The realm of heat press machinery is both vast and nuanced, presenting a plethora of opportunities for individuals and businesses alike. This technology, central to various printing and manufacturing processes, has evolved significantly, incorporating advanced features that cater to a wide array of materials and applications. In this guide, we delve into the essential aspects of heat press machinery, breaking down its functionality, types, application techniques, maintenance tips, and the latest technological advancements. Whether you’re a seasoned professional or new to the field, this article aims to equip you with a deeper understanding of heat presses, empowering you to make informed decisions and optimize your use of this versatile equipment.
Table of Contents:
– Understanding heat press machinery
– Types of heat presses and their applications
– Mastering the art of heat press application
– Maintenance tips for long-lasting performance
– The future of heat press technology
Understanding heat press machinery
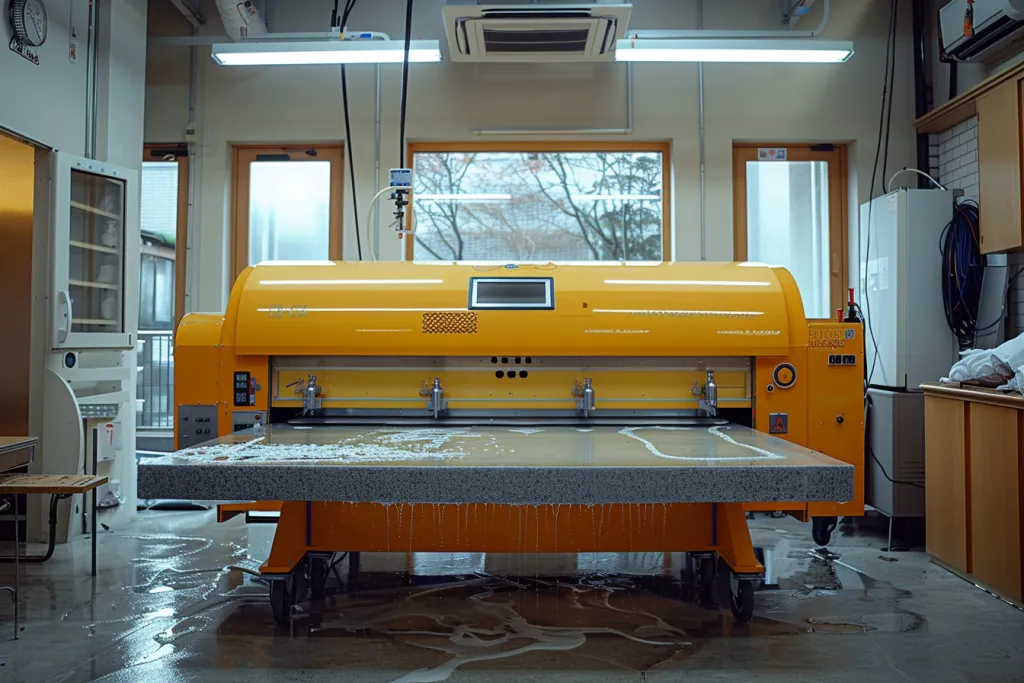
Heat press machinery is designed to imprint a design or graphic on a substrate, such as a t-shirt, mug, or hat, using heat and pressure for a preset period. At its core, the machine comprises a heat plate or platen, a pressing mechanism, and a digital interface to control temperature and time settings. The process begins with the placement of the substrate and the transfer material, such as vinyl or sublimation paper, onto the press. Once the machine is activated, the heated platen presses down onto the transfer material, facilitating the transfer of the design onto the substrate through the application of heat and pressure.
The versatility of heat press machinery lies in its ability to accommodate a wide range of materials and surfaces. From textiles and ceramics to wood and metal, the potential applications are vast, making it a crucial tool in various industries, including advertising, fashion, and home decor. Understanding the specific requirements of your substrate and transfer material is key to achieving optimal results, as different materials react differently under heat and pressure.
