حالیہ برسوں میں، پلاسٹک اور دھاتوں کی عالمی مانگ کو پورا کرنے کے لیے مینوفیکچرنگ کی سرگرمیوں میں اضافہ ہوا ہے۔ نتیجے کے طور پر، انجکشن مولڈنگ اور اخراج کے عمل کے استعمال میں بھی نمایاں اضافہ ہوا ہے۔ یہ عمل مسابقتی رفتار سے بڑے پیمانے پر پلاسٹک پیدا کرنے کے لیے استعمال ہوتے ہیں۔
تاہم، دونوں طریقوں میں کافی فرق ہے۔ مثال کے طور پر، انجکشن مولڈنگ تین جہتی شکلوں کے لیے زیادہ موزوں ہے، جب کہ دو جہتی اشکال کے لیے اخراج بہتر ہے۔ یہ بلاگ ان عملوں کا مزید موازنہ کرتا ہے، پلاسٹک مینوفیکچرنگ میں ان کے استعمال، ان کے فائدے اور نقصانات اور بڑے فرق کو تلاش کرتا ہے۔
کی میز کے مندرجات
انجیکشن مولڈنگ کا عمل
اخراج عمل
انجیکشن مولڈنگ اور اخراج کے درمیان فرق
نتیجہ
انجیکشن مولڈنگ کا عمل
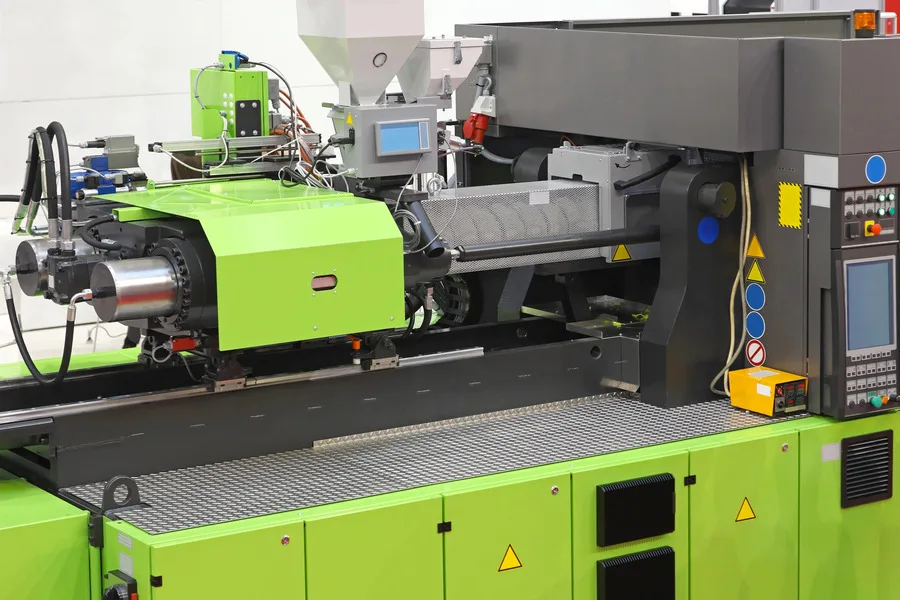
دنیا بھر میں مینوفیکچررز ایسے عمل اور اختراعات کو اپنا رہے ہیں جو کم لاگت والے بڑے پیمانے پر پیداوار میں سہولت فراہم کرتے ہیں۔ نتیجے کے طور پر، انجیکشن مولڈنگ زیادہ تر مینوفیکچررز کے لیے جانے والا عمل بن گیا ہے کیونکہ یہ اعلی حجم کی پیداوار اور وسیع ایپلی کیشنز کو قابل بنانے کے لیے کم لاگت والی ٹیکنالوجی کا استعمال کرتا ہے۔ اس کا ثبوت تیزی سے بڑھتی ہوئی عالمی انجیکشن مارکیٹ کے سائز سے ہے، جس کی قدر کی گئی تھی۔ 261.8 میں 2021 بلین امریکی ڈالر اور 4.8-2022 کے درمیان 2030% کی CAGR سے بڑھنے کا امکان ہے۔
انجیکشن مولڈنگ کا عمل پلاسٹک کی رال کو گرمی، دباؤ، انجیکٹر اور مولڈ کا استعمال کرتے ہوئے پیچیدہ پلاسٹک کی مصنوعات میں تبدیل کرتا ہے۔ اس صورت میں، ٹھوس پلاسٹک کو ایک مخصوص پگھلنے والے مقام پر پگھلا کر ایک مقررہ رفتار سے مولڈ ڈھانچے میں داخل کیا جاتا ہے۔ دی انجیکشن مشین مطلوبہ دباؤ فراہم کرتا ہے، جبکہ آبی گزرگاہ مطلوبہ مصنوعات حاصل کرنے کے لیے ٹھنڈک کی سہولت فراہم کرتی ہے۔
انجیکشن مولڈنگ کے فوائد
- اعلی صحت سے متعلق اور درستگی
- زیادہ تر پلاسٹک کے ساتھ مطابقت
- اعلی حجم کی پیداوار کے لیے سرمایہ کاری مؤثر
- اعلی کارکردگی اور پیداوری
- مستقل کارکردگی
خامیاں
- طویل ابتدائی لیڈ اوقات
- کم حجم کی پیداوار کے لیے غیر موزوں
- اعلی سیٹ اپ کے اخراجات
اخراج عمل
