In 2025, the global market for industrial concentrators continues to grow, driven by advancements in automation and sustainable technologies. This article provides an in-depth analysis of selecting the right concentrator, focusing on aspects like performance, material quality, and regulatory compliance. Professional buyers will find valuable guidance to make informed purchasing decisions, ensuring long-term value and efficiency. Transitioning into the main content, let’s explore the crucial factors to consider.
Table of Contents:
1. Market Overview of Concentrators in Industrial Applications
2. Detailed Analysis of the Industrial Concentrator Market
3. Key Factors When Selecting Industrial Concentrators
4. Integration with Existing Systems
5. Regulatory Compliance
6. Future Trends in Industrial Concentrators
7. Wrapping Up
Market Overview of Concentrators in Industrial Applications
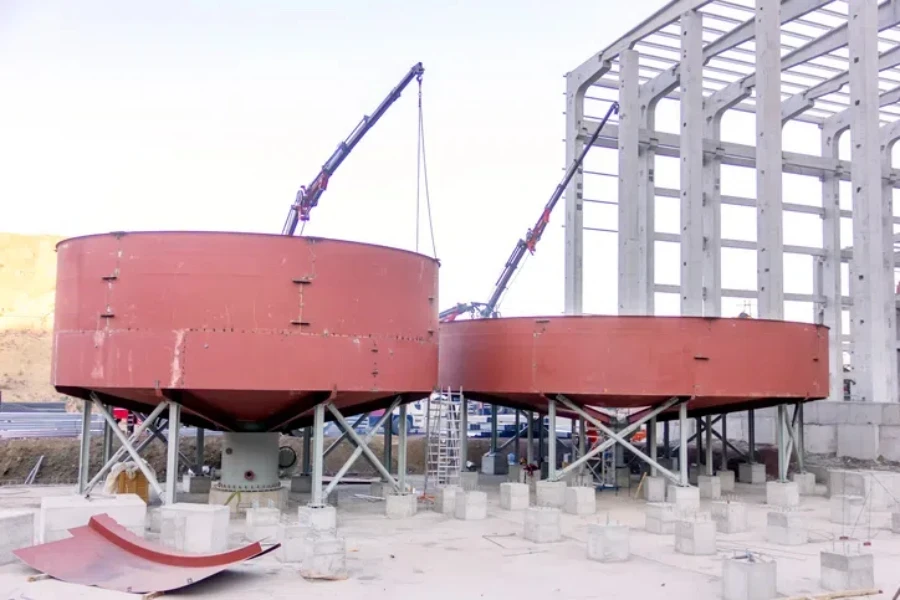
The global market for industrial concentrators is growing steadily, driven by demand in sectors like pharmaceuticals, chemicals, and food and beverage. Recent reports value the market at approximately USD 8.78 billion in 2023, with projections suggesting it will reach USD 12.67 billion by 2030, growing at a compound annual growth rate (CAGR) of 5.37%. This growth is primarily due to the increasing need for efficient separation and purification processes.
Regionally, the Asia-Pacific region leads the market, with China and India at the forefront. Rapid industrialization and increasing investments in healthcare and R&D in these countries have significantly boosted demand. North America and Europe also hold substantial market shares, driven by strict environmental regulations and a strong presence of key industries such as pharmaceuticals and biotechnology.
The market is segmented by type into filtering concentrators and sedimentation concentrators. Filtering concentrators are preferred for applications requiring fine particle filtration, while sedimentation concentrators are used for separating solids from liquids. The market is also categorized by end-use industries, with significant demand from power generation, manufacturing, and wastewater treatment sectors.