Types of heat presses and their applications
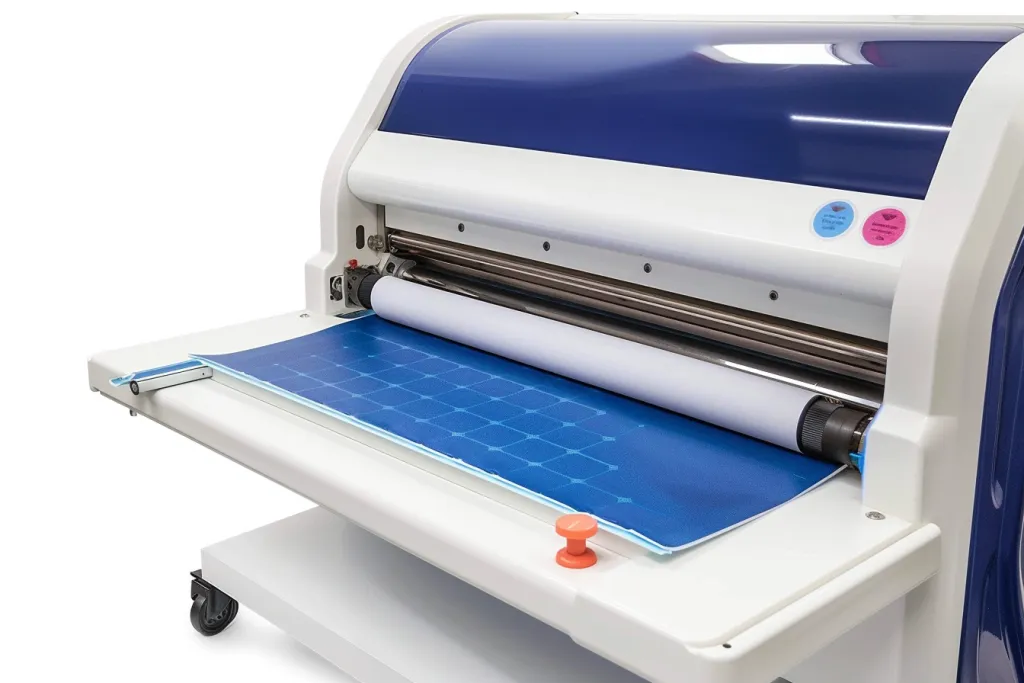
Heat presses come in various configurations, each suited to particular applications and work volumes. The most common types include clamshell, swing-away, and draw heat presses. Clamshell models are known for their compact design, with the upper heat platen opening like a clamshell. This type is ideal for projects with limited space and those involving flat substrates. Swing-away models feature a heat platen that swings away from the lower platen, providing full access to the workspace and reducing the risk of accidental contact with the heated surface. This design is preferable for precision work and items that require more careful placement. Draw heat presses, on the other hand, allow the lower platen to be pulled out like a drawer, offering safe and straightforward layout adjustments.
Selecting the right type of heat press depends on several factors, including the volume of work, the variety of substrates you plan to work with, and the physical space available. For instance, businesses with high production volumes may benefit from pneumatic heat presses, which use air pressure to automate the pressing process, significantly increasing efficiency and consistency.
Mastering the art of heat press application

Achieving excellence in heat press application requires understanding the interplay between temperature, pressure, and time. Each substrate and transfer material combination has a specific set of requirements that, when precisely met, result in a high-quality transfer. Temperature settings vary depending on the material; for example, thicker fabrics may require higher temperatures, while delicate substrates need lower heat to avoid damage. Similarly, the pressure must be adjusted to ensure even contact without crushing the substrate. Timing is equally crucial, as under-pressing can lead to incomplete transfers, while over-pressing might burn the material or cause the design to peel.
Experimentation and experience play significant roles in mastering heat press application. Keeping detailed records of successful settings for different material combinations can serve as a valuable reference for future projects. Additionally, leveraging the digital controls available on modern heat presses can help achieve precise outcomes consistently.
Maintenance tips for long-lasting performance
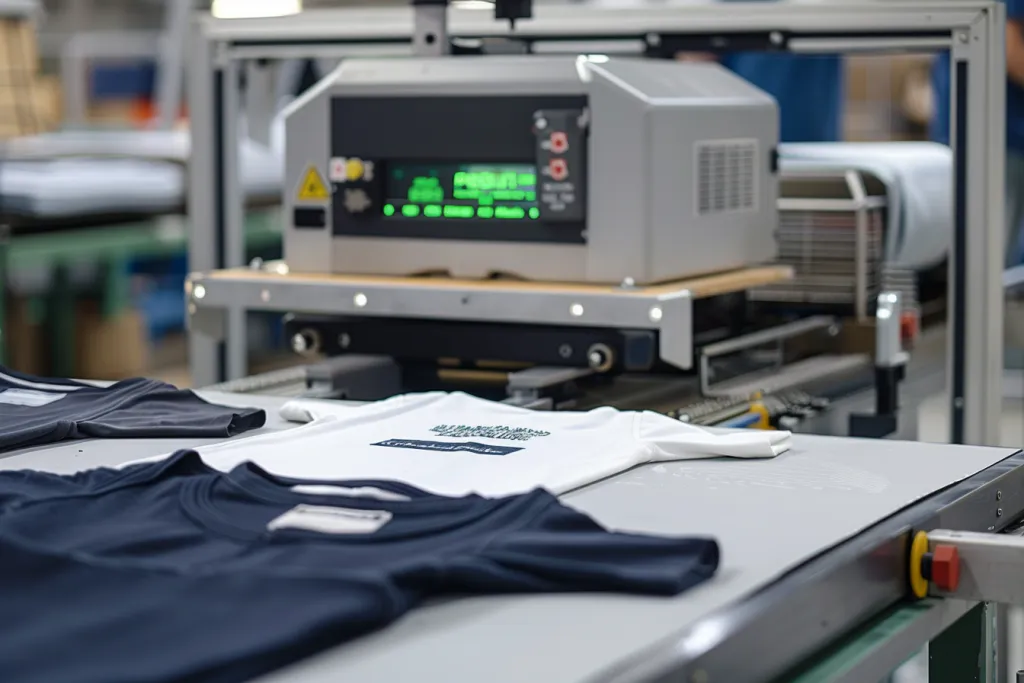
Regular maintenance is essential to ensure the longevity and efficiency of heat press machinery. Keeping the heat platen clean from adhesive residue and other contaminants is crucial to prevent transfer errors and potential damage to substrates. This can be achieved by using a non-abrasive cleaner when the machine is cool and ensuring the platen is dry before use. Checking the machine’s components, such as the silicone pad on the lower platen and the condition of the heating element, can help identify wear and tear early, preventing more significant issues down the line.
