The demand for spot welding in 2025 has surged due to innovations in the automotive and electronics sectors. This article delves into critical aspects of selecting spot welding equipment, including technical specifications, material compatibility, and safety standards. Professional buyers will find valuable insights to enhance decision-making and optimize their procurement strategies.
İçindekiler:
– Market Overview of Spot Welding
– Detailed Analysis of the Spot Welding Market
– Key Factors When Selecting Spot Welding Equipment
– Latest Technological Advancements in Spot Welding
– Ensuring Regulatory Compliance and Safety in Spot Welding
- Sonuç
Market Overview of Spot Welding
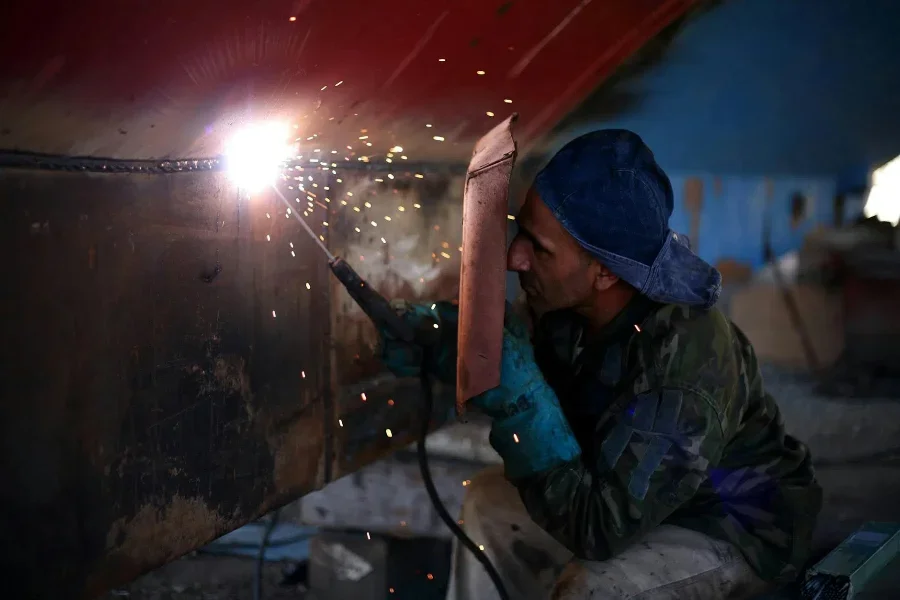
The spot welding market has shown substantial growth, mainly driven by demand in the automotive and electronics industries. As of 2024, the global welding machinery market, including spot welding, was worth USD 30.58 billion. It is expected to reach USD 47.52 billion by 2030, growing at a compound annual growth rate (CAGR) of 7.54%. This growth highlights the increasing adoption of automated welding solutions and the expansion of manufacturing activities worldwide.
In terms of regional distribution, the Asia-Pacific region leads the spot welding market, driven by rapid industrialization and automotive sector expansion. China, Japan, and India contribute significantly, with a combined market share exceeding 45%. The Americas, particularly the United States, also play a crucial role with substantial investments in automotive and aerospace manufacturing, boosting the demand for advanced welding technologies.
Technological advancements in welding machinery, such as laser welding integration and robotic automation, drive market growth. The development of more efficient and cost-effective spot welding solutions is expected to accelerate market expansion. The introduction of new materials, including high-strength steels and aluminum alloys, requires advanced welding techniques, increasing the demand for sophisticated spot welding equipment.
