยานยนต์
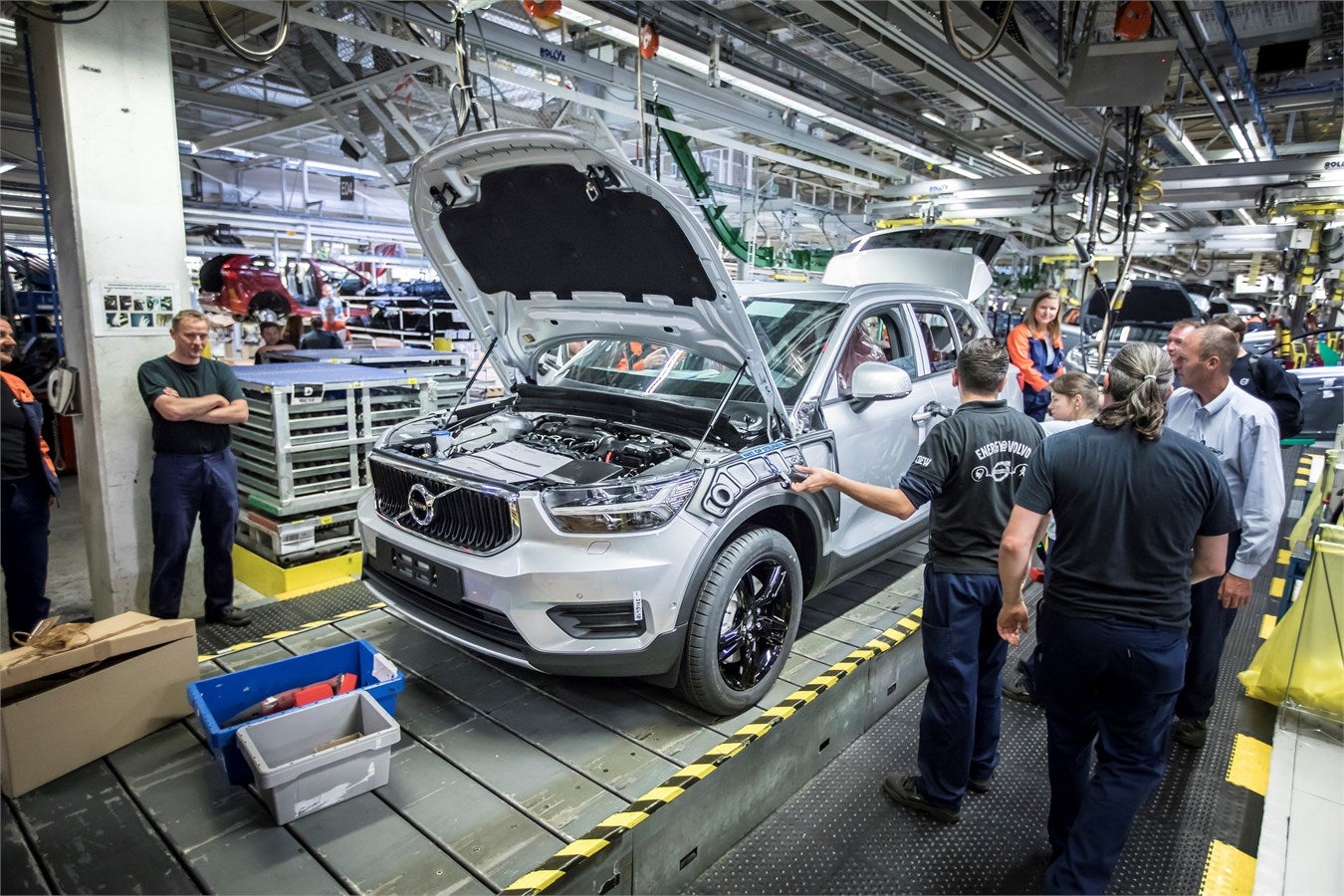
รถยนต์ที่ไม่ธรรมดาสามารถมีชิ้นส่วนได้ตั้งแต่ 15,000 ถึง 25,000 ชิ้น ขึ้นอยู่กับวิธีการวัดและการออกแบบระบบหลัก ซึ่งต้องใช้วัสดุจำนวนมากในการประกอบเข้าด้วยกันเพื่อให้ผลิตภัณฑ์ขั้นสุดท้ายมีความสมบูรณ์ ไม่ใช่เรื่องง่ายเลยที่จะประกอบชิ้นส่วนทั้งหมดเข้าด้วยกันในลำดับที่ถูกต้อง รถยนต์ทุกคันที่มีอยู่ล้วนเป็นเครื่องพิสูจน์ถึงการวางแผนกระบวนการ การจัดระเบียบ วิศวกรรมการผลิต และการขนส่งการผลิต กาลครั้งหนึ่ง ผู้ผลิตยานยนต์มีการบูรณาการในแนวตั้งอย่างมาก แต่แนวทางดังกล่าวได้ถูกแทนที่ด้วยการปลดพนักงาน (ใครจำได้บ้างว่า Visteon มาจากไหนและบริษัทต่างๆ ที่ประกอบกันเป็นกลุ่มชิ้นส่วนยานยนต์ของ General Motors นั้นมีเครือข่ายที่ยุ่งเหยิง) และซัพพลายเออร์ชิ้นส่วนเฉพาะทางที่สามารถมุ่งเน้นที่การพัฒนาผลิตภัณฑ์และดำเนินการอย่างมีประสิทธิภาพมากขึ้นในระดับที่สูงขึ้นสำหรับลูกค้ามากกว่าหนึ่งราย
ผู้ผสานระบบระดับ 1 รายใหญ่จะจัดหาสินค้าให้ผู้ผลิตยานยนต์โดยตรง โดยมักจะมาจากแหล่งซัพพลายเออร์ที่ตั้งอยู่ใกล้กับโรงงานประกอบและการผลิตยานยนต์ แต่ยังมีซัพพลายเออร์รายย่อยอีกหลายระดับที่ต่ำกว่าระดับบนสุด โดยแต่ละระดับมีบทบาทสำคัญในเส้นทางอันยาวไกลจากวัตถุดิบจนถึงผลิตภัณฑ์สำเร็จรูป
การจัดหาชิ้นส่วนจากต่างประเทศได้กลายมาเป็นมาตรฐานของอุตสาหกรรมมาหลายทศวรรษแล้ว เนื่องจากผู้ผลิตอุปกรณ์ดั้งเดิมและซัพพลายเออร์รายใหญ่ต่างพยายามหาชิ้นส่วนและวัสดุที่ตรงตามเกณฑ์คุณภาพที่จำเป็นในต้นทุนที่ต่ำที่สุดจากตลาดโลก ระยะทาง (และต้นทุน) สำหรับการขนส่งและการจัดการคลังสินค้าก็เป็นส่วนหนึ่งของภาพรวมเช่นกัน แต่ประสิทธิภาพที่สูงขึ้นและความก้าวหน้าทางเทคโนโลยีในการขนส่งสินค้าระหว่างประเทศได้สนับสนุนการเติบโตอย่างก้าวกระโดดของการขนส่งชิ้นส่วนระหว่างประเทศ