Detailed Analysis of the Industrial Concentrator Market
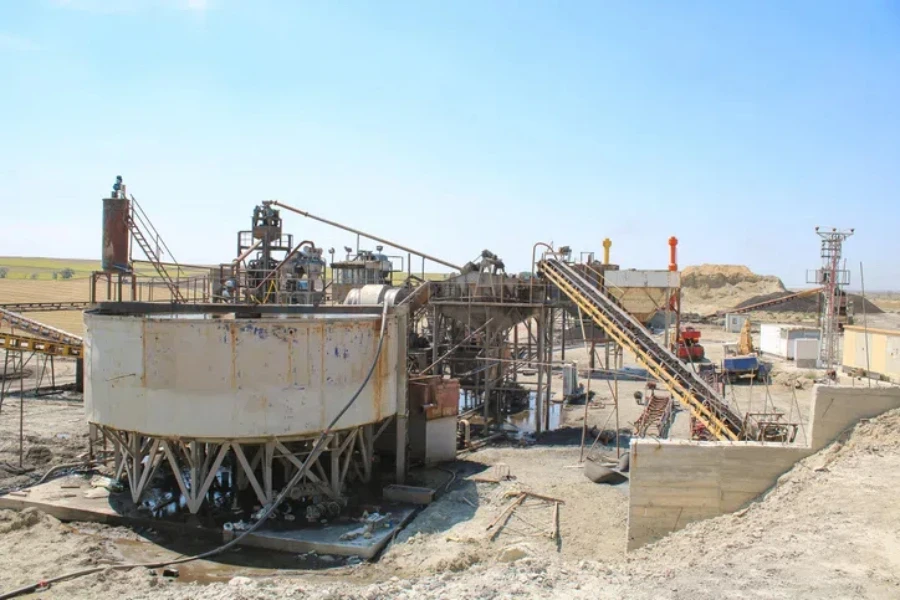
Key Performance Benchmarks and Market Share Dynamics
Industrial concentrators are evaluated on efficiency, capacity, and operational costs. Filtering concentrators handle high volumes of fine particles with minimal energy consumption, whereas sedimentation concentrators are robust in separating solids from liquids. The market is shifting towards more automated and energy-efficient systems, driven by technological advancements.
Leading players like Alfa Laval AB, Andritz AG, and GEA Group AG are enhancing their product portfolios through strategic investments and innovations. For example, GEA Group’s EUR 50 million investment in its German production sites highlights its commitment to sustainable and advanced manufacturing practices. These investments are expected to strengthen their market positions and drive growth.
Economic Influences and Consumer Behavior Shifts
Economic factors such as industrial growth, environmental regulations, and technological advancements heavily influence the market. There is a growing emphasis on wastewater management and resource recovery, increasing the demand for advanced concentrator systems. The expansion of industries like pharmaceuticals and biotechnology, where high-purity separation is crucial, also fuels market growth.
Consumer behavior is shifting towards more sustainable and efficient technologies, evident in the preference for high-efficiency and low-energy concentrators. The need for skilled personnel to operate these advanced systems is driving demand for training and support services, creating new opportunities for market players.
Recent Innovations and Digitalization
Recent innovations include more energy-efficient and automated systems. For example, ANDRITZ AG has introduced decanter centrifuges for challenging oil recovery applications, with advanced sealing solutions compliant with ATEX Zone 1 and Zone 2 standards. These innovations enhance efficiency and ensure compliance with stringent safety regulations.
Digitalization is transforming the market with smart sensors and real-time monitoring capabilities, enabling predictive maintenance and operational optimization. This shift towards digital solutions is expected to improve productivity and cost-efficiency, further driving market growth.
Key Factors When Selecting Industrial Concentrators
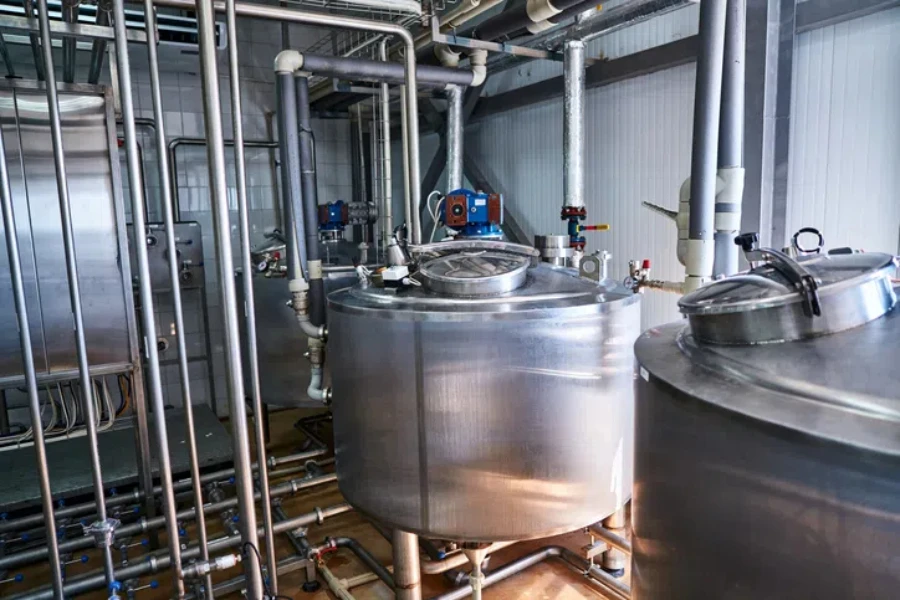
Performance and Efficiency
When selecting an industrial concentrator, performance and efficiency are crucial. The primary function of a concentrator is to separate and concentrate specific components from a mixture, requiring precision and efficiency to ensure maximum yield with minimal waste.
