In 2025, the crystallization industry has seen innovations that boost efficiency and environmental sustainability. This article provides an in-depth analysis of selecting the right crystallizer, covering types, technical specifications, performance metrics, and safety standards. It is a valuable resource for professional buyers aiming to make informed purchasing decisions.
Table of Contents:
– Market Overview of Crystallizers
– Key Factors When Selecting a Crystallizer
– Applications of Crystallizers
– Technological Advancements in Crystallizers
– Diverse Crystallizer Models and Sizes
– Final Thoughts
Market Overview of Crystallizers
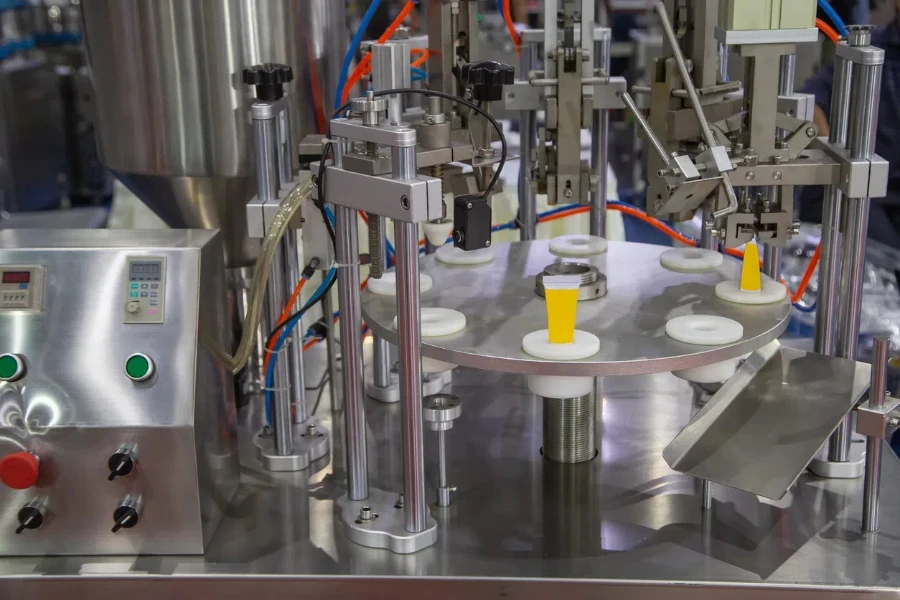
The global industrial crystallizers market was worth approximately $3.58 billion in 2023 and is projected to reach $6.11 billion by 2032, representing a compound annual growth rate (CAGR) of 6.40% from 2024 to 2032. Crystallizers are essential in industries such as chemicals, pharmaceuticals, and food and beverage, where they aid in the purification and production of solid materials through controlled crystallization. Key market segments include evaporative, cooling, and vacuum crystallizers, each suited to specific applications.
North America, Europe, and Asia-Pacific lead this market due to their strong industrial infrastructure and investments in technological advancements. The demand for purified chemicals and pharmaceuticals, along with innovations in crystallization technologies that boost efficiency and minimize environmental impact, drive market growth. Additionally, the need for wastewater treatment, particularly in regions with strict environmental regulations, supports the market.
Detailed Market Analysis
The industrial crystallizers market is dynamic, influenced by various factors. Purity and scale of crystallization processes are primary benchmarks. Common crystallizer types include forced circulation, draft tube baffle (DTB), and vacuum crystallizers, each serving specific industry needs. DTB crystallizers hold the largest market share due to their versatility and efficiency, making them popular in the chemicals and pharmaceuticals sectors.
Economic factors significantly impact market dynamics. High manufacturing and operational costs can hinder product penetration. However, the adoption of efficient and sustainable crystallization methods drives innovation. Companies are integrating automation and control systems to enhance performance and comply with environmental regulations. Notably, continuous crystallization processes offer higher throughput and consistent product quality, making them preferred for large-scale production.
Consumer behavior is shifting towards environmental sustainability and operational efficiency. This trend is evident in the adoption of Zero Liquid Discharge (ZLD) systems in industries like textiles and pharmaceuticals, where crystallizers help reclaim and recycle water and chemicals. The food and beverage industry also relies on crystallizers for processes such as sugar refining and salt production. Companies like Raízen in Brazil and Fonterra in New Zealand exemplify the use of crystallizers for achieving high purity and quality.