การเติบโตของอุตสาหกรรมรถยนต์ของจีนในช่วงสองทศวรรษที่ผ่านมาเป็นปัจจัยสำคัญในการจัดหาชิ้นส่วนยานยนต์จากทั่วโลก โดยเฉพาะอย่างยิ่งชิ้นส่วนที่อาจเรียกได้ว่าเป็นชิ้นส่วนสากลหรือชิ้นส่วนสินค้าโภคภัณฑ์ที่ขายตามต้นทุนเป็นหลัก ซัพพลายเออร์ชาวจีนได้รับประโยชน์จากสัญญาขนาดใหญ่ในท้องถิ่นซึ่งช่วยกระตุ้นเศรษฐกิจจากขนาด ตลอดจนเงินอุดหนุนแอบแฝงที่เกิดจากโครงสร้างความเป็นเจ้าของที่ซับซ้อนซึ่งเกี่ยวข้องกับบริษัทแม่ของ OEM รัฐวิสาหกิจ และหุ้นที่หลากหลาย ในช่วงต้นทศวรรษปี 2000 โดยเฉพาะผู้ผลิตยานยนต์ในสหรัฐฯ ได้หันไปหาชิ้นส่วนราคาถูกจากเอเชียมากขึ้น ซึ่งส่งผลให้บริษัทที่ก่อตั้งมายาวนานในฐานซัพพลายเออร์ในสหรัฐฯ บางแห่งต้องสูญเสียส่วนแบ่งการตลาดไป
การค้าระหว่างประเทศในผลิตภัณฑ์ยานยนต์ทั่วโลก ไม่ว่าจะเป็นยานยนต์สำเร็จรูปหรือชิ้นส่วนต่างๆ ล้วนมีมูลค่ามหาศาลในปัจจุบัน ประมาณการที่รวบรวมโดย GlobalData แสดงให้เห็นว่าเยอรมนีเป็นผู้นำระดับโลกในด้านการส่งออกผลิตภัณฑ์อุตสาหกรรมยานยนต์ โดยการส่งออกดังกล่าวสะท้อนให้เห็นการนำเข้าและสินค้าขั้นกลางที่เชื่อมโยงกันซึ่งใช้เป็นปัจจัยการผลิตของระบบส่วนประกอบที่ผ่านการปรับแต่งและออกแบบในขั้นตอนต่างๆ ของกระบวนการผลิต และสามารถส่งออกข้ามพรมแดนระหว่างประเทศได้หลายครั้ง
ลักษณะโครงสร้างที่สำคัญอีกประการหนึ่งสำหรับห่วงโซ่อุปทานในอุตสาหกรรมยานยนต์คือความสำคัญของปรัชญาการจัดการห่วงโซ่อุปทานที่ลดต้นทุนสินค้าคงคลังให้เหลือน้อยที่สุด เพิ่มประสิทธิภาพของกระบวนการและวงจรการสื่อสารตอบกลับเพื่อยกระดับมาตรฐานคุณภาพ แนวคิดนี้เรียกว่า "การผลิตแบบลีน" ซึ่งเริ่มต้นจากโตโยต้า และแก่นแท้ของแนวคิดนี้สรุปได้ด้วยคำว่า "แบบตรงเวลา" เพื่ออธิบายวิธีการและหลักการของการจัดหาแบบลีน การเพิ่มขึ้นของเทคโนโลยีดิจิทัลและเทคโนโลยีที่เชื่อมต่อซึ่งนำทุกส่วนของกระบวนการผลิตและการค้าปลีกมารวมกันได้ช่วยสนับสนุนวิธีการทำงานเหล่านี้ในช่วงทศวรรษที่ผ่านมา
