In 2024, the demand for arc welding equipment surged, driven by advancements in automation and AI integration. As the market is projected to reach USD 7.2 billion by 2030, business buyers must stay informed about the latest trends and technologies to make strategic purchasing decisions. This guide provides comprehensive insights into selecting the best arc welders for wholesalers, retailers, and purchasing professionals.
Table of Contents:
Arc Welder Market Overview
Detailed Market Analysis
Key Factors When Selecting an Arc Welder
Latest Technology Features in Arc Welders
Energy Efficiency and Environmental Impact
Customer Support and Warranty
Final Thoughts
Arc Welder Market Overview
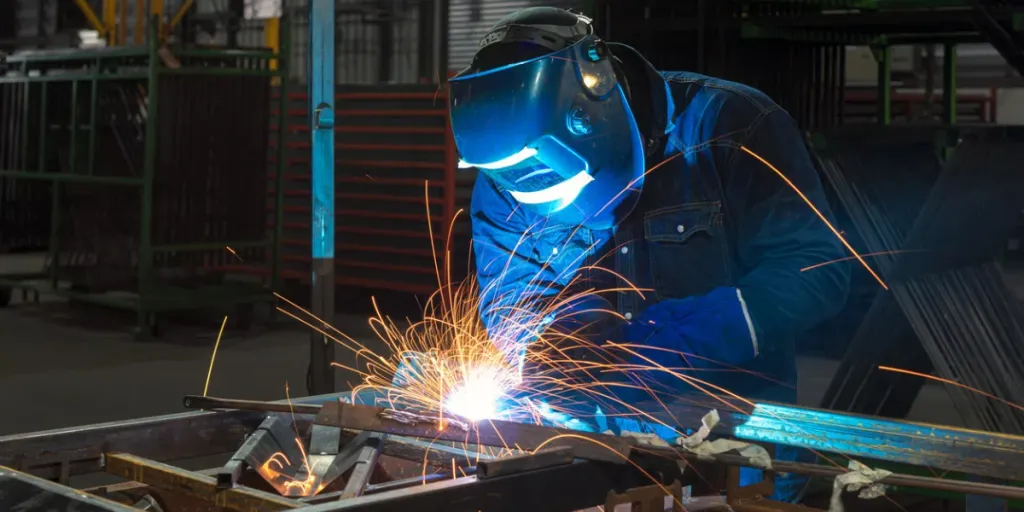
The global Arc Welding Equipment market is growing steadily, with an estimated value of USD 5.2 billion in 2023 and a projected value of USD 7.2 billion by 2030. This represents a compound annual growth rate (CAGR) of 4.2% from 2023 to 2030. The market’s expansion is driven by the increasing demand for welding equipment in various sectors, notably in energy, utilities, and automotive industries. The energy and utilities segment alone is expected to reach USD 2.2 billion by 2030, growing at a CAGR of 5.1%. Similarly, the automotive sector is anticipated to grow at a CAGR of 4.3%, reflecting the ongoing need for advanced welding solutions in vehicle manufacturing.
Regionally, the United States market was valued at USD 1.4 billion in 2023. China’s market, on the other hand, is set to grow at an impressive CAGR of 6.5%, reaching USD 1.6 billion by 2030. Other significant regions include Japan, Canada, Germany, and the broader Asia-Pacific, each contributing to the global growth of the arc welding equipment market.