عالمی مینوفیکچرنگ سیکٹر میں ترقی طلب کو بڑھا رہی ہے۔ اخراج مشینری. یہ مطالبہ عالمی اخراج مشینری مارکیٹ میں ظاہر ہوتا ہے، جس کی قدر کی گئی تھی۔ 8.33 میں 2022 بلین امریکی ڈالر اور 4.3-2023 کے درمیان 2030% کی CAGR سے بڑھنے کا امکان ہے۔
ایکسٹروڈڈ پروڈکٹس کی بہت زیادہ مانگ ہے کیونکہ وہ دنیا بھر میں پھیلی ہوئی متعدد صنعتوں میں استعمال ہوتی ہیں، بشمول آٹوموٹو، صارفی سامان اور پیکیجنگ۔ اگرچہ اخراج کا عمل دھاتوں اور سیرامکس میں استعمال کیا جا سکتا ہے، لیکن یہ بنیادی طور پر پلاسٹک کے مواد کے ساتھ استعمال ہوتا ہے، جس کا حساب 76.9٪ 2022 میں عالمی آمدنی کا حصہ۔
اخراج کے عمل میں تھرمو پلاسٹک مواد کو گھسنے والے کو کھانا کھلانا شامل ہے، جہاں انہیں گرم کیا جاتا ہے، پگھلا دیا جاتا ہے، اور پھر ڈائی کے ذریعے ایک مسلسل، مخصوص شکل بنانے کے لیے مجبور کیا جاتا ہے۔ ایکسٹروڈر عام طور پر گھومنے والے اسکرو پر مشتمل ہوتا ہے جو پگھلے ہوئے مواد کو آگے بڑھاتا ہے، جو اخراج کے لیے ضروری دباؤ فراہم کرتا ہے۔ جیسے ہی مواد ڈائی سے باہر نکلتا ہے، یہ مضبوط ہوتا ہے اور مطلوبہ شکل کو برقرار رکھتا ہے۔ یہ عمل مصنوعات بنانے کے لیے موزوں ہے جیسے اڑا فلمیں، پلیٹیں، ٹیوبیں، سلاخیں، اور شکل کا مواد۔
فوائد
- اعلی حجم کی پیداوار کے لئے مثالی۔
- انتہائی ورسٹائل
- کم قیمت
- عظیم سطح ختم
خامیاں
- کراس سیکشن یا سائز میں انحراف کو سنبھالنے میں ناکامی۔
- ممکنہ ماحولیاتی خدشات
انجیکشن مولڈنگ اور اخراج کے درمیان فرق
انجیکشن مولڈنگ اور اخراج کے عمل کے درمیان سمجھی جانے والی مماثلت کے باوجود، وہ مختلف پہلوؤں میں مختلف ہیں، بشمول عمل کے بنیادی اصول، درستگی کی سطح، اور مطابقت۔
عمل
انجکشن مولڈنگ اور اخراج حتمی پروڈکٹ تیار کرنے کے لیے مختلف عمل کا استعمال کرتے ہیں۔
1) انجکشن مولڈنگ عمل
انجیکشن مولڈنگ کا عمل مواد کو پگھلانے اور اسے مطلوبہ شکل کے گہاوں کے ساتھ مولڈ ڈھانچے میں انجیکشن لگانے سے شروع ہوتا ہے، جہاں یہ پھر ٹھنڈا اور مضبوط ہوتا ہے۔ یہ عمل ایک مخصوص چکر میں ہوتا ہے جو سات اہم مراحل پر مشتمل ہوتا ہے جو ذیل میں بیان کیے گئے ہیں۔
- مولڈنگ سے پہلے کی تیاری
مینوفیکچررز معیاری مصنوعات بنانے کے خواہاں ہیں اور ہموار کا مقصد رکھتے ہیں۔ پلاسٹک انجکشن مولڈنگ عمل مختلف تیاری کی سرگرمیوں کو اپنانے. ان میں شامل ہیں:
- خام مال کی تیاری
- بیرل کی صفائی
- ڈالنے کو پہلے سے گرم کرنا