ในอดีต ภัยพิบัติทางธรรมชาติและผลกระทบที่เกิดขึ้นในพื้นที่ต่างๆ ส่งผลกระทบต่อบริษัทผลิตรถยนต์และแสดงให้เห็นถึงความเปราะบางของห่วงโซ่อุปทานของยานยนต์ หลังจากเหตุการณ์แผ่นดินไหวและคลื่นสึนามิในญี่ปุ่นเมื่อปี 2011 มีตัวอย่างการหยุดชะงักที่สำคัญหลายประการ ผู้ผลิตรถยนต์ระดับพรีเมียมระดับโลกประสบปัญหาด้านอุปทานหรือเม็ดสีสีแดงที่มาจากญี่ปุ่นเพียงแหล่งเดียว อุทกภัยในประเทศไทยในช่วงปลายปีนั้นทำให้ขาดแคลนหน้าจอ LCD สำหรับแสดงข้อมูลรถยนต์ ผู้ผลิต OEM และตัวแทนจำหน่ายต้องปรับตัวให้เข้ากับภาวะขาดแคลน สงครามในยูเครนแสดงให้เห็นว่าเหตุการณ์ทางภูมิรัฐศาสตร์ที่ไม่คาดคิดสามารถหยุดชะงักห่วงโซ่อุปทานได้เช่นกัน
ความท้าทายของเซมิคอนดักเตอร์
บริษัททั้งหมดได้รับผลกระทบโดยตรงจากวิกฤตสาธารณสุขในปี 2020 และโดยอ้อมจากผลกระทบอื่นๆ อีกมากมายต่อห่วงโซ่อุปทานทั่วโลก ยิ่งไปกว่านั้น การฟื้นตัวของยอดขายทั่วโลกในปี 2021 ยังได้รับผลกระทบอย่างรุนแรงจากผลที่ไม่คาดคิดของวิกฤตโควิด-2020 เมื่อปีที่แล้ว เมื่อผู้ผลิตยานยนต์ปิดโรงงานตามคำสั่งของรัฐบาลและลดคำสั่งซื้อชิ้นส่วนลงอย่างมากในปี XNUMX ผู้ผลิตเซมิคอนดักเตอร์ก็พบว่ามีธุรกิจทางเลือกในพื้นที่ เช่น อุปกรณ์อิเล็กทรอนิกส์สำหรับผู้บริโภค
เมื่อโรงงานผลิตรถยนต์ที่กำลังฟื้นตัวสั่งชิปเพิ่มมากขึ้นในไตรมาสแรกของปี 2021 ปัญหาด้านอุปทานที่ตึงตัวก็ปรากฏชัดเจนอย่างรวดเร็ว
การขาดแคลนเซมิคอนดักเตอร์ก็ไม่สามารถเอาชนะได้ง่ายเช่นกัน เนื่องจากระยะเวลาดำเนินการที่ยาวนานในการเพิ่มกำลังการผลิตชิปในโรงงานต้นทาง ชิ้นส่วนที่ขาดหายไปซึ่งมีความสำคัญต่อความปลอดภัยหรือถือเป็นสิ่งจำเป็นสำหรับผลิตภัณฑ์สำเร็จรูปในลักษณะอื่นๆ ส่งผลให้สายการผลิตบางรุ่นได้รับผลกระทบรุนแรงกว่ารุ่นอื่นๆ ผู้ผลิตยานยนต์สามารถปรับเปลี่ยนส่วนผสมทางการตลาดได้ในบางกรณี แต่สุภาษิตเก่าก็เป็นจริงอีกครั้ง: ห่วงโซ่อุปทานจะดี/แข็งแกร่งได้เท่ากับจุดที่อ่อนแอที่สุดเท่านั้น
วิธีการและกระบวนการจัดซื้อทั่วทั้งอุตสาหกรรมอยู่ภายใต้การตรวจสอบอย่างเข้มงวดมากขึ้นกว่าที่เคย