Regional Insights and Competitive Landscape
North America dominates the industrial crystallizers market, with the United States and Canada leading due to their strong industrial base and technological capabilities. Strict regulatory standards and significant R&D investments drive the use of advanced crystallization technologies. The Asia-Pacific region is the fastest-growing market, fueled by rapid industrialization in China, India, and Southeast Asia. Government support for manufacturing and increasing urbanization further boost the demand for efficient crystallization technologies.
The competitive landscape features key players such as GEA Group, Sulzer Ltd., and Sumitomo Heavy Industries, who hold significant market shares due to their R&D efforts and strategic partnerships. Competitive factors include pricing, product quality, and technological innovation. As the market grows, competitive intensity will increase, with companies focusing on novel innovations and strategic growth tactics to gain an edge.
Key Factors When Selecting a Crystallizer
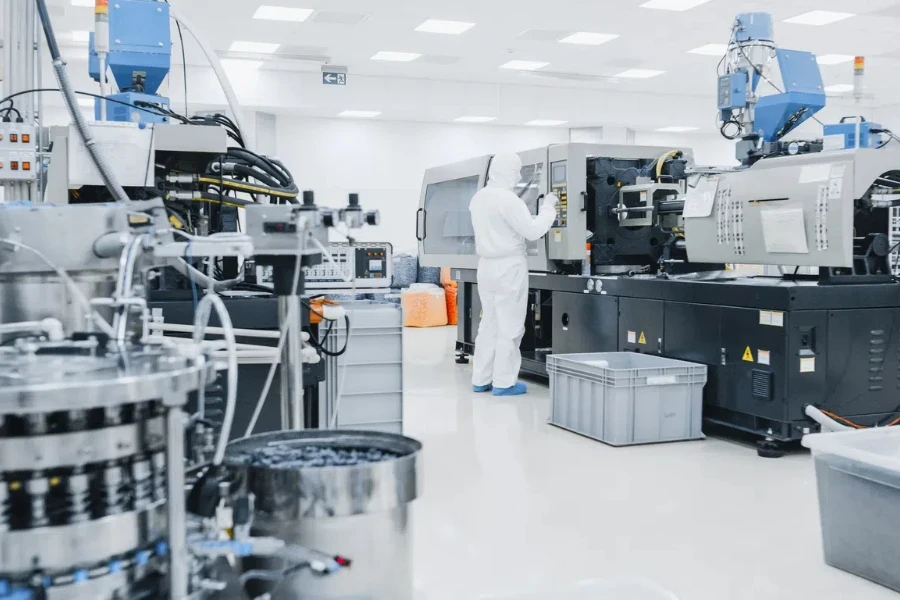
Types of Crystallizers
Selecting a crystallizer begins with understanding the available types and their specific applications. There are three primary types: concentration, cooling, and reaction or equilibrium displacement. Concentration crystallizers process wastewater, producing solid crystals and clean water. Cooling crystallizers, often operating under vacuum or using a heat exchanger, are for substances needing cooling to crystallize. Reaction or equilibrium displacement crystallizers are used when crystallization results from a chemical reaction or a shift in equilibrium.
Choose the type of crystallizer based on the material being processed, the required purity of the end product, and the operational conditions. For instance, a vertical continuous cooling crystallizer (VCCC) is ideal for highly viscous, slowly crystallizing substances, while a salt crystallizer is tailored for saline wastewater.
Technical Specifications
The technical specifications of a crystallizer must match the application requirements. Key specifications include capacity, material compatibility, and operational efficiency. For example, a resin crystallizer is designed for crystallizing flake or amorphous resin pellets, needing specific material compatibility and operational parameters.
The design must also accommodate the feed material’s physical and chemical properties. Factors like viscosity, crystallization rate, and thermal sensitivity influence equipment choice. Efficiency in energy consumption, throughput, and recovery rate is crucial in selecting a crystallizer.
Performance and Functionality
A crystallizer’s performance and functionality are determined by its ability to consistently produce high-purity crystals while minimizing energy consumption and operational costs. Key performance metrics include crystallization rate, product yield, and purity levels.
For example, a brine concentrator, often used with crystallizers, can recover 95% to 99% of wastewater, making it highly efficient for industries aiming for zero liquid discharge (ZLD). The ability to integrate with other technologies, such as evaporators, enhances functionality and efficiency.
