Dijital yeniliklerdeki son artış ve otomatik kaynak çözümlerine olan talebin artmasıyla, tozaltı kaynak makinesi pazarı her zamankinden daha dinamik. Bu makale, tozaltı kaynak makinesi seçmenin kritik yönlerini ele alarak profesyonel alıcılara bilinçli kararlar almaları için değerli içgörüler sunuyor. Bu faktörleri anlamak, işletmelerin pazarın karmaşıklıklarında gezinmelerine ve kaynak operasyonlarını optimize etmelerine yardımcı olacaktır.
İçindekiler:
– Pazar Genel Bakışı: Tozaltı Kaynak Makinesi
– Ayrıntılı Pazar Analizi: Submerged Arc Kaynak Makinesi Endüstrisi
– Bir Alt Ark Kaynak Makinesi Seçerken Önemli Faktörler
– Alt Ark Kaynak Makinelerinin Maliyet-Fayda Oranının Değerlendirilmesi
– SAW Verimliliğini Artırmada Teknolojinin Rolü
– Alt Ark Kaynak Teknolojisindeki Gelecek Trendler
– Özetleme
Pazar Genel Bakışı: Tozaltı Kaynak Makinesi
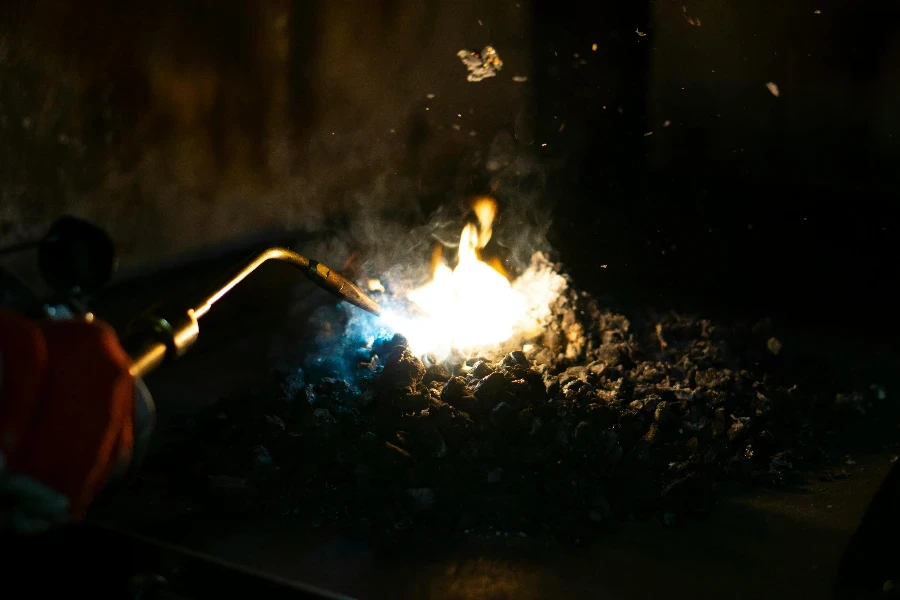
Çeşitli endüstrilerde verimli ve yüksek kaliteli kaynak süreçlerine olan talebin artması nedeniyle, küresel tozaltı kaynak makineleri pazarının önemli ölçüde büyümesi bekleniyor. 2023 yılında, tozaltı kaynak makineleri de dahil olmak üzere küresel tozaltı kaynak ekipmanı pazarı yaklaşık 5.2 milyar ABD doları olarak değerlendirildi. Bu pazarın 7.2 yılına kadar %2030'lik bileşik yıllık büyüme oranıyla (CAGR) 4.2 milyar ABD dolarına ulaşması bekleniyor. Bu büyümenin önemli bir kısmı, 2.2 yılına kadar %2030'lik bir CAGR ile 5.1 milyar ABD dolarına ulaşması beklenen Enerji ve Kamu Hizmetleri segmentine atfediliyor.