Performance is measured by throughput capacity and separation efficiency. Throughput capacity refers to the volume of feed material the concentrator can process within a given time frame, which is vital for large-scale operations. For instance, in mining, concentrators must handle several tons of ore per hour to be economically viable.
Separation efficiency indicates how effectively the concentrator separates the desired component from the mixture, usually expressed as a percentage. Advanced concentrators use technologies like centrifugal force or membrane filtration to achieve high separation efficiencies, isolating even minute particles to ensure the final product’s purity.
Material and Build Quality
The material and build quality of a concentrator are critical for its durability and longevity. Industrial concentrators often face harsh conditions, including high pressures, temperatures, and corrosive substances. Therefore, robust and wear-resistant materials are essential.
Common materials include stainless steel, titanium, and specialized alloys. Stainless steel is preferred for its corrosion resistance and strength, while titanium, though more expensive, offers superior resistance to corrosion and is used in highly corrosive environments, such as chemical processing.
Build quality also involves manufacturing precision. High-quality concentrators are designed with tight tolerances to ensure seamless component integration, reducing the likelihood of leaks and mechanical failures.
Safety Standards and Certifications
Compliance with safety standards and certifications is essential when selecting an industrial concentrator. These standards ensure safe and efficient operation, protecting both operators and the environment.
Industrial concentrators must adhere to various safety standards. For example, ISO 9001 certification indicates stringent quality management practices, and the CE marking signifies compliance with European safety, health, and environmental protection requirements.
Specific safety features, such as pressure relief valves, emergency shutdown mechanisms, and automated monitoring systems, enhance both safety and reliability.
Technological Features and Upgradability
Advanced technological features can significantly enhance an industrial concentrator’s functionality and efficiency. Modern concentrators often include digital control systems, real-time monitoring capabilities, and automated adjustment mechanisms.
Digital control systems allow precise control over operating parameters like pressure, temperature, and flow rate, ensuring optimal performance and reducing operational errors. Real-time monitoring enables continuous performance tracking and immediate corrective actions if deviations occur.
Upgradability is also crucial. As technology evolves, having the flexibility to upgrade with the latest advancements, such as software updates or new sensors, ensures the equipment remains efficient and provides long-term value.
Cost and Return on Investment
The cost of an industrial concentrator should be evaluated in terms of return on investment (ROI). While high-quality concentrators may have a substantial initial cost, their superior performance, durability, and efficiency can lead to significant long-term savings.
Consider both the initial purchase price and ongoing operational costs, such as energy consumption and maintenance. High-efficiency concentrators with low energy consumption can save on utility bills, while durable concentrators with minimal maintenance reduce overall ownership costs.
Calculate ROI by comparing the total cost with the financial benefits, such as increased productivity, higher yield, and reduced waste. A higher upfront cost may offer a better ROI if the concentrator’s performance and operational costs are superior.