Material and Build Quality
The material and build quality significantly impact a crystallizer’s durability, maintenance needs, and lifespan. Crystallizers are typically made from materials that withstand the corrosive nature of processed substances. Common materials include stainless steel and specialized alloys resistant to corrosion and wear.
High-quality construction ensures continuous operation under harsh conditions, reducing the need for frequent repairs and replacements. This reliability is crucial for industries with high production demands and stringent quality standards.
Safety Standards and Certifications
Compliance with safety standards and certifications is essential when selecting a crystallizer. Ensuring the equipment meets industry-specific safety regulations protects workers and maintains operational integrity. Certifications like ISO and CE mark indicate rigorous testing and adherence to international safety and performance standards.
Safety features such as automatic shutdown mechanisms, pressure relief valves, and robust control systems prevent accidents and ensure safe operation. Adherence to environmental regulations ensures the crystallizer operates within permissible emission limits, contributing to sustainable industrial practices.
Applications of Crystallizers
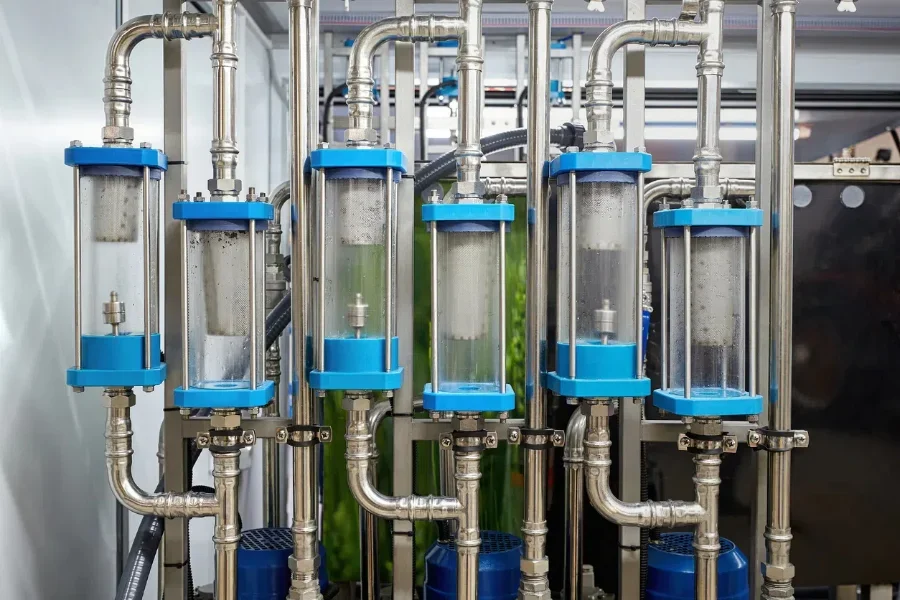
Crystallizers are used across various industries, including manufacturing, chemical processing, mining, petrochemical refining, and electronics. In manufacturing, they recover valuable salts from wastewater, optimizing resource utilization and meeting ZLD requirements.
In chemical processing, crystallizers produce high-purity chemicals and intermediates essential for pharmaceuticals and specialty chemicals. The mining industry uses crystallizers to extract and purify minerals from ore slurry, enhancing mineral recovery efficiency.
Petrochemical refineries use crystallizers to separate and purify hydrocarbons, improving fuel and petrochemical product quality. In electronics, crystallizers are crucial for fabricating high-purity components required for advanced electronic devices.