Bölgesel olarak, Amerika Birleşik Devletleri ve Çin kilit pazarlardır. 2023'te ABD pazarının 1.4 milyar ABD doları olduğu tahmin edilirken, Çin'in 6.5'a kadar 1.6 milyar ABD dolarına ulaşarak %2030'lik kayda değer bir CAGR ile büyümesi bekleniyor. Diğer önemli pazarlar arasında Japonya, Kanada, Almanya ve Asya-Pasifik bölgesi yer alıyor ve hepsi farklı pazar penetrasyonu ve genişleme dereceleriyle genel büyümeye katkıda bulunuyor.
Batık ark kaynak makinelerine olan talep, otomotiv, gemi yapımı ve inşaat gibi ağır sanayilerdeki kapsamlı uygulamalarıyla desteklenmektedir. Özellikle otomotiv segmentinin önümüzdeki sekiz yıl içinde %4.3'lük bir bileşik yıllık büyüme oranıyla büyümesi öngörülmektedir. Bu büyüme, kaynak teknolojilerindeki gelişmeler ve üretim süreçlerinde otomatik ve verimli kaynak çözümlerine olan artan ihtiyaç tarafından yönlendirilmektedir.
Ayrıntılı Pazar Analizi: Submerged Arc Kaynak Makinesi Endüstrisi

Sualtı ark kaynağı (SAW), derin kaynak penetrasyonu, yüksek biriktirme oranları ve mükemmel kaynak kalitesiyle bilinir. Sualtı ark kaynak makineleri için pazar dinamikleri, performans kıstasları, pazar payı dinamikleri ve son yeniliklerden etkilenir. SAW için temel performans kıstasları arasında yüksek kaynak hızları, minimum sıçrama ve gemi yapımı ve boru hattı inşaatı gibi güçlü ve dayanıklı kaynaklar gerektiren endüstriler için kritik olan üstün kaynak mekanik özellikleri yer alır.
Lincoln Electric, ITW Welding ve Fronius International GmbH gibi kaynak endüstrisindeki önemli oyuncular pazara hakimdir. Bu şirketler, dijital kontroller ve gerçek zamanlı izleme sistemleri entegre etmek de dahil olmak üzere, tozaltı kaynak makinelerinin yeteneklerini geliştirmek için sürekli olarak yenilik yapmaktadır. Dalgalanan çelik fiyatları ve küresel altyapı geliştirme projeleri gibi ekonomik faktörler de pazarı önemli ölçüde şekillendirmektedir.
Tüketici davranışı, üretkenliği artırmak ve işçilik maliyetlerini azaltmak için otomatik ve yarı otomatik kaynak çözümlerine doğru kayıyor. Doğrudan satış ve çevrimiçi platformlara yönelik artan tercihle birlikte, tozaltı kaynak makineleri için dağıtım kanalları gelişiyor ve bu da üreticilerin daha geniş bir müşteri tabanına ulaşmasını sağlıyor. Alandaki yenilikler arasında kaynak kalitesini ve verimliliğini artıran gelişmiş kaynak akıları ve telleri geliştirmek yer alıyor. Tozaltı kaynak makineleri için ürün yaşam döngüsü genellikle birkaç yılı kapsıyor ve optimum performansı sağlamak için düzenli bakım ve yükseltmeler gerekiyor.
Dijitalleşme, IoT ve AI gibi Endüstri 4.0 teknolojilerini benimseyerek tozaltı ark kaynak pazarını dönüştürüyor. Bu teknolojiler, kaynak operasyonlarının genel verimliliğini ve güvenilirliğini artırarak öngörücü bakım, gerçek zamanlı veri analitiği ve uzaktan izleme olanağı sağlıyor. Sürdürülebilir üretim uygulamalarına artan odaklanma gibi sosyal eğilimler de pazarı etkileyerek enerji açısından verimli kaynak çözümlerine olan talebi artırıyor.