Integration with Existing Systems
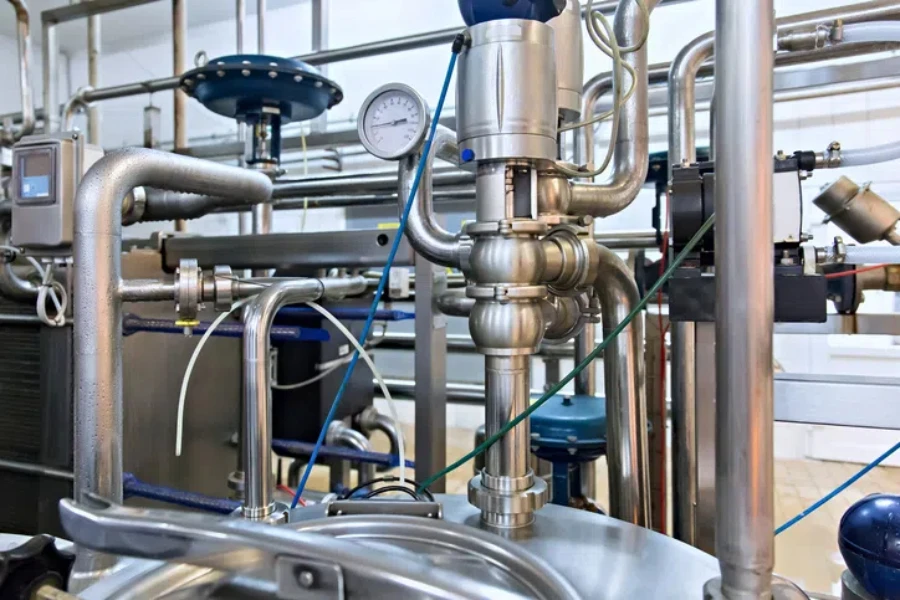
Compatibility with Current Infrastructure
Ensuring compatibility with existing infrastructure is critical when selecting an industrial concentrator. The concentrator must integrate seamlessly with current systems to avoid operational disruptions, including compatibility with piping, electrical systems, and control software.
For instance, in a chemical processing plant, the concentrator must fit into the existing piping network without extensive modifications. The electrical systems should support its power requirements, and the control software must communicate with the concentrator’s digital control system, saving time and resources during installation.
Scalability
Scalability is vital for businesses planning future expansions. A scalable concentrator can handle increased workloads without compromising performance, particularly important in industries like mining or pharmaceuticals, where production demands can vary.
Scalable concentrators often feature modular designs, allowing additional units to be added as needed. This modularity enables incremental scaling of operations, reducing the need for substantial upfront investments and adapting to changing production requirements.
Training and Support
The availability of training and support from the manufacturer is essential. Proper training ensures operators can use the concentrator efficiently and safely, maximizing performance and lifespan. Manufacturers often provide comprehensive training programs, including on-site training, online courses, and detailed user manuals.
Support services ensure issues with the concentrator are resolved quickly and effectively, including technical support, maintenance services, and access to spare parts. A robust support infrastructure can significantly reduce downtime and maintain optimal performance.
Regulatory Compliance
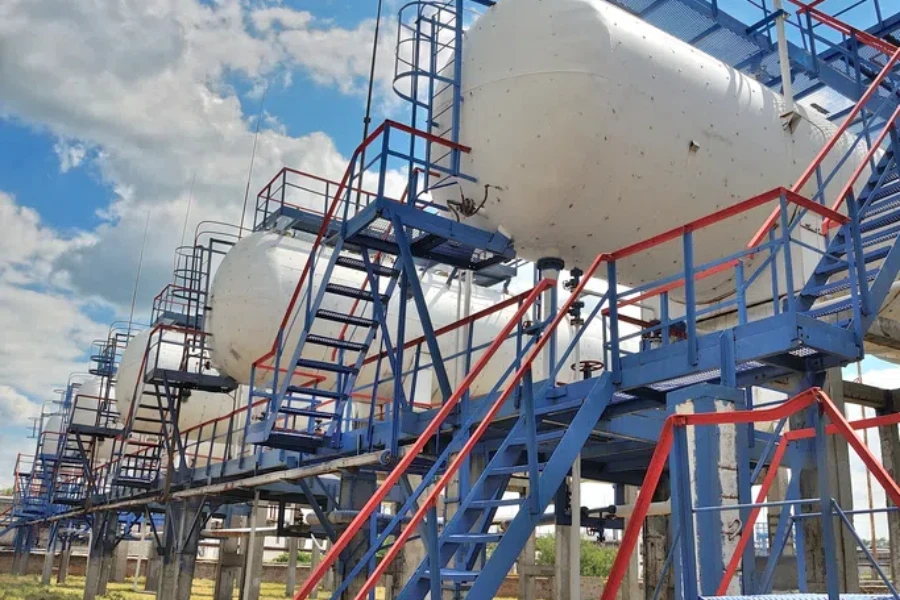
Environmental Regulations
Industrial concentrators must comply with environmental regulations to minimize their environmental impact. These regulations dictate permissible emission levels, waste disposal methods, and energy consumption standards. Non-compliance can result in hefty fines and reputational damage.
For example, in wastewater treatment, concentrators must meet strict waste disposal regulations. Advanced concentrators with efficient separation technologies reduce waste volume, easing regulatory compliance. Energy-efficient concentrators help meet energy consumption standards, reducing carbon footprints and operational costs.
