In 2025, the global punching machine market is thriving, projected to reach USD 392.65 million by 2030. This article provides an in-depth analysis of the essential factors for selecting the right punch in machine, offering valuable insights and assistance for professional buyers to make informed decisions.
Table of Contents:
– Market Overview of Punching Machines in 2025
– Detailed Analysis and Key Insights
– Key Factors When Selecting a Punching Machine
– Performance and Functionality Considerations
– Durability and Build Quality
– Energy Efficiency and Environmental Impact
– Packaging and Regulatory Compliance
– Wrapping Up: Key Considerations for Punching Machines
Market Overview of Punching Machines in 2025
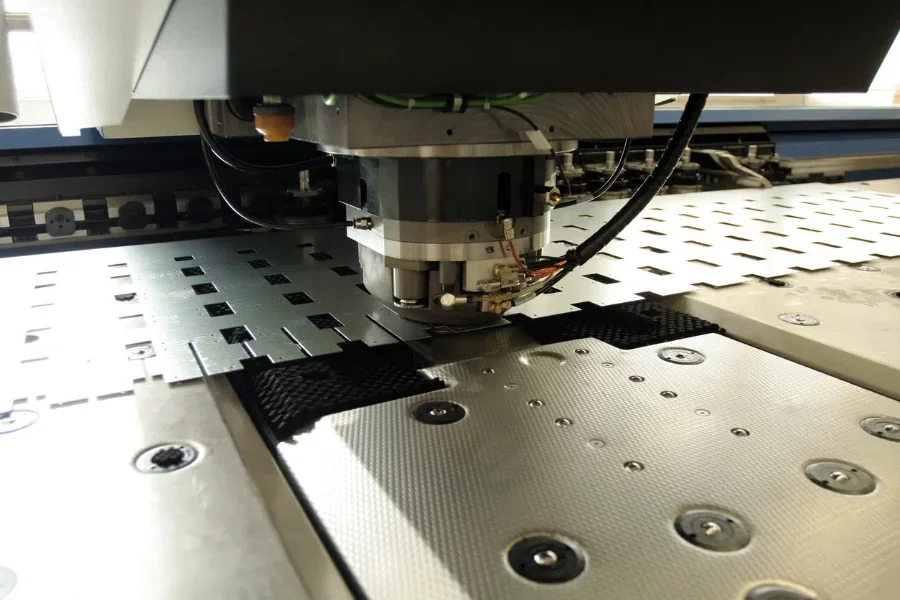
The global punching machine market is growing significantly. The market size reached about USD 280.16 million in 2024 and is growing at a compound annual growth rate (CAGR) of 5.71%, reaching USD 392.65 million by 2030. This growth highlights the increasing demand for punching machines in industries like automotive, construction, and metalworking. Technological advancements and the need for high-precision metal fabrication processes are driving this expansion.
The Americas and Asia-Pacific regions are leading the market due to strong industrial activities and innovations. The U.S. market was worth approximately USD 527.8 million in 2023, while China is projected to grow at a CAGR of 4.5%, reaching USD 443.1 million by 2030. The growth in these regions is driven by expanding manufacturing industries and the adoption of advanced punching technologies.
The market includes various types of punching machines, such as CNC, electric, hydraulic, mechanical, and pneumatic. CNC punching machines are popular for their precision and automation in high-volume production. The market also features automatic and semi-automatic machines, valued for their efficiency and lower labor costs.