Müşterilerin canını sıkan noktalar arasında yüksek ilk yatırım maliyetleri ve gelişmiş kaynak sistemlerini yönetmek ve sürdürmek için yetenekli operatörlere duyulan ihtiyaç yer alır. Bu sorunları ele almak için şirketler kapsamlı eğitim programları ve satış sonrası destek sağlamaya odaklanmaktadır. Marka konumlandırma stratejileri, tozaltı ark kaynak makinelerinin üstün performansını, güvenilirliğini ve maliyet etkinliğini vurgulamayı içerir. Farklılaştırma stratejileri, belirli endüstri gereksinimlerine göre uyarlanmış özelleştirilmiş kaynak çözümleri sunmayı ve katma değerli özellikler sağlamak için teknolojik gelişmelerden yararlanmayı içerir.
Sualtı ark kaynak endüstrisindeki niş pazarlar, kaplama, sert yüzey kaplama ve egzotik malzemelerin kaynaklanması gibi uzmanlaşmış uygulamaları içerir. Bu niş uygulamalar, şirketlere uzmanlaşmış ürünler ve hizmetler geliştirme fırsatları sağlayan benzersiz kaynak parametreleri ve sarf malzemeleri gerektirir.
Özetle, kaynak teknolojilerindeki gelişmeler, artan otomasyon ve çeşitli endüstrilerde verimli ve yüksek kaliteli kaynak çözümlerine yönelik artan taleple yönlendirilen batık ark kaynak makinesi pazarı önemli bir büyümeye hazırlanıyor. Dijital teknolojilerin entegrasyonu ve sürdürülebilir üretim uygulamalarına odaklanma, önümüzdeki yıllarda pazarın büyüme beklentilerini daha da artıracaktır.
Bir Tozaltı Ark Kaynak Makinesi Seçerken Önemli Faktörler
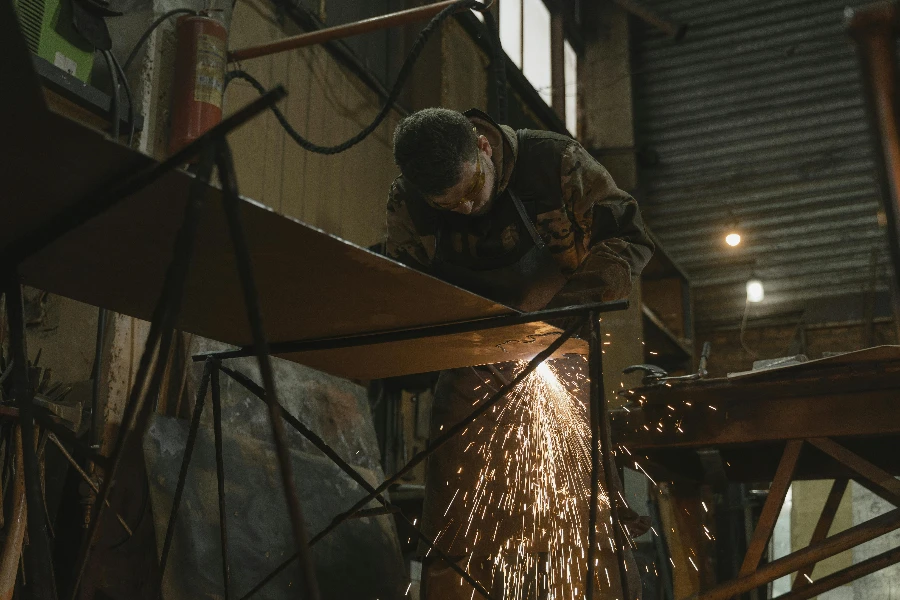
Performans ve İşlevsellik
Submerged Arc Welding (SAW) makineleri yüksek biriktirme oranları ve derin penetrasyonlarıyla bilinir. Bir SAW makinesi seçerken performans ölçütlerini değerlendirin. Yüksek performanslı SAW makineleri genellikle beslemeli bir tel elektrot ve kaynak bölgesini atmosferik kirlenmeden koruyan bir akı örtüsüne sahiptir.