Industry-Specific Standards
Different industries have specific standards that concentrators must meet. In the pharmaceutical industry, concentrators must comply with Good Manufacturing Practices (GMP) to ensure product safety and effectiveness. In the food processing industry, concentrators must meet food safety standards to prevent contamination.
Compliance with industry-specific standards ensures product quality and safety. Manufacturers provide documentation and certifications to demonstrate compliance, which should be reviewed and verified before purchasing.
International Standards
For businesses operating globally, compliance with international standards is crucial. These standards ensure safe and effective use in different countries, facilitating international trade and expansion.
International standards, set by organizations like the International Organization for Standardization (ISO) and the International Electrotechnical Commission (IEC), cover various aspects of concentrator design and performance. Compliance ensures global quality and safety benchmarks, enhancing marketability.
Future Trends in Industrial Concentrators
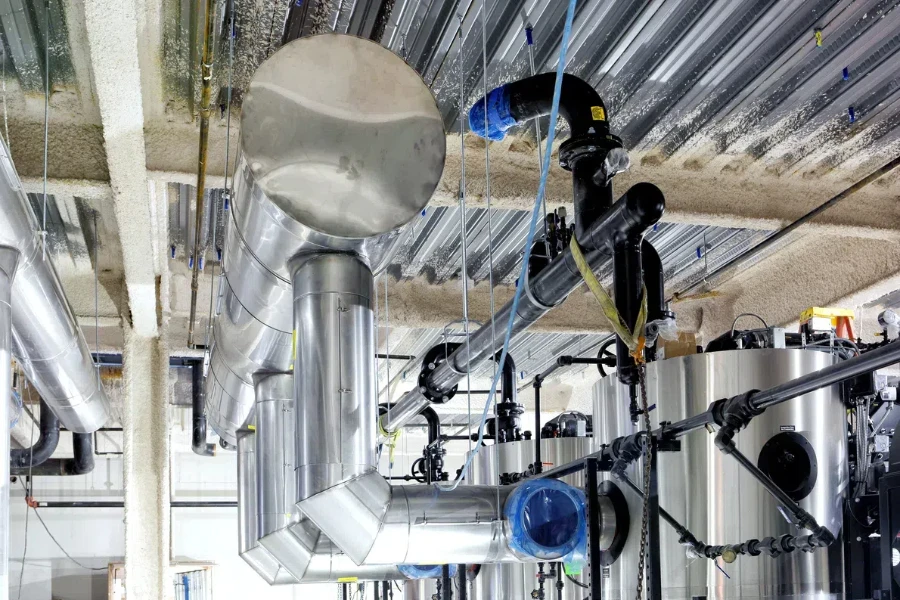
Automation and AI Integration
Automation and artificial intelligence (AI) are revolutionizing the industrial concentrator market. Automated concentrators operate with minimal human intervention, reducing labor costs and increasing efficiency. AI algorithms optimize performance by analyzing real-time data and adjusting operating parameters.
For instance, AI can predict maintenance needs, preventing unexpected breakdowns and reducing downtime. It can also optimize the separation process by adjusting settings based on feed material properties, ensuring consistent performance and maximizing efficiency.
Sustainable Technologies
Sustainability is a key focus in the industrial sector. Manufacturers are developing concentrators with sustainable technologies to reduce environmental impact, including energy-efficient designs, renewable energy integration, and waste minimization technologies.
Energy-efficient concentrators consume less power, reducing costs and emissions. Integrating renewable energy sources, like solar or wind power, further reduces environmental footprints. Advanced filtration systems reduce waste volume, easing regulatory compliance.
Advanced Materials
Advanced materials enhance the performance and durability of industrial concentrators. These materials offer superior resistance to corrosion, wear, and extreme temperatures, extending lifespan and reducing maintenance needs.
For example, advanced ceramics and composite materials are used to improve durability and performance, withstanding harsh conditions and ensuring consistent performance.
Wrapping Up
Selecting the right industrial concentrator involves considering factors like performance, material quality, safety standards, technological features, cost, and regulatory compliance. By evaluating these factors, businesses can choose a concentrator that meets their needs and provides long-term value. As technology evolves, automation, AI, sustainable technologies, and advanced materials will further enhance industrial concentrators’ performance and efficiency, making them indispensable in various industries.