สิ่งที่น่าสังเกตอีกอย่างก็คือ มีองค์ประกอบเชิงโครงสร้างที่ทำงานอยู่ ซึ่งหมายความว่าแรงกดดันด้านอุปทานเซมิคอนดักเตอร์บางส่วนอาจยังคงเป็นความเสี่ยงในอนาคต นั่นก็คือ เนื้อหาอิเล็กทรอนิกส์ขั้นสูงของยานพาหนะกำลังเพิ่มขึ้นเนื่องจากการติดตั้งคุณสมบัติทางเทคโนโลยีที่ซับซ้อนมากขึ้นเรื่อยๆ ซึ่งทำให้บริษัทบางแห่งหันไปใช้พันธมิตรเชิงกลยุทธ์กับผู้ผลิตชิป ซึ่งไม่เพียงแต่จะช่วยให้มั่นใจได้ว่าจะมีอุปทานไมโครโปรเซสเซอร์ที่สำคัญในอนาคตเท่านั้น แต่ยังช่วยอำนวยความสะดวกให้เกิดความสัมพันธ์ในการพัฒนาผลิตภัณฑ์ในอนาคตที่เป็นประโยชน์ร่วมกัน ซึ่งเห็นได้ชัดว่าเป็นส่วนประกอบที่มีคุณค่าเชิงกลยุทธ์
แรงกดดันอื่นๆ ต่อห่วงโซ่อุปทานมีมาจากแหล่งอื่น เช่น การขาดแคลนแรงงานที่ไม่คาดคิด และราคาการขนส่งตู้คอนเทนเนอร์ระหว่างประเทศที่สูงขึ้นมาก เนื่องจากราคาพลังงานที่พุ่งสูงขึ้น
การถกเถียงเรื่องแหล่งทรัพยากรแบบคู่เทียบกับหลายแหล่ง
ความเปราะบางในห่วงโซ่อุปทานยานยนต์เกิดจากการที่ห่วงโซ่อุปทานมีหลายระดับ กระแสการจัดหาจากต่างประเทศ และแนวโน้มของการจัดหาจากแหล่งเดียวเพื่อเพิ่มการประหยัดจากขนาดในโครงการยานยนต์ทั่วโลก ในหลายกรณี โครงสร้างแบบดั้งเดิมนี้ยังฝังรากลึกอยู่ในวัฒนธรรมของพันธมิตรที่ต้องการในทุกระดับการจัดหา ข้อดีอาจรวมถึงระบบที่ใช้ร่วมกันและต้นทุนด้านโลจิสติกส์ โดยมีการกระจายต้นทุนระหว่างปริมาณการผลิตในรุ่นและระบบอื่นๆ ด้วยเช่นกัน
เทคโนโลยียังมีส่วนสนับสนุนการจัดหาแหล่งผลิตแบบเดียว เนื่องจากบริษัทต่างๆ รวมถึงบริษัทในระดับ 3 และ 4 มักจะรวมความเชี่ยวชาญและการลงทุนไว้ในสถานที่เดียวที่ใช้ในการผลิตปริมาณมาก ปัญหาเกิดขึ้นเมื่อมีบางอย่างผิดพลาดจนทำให้แผนต้องล่มสลาย (เช่น ไฟไหม้โรงงานไมโครโปรเซสเซอร์ Renesas เมื่อปีที่แล้ว)
อุปกรณ์อิเล็กทรอนิกส์และเซ็นเซอร์เป็นตัวอย่างของส่วนประกอบที่สำคัญสำหรับชิ้นส่วนย่อยที่อาจส่งผลกระทบอย่างมากต่อกระบวนการผลิตยานยนต์หากมีการหยุดชะงักในการผลิต การค้นหาซัพพลายเออร์ทางเลือกที่มีกำลังการผลิตสำรองในระยะเวลาอันสั้นถือเป็นความท้าทายอย่างยิ่ง