Detailed Analysis of the Spot Welding Market
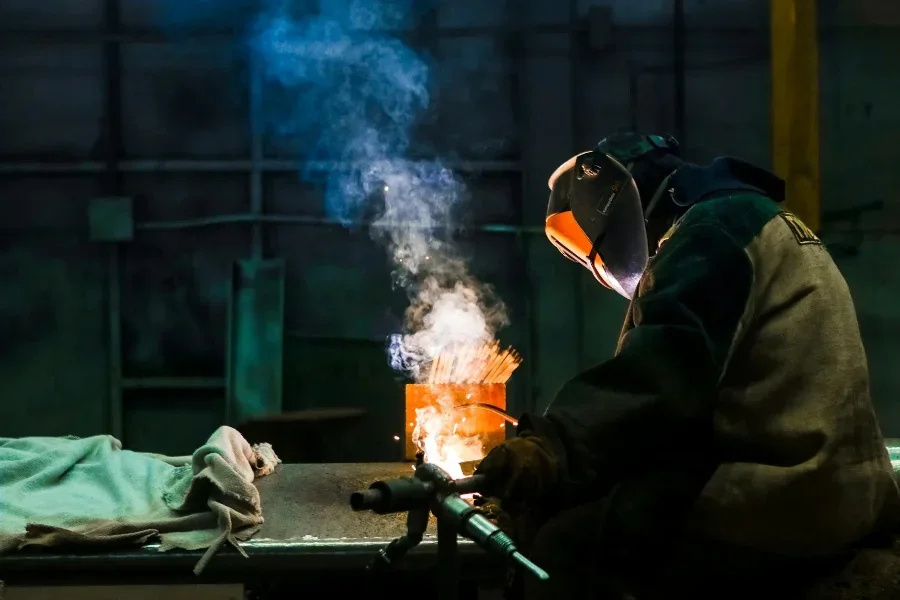
Spot welding, a resistance welding process, is essential in various manufacturing sectors due to its efficiency, speed, and reliability. The automotive industry remains the largest end-user, accounting for over 40% of the market share. The rising production of electric vehicles (EVs) and the need for lightweight, high-strength materials are driving the demand for advanced spot welding technologies.
Key performance benchmarks in the spot welding industry include weld strength, cycle time, and energy efficiency. Modern spot welding machines feature sophisticated controls and monitoring systems to ensure consistent weld quality and minimize defects. The adoption of automated and semi-automated spot welding systems is increasing, driven by the need to boost productivity and reduce labor costs.
Economic factors such as fluctuating raw material prices and the availability of skilled labor impact market dynamics. The high initial investment and maintenance costs of advanced welding equipment pose challenges for small and medium-sized enterprises (SMEs). However, government initiatives promoting industrial automation and digitalization are expected to mitigate these challenges and support market growth.
Recent innovations in spot welding include hybrid welding systems combining resistance welding with laser technology. These systems offer improved weld quality, reduced cycle times, and enhanced flexibility in welding complex geometries. The introduction of Industry 4.0 technologies, such as the Industrial Internet of Things (IIoT) and artificial intelligence (AI), is revolutionizing welding processes by enabling real-time monitoring, predictive maintenance, and adaptive control.
Customer pain points in the spot welding market mainly involve the need for skilled operators, equipment maintenance, and integrating new technologies. Manufacturers are addressing these issues by offering training programs, developing user-friendly interfaces, and providing comprehensive after-sales support. Differentiation strategies include developing customizable welding solutions, focusing on specific industry requirements, and enhancing the overall customer experience.
Leading players such as Lincoln Electric, Miller Electric, and ESAB are leveraging their extensive product portfolios and global distribution networks to maintain a competitive edge. These companies invest heavily in research and development to introduce innovative products and expand their market presence in emerging economies.
The spot welding market is poised for significant growth, driven by technological advancements, increasing automation, and the expanding automotive and electronics sectors. Focusing on enhancing weld quality, reducing operational costs, and addressing customer pain points will be crucial for market players to capitalize on emerging opportunities in this dynamic industry.
Key Factors When Selecting Spot Welding Equipment
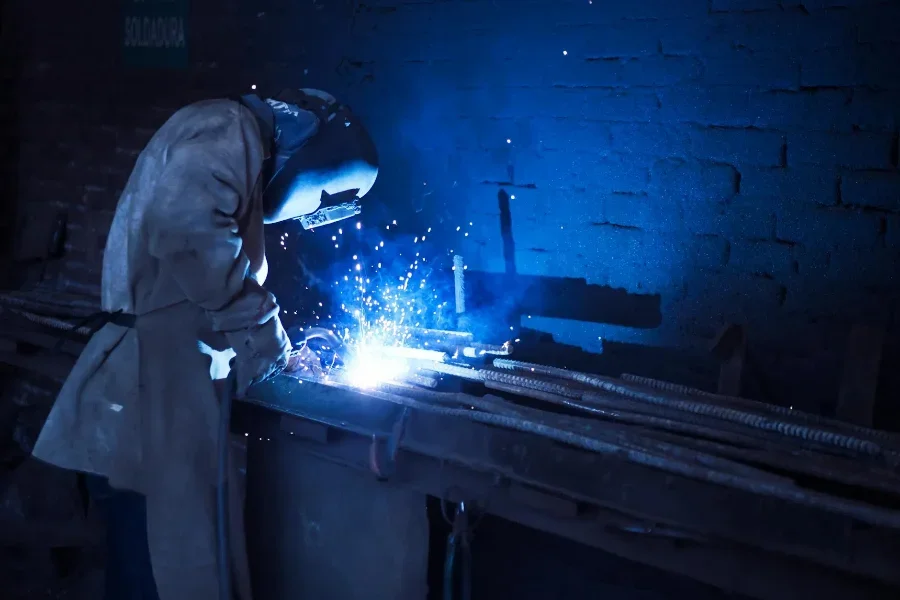
When selecting spot welding equipment, several key factors must be considered to ensure optimal performance and compatibility with specific applications. These include technical specifications, material compatibility, safety standards, and cost considerations.