Detailed Market Analysis
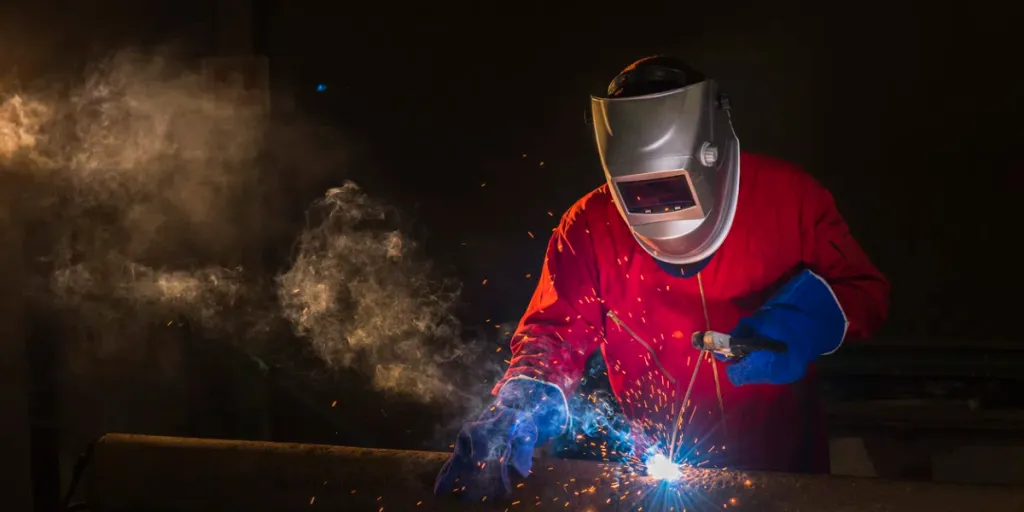
Key Performance Benchmarks
The arc welding equipment market’s performance is measured by its application in various industries and technological advancements. The market’s growth is underpinned by innovations in welding technologies that enhance efficiency, precision, and safety. For instance, the rise of automated and semi-automated welding machines is improving productivity and reducing human error. The integration of AI and machine learning in welding equipment is also notable, allowing for real-time adjustments and improved welding outcomes.
Market Share Dynamics
Market share dynamics reveal a competitive landscape with several key players. Major companies like Amada Miyachi Co., Ltd., American Torch Tip, and Arc Machines, Inc. are leading the way with innovative products and strategic market positioning. The market is fragmented, with significant contributions from both established players and new entrants. This competitive environment drives continuous innovation and improvements in product offerings.
Economic Influences and Consumer Behavior Shifts
Economic factors, such as the rising demand for infrastructure development and the growth of the automotive and energy sectors, significantly influence the market. Consumer behavior is shifting towards the adoption of more efficient and cost-effective welding solutions. There is a growing preference for automated welding equipment, driven by the need for higher precision and lower operational costs. Seasonal demand patterns also play a role, with peak periods aligning with major industrial and construction projects.
Distribution Channel Preferences
Distribution channels for arc welding equipment include direct sales, distributors, and online platforms. Direct sales and distributors remain dominant, providing personalized services and technical support. However, the rise of e-commerce is gradually changing the landscape, offering convenience and broader reach to end-users.
Recent Innovations
Recent innovations in arc welding equipment focus on enhancing automation, precision, and safety. For example, the development of user-friendly programming interfaces and offline programming software allows operators to simulate and adjust welding paths before execution, reducing setup times and minimizing downtime. Collaborative robots, or cobots, designed to work alongside human operators, are also emerging, enhancing flexibility and enabling more complex or custom welding tasks.
Product Lifecycle Stages
The product lifecycle of arc welding equipment typically includes the introduction, growth, maturity, and decline stages. Currently, many advanced welding technologies are in the growth stage, characterized by increasing adoption and continuous improvements. As these technologies mature, the focus will likely shift towards enhancing cost-efficiency and expanding applications.
Digitalization and Social Trends
Digitalization is transforming the arc welding equipment market. The integration of IoT and data analytics enables real-time monitoring and predictive maintenance, improving operational efficiency and reducing downtime. Social trends, such as the emphasis on workplace safety and environmental sustainability, are also influencing market dynamics. Companies are increasingly adopting eco-friendly welding solutions and technologies that reduce harmful emissions.
Environmental Regulations
Environmental regulations are playing a crucial role in shaping the arc welding equipment market. Governments worldwide are implementing stringent standards to reduce industrial emissions and promote sustainable practices. Compliance with these regulations drives the adoption of advanced welding technologies that are more energy-efficient and environmentally friendly.
Customer Pain Points
Key customer pain points include the high initial costs of advanced welding equipment and the need for skilled operators. Ongoing maintenance and repair costs also pose challenges. Addressing these pain points involves providing cost-effective solutions, offering training programs for operators, and enhancing the durability and reliability of welding equipment.
Brand Positioning Strategies
Brand positioning strategies in the arc welding equipment market focus on innovation, quality, and customer service. Leading companies emphasize their technological advancements and reliability to differentiate themselves from competitors. Building strong relationships with customers through excellent after-sales support and technical assistance is also a critical strategy.
Differentiation Strategies
Differentiation strategies include offering customized solutions tailored to specific industry needs, integrating advanced technologies like AI and IoT, and ensuring compliance with environmental regulations. Companies that can provide high-quality, efficient, and eco-friendly welding solutions are likely to gain a competitive edge.