Technological Advancements in Crystallizers
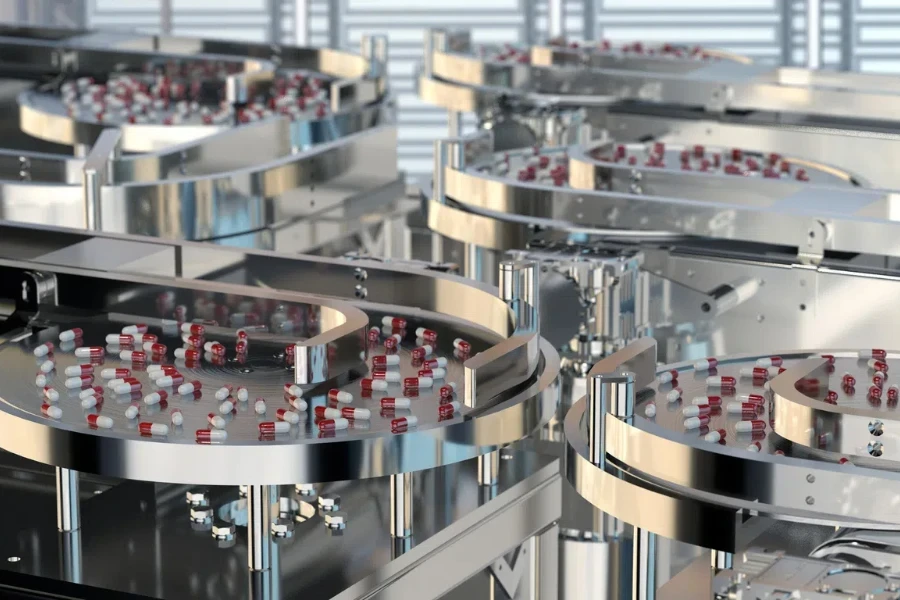
Advancements in crystallizer technology are enhancing efficiency, automation, and scalability. Modern crystallizers feature advanced control systems for precise monitoring and adjustment of operational parameters, ensuring optimal performance.
Innovations like continuous crystallization processes produce uniform crystals with consistent quality, reducing batch variability. Integration of digital sensors and IoT technologies enables real-time data collection and analysis, facilitating predictive maintenance and reducing downtime.
Energy-efficient designs, such as heat recovery systems, are becoming more common, reducing overall energy consumption. These advancements make crystallizers more adaptable to evolving industrial needs, promoting sustainable and cost-effective operations.
Diverse Crystallizer Models and Sizes
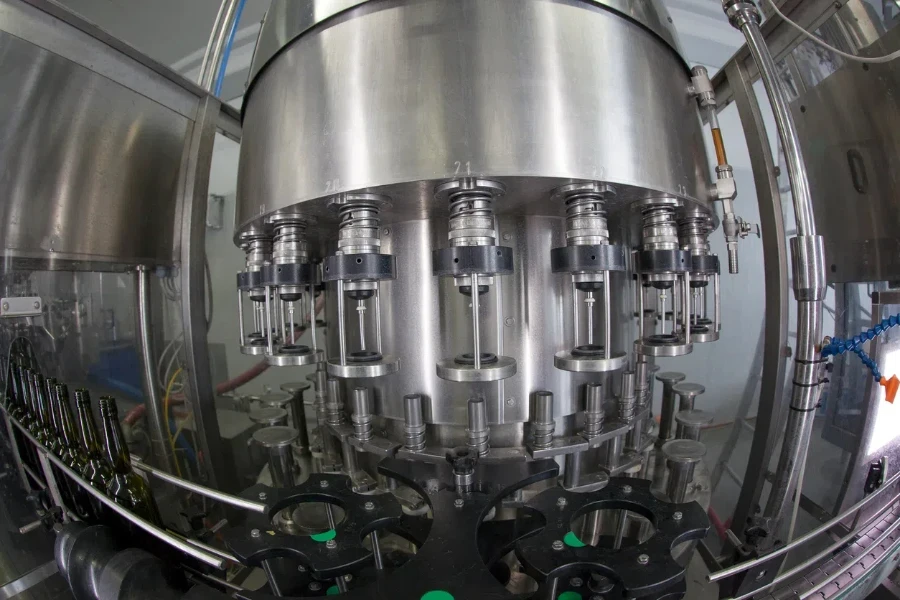
Crystallizers come in various sizes and models to meet different industrial needs. From small-scale laboratory crystallizers for research and development to large-scale industrial crystallizers for mass production, there is a suitable option for every application.
Laboratory crystallizers allow researchers to study crystallization processes and optimize parameters on a small scale. Pilot-scale crystallizers bridge the gap between laboratory experiments and full-scale production, enabling near-industrial condition testing.
Industrial crystallizers are designed for high-capacity operations, efficiently processing large volumes of material. These models often feature modular designs for easy scalability and integration with existing production lines, providing flexibility for growing industrial needs.
Final Thoughts
Selecting the right crystallizer involves evaluating factors such as the type of crystallizer, technical specifications, performance, material quality, and safety standards. Understanding the specific application requirements and keeping up with technological advancements can significantly enhance the efficiency of crystallization processes.
By considering these critical aspects and leveraging the latest innovations, industries can optimize their crystallization operations, achieve higher product quality, and contribute to sustainable industrial practices.