Bir SAW makinesinin işlevselliği, özel kaynak ihtiyaçlarınıza uymalıdır. Yüksek biriktirme oranları için tasarlanmış makineler, gemi inşasında ve ağır inşaatta yaygın olan kalın malzemelerin kaynaklanması için idealdir. SAW süreçlerindeki otomasyon kolaylığı, tutarlı kaynak kalitesinin çok önemli olduğu büyük ölçekli üretim için de uygun hale getirir.
Teknik özellikler
Güç çıkışı, tel besleme hızı ve farklı akı tipleriyle uyumluluk gibi temel teknik özellikleri göz önünde bulundurun. Güç çıkışı, makinenin çeşitli malzeme kalınlıklarını işleme yeteneğini belirlediği için kritik öneme sahiptir. Ağır hizmet uygulamaları için, istenen penetrasyon ve kaynak kalitesi için daha yüksek güç çıkışına sahip bir makine gereklidir.
Tel besleme hızı bir diğer önemli faktördür. Ayarlanabilir tel besleme hızına sahip bir makine daha fazla çok yönlülük sunarak operatörlerin farklı malzemeler ve birleştirme yapılandırmaları için kaynak işlemini ince ayar yapmasına olanak tanır. Çeşitli akı tipleriyle uyumluluk da önemlidir çünkü farklı akı türleri cüruf giderme, kaynak boncuğu görünümü ve mekanik özelliklerde benzersiz faydalar sağlar.
Kalite ve Dayanıklılık Oluşturun
Bir SAW makinesinin yapı kalitesi, uzun ömürlülüğünü ve güvenilirliğini önemli ölçüde etkiler. Paslanmaz çelik ve güçlendirilmiş bileşenler gibi yüksek kaliteli malzemelerle üretilen makineler daha dayanıklıdır ve aşınma ve yıpranmaya karşı dirençlidir. Su soğutmalı torçlar ve ağır hizmet tipi tel besleyiciler gibi özellikler, makinenin dayanıklılığını ve performansını artırır.
Dayanıklılık, makinelerin sürekli çalışma ve zorlu ortamlarla karşı karşıya kaldığı endüstriyel ortamlarda özellikle önemlidir. Sağlam bir SAW makinesine yatırım yapmak, bakım maliyetlerini ve duruş sürelerini azaltarak üretkenliği ve operasyonel verimliliği artırabilir.
Güvenlik Standartları ve Sertifikalar
Bir SAW makinesi seçerken güvenlik standartlarına ve sertifikalarına uyum esastır. ISO 9692, AWS D1.1 ve CE işareti gibi uluslararası standartlara uyan makineleri arayın. Bu sertifikalar, makinenin sıkı güvenlik ve performans kriterlerini karşılamasını, operatörleri korumasını ve tutarlı kaynak kalitesini garanti etmesini sağlar.
Otomatik kapanma mekanizmaları, aşırı yük koruması ve gerçek zamanlı izleme sistemleri gibi gelişmiş güvenlik özelliklerine sahip makineleri göz önünde bulundurun. Bu özellikler operatör güvenliğini artırır ve makineye ve iş parçasına zarar gelmesini önleyerek makinenin kullanım ömrünü uzatır.
İlk Kurulum Karmaşıklığı ve Kullanım Kolaylığı
İlk kurulumun karmaşıklığı ve kullanım kolaylığı, özellikle sınırlı teknik uzmanlığa sahip işletmeler için kritik faktörlerdir. Kullanıcı dostu arayüzlere, sezgisel kontrollere ve net kurulum talimatlarına sahip makineler öğrenme eğrisini azaltabilir ve operasyonel hataları en aza indirebilir.