Niche Markets
Niche markets within the arc welding equipment industry include specialized applications in aerospace, medical device manufacturing, and renewable energy sectors. These markets require highly precise and reliable welding solutions, presenting opportunities for companies that can meet these specific demands.
In summary, the arc welding equipment market is poised for significant growth, driven by technological advancements, increasing demand in key industries, and the adoption of digitalization and sustainable practices. Companies that can innovate and address customer pain points while navigating regulatory challenges will be well-positioned to succeed in this dynamic market.
Key Factors When Selecting an Arc Welder
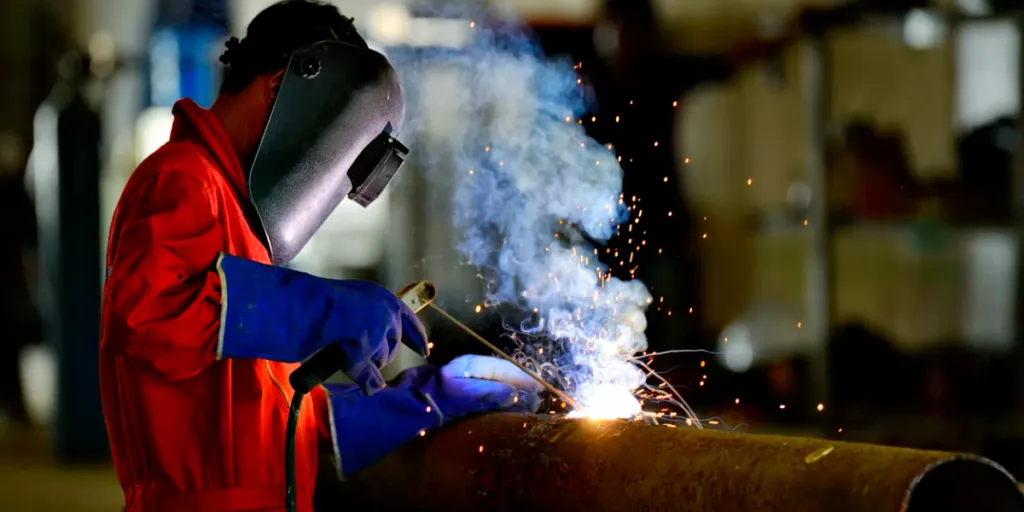
Choosing the right arc welder is crucial for optimal performance, safety, and efficiency in welding operations. Consider various factors to ensure the welder’s functionality and suitability for specific tasks.
Types of Arc Welders
Different arc welders are designed for various welding processes and materials. The most common types include:
- Shielded Metal Arc Welding (SMAW): This versatile and simple method uses a consumable electrode coated in flux. It’s suitable for welding ferrous and non-ferrous metals and is ideal for outdoor and field applications due to its portability and adaptability to various conditions.
- Gas Metal Arc Welding (GMAW), also known as MIG welding: This method uses a continuously fed wire electrode and shielding gas to protect the weld pool. It’s preferred for its high welding speed and ease of automation, making it suitable for large-scale production and industrial applications.
- Gas Tungsten Arc Welding (GTAW), or TIG welding: This method uses a non-consumable tungsten electrode and an inert gas shield to produce high-quality, precise welds. It’s commonly used for welding thin materials and applications requiring superior weld quality, such as in aerospace and automotive industries.
Performance and Functionality
The performance and functionality of an arc welder depend on several specifications:
- Amperage Range: Dictates the material thickness that can be welded. A wide range offers greater versatility for various tasks.
- Duty Cycle: Indicates the percentage of time a welder can operate without overheating. A higher duty cycle is crucial for prolonged welding operations and industrial applications.
- Arc Stability: Ensures consistent and smooth welding, crucial for high-quality welds. Advanced features like inverter-based power sources and pulse welding enhance arc stability and control.
Technical Specifications
Key specifications to consider include:
- Input Voltage: Varies depending on the power source and application. Most welders are designed for single-phase or three-phase power supplies, ranging from 110V to 480V.
- Output Power: Measured in amperes, it determines the welder’s capacity to handle different tasks. Higher output power is suitable for heavy-duty welding.
- Compatibility: Some welders are designed for specific processes, while others offer multi-process capabilities, allowing users to switch between SMAW, GMAW, and GTAW.
Safety Standards and Certifications
Selecting an arc welder that meets industry safety standards and certifications is crucial. Compliance with standards set by organizations like ANSI, ISO, and OSHA ensures safety. Certifications such as the CE mark and UL certification indicate adherence to safety requirements, reducing the risk of accidents.