Teknik özellikler
Spot welding equipment varies significantly in terms of technical specifications. Key parameters include:
Current Range and Control: The current range is crucial as it determines the equipment’s capability to weld different thicknesses and types of metals. Standard spot welders typically operate within a range of 1,000 to 10,000 amperes. Precision control of the current is essential for consistent weld quality. Advanced equipment offers programmable current settings, allowing for adjustments based on specific material requirements.
elektrot kuvveti: The force applied by the electrodes is another vital parameter. Insufficient force can lead to weak welds, while excessive force may cause material deformation. Modern spot welding machines feature adjustable electrode force settings, typically ranging from 200 to 2,000 pounds, to accommodate various material thicknesses and types.
Devir süresi: Cycle time, or the duration of the welding process, affects production efficiency. High-speed spot welders with cycle times as low as 0.1 seconds per weld are ideal for mass production environments. The ability to control and minimize cycle time without compromising weld quality is a significant advantage in high-volume manufacturing.
Malzeme Uyumluluğu
Different materials require specific welding parameters and equipment capabilities:
Çelik ve Paslanmaz Çelik: Spot welding is highly effective for steel and stainless steel due to their electrical and thermal conductivity. Equipment designed for these materials often features robust current and force settings. For stainless steel, precise control of heat input is crucial to avoid oxidation and maintain material integrity.
Aluminum and Non-Ferrous Metals: Aluminum and other non-ferrous metals pose challenges due to their high thermal conductivity and lower melting points. Specialized spot welding machines with advanced cooling systems and precise current control are necessary. Equipment designed for aluminum often includes features like dual-pulse welding to preheat the material and ensure a strong weld.
Coated and Dissimilar Metals: Welding coated metals or dissimilar metals requires equipment with adaptive control systems that can adjust parameters in real-time to accommodate varying material properties. Advanced spot welders may include features such as automatic material recognition and adaptive welding programs.
Güvenlik Standartları
Adhering to safety standards is paramount in any welding operation:
Sertifikalar: Ensure the spot welding equipment complies with international safety standards such as ISO 9692 and AWS D1.1. These certifications guarantee that the equipment meets stringent safety and performance criteria. Manufacturers should provide documentation of compliance with these standards.
Koruyucu Özellikler: Modern spot welders are equipped with safety features such as automatic shut-off mechanisms, overload protection, and insulated electrode holders to prevent electrical hazards. Operator safety can be further enhanced with features like ergonomic design, minimal heat radiation, and efficient fume extraction systems.
Maliyet Hususları
Balancing cost with performance and features is essential:
İlk Yatırım: High-quality spot welding equipment can range from $10,000 to over $100,000, depending on the specifications and features. While the initial investment is significant, advanced machines offer better efficiency and durability. Consider long-term benefits such as reduced maintenance costs, higher production rates, and improved weld quality when evaluating the initial investment.
Operasyonel Maliyetler: Operational costs include energy consumption, maintenance, and consumables like electrodes. Energy-efficient models with features like programmable energy settings can significantly reduce operational costs. Regular maintenance and the availability of affordable replacement parts also impact the overall cost of ownership.
Yatırım Getirisi (ROI): Calculate the ROI by considering factors such as increased production speed, reduced downtime, and improved weld quality. Advanced spot welders with higher upfront costs often provide a quicker ROI through enhanced performance and reliability.
Dayanıklılık ve Kalite
The build quality and durability of spot welding equipment are critical for ensuring long-term performance:
İnşaat malzemeleri: High-quality spot welding machines are constructed from durable materials such as reinforced steel and high-grade aluminum. These materials provide structural integrity and resistance to wear and tear. Components like electrodes and electrode holders should be made from high-conductivity materials to ensure consistent performance and longevity.
Üretici İtibarı: Choose equipment from reputable manufacturers with a proven track record in the industry. Established brands often provide better customer support, warranty options, and reliable performance. Research customer reviews and case studies to gauge the reliability and quality of the equipment.