Bazı SAW makineleri, kurulum sürecini basitleştiren yaygın uygulamalar için önceden yapılandırılmış kaynak programlarıyla birlikte gelir. Dijital ekranlar, uzaktan kumandalar ve otomatik akı işleme sistemleri gibi özellikler kullanım kolaylığını artırarak operatörlerin yüksek kaliteli kaynaklar elde etmeye odaklanmasını sağlar.
Tozaltı Ark Kaynak Makinelerinin Maliyet-Fayda Oranının Değerlendirilmesi
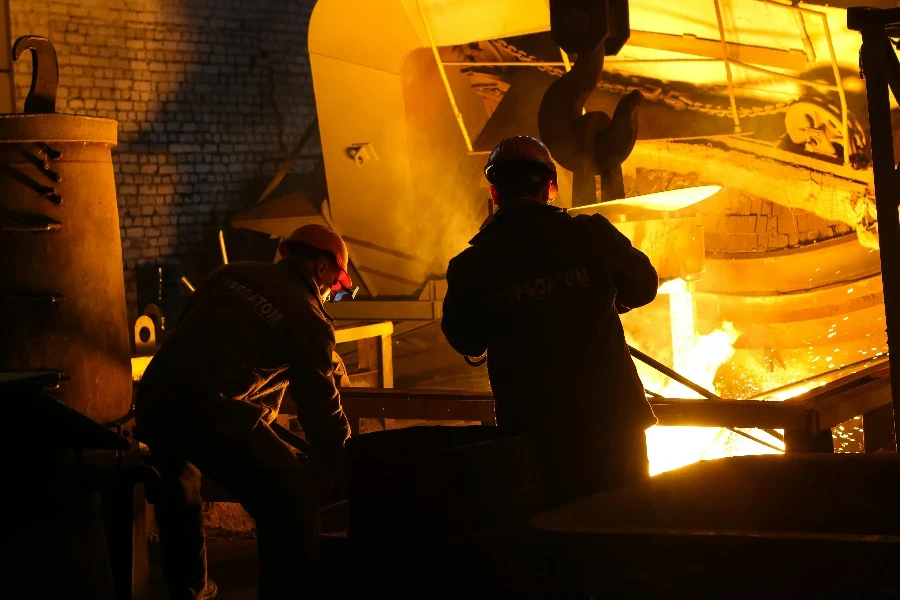
Bir SAW makinesini değerlendirirken maliyet-fayda oranını göz önünde bulundurun. Gelişmiş özelliklere sahip üst düzey makineler daha yüksek bir ön maliyete sahip olabilir ancak genellikle daha iyi performans, dayanıklılık ve uzun vadeli tasarruflar sağlar. Örneğin, yüksek biriktirme oranlarına ve otomasyon yeteneklerine sahip bir makine işçilik maliyetlerini azaltabilir ve üretim verimliliğini artırabilir.
Bütçe dostu makineler, daha küçük operasyonlar veya üst düzey özelliklerin gereksiz olduğu belirli uygulamalar için uygun olabilir. Bakım maliyetleri, enerji tüketimi ve olası duruş süresi gibi faktörleri göz önünde bulundurarak ilk yatırımı beklenen yatırım getirisi (YG) ile dengeleyin.
SAW Verimliliğini Artırmada Teknolojinin Rolü
Teknolojideki ilerlemeler SAW makinelerinin verimliliğini ve yeteneklerini önemli ölçüde iyileştirmiştir. Modern SAW makineleri gerçek zamanlı izleme, uyarlanabilir kontrol sistemleri ve veri kaydı yeteneklerine sahiptir. Bu teknolojiler operatörlerin kaynak parametrelerini izlemesine, anormallikleri tespit etmesine ve kaynak sürecini optimize etmek için gerçek zamanlı ayarlamalar yapmasına olanak tanır.