Detailed Analysis and Key Insights
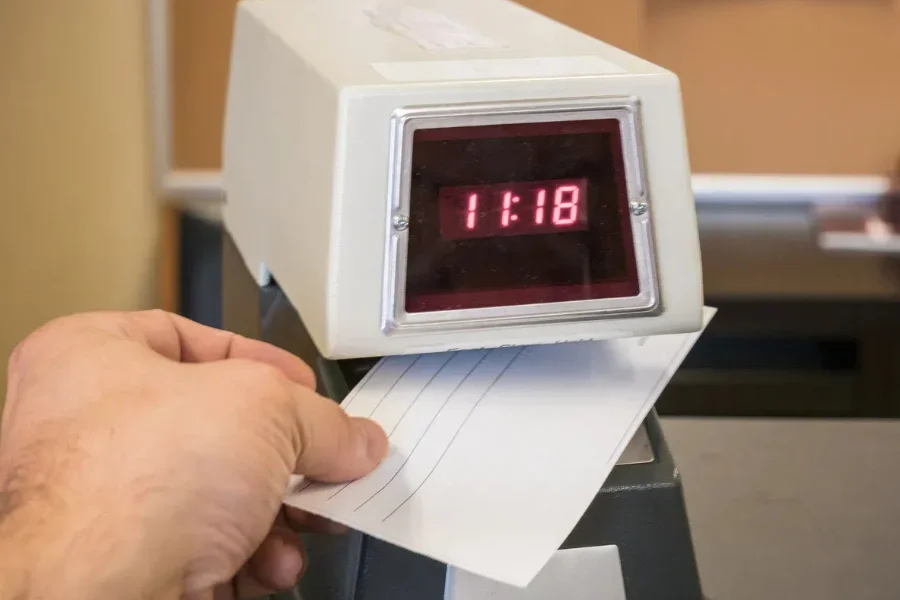
The punching machine market focuses on precision, speed, and operational efficiency. CNC punching machines use advanced control systems for high accuracy, making them ideal for complex tasks. Hydraulic punching machines, projected to reach USD 1.1 billion by 2030, are known for handling thick and tough materials effectively.
Key players like Amada Co. Ltd., Boschert GmbH, and Trumpf GmbH + Co. KG dominate the market. These companies innovate continuously, integrating digital technologies such as IoT and AI for real-time monitoring and predictive maintenance. This digitalization trend aims to streamline operations, reduce downtime, and boost productivity.
Economic factors, including the resurgence of manufacturing industries and infrastructural development, are increasing the demand for punching machines. Shifts in consumer behavior towards customized and high-quality metal products encourage manufacturers to invest in advanced punching technologies. The rise of prefabricated buildings and stringent automotive industry standards further increase the need for precise punching solutions.
Distribution channels favor direct sales and online marketplaces, allowing manufacturers broader market reach and efficient supply chains. Innovations like servo-electric punching machines offer energy efficiency and lower operational costs, aligning with the demand for sustainable manufacturing practices.
High initial investment costs and the need for skilled operators are common challenges in the punching machine market. Companies are addressing these issues by developing cost-effective machines and offering extensive training programs. This approach enhances the skilled labor pool and promotes the adoption of advanced technologies.
Market leaders are focusing on product development and innovation for brand positioning and differentiation. Investments in R&D aim to introduce new technologies and improve machine capabilities, such as handling varied material thicknesses and complex patterns. Strategic collaborations and acquisitions further strengthen their competitive position.
Niche markets like aerospace and electronics are growing due to their need for high-precision and customized components. These sectors require advanced punching solutions that meet strict quality and safety standards, driving further market expansion.
The punching machine market is set for robust growth, driven by technological advancements, economic influences, and evolving consumer demands. Companies that leverage innovation, digitalization, and strategic positioning are expected to gain a competitive edge in this dynamic market.
Key Factors When Selecting a Punching Machine
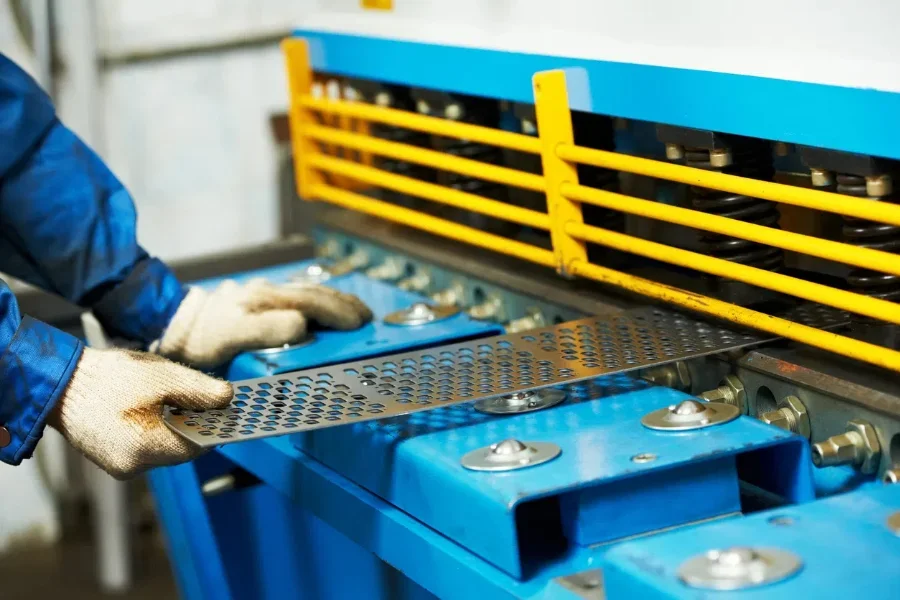
Choosing the right punching machine for your business involves various considerations to ensure optimal performance and cost-effectiveness. Here, we explore the critical factors to guide your decision-making process.