Servis ve Destek: Availability of technical support and service centers is crucial for minimizing downtime. Manufacturers offering comprehensive support services, including on-site training and regular maintenance, ensure smooth operation. Consider extended warranty options and service contracts to protect your investment and ensure uninterrupted production.
Latest Technological Advancements in Spot Welding
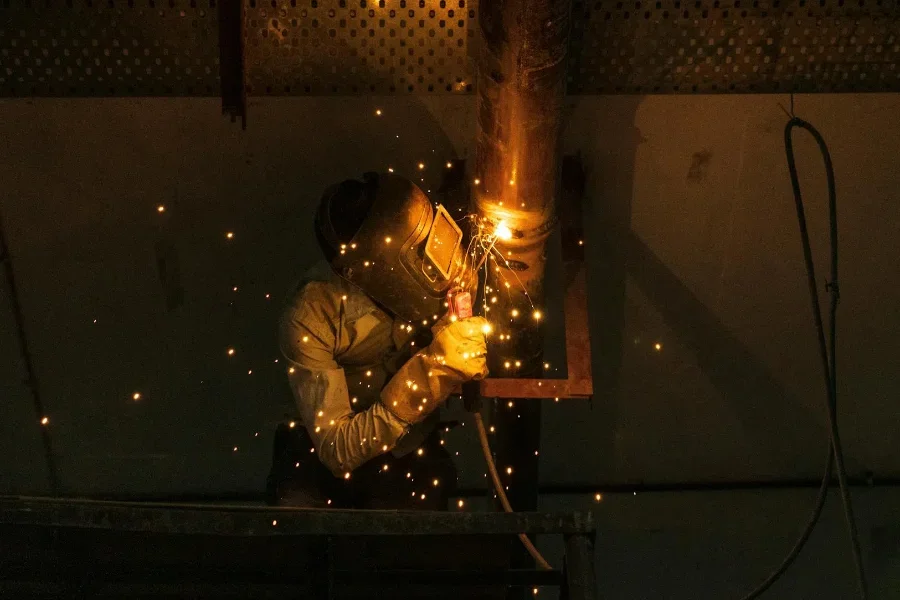
The spot welding industry has seen significant technological advancements aimed at improving efficiency, precision, and safety. Here are some of the latest innovations:
Gelişmiş Kontrol Sistemleri
Modern spot welding machines are equipped with sophisticated control systems:
Programlanabilir Lojik Kontrolörler (PLC'ler): PLCs allow for precise control over welding parameters and the ability to store multiple welding programs for different materials and applications. These controllers enable real-time monitoring and adjustments, ensuring consistent weld quality and reducing the risk of defects.
Adaptive Welding Technology: Adaptive welding technology uses sensors and real-time data to adjust welding parameters dynamically. This technology ensures optimal weld quality by compensating for variations in material properties and thickness. It is particularly useful for welding coated or dissimilar metals, where traditional fixed-parameter welding may result in inconsistent welds.
Gelişmiş Soğutma Sistemleri
Efficient cooling systems are essential for maintaining weld quality and equipment longevity:
Water-Cooled Electrodes: Water-cooled electrodes help dissipate heat more effectively than air-cooled counterparts, allowing for higher welding currents and longer continuous operation. This feature is particularly beneficial for high-volume production environments, where equipment is subject to prolonged use.
Entegre Soğutma Kanalları: Modern spot welders feature integrated cooling channels within the welding gun and electrodes, ensuring uniform heat distribution and preventing overheating. This design improves the overall efficiency and lifespan of the equipment.
Otomasyon ve Robotik
Automation and robotics have revolutionized spot welding by enhancing precision and productivity:
Robotic Spot Welding: Robotic spot welding systems provide unparalleled accuracy and repeatability, making them ideal for complex and high-volume applications. These systems can be programmed to perform precise welding operations, reducing the risk of human error and increasing production speed.
İşbirlikçi Robotlar (Cobot'lar): Cobots are designed to work alongside human operators, enhancing flexibility and safety in the welding process. They can be easily programmed and reconfigured for different tasks, making them suitable for small to medium-sized production runs. Cobots offer a cost-effective solution for manufacturers looking to integrate automation without significant infrastructure changes.
Enerji verimliliği
Energy-efficient spot welding equipment reduces operational costs and environmental impact:
İnvertör Teknolojisi: Inverter-based spot welders offer greater energy efficiency compared to traditional transformer-based models. They provide precise control over welding currents and reduce energy consumption by up to 30%. These machines are also more compact and lightweight, making them easier to integrate into existing production lines.