Otomasyon ve robotik de SAW verimliliğini artırdı. Otomatik SAW sistemleri, karmaşık kaynak görevlerini yüksek hassasiyet ve tutarlılıkla gerçekleştirerek manuel müdahaleyi azaltır ve insan hatasını en aza indirir. Endüstri 4.0 teknolojileriyle entegrasyon, kesintisiz veri alışverişi ve süreç optimizasyonuna olanak tanır, üretkenliği ve kaliteyi daha da iyileştirir.
Alt Ark Kaynak Teknolojisindeki Gelecek Trendler
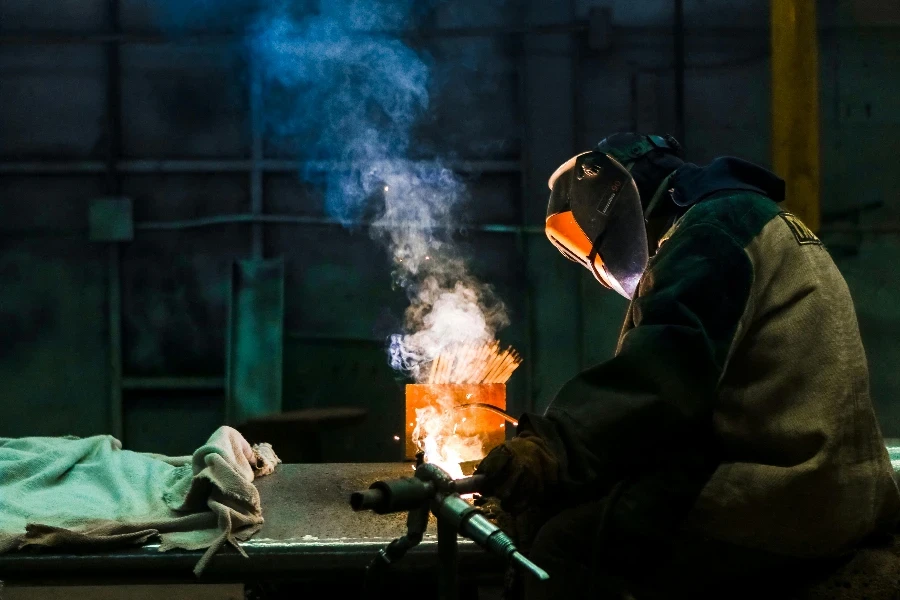
SAW teknolojisinin geleceğini şekillendirmesi beklenen birkaç trend var. Bir trend, kaynak süreçlerinin sanal simülasyonuna ve optimizasyonuna olanak tanıyan dijital ikiz teknolojisinin giderek daha fazla benimsenmesidir. Kaynak ortamının dijital bir kopyasını oluşturarak operatörler, fiziksel denemeler olmadan optimum sonuçlar elde etmek için farklı parametreleri ve yapılandırmaları test edebilir.
Bir diğer yükselen trend ise SAW makinelerinde gelişmiş malzemeler ve kaplamaların kullanılmasıdır. Bu malzemeler makinenin aşınma ve korozyona karşı direncini artırarak ömrünü uzatır ve bakım ihtiyaçlarını azaltır. Çevre dostu akılar ve sarf malzemelerinin geliştirilmesi, üretimde sürdürülebilirlik ve çevresel sorumluluğa verilen artan önemle uyumludur.
Yukarı tamamlayan
Özetle, doğru Submerged Arc Kaynak Makinesini seçmek, performans ölçümlerini, teknik özellikleri, yapı kalitesini, güvenlik standartlarını ve kullanım kolaylığını değerlendirmeyi içerir. Bu faktörleri göz önünde bulundurarak ve teknolojik gelişmeleri takip ederek, işletmeler kaynak operasyonlarını geliştiren ve uzun vadeli başarıyı sağlayan bilinçli kararlar alabilirler.