การสำรองชิ้นส่วนบางส่วนไว้ในสต็อกนั้นมีค่าใช้จ่ายและขัดต่อหลักการสำคัญของการผลิตแบบลีน แน่นอนว่าเราสามารถตัดสินใจได้ว่าจะดูดซับหรือตัดค่าใช้จ่ายที่เกิดจากการหยุดชะงักที่เกิดขึ้นหรือไม่ ซึ่งท้ายที่สุดแล้วจะขึ้นอยู่กับการประเมินความเสี่ยงเป็นปริมาณ
ประสบการณ์ในช่วงไม่กี่ปีที่ผ่านมาชี้ให้เห็นอย่างน้อยว่าบริษัทต่างๆ เริ่มตั้งคำถามมากขึ้นเรื่อยๆ ว่าการจัดหาแบบแยกส่วนนั้นน่าปรารถนาเหมือนแต่ก่อนหรือไม่ โลกที่เต็มไปด้วยความเสี่ยงและความไม่แน่นอนที่สูงขึ้นอาจต้องการแนวทางใหม่ การทำซ้ำภายในห่วงโซ่อุปทาน แม้ว่าจะหมายถึงการต้องแบ่งปันกับคู่แข่งก็ตาม อาจเป็นทางออกที่ดีกว่า - อย่างน้อยก็สำหรับส่วนประกอบบางส่วน - มากกว่าการจัดหาแบบแยกส่วน ความปลอดภัยของผลิตภัณฑ์ที่ดีขึ้นจะเป็นประโยชน์ของการจัดหาแบบแยกส่วน เช่นเคย เป็นเรื่องของต้นทุนโดยรวม
การใช้ไฟฟ้าและรูปแบบห่วงโซ่อุปทานใหม่
การใช้ไฟฟ้าสร้างความท้าทายใหม่ให้กับห่วงโซ่อุปทานในอนาคตของยานยนต์ ผู้ผลิตอุปกรณ์ดั้งเดิมต้องเผชิญกับความไม่แน่นอนอย่างมากเกี่ยวกับการจัดหาชิ้นส่วนใหม่และชิ้นส่วนสำคัญ โดยเฉพาะอย่างยิ่งแบตเตอรี่ระบบส่งกำลัง ซึ่งพวกเขากำลังพยายามแก้ไข นอกจากนี้ยังมีคำถามเชิงกลยุทธ์เกี่ยวกับระดับของการบูรณาการแนวตั้งที่พึงประสงค์เพื่อลดความเสี่ยงในอนาคตและควบคุมด้านการค้าของการจัดหา มีการจัดตั้งบริษัทร่วมทุนกับผู้เชี่ยวชาญด้านแบตเตอรี่ ส่วนประกอบสำคัญอื่นๆ สำหรับยานยนต์ไฟฟ้า เช่น มอเตอร์ ชิ้นส่วนระบบขับเคลื่อน อินเวอร์เตอร์แรงดันสูง จะต้องได้รับการลงทุนเพิ่มขึ้นควบคู่ไปกับการพิจารณาห่วงโซ่อุปทาน
กลยุทธ์การใช้ไฟฟ้าที่ทะเยอทะยานจะทำให้ความต้องการเซลล์แบตเตอรี่ลิเธียมไอออนเพิ่มสูงขึ้นอย่างรวดเร็ว ผู้ผลิตแบตเตอรี่ทั่วโลกต่างมุ่งมั่นที่จะขยายธุรกิจด้วยงบประมาณหลายพันล้านดอลลาร์ โดยเปิดโรงงานขนาดใหญ่แห่งใหม่เพื่อจัดหาเซลล์ให้กับผู้ผลิตรถยนต์