Drive Type and Automation
The drive type of a punch press significantly influences its capabilities. Air-driven punch presses, powered by pneumatic cylinders, are ideal for light-duty tasks. They offer precision and ease of use but are limited in the force they can generate. Hydraulic punch presses use fluid-filled cylinders to exert immense force, making them suitable for heavy-duty operations involving thick or hard materials. Mechanical punch presses utilize rotary motors and mechanical linkages for high-speed operations, offering a balance between power and speed. Servo-controlled punch presses, driven directly by servo motors, provide unparalleled precision and programmability, making them perfect for complex and repetitive tasks.
Automation levels vary from manual to fully automatic systems. Manual punch presses require significant operator intervention and are best suited for low-volume, custom jobs. Semi-automatic machines reduce manual labor and increase efficiency, while fully automatic systems, often integrated with CNC or PLC controls, maximize throughput and consistency by automating part loading, punching, and unloading processes.
Operating Force and Rated Capacity
Understanding the operating force and rated capacity of a punch press is crucial. The operating force is the maximum load the machine can exert to cut or form parts, typically measured in tons. This specification ensures the machine can handle the materials and thicknesses you intend to work with. Rated capacity, also measured in tons, indicates the pressure the slide or ram exerts at the bottom of its stroke. For instance, a mechanical punch press’s operating force is linked to the bending capacity of its main shaft, dictating the machine’s capability to handle various material thicknesses without compromising performance.
Production Rate and Sheet Capacity
The production rate of a punch press, measured in strokes or hits per minute, determines its efficiency and suitability for high-volume operations. This rate can vary significantly based on the complexity of the parts being produced and the number of operations required. Sheet capacity, encompassing maximum thickness, working length, and working depth, defines the machine’s ability to accommodate different material sizes. For example, a punch press with a working length of 2000mm and a thickness capacity of 10mm is suitable for large, thick metal sheets, whereas smaller capacity machines are ideal for more delicate tasks.
Special Features and Accessories
Modern punch presses come equipped with various special features and accessories to enhance functionality and versatility. Integral shearing capabilities allow for simultaneous punching and cutting, increasing efficiency. Optional material feeders automate the feeding process, reducing manual intervention and ensuring consistent material flow. Laser cutting systems integrated into punch presses offer precision and flexibility, especially for complex shapes and patterns. Multi-station punch presses with rotary tools and turrets enable quick tool changes and accommodate multiple operations without manual reconfiguration. Advanced monitoring systems provide real-time feedback on machine performance and part quality, facilitating preventive maintenance and reducing downtime.
Safety Standards and Certifications
Compliance with safety standards and certifications is non-negotiable in the machinery industry. Punch presses should adhere to relevant safety regulations such as OSHA guidelines in the United States or CE marking in Europe. These certifications ensure the machines are designed and manufactured to minimize risks to operators and maintain safe working conditions. Features like emergency stop buttons, safety guards, and light curtains are essential to prevent accidents and protect workers. Additionally, machines with certifications like ISO 9001 for quality management systems or ISO 14001 for environmental management systems demonstrate a commitment to high standards and sustainable practices.