- ریلیز ایجنٹ کا انتخاب
- مواد شامل کرنا
انجیکشن مولڈنگ کے عمل میں پہلا قدم مواد کو شامل کرنا ہے۔ آپریشنل استحکام اور پلاسٹکائزیشن کی یکسانیت کو یقینی بنانے کے لیے حجم کو مستقل رکھ کر مواد کو مقداری طور پر شامل کیا جانا چاہیے، جس کے نتیجے میں اعلیٰ معیار کی مصنوعات حاصل ہوتی ہیں۔
- پلاسٹکائزنگ
میں بیرل انجکشن مولڈنگ مشین مولڈنگ مواد کو گرم کرنے، دبانے اور مکس کرنے کے لیے استعمال کیا جاتا ہے، اس طرح اسے دانے دار ٹھوس یا ڈھیلے پاؤڈر سے ایک مسلسل ہم آہنگ پگھلنے میں تبدیل کیا جاتا ہے۔
- انجیکشن لگانا
پلنجر یا اسکرو انجیکشن سلنڈر اور پسٹن کے ذریعے نمایاں دباؤ ڈالتا ہے، پلاسٹکائزڈ پلاسٹک کو بیرل کے سامنے والے نوزل اور مولڈ کے نوزل دونوں کے ذریعے پگھلاتا ہے۔
- کولنگ
ایک بار جب پلاسٹک کے پگھلنے کو بند مولڈ گہا میں داخل کیا جاتا ہے، تو سڑنا کو مزید ٹھنڈا کرنے کے لیے ٹھنڈا کرنے والے مواد جیسے پانی، ہوا یا تیل متعارف کرایا جاتا ہے۔
- ڈیمولڈنگ
اس مقام پر، ٹھنڈے ہوئے پلاسٹک کو انجیکشن تکنیک کا استعمال کرتے ہوئے سانچے سے باہر دھکیل دیا جاتا ہے، جیسے کہ ایجیکٹر پن یا پلیٹوں کے ذریعے۔ یہ مرحلہ انجیکشن مولڈنگ کے عمل کے اختتام کو یقینی بنا کر اس بات کو یقینی بناتا ہے کہ مولڈ کا تیار شدہ حصہ اس کی شکل میں کسی قسم کا نقصان یا بگاڑ پیدا کیے بغیر الگ ہو گیا ہے۔
- مصنوعات کی پوسٹ پروسیسنگ
اس پوسٹ پروسیسنگ مرحلے میں مختلف سرگرمیاں شامل ہیں، جیسے موٹائی، شگافوں، یا مسخ شدہ شکلوں کے تغیرات میں جھلکنے والے ڈھالے ہوئے حصوں میں بقایا تناؤ کو دور کرنا۔ اس میں نمی بھی شامل ہو سکتی ہے، جس میں ڈھالے ہوئے حصے کے رنگ، کارکردگی اور سائز کو مستحکم کرنا شامل ہے۔
2) اخراج کا عمل
اخراج کے دوران، پولیمر مواد کو دباؤ کے تحت سکرو یا پلنگر کا استعمال کرتے ہوئے ڈائی کے ذریعے مجبور کیا جاتا ہے۔ اخراج کے عمل کو تین مراحل میں تقسیم کیا گیا ہے:
- مواد کی پلاسٹکائزیشن اور دباؤ
اس مرحلے میں خام مال کو چھروں یا دانے داروں کی شکل میں کھلایا جاتا ہے۔ extruder ہاپر کے ذریعے. اس کے بعد ایک سکرو مواد کو بیرل میں دھکیلنے کے لیے استعمال کیا جاتا ہے، جس سے اسے گرمی اور مکینیکل کارروائی کے لیے پلاسٹکائزیشن شروع کیا جاتا ہے۔ یہ مواد کو پگھلی ہوئی یا پلاسٹکائزڈ حالت میں بدل دیتا ہے۔ اس کے ساتھ ہی، گھومنے والا اسکرو گرمی پیدا کرتا ہے، اختلاط کو فروغ دیتا ہے، اور مواد کی مستقل پلاسٹکائزیشن کو یقینی بنانے کے لیے دباؤ کا اطلاق کرتا ہے۔