ตัวอย่างที่โดดเด่นอย่างหนึ่งของความร่วมมือเชิงลึกระหว่าง OEM และ Tier 1 ในพื้นที่นี้ ได้แก่ การลงนามบันทึกความเข้าใจระหว่าง Volkswagen และ Bosch บริษัททั้งสองมีแผนที่จะจัดหาระบบการผลิตแบตเตอรี่แบบบูรณาการ การปรับปรุงสถานที่ และการสนับสนุนการบำรุงรักษาสำหรับผู้ผลิตเซลล์แบตเตอรี่และระบบแบตเตอรี่ โดยทั้งสองบริษัทระบุว่าพวกเขามุ่งหวังที่จะเป็นผู้นำด้านต้นทุนและเทคโนโลยีในเทคโนโลยีแบตเตอรี่ในระดับอุตสาหกรรม และการผลิต 'แบตเตอรี่ที่ยั่งยืนและล้ำสมัย' ในปริมาณมาก
เฉพาะในยุโรป กลุ่ม Volkswagen มีแผนที่จะสร้างโรงงานผลิตเซลล์ 2030 แห่งภายในปี 700 และผู้ผลิตรายอื่นก็กำลังดำเนินการในลักษณะเดียวกันเพื่อจัดหาเซลล์และชุดแบตเตอรี่ในอนาคต ภูมิภาคนี้น่าจะมีกำลังการผลิตชุดแบตเตอรี่รวมต่อปีประมาณ 2030 กิกะวัตต์ชั่วโมงภายในปี XNUMX
เมื่อมองไปข้างหน้า บริษัทโตโยต้าได้ร่วมทุนกับบริษัทพานาโซนิค (Prime Planet Energy & Solutions – PPES) ซึ่งได้ลงนามในข้อตกลงกับบริษัทยักษ์ใหญ่ด้านเหมืองแร่อย่าง BHP เพื่อจัดหานิกเกิลซัลเฟตในอนาคต ซึ่งเป็นพื้นฐานของนิกเกิลในแคโทดของเซลล์แบตเตอรี่ลิเธียมไอออนส่วนใหญ่ นอกจากนี้ Tesla ยังได้ลงนามในข้อตกลงที่คล้ายกันกับ BHP ซึ่งแสดงให้เห็นว่าวัตถุดิบยังมีความสำคัญอย่างมากต่อความมั่นคงในการจัดหาในอนาคต
ข้อตกลงเหล่านี้เน้นย้ำถึงความจำเป็นที่ผู้ผลิตยานยนต์จะต้องมองไปยังห่วงโซ่อุปทานแบตเตอรี่ให้มากขึ้น เพื่อให้แน่ใจว่าพวกเขาสามารถเข้าถึงวัตถุดิบที่เพียงพอสำหรับการผลิตแบตเตอรี่ลิเธียมไอออนเพื่อรองรับการเติบโตของกำลังการผลิตมหาศาลที่จำเป็นสำหรับยานยนต์ไฟฟ้าแบตเตอรี่รุ่นใหม่ที่จะเปิดตัวในอีกไม่กี่ปีข้างหน้า การรีไซเคิลยังเป็นปัจจัยสำคัญในข้อตกลงหลายฉบับที่ทำไปแล้ว
บล็อคเชนสำหรับการมองเห็นห่วงโซ่อุปทาน