Enerji Geri Kazanım Sistemleri: Advanced spot welders feature energy recovery systems that capture and reuse energy generated during the welding process. This technology reduces overall energy consumption and operational costs. Energy recovery systems are particularly beneficial in high-volume production environments, where energy savings can be substantial.
Ensuring Regulatory Compliance and Safety in Spot Welding
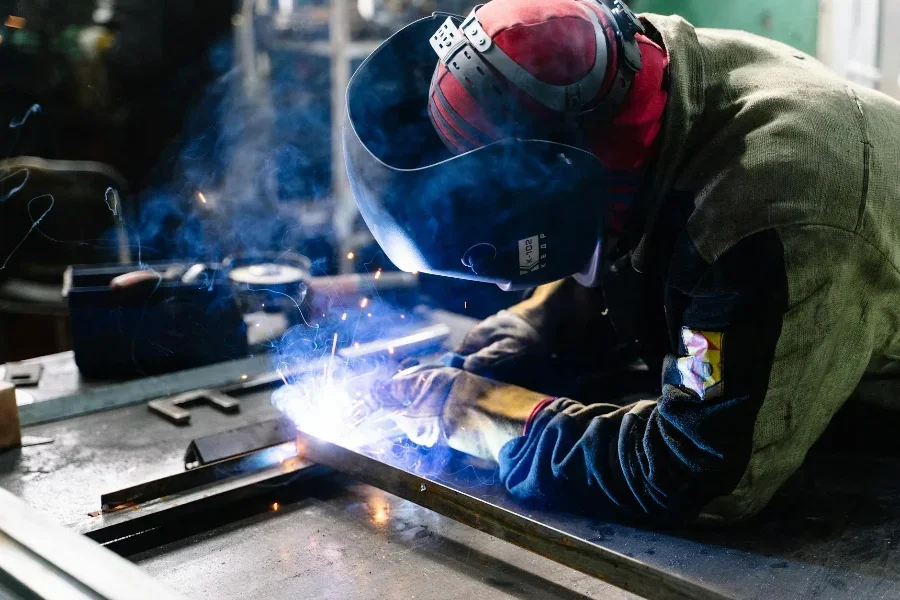
Compliance with regulatory standards and ensuring safety are critical aspects of spot welding operations. Adhering to these standards not only ensures the safety of operators but also guarantees the quality and reliability of the welds.
Düzenleyici Standartlar
Spot welding equipment and operations must comply with various international standards:
ISO 9692 – Welding and Allied Processes: ISO 9692 provides guidelines for the preparation of materials and the execution of welding processes. Compliance with this standard ensures that welding operations meet international quality and safety benchmarks. Manufacturers should provide documentation of compliance with ISO 9692 to assure customers of their product’s reliability and safety.
AWS D1.1 – Structural Welding Code: The American Welding Society’s (AWS) D1.1 code outlines requirements for structural welding, including material specifications, welding procedures, and inspection criteria. Adherence to AWS D1.1 is essential for applications involving structural components, ensuring the integrity and safety of the welds.
Güvenlik önlemleri
Implementing robust safety measures is essential to protect operators and maintain a safe working environment:
Kişisel Koruyucu Donanım (PPE): Operators must wear appropriate PPE, including welding helmets, gloves, and protective clothing, to shield against electrical hazards, heat, and UV radiation. PPE should meet relevant safety standards, such as ANSI Z87.1 for eye protection and ANSI Z49.1 for welding safety.
Duman Tahliye Sistemleri: Welding fumes contain hazardous substances that can pose health risks to operators. Installing efficient fume extraction systems helps remove harmful fumes and maintain air quality in the workspace. These systems should comply with OSHA regulations and other local safety standards.
Eğitim ve Sertifikasyon: Ensuring that operators are adequately trained and certified is crucial for safe and efficient welding operations. Training programs should cover equipment operation, safety protocols, and emergency procedures. Regular refresher courses and certification renewals help maintain high safety standards and keep operators updated on the latest practices.
Sonuç
Selecting the right spot welding equipment involves careful consideration of technical specifications, material compatibility, safety standards, and cost factors. Advanced technologies, such as adaptive welding and robotic systems, offer significant improvements in efficiency and precision. Ensuring regulatory compliance and implementing robust safety measures are essential to protect operators and maintain high-quality welds. By evaluating these factors and leveraging the latest advancements, manufacturers can optimize their spot welding operations for maximum productivity and reliability.