Performance and Functionality Considerations
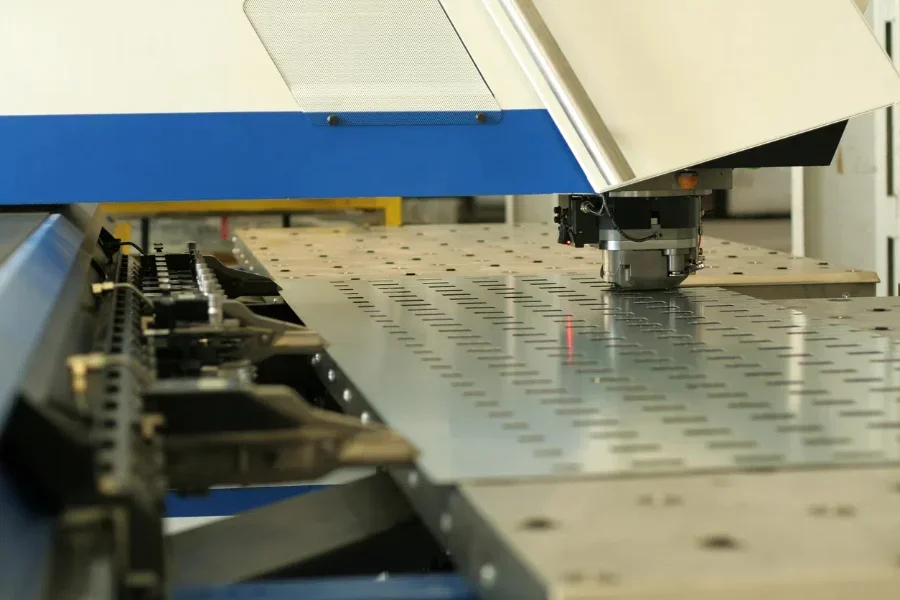
When evaluating punching machines, performance and functionality are paramount. The machine’s ability to consistently produce high-quality parts at the desired speed and accuracy directly impacts productivity and profitability.
Speed and Precision
The speed of a punch press is a critical factor for high-volume production environments. Machines with higher strokes per minute can produce more parts in less time, increasing throughput. However, speed should not compromise precision. Advanced servo-controlled punch presses offer high-speed operations without sacrificing accuracy, making them ideal for complex parts requiring tight tolerances. CNC-controlled machines provide programmable precision, ensuring consistent part quality across large production runs.
Material Compatibility
Punch presses must be compatible with the materials they will process. Different materials, such as aluminum, steel, or composite materials, have varying hardness and thicknesses, requiring specific machine capabilities. For instance, hydraulic punch presses are well-suited for thick, hard materials due to their high force output, while mechanical presses are better for thinner, softer materials where speed is more critical. Ensuring the machine’s specifications match the material requirements is essential for optimal performance and longevity.
Versatility and Adaptability
Versatility in a punch press allows for a broader range of applications and increased flexibility in production. Machines with multi-tool turrets or quick-change tool systems enable rapid transitions between different operations, reducing setup times and increasing efficiency. Adaptability to future upgrades, such as integrating new technologies or expanding capabilities, ensures the machine remains relevant and valuable as production needs evolve. This adaptability can include software upgrades, additional tool stations, or enhanced automation features.
Durability and Build Quality
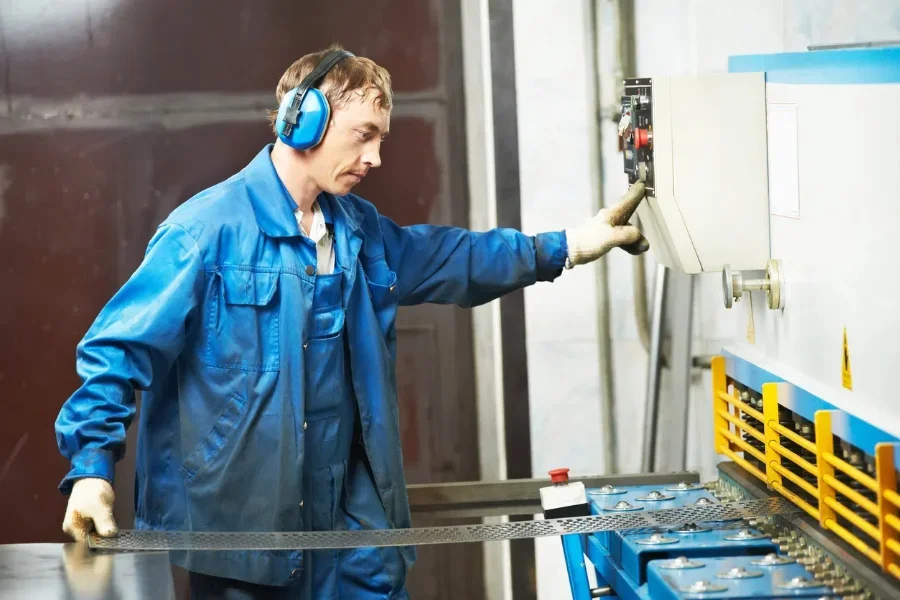
The durability and build quality of a punch press determine its lifespan, maintenance requirements, and overall cost of ownership. Investing in a high-quality machine can lead to long-term savings and improved operational efficiency.