บริษัทผลิตรถยนต์จำนวนมากขึ้นเรื่อยๆ กำลังใช้เทคโนโลยีบล็อคเชนเพื่อให้เกิดความโปร่งใสในประเด็นห่วงโซ่อุปทาน เช่น การปล่อย CO2 และแหล่งที่มาของโคบอลต์สำหรับแบตเตอรี่ (ซึ่งอาจมาพร้อมกับคำถามทางจริยธรรมที่เกี่ยวข้องกับการขุดแร่อันมีค่า)
แนวคิดเดิมของบล็อคเชนนั้น ตามชื่อก็บอกอยู่แล้วว่าเป็นห่วงโซ่ของบล็อคหรือบันทึกที่มีการประทับเวลา (บล็อค = ข้อมูลดิจิทัล ห่วงโซ่ = ฐานข้อมูลสาธารณะ/ชุมชน) บล็อคจะจัดเก็บข้อมูลเกี่ยวกับธุรกรรม เมื่อบล็อคจัดเก็บข้อมูลใหม่ ซึ่งก็คือธุรกรรม ข้อมูลนั้นจะถูกเพิ่มเข้าไปในบล็อคเชน และเมื่อได้รับการยืนยันโดยเครือข่ายคอมพิวเตอร์แบบเพียร์ทูเพียร์แล้ว ใครๆ ก็สามารถดูข้อมูลนั้นได้ (หรืออาจต้องได้รับอนุญาตจากเครือข่ายส่วนตัว เช่น ห่วงโซ่อุปทานของ OEM ซึ่งก็คือ 'บัญชีแยกประเภทแบบกระจาย')
อย่างไรก็ตาม ทุกฝ่ายมีสิทธิ์เข้าถึงข้อมูลเฉพาะที่ตนได้รับอนุญาตให้ดูเท่านั้น คอมพิวเตอร์แต่ละเครื่องในเครือข่ายบล็อคเชนจะมีสำเนาของบล็อคเชนเป็นของตัวเอง อย่างไรก็ตาม ตามหลักการแล้ว แนวคิดคือการสร้างระบบที่โปร่งใสสูงโดยไม่มีค่าใช้จ่ายในการทำธุรกรรมระหว่างสองฝ่ายที่สร้างบล็อคขึ้นมา
เราคาดว่าจะได้เห็นบริษัทผลิตรถยนต์นำกระบวนการบล็อคเชนมาใช้มากขึ้น โดยเฉพาะอย่างยิ่งกระบวนการบัญชีแยกประเภทแบบกระจาย (เช่น เครือข่ายส่วนตัว) เพื่อลดความเสี่ยงของการ "หยุดชะงัก" ของห่วงโซ่อุปทาน และเพื่อทำความเข้าใจจุดแข็งและจุดอ่อนตลอดห่วงโซ่ แต่ยังเป็นวิธีแสดงให้เห็นถึงความต้องการที่เพิ่มมากขึ้นในการปฏิบัติตามกฎระเบียบในด้านต่างๆ เช่น ความยั่งยืนอีกด้วย
บทเรียนจากโตโยต้า
โดยทั่วไปแล้ว โตโยต้าถือเป็นบริษัทที่มีผลงานดีที่สุดในอุตสาหกรรมยานยนต์ในด้านการจัดการห่วงโซ่อุปทาน นอกจากจะเป็นผู้ริเริ่มวิธีการผลิตแบบลีนซึ่งต่อมาได้กลายเป็นแนวทางปฏิบัติที่ดีที่สุดที่ผู้ผลิตอุปกรณ์ดั้งเดิมและซัพพลายเออร์รายใหญ่ส่วนใหญ่นำไปใช้แล้ว โตโยต้ายังได้ปรับปรุงระบบและกระบวนการต่างๆ ให้สอดคล้องกับสถานการณ์ที่เปลี่ยนแปลงไปเกี่ยวกับมาตรการบรรเทาความเสี่ยง นอกจากนี้ โตโยต้ายังทำงานอย่างใกล้ชิดกับซัพพลายเออร์ในบางครั้งและเพื่อประโยชน์ของเป้าหมายของภาคส่วนที่กว้างขึ้นเมื่อเผชิญกับสถานการณ์ฉุกเฉิน