- شکل دینا
اس مرحلے میں، اخراج شدہ مواد ڈائی کی شکل دینے والے عناصر سے گزرتا ہے، جس میں خاص طور پر ڈیزائن کردہ سوراخ یا چینلز شامل ہوتے ہیں۔ یہ نکالے گئے مواد کو مطلوبہ شکل، شکل اور طول و عرض لینے میں مدد کرتے ہیں۔
- کولنگ
جیسے ہی باہر نکالا گیا مواد ڈائی سے نکلتا ہے یہ کولنگ زون میں داخل ہوتا ہے، اسے ٹھنڈک کرنے والے میکانزم جیسے محیطی ہوا، پانی کے اسپرے، یا کولنگ حمام کے سامنے لاتا ہے۔ یہ مواد کے درجہ حرارت کو کم کرنے اور اسے مضبوط بنانے میں مدد کرتا ہے، اس طرح اسے پگھلی ہوئی حالت سے ٹھوس شکل میں تبدیل کر دیتا ہے۔
پلاسٹک کے ساتھ مطابقت
اگرچہ انجیکشن مولڈنگ اور اخراج میں استعمال ہونے والے پلاسٹک کی کچھ قسمیں اوورلیپ ہو سکتی ہیں، لیکن خصوصیات اور مطابقت میں فرق کی وجہ سے کچھ مواد ایک یا دوسرے عمل کے لیے بہتر ہو سکتے ہیں۔ مثال کے طور پر، انجیکشن مولڈنگ ہر قسم کے پلاسٹک کے ساتھ مطابقت رکھتی ہے، بشمول تھرمو پلاسٹک اور زیادہ تر تھرموسیٹ پلاسٹک۔ یہ مطابقت پیچیدہ کیمیائی مرکبات کے ساتھ مواد پر کارروائی کرنے کے عمل کی صلاحیت پر مبنی ہے۔
اس کے برعکس، زیادہ تر extruders بہترین پگھلنے کے بہاؤ کی خصوصیات اور استحکام کے ساتھ بنیادی طور پر تھرمو پلاسٹک کے ساتھ ہم آہنگ ہیں۔ اس کی وجہ یہ ہے کہ یہ عمل زیادہ تر ہموار اخراج کے لیے مواد کے مسلسل بہاؤ پر انحصار کرتا ہے۔
صحت سے متعلق
انجکشن مولڈنگ اخراج سے زیادہ درستگی اور سخت رواداری پیش کرتی ہے۔ یہ بہترین جہتی درستگی کے ساتھ انتہائی درست اور پیچیدہ حصوں کو تیار کرنے کی صلاحیت کے لیے جانا جاتا ہے۔ اس کی وجہ یہ ہے کہ اس عمل میں پگھلے ہوئے مواد کو زیادہ دباؤ کے تحت بند مولڈ گہا میں داخل کرنا شامل ہے، اس طرح حتمی مصنوع کی شکل، سائز، اور سطح کی تکمیل پر قطعی کنٹرول کی سہولت فراہم کی جاتی ہے۔
اخراج میں ڈائی کے ذریعے پگھلے ہوئے مواد کا مسلسل بہاؤ شامل ہوتا ہے۔ اگرچہ اخراج ڈیز کو ٹھیک ٹھیک انجنیئر کیا جا سکتا ہے، لیکن درستگی کی سطح انجیکشن مولڈنگ سے کم ہے۔ تاہم، اخراج قابل قبول صحت سے متعلق سطحوں کو حاصل کر سکتا ہے، خاص طور پر آسان شکلوں اور پروجیکٹوں کے ساتھ جن میں کم سخت رواداری کی ضرورت ہوتی ہے۔