Structural Integrity and Components
The structural integrity of a punch press is foundational to its performance and longevity. Machines constructed with high-grade materials and robust frameworks can withstand the rigors of continuous operation and heavy loads. Key components, such as the ram, bed, and drive mechanisms, should be engineered for durability and precision. For example, hardened steel rams and precision-ground beds ensure consistent performance and reduce wear over time.
Maintenance and Serviceability
Regular maintenance is crucial to keep punch presses operating at peak efficiency. Machines with easily accessible components and user-friendly maintenance features simplify routine upkeep and reduce downtime. Built-in diagnostic systems and real-time monitoring can alert operators to potential issues before they escalate, allowing for proactive maintenance. Additionally, choosing a machine from a reputable manufacturer with a strong service network ensures access to spare parts, technical support, and professional servicing when needed.
Warranty and Support
A comprehensive warranty and robust support from the manufacturer are indicators of a high-quality punch press. Warranties covering key components and overall machine performance provide peace of mind and financial protection. Manufacturers offering extensive support, including training, technical assistance, and regular updates, enhance the value of the machine and ensure it remains a reliable asset in your production environment.
Energy Efficiency and Environmental Impact
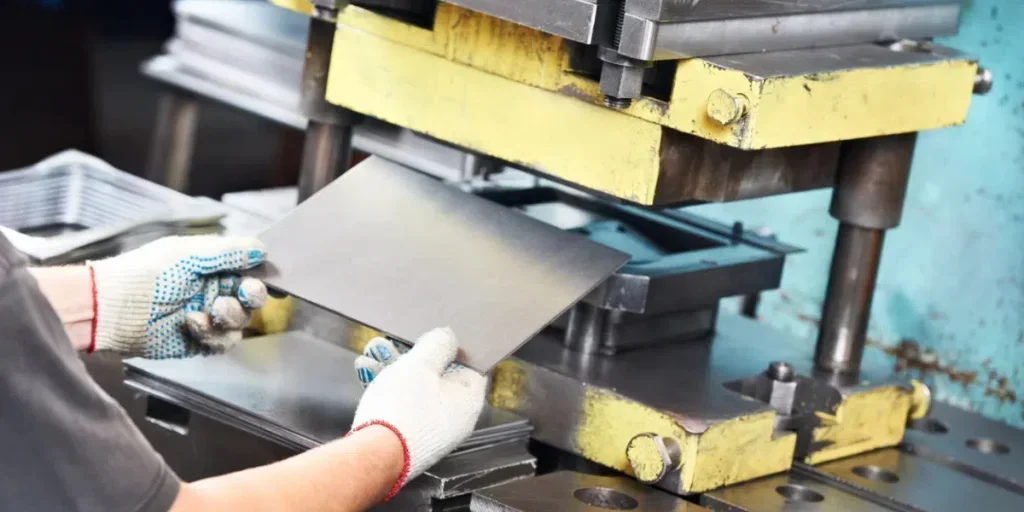
In today’s environmentally conscious market, energy efficiency and sustainability are critical considerations for punch press buyers. Machines that minimize energy consumption and reduce environmental impact can lead to cost savings and improved corporate responsibility.