หลังจากเหตุการณ์แผ่นดินไหวและคลื่นสึนามิที่เกียวโตในปี 2011 โตโยต้าได้ทำงานร่วมกับซัพพลายเออร์ในญี่ปุ่นเพื่อจัดทำฐานข้อมูลที่ครอบคลุมเกี่ยวกับข้อมูลห่วงโซ่อุปทานเพื่อสนับสนุนภาคการผลิตของญี่ปุ่น นอกจากนี้ โตโยต้ายังได้แนะนำกลยุทธ์ในการจัดหาชิ้นส่วนสำคัญจากหลายแหล่ง ซึ่งหมายถึงการจัดการจัดหาจากสามแหล่งที่แตกต่างกัน แต่ซัพพลายเออร์หลักจะจัดเตรียมการผลิตเกือบสองในสามของคำสั่งซื้อเพื่อให้แน่ใจว่าประหยัดจากขนาด ซัพพลายเออร์หลายรายอาจส่งผลกระทบต่อการประหยัดจากขนาด แต่ก็หมายความว่ามีทางเลือกอื่นหากจำเป็น
นอกจากนี้ โตโยต้ายังมีระบบที่พัฒนาอย่างดีสำหรับตรวจสอบเครือข่ายซัพพลายเออร์จำนวนมากและระบบเตือนล่วงหน้าสำหรับการขาดแคลน บริษัทบางแห่งหันมาใช้ AI เพื่อประเมินการพัฒนาในห่วงโซ่อุปทานของตน แม้ว่าจะต้องอาศัยฐานข้อมูลที่เชื่อถือได้ ครอบคลุม และมีรายละเอียดตั้งแต่แรกก็ตาม
ทางเลือกอื่นสำหรับบริษัทต่างๆ คือ การสำรองชิ้นส่วนสำคัญไว้ในกรณีฉุกเฉินหรือสำรองสต็อกไว้ โดยเฉพาะอย่างยิ่งชิ้นส่วนที่อาจทำให้สายการผลิตต้องหยุดลง ซึ่งก็หมายความว่าจะต้องมีต้นทุนเพิ่มเติมในการจัดเก็บหรือเก็บสินค้าในคลังสินค้า แต่ก็ต้องตัดสินใจว่าจะจ่ายต้นทุนหรือ "เบี้ยประกัน" ในระดับใดจึงจะคุ้มค่า นอกจากนี้ วิธีนี้ยังไม่สามารถแก้ปัญหาได้ถาวร โตโยต้าอาจมีเซมิคอนดักเตอร์สำรองไว้บ้าง แต่การขาดแคลนชิปทั่วโลกทำให้ในท้ายที่สุด โตโยต้าก็ต้องลดการผลิตลงเช่นกัน บทเรียนที่สำคัญที่สุดจากโตโยต้าอาจเป็นความจำเป็นในการทบทวนและปรับตัวให้เข้ากับสถานการณ์และความไม่แน่นอนที่เปลี่ยนแปลงอยู่ตลอดเวลา
ที่มาจาก เพียงแค่อัตโนมัติ
ข้อสงวนสิทธิ์: ข้อมูลที่ระบุไว้ข้างต้นจัดทำโดย just-auto.com โดยเป็นอิสระจาก Chovm.com Chovm.com ไม่รับรองหรือรับประกันคุณภาพและความน่าเชื่อถือของผู้ขายและผลิตภัณฑ์