Additionally, it’s important to adhere to the manufacturer’s guidelines for servicing and use only recommended parts for replacements. This not only extends the lifespan of the machine but also ensures that it operates at peak performance, delivering consistent results.
The future of heat press technology
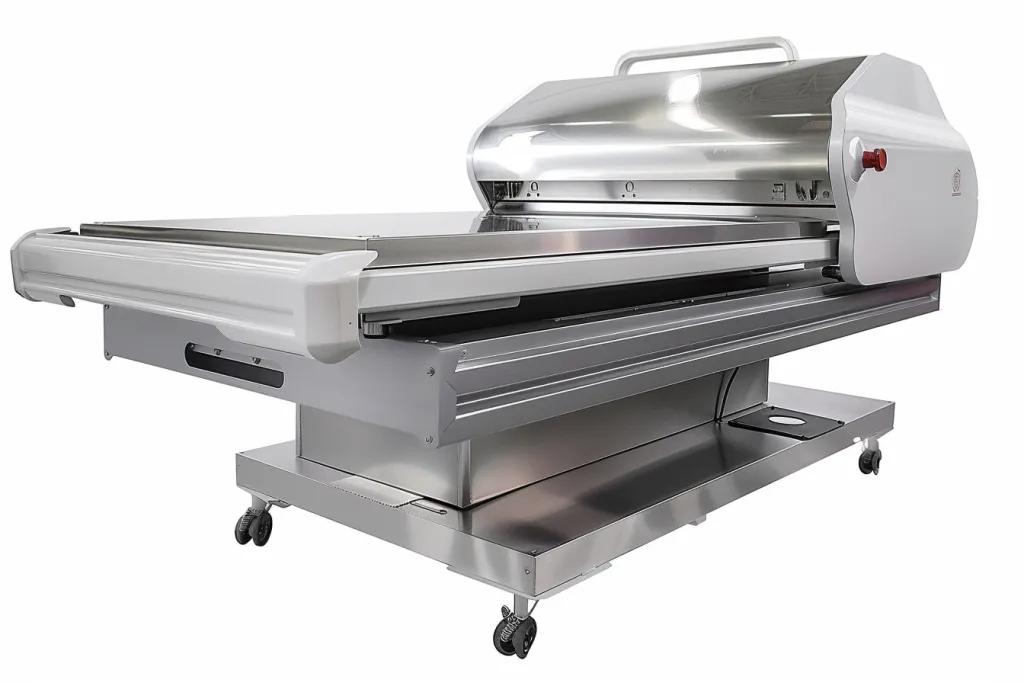
As we look towards the future, heat press technology continues to evolve, with advancements focusing on improving efficiency, versatility, and user-friendliness. Innovations such as automated pressure adjustments, enhanced digital interfaces for more precise control, and eco-friendly models that reduce energy consumption are shaping the next generation of heat presses. These developments promise to expand the creative possibilities and applications of heat press machinery, making it an even more indispensable tool in various industries.
Conclusion:
Heat press machinery stands as a cornerstone in the world of printing and manufacturing, offering unparalleled versatility and efficiency. By understanding the fundamentals, selecting the right equipment, mastering application techniques, and adhering to maintenance best practices, users can unlock the full potential of these powerful tools. As technology advances, staying informed and adaptable will be key to leveraging the evolving capabilities of heat presses, ensuring continued success in your projects and endeavors.