Energy Consumption
Energy-efficient punch presses reduce operational costs and contribute to sustainability goals. Servo-controlled machines, for example, consume less energy compared to traditional hydraulic or mechanical presses due to their precise control and reduced power wastage. Monitoring and optimizing energy usage through advanced control systems can further enhance efficiency and lower utility expenses.
Environmental Regulations
Compliance with environmental regulations is essential for modern manufacturing operations. Punch presses that adhere to standards such as ISO 14001 for environmental management demonstrate a commitment to reducing environmental impact. Features like energy-efficient motors, eco-friendly lubrication systems, and waste reduction technologies contribute to sustainable operations and regulatory compliance.
Sustainable Practices
Adopting sustainable practices in the use and maintenance of punch presses can enhance their environmental performance. This includes using biodegradable lubricants, recycling scrap materials, and implementing energy-saving measures such as automated shutdown during idle periods. Manufacturers offering environmentally friendly options and guidance on sustainable practices support the broader goal of reducing the industry’s environmental footprint.
Packaging and Regulatory Compliance
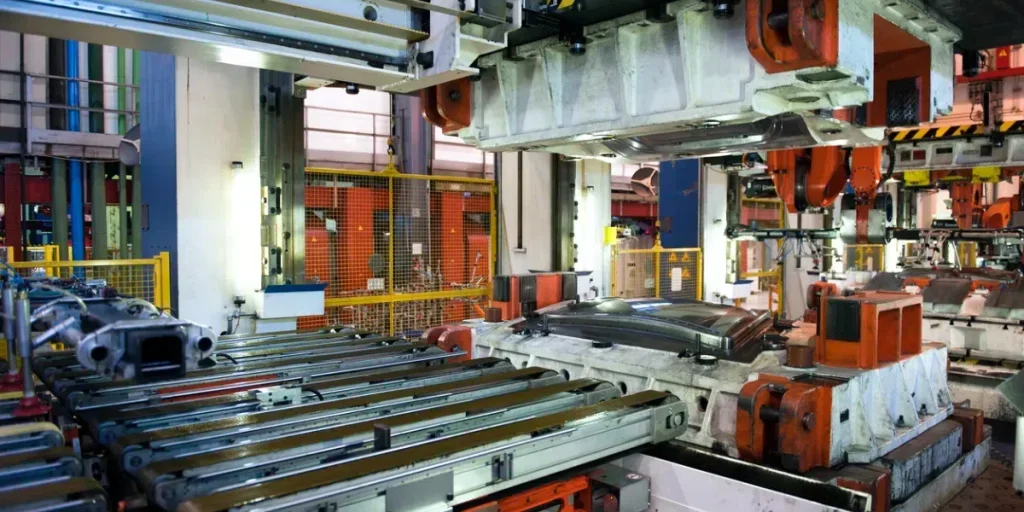
Packaging quality and regulatory compliance are vital aspects to consider when selecting a punching machine. Proper packaging ensures safe transportation and handling, while compliance with industry regulations guarantees safe and reliable operation.
Packaging Quality
The packaging of a punch press should protect the machine during transit and storage. High-quality packaging materials and secure packing methods prevent damage and ensure the machine arrives in optimal condition. Proper labeling and documentation, including handling instructions and safety warnings, facilitate smooth and safe installation.
Regulatory Compliance
Adhering to industry regulations and standards is crucial for ensuring the safety and reliability of punch presses. Compliance with safety standards such as OSHA, CE, or other regional certifications ensures the machine meets stringent safety requirements. Additionally, adherence to quality standards like ISO 9001 signifies a commitment to high manufacturing standards and consistent product quality.
Documentation and Certification
Comprehensive documentation and certification from the manufacturer provide assurance of compliance and support operational efficiency. This includes user manuals, maintenance guides, safety certifications, and performance test reports. Proper documentation facilitates training, maintenance, and troubleshooting, ensuring the machine operates safely and effectively throughout its lifespan.
Wrapping Up: Key Considerations for Punching Machines
Selecting the right punching machine involves a thorough evaluation of various factors, from drive type and automation to durability and energy efficiency. Prioritizing these considerations ensures you invest in a machine that meets your operational needs, enhances productivity, and aligns with sustainability goals. By focusing on high-quality construction, advanced features, and regulatory compliance, you can secure a punch press that delivers long-term value and reliable performance.