Durability and Build Quality
Durability and build quality are essential for long-term performance. Look for welders constructed with high-quality materials and robust components. Features like a rugged chassis, reinforced cables, and advanced cooling systems enhance durability. Regular maintenance and proper care also extend the equipment’s lifespan.
Latest Technology Features in Arc Welders
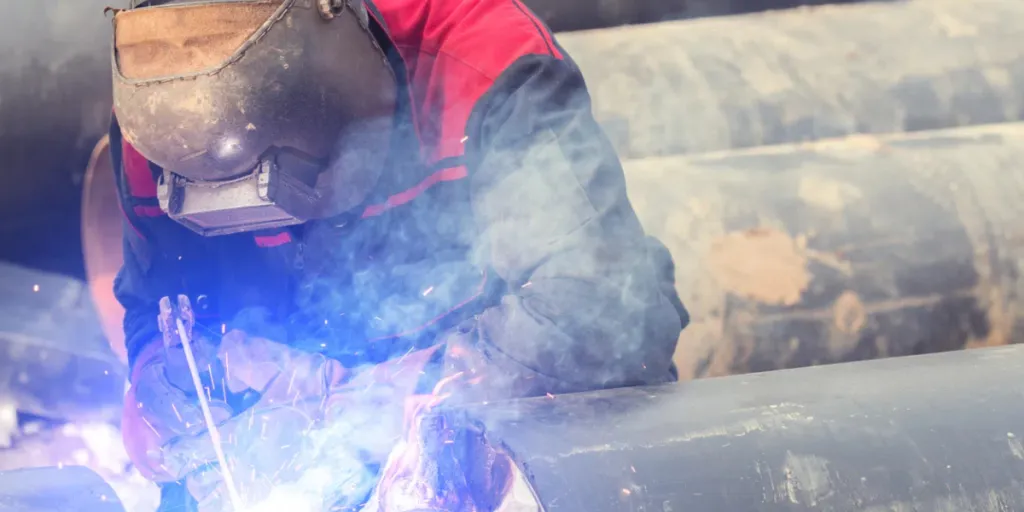
Modern arc welders incorporate innovative features to improve efficiency, precision, and ease of use:
- Inverter Technology: Inverter-based welders are more compact, lightweight, and energy-efficient compared to traditional welders. They offer better control over the welding process.
- Pulse Welding: This technology alternates between high and low current levels, improving heat control and reducing distortion. It’s beneficial for welding thin materials and achieving high-quality welds.
- Digital Interfaces and Programmable Settings: These features enable users to save and recall welding parameters, ensuring consistent results. Some welders offer remote control capabilities for added convenience.
Energy Efficiency and Environmental Impact
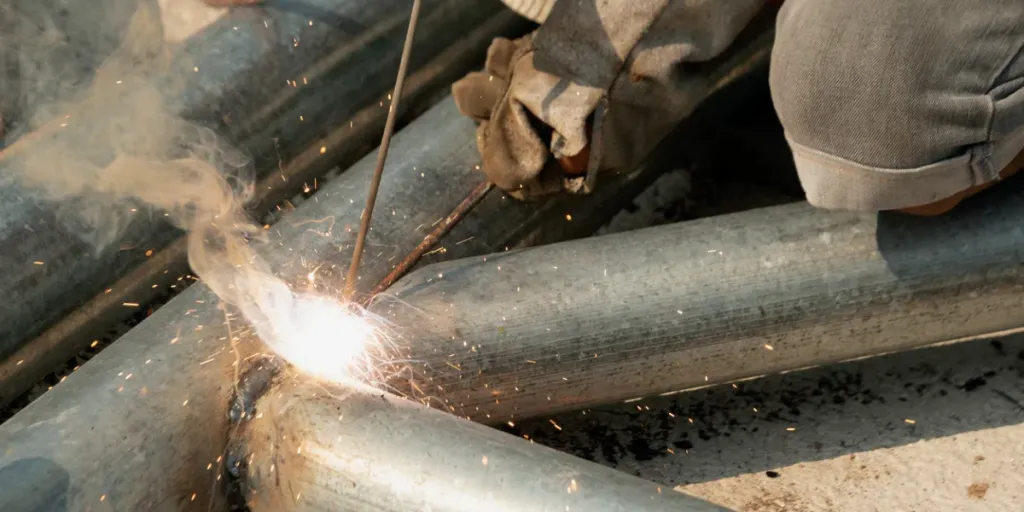
Energy efficiency is critical for operational costs and environmental sustainability. Inverter-based welders consume less power while delivering superior performance. Many manufacturers now focus on eco-friendly welders that minimize energy consumption and emissions. Some welders feature power-saving modes that reduce power consumption when idle.