مواد کی روانی
مواد کی روانی دونوں عملوں کے لیے ایک اہم جزو ہے۔ تاہم، انجکشن مولڈنگ خاص طور پر پیچیدہ اور پتلی دیواروں والی مصنوعات کے لیے مناسب مولڈ بھرنے کو یقینی بنانے کے لیے اعلیٰ مواد کی روانی کی ضرورت ہوتی ہے۔ اس عمل میں استعمال ہونے والے پگھلے ہوئے مواد میں مولڈ گہاوں کے پیچیدہ شکلوں، کونوں اور پتلے حصوں میں آسانی سے پھیلنے کے لیے بہترین روانی ہونی چاہیے۔
اس کے برعکس، اخراج میں اس کی مسلسل اور کھلی نوعیت کی وجہ سے مواد کے بہاؤ کی کم سخت ضرورت ہوتی ہے۔ اس عمل کے لیے، پیچیدہ مولڈ گہاوں کو پُر کرنے کی ضرورت نہیں ہے، مطلب یہ ہے کہ مواد کو ڈائی کے ذریعے آسانی سے بہنے اور نکالے گئے پروڈکٹ کی لمبائی کے ساتھ ایک مستقل شکل اور طول و عرض کو برقرار رکھنے کے لیے صرف کافی روانی کی ضرورت ہوتی ہے۔
پگھلنے والی طاقت
دونوں عملوں کو پگھلنے کی طاقت کی مختلف ڈگریوں کی ضرورت ہوتی ہے۔ مثال کے طور پر، انجیکشن مولڈنگ کو زیادہ پگھلنے کی طاقت کی ضرورت نہیں ہوتی ہے کیونکہ پلاسٹک کو ڈائی میں ڈھالا جاتا ہے، اس طرح جیومیٹریکل حدود کے تابع ہوتا ہے۔ اس کے علاوہ، مواد کو کنٹرول شدہ کولنگ میں داخل کیا جاتا ہے، جس سے فوری ٹھوس ہونے کا موقع ملتا ہے۔
اخراج میں، مواد آزادانہ طور پر ڈائی سے باہر نکلتا ہے اور اس کے بعد تھرموفارمنگ اور ہولو بلو مولڈنگ جیسے عمل کی ضرورت پڑسکتی ہے۔ ان عملوں کے نتیجے میں بگاڑ پیدا ہو سکتا ہے جیسے جھک جانا اور کھینچنا، جو تیار شدہ مصنوعات کے معیار کو کم کر سکتا ہے۔ اس طرح، انجکشن مولڈنگ کے مقابلے میں اخراج میں دھات کی مطلوبہ طاقت زیادہ ہوتی ہے۔
نتیجہ
مینوفیکچرنگ سیکٹر میں ترقی نے انجیکشن مولڈنگ اور اخراج کو اپنانے میں نمایاں اضافہ کیا ہے۔ اگرچہ دونوں عمل پلاسٹک کی پیداوار میں استعمال ہوتے ہیں، ان میں کافی فعال فرق اور صفات ہیں۔ مثال کے طور پر، انجکشن مولڈنگ 3D مصنوعات کے لیے موزوں ہے، جبکہ اخراج 2D مصنوعات کے لیے موزوں ہے۔ اس کے علاوہ، انجکشن مولڈنگ اخراج کے مقابلے میں پلاسٹک کی وسیع رینج کے ساتھ مطابقت رکھتی ہے۔ اس طرح، دونوں کے درمیان انتخاب عمل، مواد، اور کارکردگی کی محتاط غور و فکر اور منصوبہ بندی پر مبنی ہونا چاہیے۔
انجیکشن مولڈنگ اور اخراج سے متعلق ہزاروں مصنوعات اور مشینیں تلاش کرنے کے لیے، ملاحظہ کریں۔ علی بابا.