Customer Support and Warranty
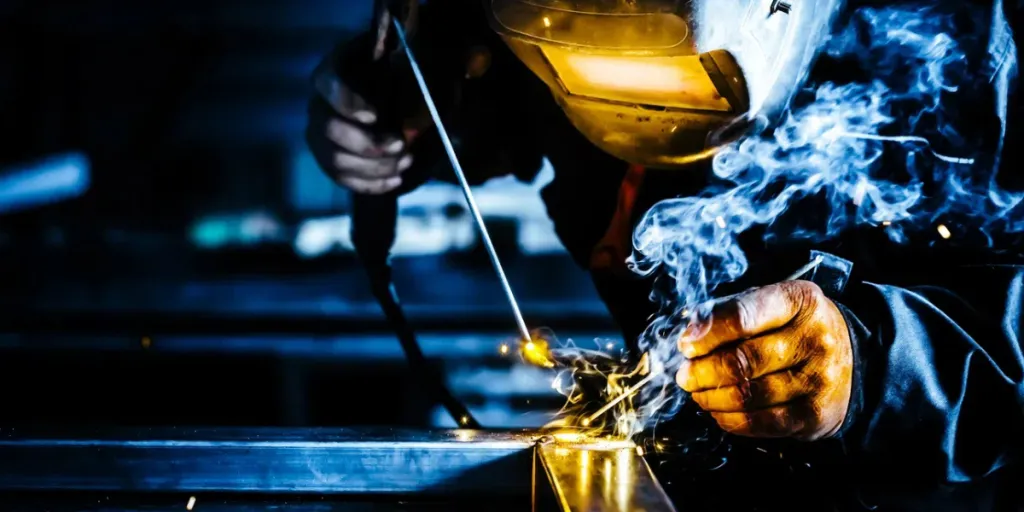
Reliable customer support and warranty are essential. Reputable manufacturers offer comprehensive support services, including technical assistance and repair services. A robust warranty, typically ranging from one to three years, provides peace of mind. Review warranty terms and consider extended warranty options for additional protection.
Final Thoughts
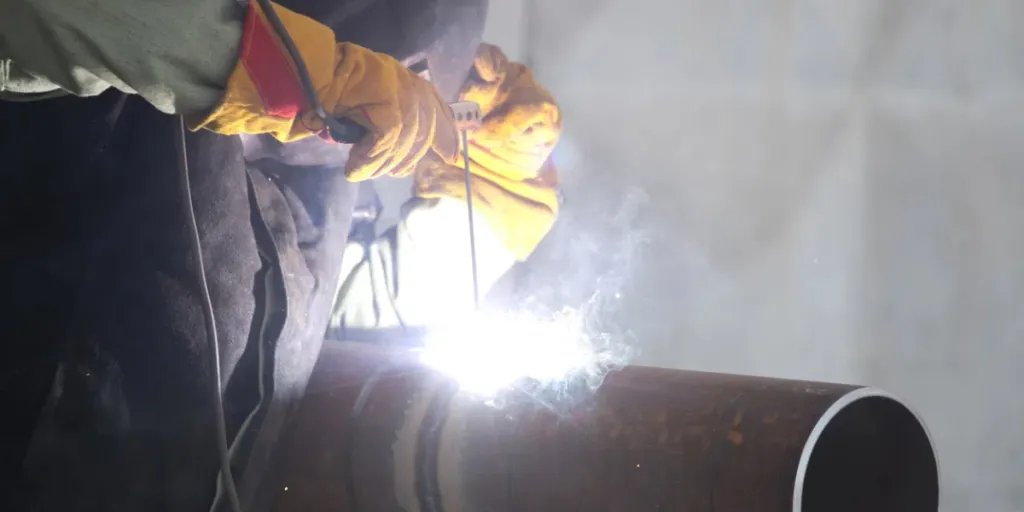
Selecting the right arc welder involves careful consideration of various factors, including types of welders, performance, technical specifications, safety standards, durability, technology features, energy efficiency, and customer support. By evaluating these factors, businesses can make informed decisions and choose the most suitable arc welder for their needs.